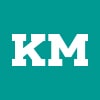
«Троицкий крановый завод» организовал производство «углеволоконной паутины»
рубрика: технологии
На Форуме будущих технологий многих заинтересовал ажурный многогранник из углеволокна на стенде Росатома. Это изделие Троицкого кранового завода (ТКЗ), потенциального партнера госкорпорации, получено методом пространственной стержневой намотки, сообщает газета «Страна Росатом».
Для ТКЗ, одного из крупнейших в России производителей грузоподъемного оборудования, композиты — новое направление бизнеса, рассказывает главный технолог по композитным материалам завода Александр Безруков. Для позиционирования и развития направления придумали бренд «Монокрафт».
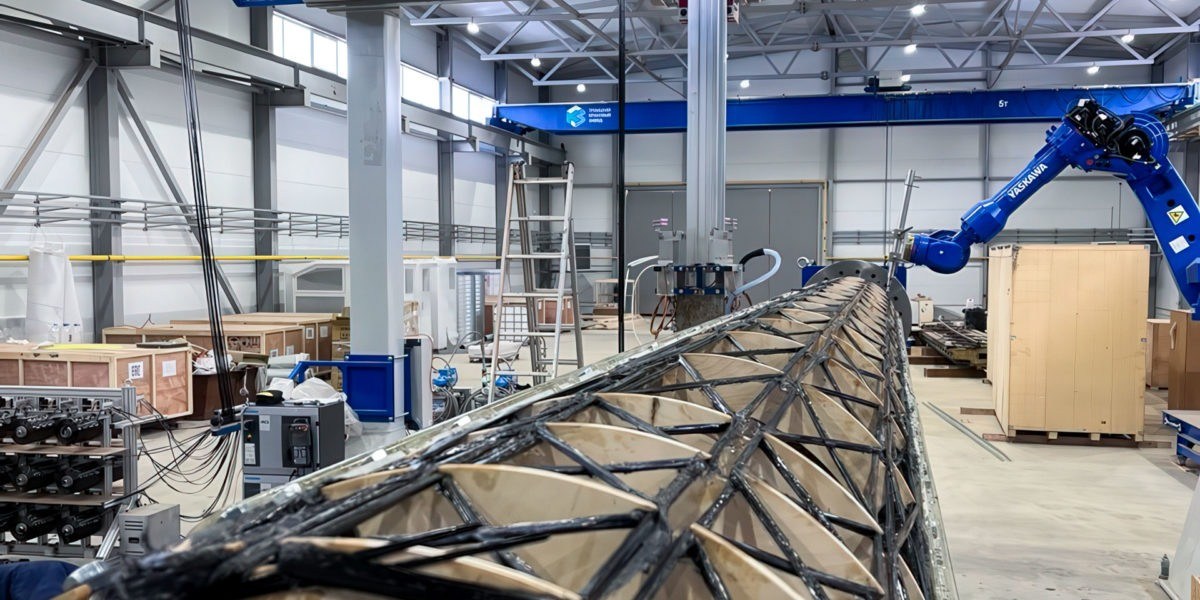
В Тверской области в цехе площадью около 1,5 тыс. м2 недавно установили роботизированную линию намотки. Идет пусконаладка оборудования и пробное изготовление изделий методом пространственной стержневой намотки — впервые в стране. Эти мощности понадобились, чтобы выполнить опытно-конструкторские работы для концерна «Океанприбор» по заказу Минпромторга и изготовить телескопические стрелы.
Композитные изделия чаще всего изготавливают из угле- или стеклотканей. Их раскраивают и укладывают в форму, затем пропитывают смолой и отверждают. В пространственной стержневой намотке используют не ткани, а жгуты — ровинги. Из них, экономно расходуя дорогой композит, плетут крупногабаритные изделия, способные вынести большую нагрузку.
Как это устроено. На вал вращения станка с числовым программным управлением устанавливают каркасные ребра с выемками по внешнему краю, через выемки подается пропитанный смолой ровинг. Схема, в какой последовательности на какое ребро подавать, заложена в компьютере. Программу пишут инженер-проектировщик и программист. Все похоже на намотку нити на катушку. Только на «катушке», как на грифе штанги, через определенные промежутки установлены «блины» сложной формы. После термообработки и отверждения конструкции вал с ребрами извлекают и изделие отправляют клиенту.
Изготовленные методом пространственной стержневой намотки изделия могут конкурировать и со слоистыми композитными, и с металлоконструкциями, утверждает Александр Безруков.
Первое преимущество — более широкие возможности технологии. Каркасные ребра просто менять, и изготовить их быстрее, чем форму для тканей. Слоистые композиты сложнее укладывать, занимаются этим люди. Пространственная стержневая намотка роботизирована, влияние ошибки человека минимальное.
Второй плюс — меньшая материалоемкость. Из дорогого композита делают только каркас, который можно покрыть более дешевым материалом. Каркас обеспечит форму и прочность, покрытие — целостность и внешний вид. Александр Безруков считает, что, например, в автомобилях композитный каркас надежнее, чем корпус, сбережет водителя и пассажиров при аварии. «Что легче порвать — ткань или веревку? — спрашивает он. — Наши ровинги выдерживают до 2 тыс. МПа на растяжение. То есть, чтобы порвать один жгут, нужно потратить колоссальную энергию».
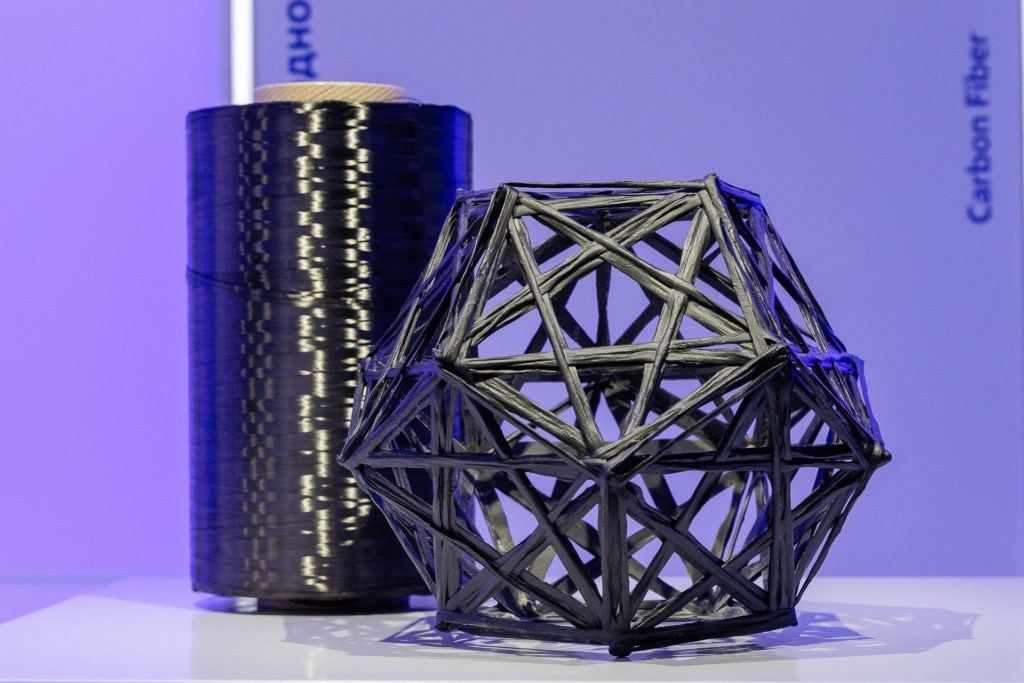
Третье преимущество — меньший вес при сопоставимых прочностных характеристиках и проектных нагрузках, что важно при монтаже и перевозке.
Ну и наконец, коррозионная и морозостойкость композитов в морской воде или арктическом климате в разы выше, чем у металлоконструкций.
Самая близкая ТКЗ область применения композитных каркасных изделий — стреловые и мачтовые конструкции, так как сквозь ферму легко проходит воздух и морское течение (если придется работать под водой). Примеры — судовой палубный кран, вышка сотовой связи. Во-первых, их не надо красить (композит не подвержен коррозии), во‑вторых, благодаря малой массе их можно перевозить на легковом автомобиле, грузить, разгружать и устанавливать в одиночку или вдвоем. Еще и композитные лесенки можно намотать, чтобы персоналу удобно было лезть на вышки. Такой заказ обсуждала с ТКЗ одна телеком-компания. Первый экземпляр готов, второй делают с учетом замечаний.
Намотать можно и каркасы небольших пешеходных мостов, транспортных средств (вагонов, катамаранов — такие есть в Китае и Германии), беспилотников и даже фермы для солнечных батарей космических аппаратов.
Дизайнерская мебель, малые архитектурные формы и арт-объекты — еще один потенциально большой рынок. «Мы исследуем сферы, в которых могли бы пригодиться наши решения», — говорит руководитель отдела продаж композитных изделий ТКЗ Роман Федоров.
ТКЗ не конкурент, а скорее потенциальный клиент «Росатома». Завод заинтересован в сотрудничестве и уже тестировал углеродный ровинг композитного дивизиона. Ровинг понравился, но требуется потолще, такой готовы брать. Возможно и партнерство в расширении номенклатуры изделий. Скажем, ТКЗ делает каркас, композитный дивизион — настилы и полную сборку.
Не исключено, что продукция под брендом «Монокрафт» заинтересует строителей, машиностроителей «Росатома» или организации, работающие на Севморпути. Перспективное направление — арктическое строительство. Напомним, что по поручению президента России госкорпорация участвует в разработке финансово-экономической и организационной модели развития Трансарктического транспортного коридора (маршрута между северо-западными и восточными портами).
«У технологии хорошие перспективы, — комментирует заместитель гендиректора, технический директор дивизиона «Росатом Композитные технологии» Юрий Свистунов. — Организовать производство сложных конструкций можно не только на стационарном предприятии, но и на месте — там, где они будут использоваться. Есть и пространство для улучшений: пока технология пропитки такова, что эпоксидного связующего чересчур много, а убрать излишки невозможно. Из-за полимеризации при естественной температуре физико-механическими характеристиками приходится жертвовать — они слабее, чем при повышенной. А хотелось бы, конечно, их улучшить».