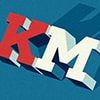
О температуре формования полимерных композитов
рубрика: технологии
В справочной и нормативно-технической литературе, включая действующие ГОСТы, СНиПы, ТУ и пр., указывается «комфортная» температура формования изделий из полимерных композиционных материалов в пределах 18–23°С [1, 2]. Для такой температуры подбирается состав и дозировка систем отверждения и определяется время желатинизации и отверждения полимера «холодного» отверждения. В конечном итоге, соблюдение регламента подготовки ламината и проведения работ по изготовлению композита определяет эксплуатационные свойства готового изделия.
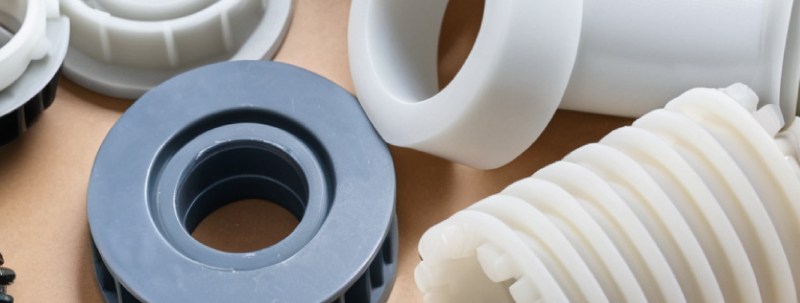
Сказанное выше — безусловная истина и не подлежит сомнению, но, как всегда, в практической работе есть определенные нюансы, которые приходится учитывать в реальных условиях проведения работ. Если работа по изготовлению композита проводится в цеховых условиях, когда возможно долговременно обеспечить указанный температурный режим, безопасный режим проветривания, требуемую освещенность рабочего места и другие санитарно-гигиенические условия проведения работ, то вопросов не возникает и работа проходит в штатном режиме. Часто при проведении работ на открытой площадке, обеспечить долговременный оптимальный рабочий режим невозможно. Температура окружающего воздуха существенно меняется в течение дня и в зависимости от сезона, возможно безветрие, повышенная влажность и др., что может служить формальным предлогом для приостановки работ по формованию композита. Подобная ситуация часто возникает при проведению футеровочных работ способом «мокрого» ламинирования на технологическом оборудовании и строительных конструкциях промышленных предприятий.
Для оценки влияния пониженной температуры окружающего воздуха на эксплуатационные свойства футеровочного покрытия в ООО СКБ «Мысль» были проведены исследования образцов по следующим параметрам:
- твердость ламината (ГОСТ 24621-2015), изготовленного из предускоренной тиксотропной) полиэфирной смолы на основе дициклопентадиена — «ДЕПОЛ С–180 ПТ» и эмульсионного стекломата плотностью 450 г/м2 при температуре окружающего воздуха + 22°С (далее — образцы группы №1) и +8°С (далее — образцы группы №2) [3];
- водопоглощение (ГОСТ 4650–2014) образцов ламината №1 и №2 [4];
- испытания на статический изгиб (ГОСТ 4648–2014), указанных выше образцов ламината [5];
- испытание на растяжение (ГОСТ 11262-2014), образцов ламината, изготовленных при разной температуре [6].
Результаты исследований приведены ниже.
Твердость образцов по шкале Шора проверялась с помощью дюрометра АТН 200 с интервалом 1, 2, 3 и 24 часа с момента их изготовления. График набора твердости представлен на рисунке 1.
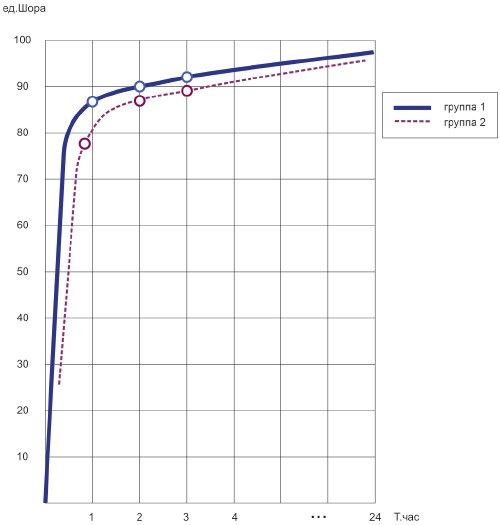
Рисунок 1
Как видно из графика образцы, изготовленные при температуре +8°С, в первые три часа после изготовления отверждались медленнее, чем образцы, изготовленные при оптимальной рабочей температуре, однако через 24 часа эта разница (в твердости) практически нивелировалась. В доказательство этого факта приводим фото эксперимента — рисунок 2.
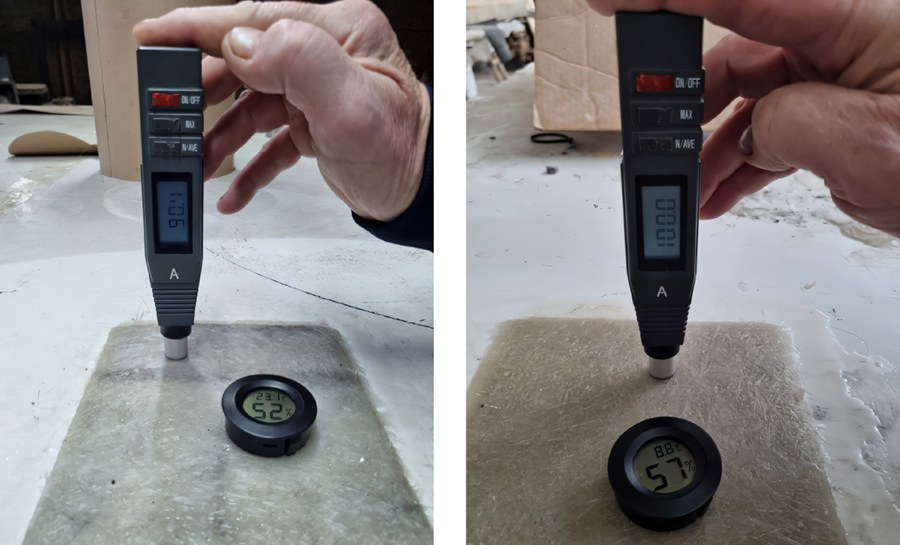
Рисунок 2
Методика испытаний на изгибную прочность — по ГОСТ 4648-2014. Испытательная машина: Shimadzu AG-X 50kN. Образец: две группы по три прямоугольных образца: толщина ~5мм, ширина ~13,5мм, расстояние между неподвижными призмами - 60мм., скорость нагружения — V = 1мм/мин. При испытании определяли: упругий модуль, как коэффициент пропорциональности между деформацией и напряжением на упругом/линейном участке деформационной кривой; предел прочности (максимальная нагрузка при испытании) и деформацию образца при достижении предела прочности. Обработка результатов экспериментов осуществляли при помощи программного обеспечения Trapezium-X, которое было предоставлено фирмой Shimadzu.
По достижению предела прочности образцов, они теряли способность к сопротивлению прикладываемой нагрузки, что соответствовало появлению разрушений в месте нагружения подвижной призмой и резкому падению напряжения на деформационной кривой. Деформационные кривые, наиболее близкие к средним, приведены на рисунке 3. Видно, что характер деформационного поведения у этих групп одинаковый. Результаты испытаний представлены в таблице 1. Установлено, что с учётом погрешности разницы в механических свойствах при трехточечном изгибе между образцами, изготовленными при разной температуре – нет.
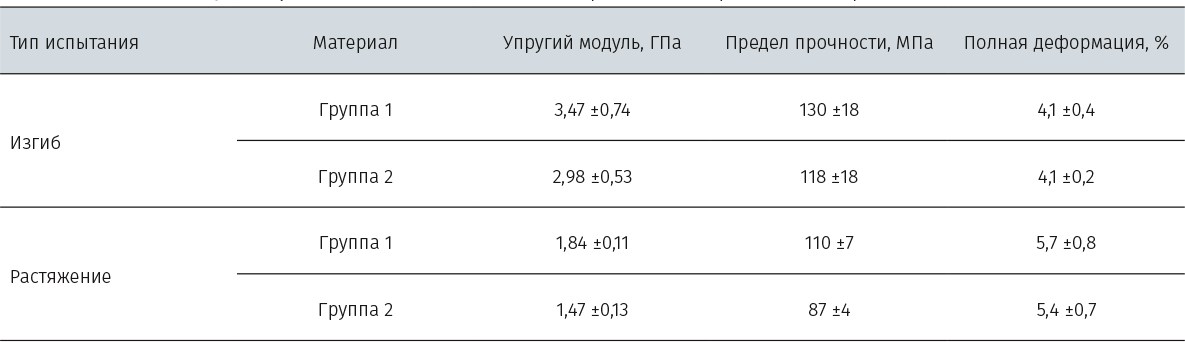
Таблица 1. Результаты механических испытаний при одноосном растяжении и трехточечном изгибе
Методика испытаний по ГОСТ 11262-2014 — одноосное растяжение. Испытательная машина: Shimadzu AG-X 50kN. Образец: две группы по три образца в виде двухсторонней лопатки. Толщина ~5 мм, ширина ~12 мм, длина рабочей части 80 мм. Скорость нагружения - V=10 мм/мин. Обработку результатов осуществляли, как и в случае при испытании на изгиб при помощи программного обеспечения Trapezium-X.
Результаты испытаний на одноосное растяжение представлены в таблице 1 и на рисунке 4. Разрушение образцов по достижении предела прочности происходило в его рабочей области. Деформационное поведение образцов группы 1 не отличалось от группы 2, тогда как при одинаковой полной деформации, упругий модуль и предел прочности у группы 2 был ниже.
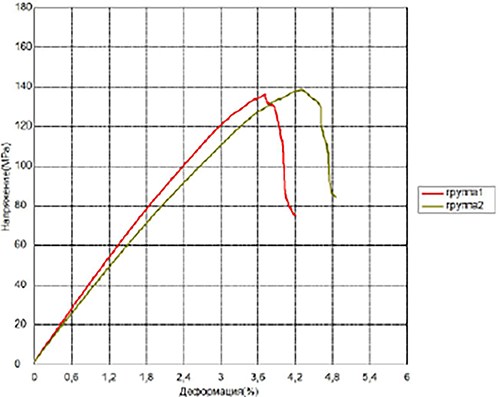
Рисунок 3
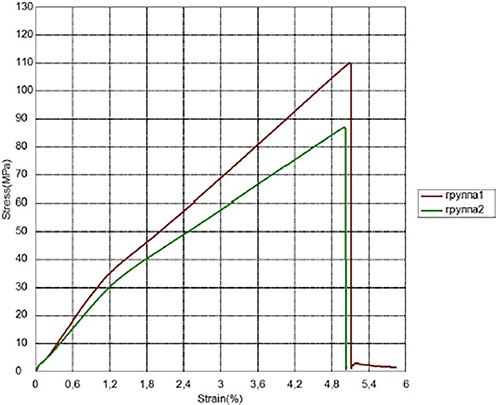
Рисунок 4
Разница в упругом модуле и пределе прочности на растяжение между образцами составила около 20% в пользу образца из группы 1, изготовленного при нормальной рабочей температуре (+20°С).
И наконец, испытания на водопоглощение образцов, выполнены в соответствии с ГОСТ 4650-2014. Два образца были взвешены и помещены в емкость с водой на 10 суток. Через указанный срок их достали и снова взвесили на лабораторных весах. Масса образцов в пределах погрешности прибора практически не изменилась, что говорит о нулевом водопоглощении.
Практическая значимость проделанной исследовательской работы заключается в следующем: изготовление изделий из полимерных композитов на открытом воздухе, к которым не предъявляются требования высокой механической прочности (например — футеровка «мокрым» ламинированием, либо локальные ремонтные работы), допустимо при температурах ниже прописанных в нормативных документах, в частности, до +8°С, при этом процесс полимеризации связующего желательно осуществлять под укрытием с принудительной вентиляцией теплым воздухом.
Список литературы
- Справочник по композиционным материалам. В 2-х кн./ Под ред. Дж.Любина.- М.: Машиностроение, 1988. – 584 с.
- Холодников Ю.В. и др. «Промышленные композиты. Возможности и перспективы»./ Изд. LAP LAMBERT Academic Publishing. GmbH & Co. KG (Германия). 2016. – 455 с.
- ГОСТ 24621-2015. ПЛАСТМАССЫ И ЭБОНИТ. Определение твердости при вдавливании с помощью дюрометра (твердость по Шору).
- ГОСТ 4650 – 2014. ПЛАСТМАССЫ. Методы определения водопоглощения.
- ГОСТ 4648-2014. ПЛАСТМАССЫ. Метод испытания на статический изгиб.
- ГОСТ 11262-2014. ПЛАСТМАССЫ. Метод испытания на растяжение