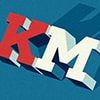
Изготовление легкой матрицы для автотюнинга
рубрика: технологии
Создание улучшенного или нестандартного обвеса для автомобилей, мотоциклов и других видов транспорта, это отдельная ветвь композитного производства, где требуется творческий подход и уникальные условия рабочего процесса. В частности, речь пойдёт о том, как можно делать матрицы для изделий автотюнинга. И как на этом экономить.
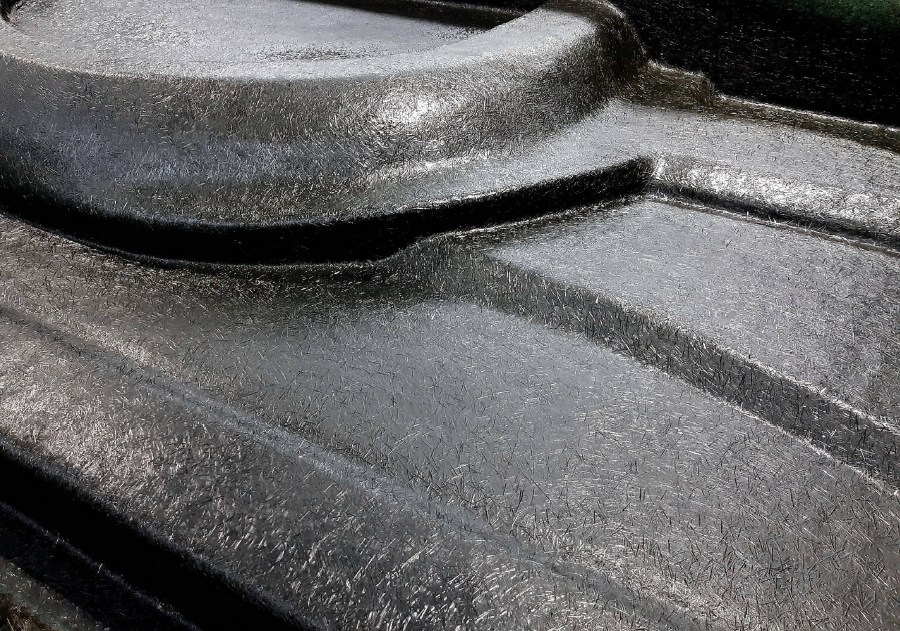
Специфика отрасли определяет как правило низкую нагрузку на матрицу для автотюнинга. Обвесов на авто очень много разных, тюнинг-ателье желательно иметь как можно больше их разновидностей. Значит, должно быть много разных матриц. Но на каждой из этих матриц относительно не часто формуют изделия, и они относительно не большой толщины (3–5 мм). Поэтому нагрузка и износ отдельной матрицы невелики.
Исходя из этих предпосылок, можем несколько видоизменить общие требования к матрицам.
Например, совсем не обязательно применять для их изготовления матричный гелькоут. Подойдет обычный гелькоут для изделий, или даже самый дешевый ортофталевый грунтовочный гель. Его называют грунтовочным, потому что тюнинговые изделия из стеклопластика как правило окрашиваются автоэмалью, а этот гелькоут в данном случае выступает подложкой. И матрица из него будет периодически радовать нас изделиями долгие годы. Конечно, матричный гель более эластичен и лучше сопротивляется образованию усталостных трещин, агрессивному воздействию стирола, поддерживает глянец однажды отполированной поверхности. Но для наших условий эксплуатации вполне хватит физико-механических качеств геля грунтовочного, а глянец нам в принципе не нужен, т.к. изделия перед установкой на автомобиль непременно будут матоваться и окрашиваться автоэмалью в нужный цвет. Единственно, желательно подкрасить гель для матрицы в какой-нибудь цвет пигментом для полиэфиров, чтобы при напылении геля изделия (такого же серого грунтовочного), его можно было различать на поверхности матрицы. Например, мы в данном случае подкрасили гель ядовито-зеленым пигментом.
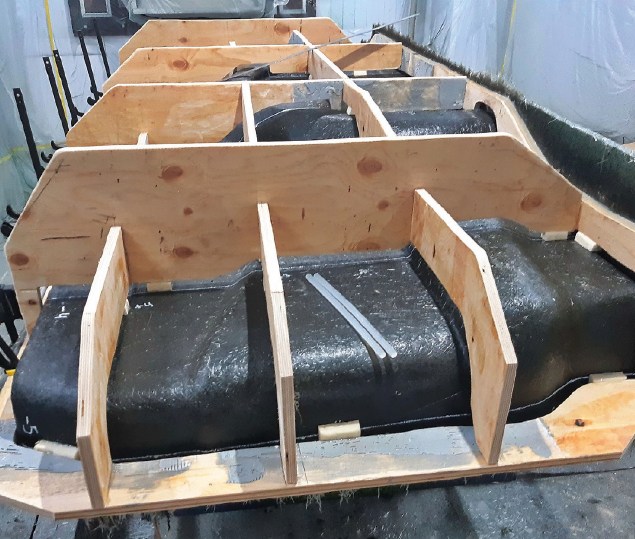
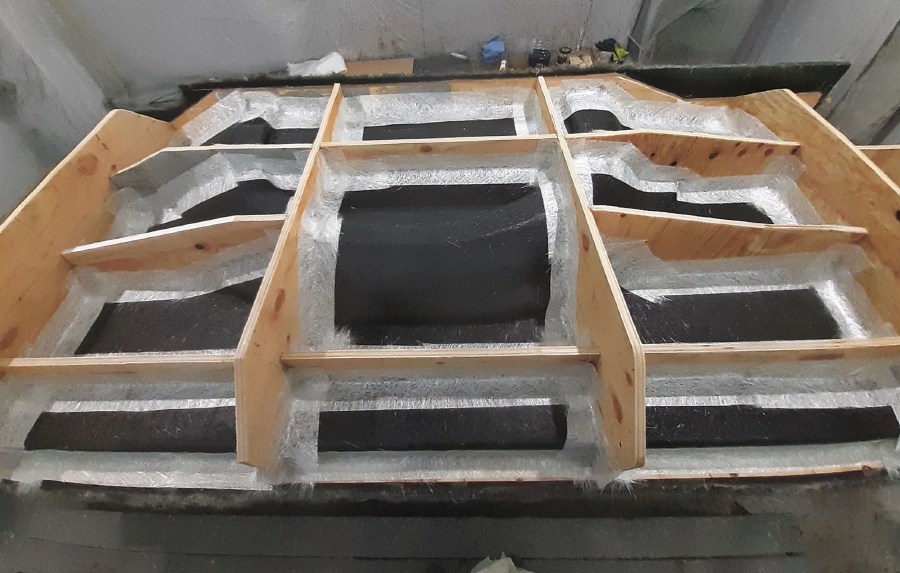
Скинкоут для тюнинговой матрицы вообще ни к чему. Этот слой нужен для постоянно нагревающихся и остывающих матриц, когда в один день на них производится 3–4 формовки или заливки. Следовательно, дорогую винилэфирку выкидываем из списка затрат.
Да и сама смола основного слоя «быстрая матрица» нам не нужна. Ни повышенная толщина ламината с ней, ни ее прочность ни к чему для легких матриц. Формуем тело матрицы обычной конструкционной ортофталевой смолой (желательно — с низкой усадкой). Если изделия будут толщиной 3–5 мм, то матрица может быть не толще 5–7 мм. Для этого достаточно уложить 1 слой стекломата плотностью 300 гр/м2 и 7 слоев стекломата 450 гр/м2. При этом на 1 м2 матрицы мы нанесем 3,5 кг стекла. Однако, для изготовления большого количества тюнинговых матриц, формовка всех этих многочисленных слоев мата вручную — это слишком расточительная особенность производства. Мы решили заменить эту рутину — одним слоем 300-го стекломата и ровингом, накидываемым из чоппера. Обычно первый слой 300-го стекломата укладывается с особой тщательностью на обычной ортофталевой конструкционке. После его отверждения, зачистка колючек и накидывание не толстого слоя ламината из стеклоровинга с той же конструкционной смолой (обычно 0,7–1 кг на м2). После прикатывания, мокрый по мокрому, накидываем всю оставшуюся норму ламината, доведя общий расход до 3,5 кг/м2. Расход стекла контролируем при помощи весов, на которых стоят бобины с выбираемой чоппером нитью. Такой подход намного сокращает время и силы на укладку слоев стекломата.
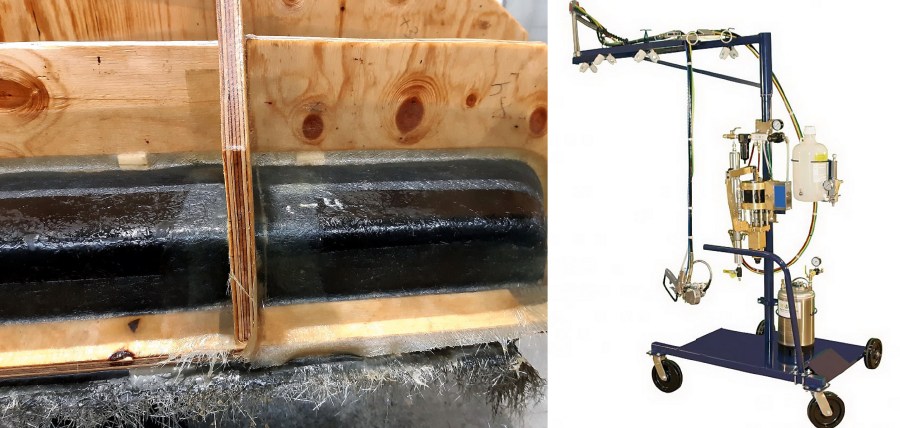
В общем даже смола с высокой усадкой никак не испортит нам матрицу сама по себе. Ну, будет усадка не 6 мм на погонном метре (низкоусадочная), а 8, или 9, это не существенно. Обычно поправка на усадку закладывается в 3D модели.
Самую большую проблему для нас составляет фиксация жесткого каркаса на поверхности нашей тонкой экономной матрицы. Дело в том, что ламинат из обычной дешевой смолы гораздо более склонен к продавливанию ребер жесткости на лицевой поверхности, чем специализированная смола «быстрая матрица».
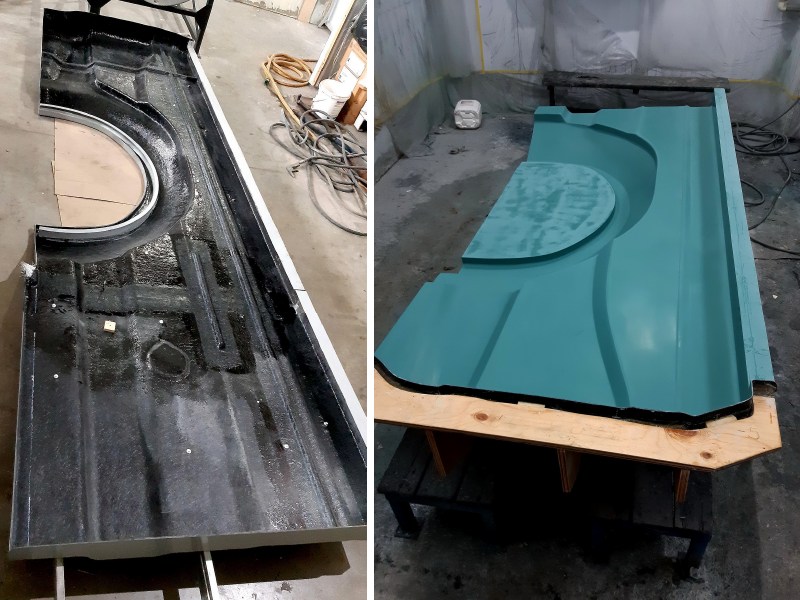
Для того, чтобы никаких продавливаний не происходило, даже при толщине матрицы не 7, а 5 мм, применяем специальный прием: каркас выставляется на сминаемые опоры. В качестве таковых берем кубики пенополиуретана плотностью 30-40 кг/м3. Между силовым каркасом и матрицей образуется просвет 1,5–2 см. Затем методом мокрого угольника приформовываем каркас к матрице. Приформовываем без просветов, по всему периметру, и только в один слой тонкого 300 стекломата. Получается, что, когда происходит усадка отвердевающего ламината угольника, и каркас притягивает к матрице, его в нее не вдавливает, просто сминаются кубики полиуретана. Получившийся слой ламината угольника толщиной всего 0,5 мм не может сделать на матрице толщиной 5 мм сколько-нибудь заметного искривления лицевой поверхности. И вместе с тем, приформовка по всему периметру оказывается очень надежной. Приклеенный таким образом каркас отлично защищает матрицу от деформации и служит удобной подставкой при работе с ней.
Обычно в первый день изготовления матрицы, наносим гелькоут, первый слой 300-го стекломата, и всю толщину из чоппера. На второй день клеим каркас. На третий день расформовка, шлифовка, разделение. Через три дня матрица готова к работе.
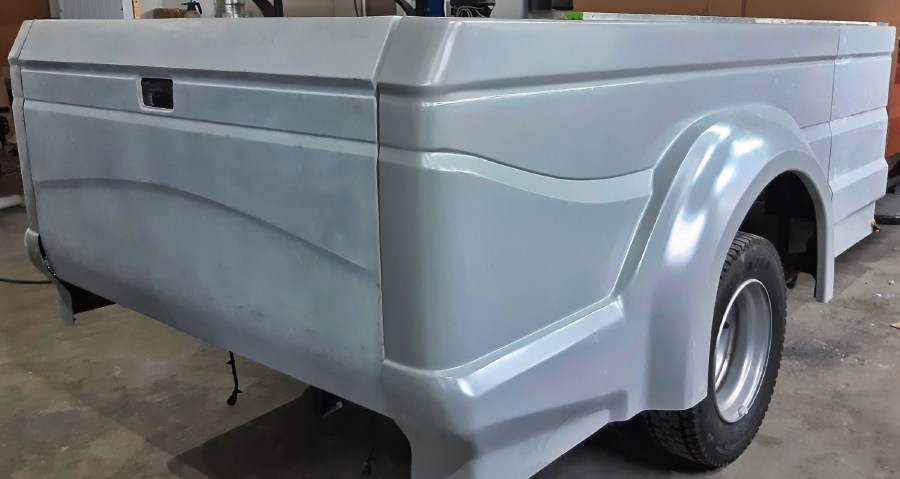
Если каркас, как и модель тюнинговой запчасти, делать в 3D, можно получить четкий быстрый раскрой фанеры на ЧПУ. Собираем каркас перед вклейкой — на термоклей. При вклейке мокрого угольника, за одно покрываем смолой и всю фанеру. Это продлевает срок качественного хранения матриц в любых условиях, в том числе и под открытым небом.
Готовые изделия получаются качественно и быстро.