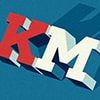
Технологии вторичной переработки полимерных композитных материалов. Современное состояние и развитие на 2020-е годы
рубрика: технологии
Обзор современного состояния и перспектив вторичной переработки полимерных композиционных материалов такими методами, как механическая переработка, термическая и химическая.
Не так давно произошли важные события, которые привели к значительному усилению социотехнического давления на разработку решений по переработке полимерных композитных материалов (ПКМ), а именно: запрет на захоронение композитных материалов в Германии в 2009 году, первая крупная волна завершения срока службы и вывода из эксплуатации композитных ветряных турбин в 2019–2020 годах, ускорение вывода из эксплуатации самолетов из-за пандемии COVID-19 и увеличение количества композитов в автомобилях массового производства.
Еще в 2014 году в журнале Reinforced Plastics писали, что препятствием для более широкого использования армированных стекловолокном и армированных углеродным волокном композитов является отсутствие технологий по переработке. Более широкое использование углепластиков и стеклопластиков в промышленности в сочетании с ограничениями и запретами на захоронение отходов привело к необходимости разработки эффективных технологий переработки этих композитов. Логично заключить, что такое социотехническое давление будет только расти в ближайшие годы [1, 2, 3].
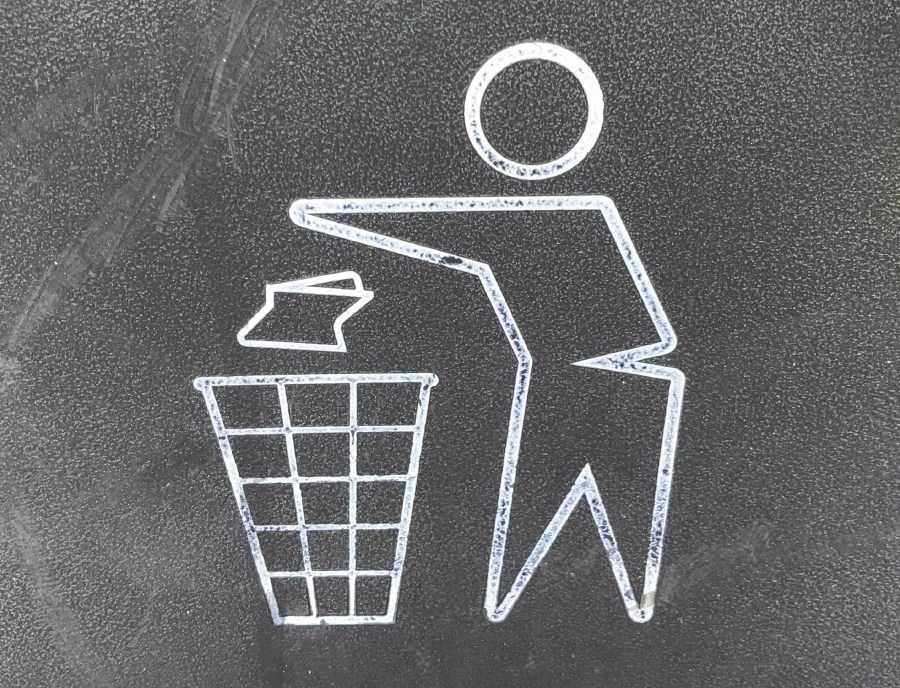
Отрасли, в которых композиты применяются в значительных объемах
Международная ассоциация воздушного транспорта (IATA) провела оценку вывода из эксплуатации 11 000 самолетов в следующие 10 лет. Пандемия COVID-19 очень сильно ограничила авиаперелеты, что ускорит вывод этого числа самолетов из эксплуатации и сделает тему утилизации еще более важной. Кроме того, содержание композитных материалов, используемых в самолетах, за последние десятилетия значительно выросло, что можно увидеть на примере коммерческих самолетов Airbus и Boeing. Например, использование композитных материалов (мас. %) в линейке коммерческих самолетов Airbus: А300 (4,5 мас. %, 1971–2007 гг. выпуска), А310 (6 мас. %, 1983–1998 гг. выпуска), А320 (10 мас. %, 1986 по настоящее время), A340 (13 мас. %, 1991–2011), A380 (25 мас. %, 2003 по настоящее время), A350 (53 мас. %, 2010 по настоящее время) и в линейке Boeing: B777 (12 мас. %, с 1993 г. по настоящее время) и B787 (50 мас. %, с 2007 г. по настоящее время). Например, у Airbus A380 есть следующие композитные детали, изготовленные из углепластика: внешние закрылки, J-образная носовая часть, центральный кессон крыла, нервюры крыла, задняя прижимная перегородка, балки пола для верхней палубы и т.д. Кроме этого, в авиастроении часто используют композиты, сочетающие в себе комбинации различных видов армирующих волокон: углеродных, арамидных, стеклянных [1, 4].
В автомобильной промышленности композиты используются в производстве спортивных автомобилей, что позволяет достигать высоких рабочих характеристик при малом весе. Недавние разработки в области мобильности проложили путь к технологиям электрических двигателей и автономных направляющих. Эти транспортные средства нуждаются в легком весе для достижения более длинных интервалов между подзарядками (электромобили), что создает новый драйвер для технологий крупносерийного производства композитов и способов их утилизации по окончанию срока службы. Уже сейчас в конструкции автомобиля Volkswagen Golf 2016 года используются композитные элементы (композитные каркасы сидений и композитные панели пола), а также в его кузове (например, композитные передние крылья и композитная задняя дверь). Важнейшая задача, которая сейчас стоит перед автомобилестроителями — это создание более экономичных, а также легковесных автомобилей. Применение углепластика в автомобильных деталях снижает вес стандартного автомобиля на 30%. Невозможно переоценить и необходимость экологической ответственности. По отношению к автомобильной промышленности законодательство Европейского союза (ЕС) требует, чтобы 85% транспортного средства подлежало вторичной переработке [2].
Композиты применяются как перспективная технология в шельфовой индустрии, как это видно на примере лопастей ветряных турбин и нефтяных скважин с более глубокими райзерами. В военно-морском кораблестроении композиты используются для достижения специальных свойств, которые важны именно для военного применения. Это немагнитные свойства для тральщиков и радиопрозрачность (незаметность для радаров). Композиты, изготовленные методом напыления рубленного ровинга на протяжении многих лет использовались для изготовления прогулочных судов, но в последнее время в этой области стали все чаще использоваться композиты, армированные непрерывными волокнами, благодаря развитию инженерных методов и инструментов, которые обеспечивают более точное проектирование, конструирование и производство [1, 2].
В ветроэнергетике композиты используются в лопастях благодаря их высокой удельной прочности. Ожидаемый срок службы турбин первой крупной волны ветроэнергетики 1990-х годов истекает в настоящее время. Таким образом, надвигается проблема утилизации лопастей из стеклопластика с истекшим сроком годности: в 2019 и 2020 годах уже должны были быть переоборудованы турбины общей производительностью около двух гигаватт. Например, Дания, которая была одним из основных игроков на рынке энергии ветра, становится одной из первых стран, столкнувшейся с проблемой массовой утилизации. Проблема утилизации композитных лопастей ветряных турбин экологически безопасным способом с каждым годом становится все острее. С увеличением использования возобновляемых источников энергии возрастает и количество отходов лопастей ветряных турбин. Согласно опубликованным данным ожидается, что использование отходов лопастей вырастет с 1 000 000 тонн в 2020 г. до 2 000 000 тонн в 2030 г., увеличившись вдвое в текущем десятилетии 2020-х годов. Прогнозируется, что четверть этих отходов по окончанию срока службы материалов придется на Европу.
Большинство роторов турбин имеют три лопасти размером от 12 м (первые ветряные турбины) до 80 м в длину, а некоторые современные — даже больше. Примеры более длинных лопастей это Siemens Gamesa Renewable Energy (SGRE) — ветряные турбины мощностью 14 МВт с лопастями IntegralBlades длиной 108 м. Многие из этих лопастей скоро превратятся в «отслужившие» элементы. Утилизация этих старых лопастей является главным приоритетом для ветроэнергетики. Эта проблема требует как логистических, так и технологических решений для разборки, сбора, транспортировки и переработки композитных конструкций [1, 3].
Текущие промышленные решения для композитных материалов по окончании срока службы
У многих композитных конструкций срок службы близится к концу. Возникает естественный вопрос: что делать с «отработанными» композитными материалами? Это приводит к трем основным вариантам: захоронение отходов, сжигание или переработка. «Можно ли переработать детали из термореактивного композита по окончанию срока службы и производственные отходы? Есть ли компании, предлагающие эту услугу?» Частота этих вопросов растет с каждым годом, указывая на то, что промышленность композитов и ее клиенты больше не довольствуются традиционными способами утилизации, такими как захоронение и сжигание отходов. За этой тенденцией стоят и политические факторы: традиционные способы утилизации, такие как захоронение и сжигание, становятся все более ограниченными и запрещенными, а компании производящие композиты и их клиенты ищут более надежные решения, согласно данным Европейской ассоциации производителей композитов (EuCIA) [1].
На рисунке 1 представлено негативное влияние каждого из способов утилизации на окружающую среду, экосистему и здоровье.
![Рисунок 1. Влияние захоронения, сжигания и переработки отходов на окружающую среду, экосистему и здоровье [5]](/articles/61c2dcfb8606de0019d92093/source/shy5kmhpqhlcagjf96ecol.jpeg)
Рисунок 1. Влияние захоронения, сжигания и переработки отходов на окружающую среду, экосистему и здоровье [5]
Захоронение на мусорных полигонах
Мусорные полигоны — это относительно дешевый, но и наименее предпочтительный способ утилизации отходов в соответствии с Рамочной директивой Европейского Союза (ЕС) по отходам. Свалки композитных отходов уже запрещены в Германии с 2009 года и ожидается, что другие страны ЕС также пойдут по этому пути. Тем не менее, во всем мире большая часть производственных отходов ПКМ по-прежнему вывозится на свалки. В Нидерландах согласно третьей редакции Национального плана управления отходами захоронение композитных отходов запрещено «в принципе». Однако операторы ветряных электростанций могут получить «исключение», если стоимость альтернативной обработки превышает 200 евро за тонну. Согласно исследованию, проведенному WindEurope, стоимость механической переработки лопастей ветряных турбин в Нидерландах колеблется в пределах 500–1000 € за тонну, включая предварительную резку на месте, транспортировку и обработку. Сама механическая переработка стоит 150–300 €/т, поэтому захоронение отходов все еще практикуется [1, 3].
Сжигание отходов
Сжигание — это процесс переработки отходов, основанный на сжигании органических веществ, содержащихся в отходах. Это еще один распространенный метод утилизации полимерных композиционных материалов. После сжигания 50% композитных отходов остается в виде золы и подлежит захоронению.
В ближайшие годы также ожидается рост стоимости сжигания отходов. Многие инициативы были посвящены механической переработке композитов из стекловолокна. В этом случае композитные отходы разбиваются, а затем измельчаются на мелкие частицы. Полученная смесь волокна, полимера и добавок затем повторно используется в других продуктах: в качестве наполнителя в формовочных смесях (SMC/BMC), а также для армирования асфальта и бетона [6].
Метод переработки в цементных печах (совместная переработка с цементом)
Один из способов утилизации композитных отходов, который изучается уже в течение нескольких лет — использование отходов ПКМ в качестве альтернативного топлива в цементной промышленности. Это один из многообещающих методов, поскольку в ходе процесса 100% композитных отходов «восстанавливается» в виде энергии и сырья. В результате чего приблизительно 67% (минеральная часть композита, то есть кремнезем, карбонат кальция, глинозем и т.д.) «встраивается» в клинкер (промежуточный продукт при производстве цемента), а около 33% превращается в энергию (органическая полимерная матрица). Такая переработка отходов стеклопластика не оказывает отрицательного влияния на качество производимого цемента.
В Германии действует предприятие промышленного масштаба CompoCycle, которое собирает композитные отходы и компоненты по окончании срока службы (например, отработанные лопасти ветряных турбин) для использования на цементном заводе, принадлежащем Holcim – одной из ведущих цементных компаний в мире. CompoCycle начала свою деятельность по переработке композитов в 2009 году с проекта по утилизации больших лопастей ветряных турбин и установления партнерства с Holcim в Германии. В 2010 году Zajons получила одобрение на строительство перерабатывающего завода мощностью 60 000 т/год с инвестициями в размере 6 миллионов евро. Датская пултрузионная компания Fiberline Composites начала поставлять свои производственные отходы стеклопластика в Zajons в рамках программы по сокращению и переработке отходов, цель которой – свести к нулю захоронение отходов на свалках [3, 6].
Переработка отходов
Энергопотребление, связанное с методами переработки композитов, разбито от наивысшего к самому низкому: химическая переработка (21–91 МДж/кг); пиролиз (24–30 МДж/кг); СВЧ пиролиз (5–10 МДж/кг); механическая переработка (0,1–4,8 МДж/кг).
Переработка ПКМ может быть выполнена без разделения волокна и матрицы. В этом случае материал может быть, например, измельчен и повторно использован в качестве наполнителя для использования в других материалах. Однако при этом способе часть стоимости материала теряется из-за неполного использования свойств материала, полученного в процессе переработки. Другие методы переработки включают отделение матрицы от волокон. Такие процессы более сложны и дороги, но имеют большую ценность, поскольку в результате этого появляется возможность изготовления новых деталей или конструкций, в которых восстановленные компоненты могут проявить часть своих первоначальных свойств.
Стоит отметить, что из двух основных составляющих фаз (волокна и матрица) волокна обычно являются наиболее ценными. Тем не менее, переработка матричного материала может быть выгодной при условии, что затраты на процесс переработки не превышают затраты на покупку нового материала. Это вводит еще одну подкатегорию методов переработки: те, которые позволяют повторно использовать волокна, и те, которые позволяют повторно использовать матрицу [1].
Рециклинг различных типов ПКМ
В этой статье акцент сделан на современное состояние переработки в ПКМ (как с термореактивной матрицей, так и с термопластической матрицей), поскольку это та область, в которой в настоящее время находится основной рынок композитных материалов.
Известно, что композиты, производимые в промышленности, примерно на 1/3 состоят из термопластов и на 2/3 из термореактивных материалов. Несмотря на все достижения и научные разработки в области углеволокна, стеклопластики по прежнему остаются доминирующим армирующим материалом на рынке композитов с долей более 95% в 2017 году, а по состоянию на 2020 год — более 90% . В 2017 году мировой спрос на углеродное волокно составил 70,5 тыс. тонн. С 2010 года годовой темп роста спроса на него составляет 11,45%. Более того, углеродные волокна с каждым годом дешевеют и занимают все большую долю рынка композитов.
Стоит отметить, что существует категория экологически чистых композитных материалов — биоразлагаемых композитов. Эти материалы имеют относительно короткое время разложения после окончания срока службы и, следовательно, требуют меньших усилий по переработке, поскольку их можно утилизировать в среде, в которой они могут быстро разлагаться. Однако эти композиты не так широко распространены; кроме того, небиоразлагаемые композиты представляют собой гораздо более сложные технические проблемы, чем их биоразлагаемые аналоги, поэтому биоразлагаемые композиты не обсуждаются подробно в этой статье.
По сравнению с быстроплавкими термопластиками термореактивные композиты имеют сшитую структуру, которая не может быть повторно расплавлена (расформирована). Некоторые термореактивные полимеры, такие как полиуретан, можно легко превратить в исходный мономер. И наоборот, коммерчески доступные термореактивные смолы, такие как полиэфирная и эпоксидная смола, трудно деполимеризовать в их исходные мономеры. Уже сейчас можно предположить, что полное восстановление волокон из отходов ПКМ, станет по-настоящему прорывной технологией и спасением для композитной отрасли. Вторичное волокно имеет дополнительную рыночную стоимость из-за низкого потребления природных ресурсов, энергии и рабочей силы, а также близкого к первичному качества. Что касается направлений в исследованиях, которые сейчас ведутся во всем мире, наибольшее распространение получили сольволиз (24%), пиролиз (31%) и механическое измельчение (18%). 20% составляют так называемые «прочие» технологии. На рисунке 2 показаны основные направления утилизации и переработки термореактивных композитов. Захоронение и сжигание мы обсудили выше в этой статье. Механическая переработка состоит из процессов механического измельчения для уменьшения отходов до вторичного использования. Термическая переработка включает термические процессы для разложения отходов материала и получения энергии, а химическая переработка включает растворение матрицы в реактивной среде [1, 2, 3].
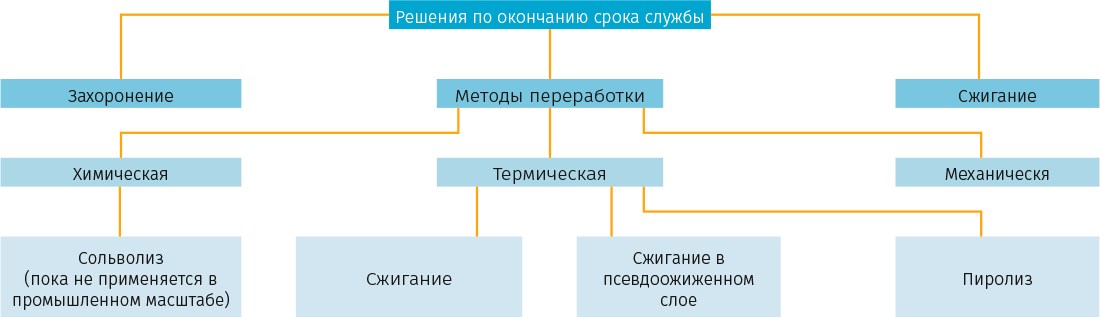
Рисунок 2. Схема сценариев переработки ПКМ, армированных углеродным волокном/стекловолокном, по окончанию их срока службы
Механическая переработка
На первом этапе механической переработки композитные отходы измельчаются на более мелкие части, также называемые рециклатами. Впоследствии различные фрагменты сортируются. Низкоскоростные режущие или измельчающие мельницы измельчают материал до 50–100 мм. Если композитные отходы однородны и не содержат металлических компонентов, используется высокоскоростное измельчение для уменьшения размера от 50 мкм до 10 мм. Таким образом, рециклаты делятся на грубый рециклат с более высоким содержанием волокна и мелкий рециклат с более высоким содержанием смол. В настоящее время все исследования в основном сосредоточены на армированном полиэфирном стеклопластике. Это связано с тем, что рециклаты и их повторное использование применяются в малоценных применениях, таких как наполнение бетона, например. Важным аспектом здесь является цена — углеволокно дороже по сравнению со стекловолокном. Нарушение физической целостности углеволокна из-за механической переработки может привести к экономическим потерям и потерям волокна. С самого начала разработки этого процесса он имел серьезные недостатки, хотя исследования некоторых авторов показали улучшение прочности бетона на изгиб после добавления переработанного наполнителя из стекловолокна. Однако другие учение показали, что использование рециклатов стекловолокна в качестве наполнителей неэкономично из-за доступности других наполнителей, таких как карбонат кальция или кремнезем, в качестве альтернативы. Однако, в последнее время в этом направлении есть заметный прогресс. Некоторым ученым и инженерам удается отделять 70% стекловолокна с помощью обычной молотковой мельницы. Оставшиеся 30% отходов затем измельчают и используют в качестве наполнителя для термопластов. В исследовании других ученых описывается, как отходы аэрокосмической промышленности дробились с помощью молотковой мельницы с последующим измельчением. Рециклаты были спрессованы в плоские поддоны и подвергнуты механическим испытаниям, которые показали снижение механических свойств не менее чем на 50–60% по сравнению с исходным композитом. По мере уменьшения размера частиц рециклата углеродного волокна, его механические свойства увеличиваются. Одним из важных аспектов более рационального предложения по механической переработке как стеклопластика, так и углепластика является то, что более высокий уровень рециркуляции более энергосберегающий, но при этом плато все же достигается при определенной скорости переработки. Кроме того, было показано, что композитная матрица используется в качестве заменителя топлива, что позволяет сэкономить на использовании других (ископаемых) видов топлива [1, 6, 7].
Термическая переработка
Основная цель процесса термической переработки — отделить волокна от матрицы. Это может быть достигнуто: процессами пиролиза, процессами пиролиза в псевдоожиженном слое и процессами микроволнового пиролиза. В этих процессах для разрушения композита используется тепло. Из-за высокой рабочей температуры 450–700°C незначительные летучие материалы сгорают, а ценные волокна остаются. Обычно температура процесса зависит от типа смолы, которая содержится в отходах. Следует отметить, что неподходящая температура может привести либо к обугливанию поверхности волокна, либо к уменьшению диаметра восстановленных волокон. Однако серьезным недостатком этих процессов является то, что в процессе сжигания в качестве побочного продукта образуется зола. Эту золу можно захоронить только как так называемые инертные отходы, которые наносят ущерб развитию экономики замкнутого цикла. Контролируемое разложение смолы при оптимальной температуре может привести к извлечению углеродного волокна с незначительным повреждением поверхности. В работах некоторых исследователей описано термическое разложение смол при 450°C в течение 2 часов. Углеродное волокно было переработано без значительного повреждения поверхности. В отличие от углеродного волокна, термическая обработка стекловолокна в условиях высоких температур (300–600°C) снижает прочность полученного стекловолокна до 80%, и в дальнейшем его трудно использовать из-за низкого потенциала армирования.
ELG Carbon Fiber — первая в мире компания-переработчик углеволокна. Процесс ELG Carbon Fiber (модифицированный пиролиз) первоначально включает в себя удаление металла и резку крупных конструкций до размеров, подходящих для последующей обработки. Затем для восстановления применяется модифицированный пиролиз (смола выгорает). Углеволокно измельчается, собирается в полотна нетканого материала или гранулируется. Сырьем в основном являются неиспользованные препреги, но этот процесс также подходит для отвержденных производственных отходов и материалов по окончанию срока службы [1. 7].
Химическая переработка
Химическая переработка определяется как процесс, в котором полимеры химически превращаются в мономеры или частично деполимеризуются в олигомеры посредством химической реакции. Полимерная матрица, присутствующая в композитных отходах, разрушается путем растворения ее в химическом растворе. Химическая переработка в основном используется для углепластиков. В зависимости от состава полимерной основы выбираются подходящие химические вещества и растворители. Кроме этого, твердые композиты перед химической обработкой шлифуют для получения большей площади поверхности. После растворения полимерной матрицы переработанные волокна промывают для удаления незначительных остатков на поверхностях. Восстановленные волокна сохраняют длину волокна и первоначальные механические свойства. Что касается процессов химической рециркуляции смолы, разложение происходит либо с помощью растворителей путем сольволиза, либо с помощью воды путем гидролиза. В случае сольволиза используются различные растворители, подбираются подходящие условия и концентрации. В процессе гидролиза для разложения смолы используется вода. Использование вредных и концентрированных химикатов может привести к значительному негативному воздействию на окружающую среду, поэтому в условиях сольволиза в сверхкритических жидкостях химические вещества должны быть заменены водой и спиртом.
Есть исследования, демонстрирующие разложение ПКМ на основе эпоксидной смолы, армированной углеродным волокном, в расплавленном гидроксиде калия. Углепластики разлагаются при атмосферном давлении при температурах от 285 до 330°C. Другие ученые используют сольволиз в сверхкритических жидкостях (воды с температурой выше 374°C и давлением выше 221 бар). Этот метод в основном применяется к углепластикам для извлечения волокон хорошего качества [1, 8, 9].
Преимущества и недостатки методов химической и термических методов переработки отражены в Таблице 1.
![Таблица 1. Преимущества и недостатки методов переработки углеродных волокон [9]](/articles/61c2dcfb8606de0019d92093/source/ztr9x8sql0lw8u9q8pxh7e.jpeg)
Таблица 1. Преимущества и недостатки методов переработки углеродных волокон [9]
Влияние переработки на свойства волокон и примеры повторного применение
Свойства восстановленных углеродных волокон
В настоящее время проводится оценка растущего спроса на более дешевые углеродные волокна (менее 20 евро/кг в качестве цены на простейшую форму углеволокон). Композиты, армированные углеродным волокном (углекомпозит), все чаще используются в различных отраслях промышленности. Мировой спрос на углепластик прогнозируется на уровне 121 015 тонн на 2020 год. Это на 11% больше по сравнению с 2019 годом. Например, только в Европе ежегодно производится 17 миллионов автомобилей. На каждую машину требуется в среднем 120 кг пластика, 20% из которого составляют композит. Однако трудно заменить чистое углеволокно переработанным материалом, потому что переработанное углеволокно — это совсем другой материал (легкий и пушистый), и, к тому же, сложный в обращении. ELG Carbon Fiber Ltd. (ELG) начала производить материалы из переработанного углеродного волокна. Кроме того, в 2017 году компания расширила сертификацию своей системы управления качеством до стандарта BS: EN9100 2016 (AS9100 Версия D). Это особенно важно, так как от этого зависит проектирование и разработка, в частности для крупномасштабных применений в автомобильной промышленности. Потенциал снижения стоимости армирования волокном составляет около 40%. Согласно ELG переработанное волокно сохраняет 90 процентов прочности на разрыв, без изменения модуля. Компания CFK Valley Stade Recycling GmbH & Co. KG предлагает различные переработанные углеродные волокна, получаемые в процессе пиролиза углепластика. Сухие волокна и затвердевшие детали и препреги из углепластика сортируются по длине волокон и стадии обработки. Рубленые волокна имеют среднюю длину от 6 до 80 мм. Достигнуты прочность на разрыв >3500 МПа и модуль упругости при растяжении >230 ГПа. Кондиционирование поверхности волокна проводится с учетом потребностей заказчика. У компании есть индивидуальные контракты, например, с Airbus и Bugatti.
Сольволиз является наиболее подходящим методом переработки углеродных волокон, поскольку в ходе него потребляется меньше энергии и получают высококачественные переработанные углеродные волокна. К сожалению, переработка с помощью сольволиза в сверхкритических жидкостях не является самым экологически чистым процессом переработки по сравнению с механической переработкой или пиролизом. Однако этот процесс дает возможность производить высококачественное переработанное углеволокно всего за 15–120 минут и может привести к потенциальному повторному использованию матрицы (например, для производства эпоксидной смолы) [1, 2, 10].
В таблице 2 показаны различные значения остаточной прочности на разрыв переработанного волокна по сравнению с первичным волокном.
![Таблица 2. Остаточная прочность на разрыв углеродного волокна по сравнению с первичным волокном [10]](/articles/61c2dcfb8606de0019d92093/source/ab3jxy101ymynul1m0eo4e.jpeg)
Таблица 2. Остаточная прочность на разрыв углеродного волокна по сравнению с первичным волокном [10]
Еще один фактор, который следует учитывать, — это то, что длина переработанных волокон может варьироваться. Наивысшие значения прочности на разрыв получены для волокон, произведенных путем химической переработки, а самые низкие - при механической переработке. Волокна, изготовленные с помощью пиролиза, имеют промежуточные значения. Кроме того, переработанные волокна могут иметь различное количество остатков смолы. Можно сделать вывод, что переработанные волокна не такие чистые и однородные, как первичные волокна. Следовательно, им необходима постобработка.
Свойства восстановленных стекловолокон
В Университете Стратклайда в Шотландии разработали процесс восстановления прочности термически переработанного стекловолокна, который является многообещающей технологией. Разработка экономически жизнеспособного процесса восстановления механических свойств термически переработанных стекловолокон будет иметь серьезные технологические, социальные, экономические и экологические последствия. Ионообменный метод химического упрочнения волокон из E-стекла был кратко упомянут Кеннерли в его докторской диссертации, в которой говорилось об увеличении средней прочности отдельных волокон на 16% для волокон из E-стекла, которые перед восстановлением были повреждены или подвергнуты термообработке при 450°C [12]. Другие ученые использовали термическое кондиционирование в комплексе с обработкой горячим NaOH. Результаты показали, что при воздействии температур, которые обычно встречаются в процессах термической переработки стеклопластика, стеклопластик теряет 80% или более своей прочности, что делает его непригодным для повторного использования в качестве армирующего компонента. Испытание на растяжение одиночного волокна показало, что до 75% этой потери прочности можно восстановить за счет быстрой обработки в горячем растворе NaOH. Влияние термического кондиционирования на прочность различных армирующих волокон изучали исследователи из Owens Corning Korwin-Edson. Они исследовали волокна S-стекла, E-стекла, кремнезема и базальта после термообработки в течение 1 часа на воздухе в диапазоне температур от 100 до 800°C. У всех волокон наблюдалось снижение прочности при температуре обработки выше 200°C. После кондиционирования при температуре 650°C волокна S-стекла имели самую высокую абсолютную прочность, а базальтовые волокна имели самый низкий уровень сохранения прочности. Однако все волокна показали потерю прочности на 70–80% после 650°C, причем базальтовое волокно оказалось материалом с самым низким значением (относительная потеря прочности составила 97%). В работе переработанное стекловолокно получали из отходов автомобильной промышленности путем пиролиза при 450°C. Потеря прочности на разрыв волокна составила 45%.
![Таблица 3. Сравнение механических свойств углеволокна до и после химической переработки композитов из углеволокна и эпоксидной смолы в нежестких условиях [11]](/articles/61c2dcfb8606de0019d92093/source/lddb09t34e9bz4n5hen4n.jpeg)
Таблица 3. Сравнение механических свойств углеволокна до и после химической переработки композитов из углеволокна и эпоксидной смолы в нежестких условиях [11]
Существует еще один недорогой и эффективный подход к переработке стекловолокна из отходов армированного стекловолокном эпоксидного полимера (стеклопластик), основанный на методе химического окисления с помощью микроволнового излучения. Было обнаружено, что в одностадийном процессе с использованием микроволнового облучения смесь перекиси водорода (H₂O₂) в качестве натурального окислителя и винной кислоты в качестве природной органической кислоты может быть использована для разложения эпоксидной матрицы отработанного стеклопластика с выходом продукта до 90%. Было получено переработанное стекловолокно с приблизительной прочностью на разрыв 92,7%, приблизительным модулем Юнга 99,0% по сравнению с первичными стекловолокнами.
Хотя механическая переработка является рентабельным процессом, она сильно ухудшает механические характеристики волокон. Более того, при использовании процессов пиролиза и псевдоожиженного слоя сообщается о сохранении прочности регенерированных волокон только на 70–75%. В настоящее время достигнуты огромные успехи в химических и электрохимических методах переработки в минимизации повреждения волокон во время процессов рециркуляции и сохранении целостности структуры волокна. В таблице 4 показаны различные значения остаточной прочности на разрыв переработанного стекловолокна по сравнению с первичным стекловолокном [1, 10, 12].
![Таблица 4. Сохраненная прочность на разрыв переработанного стекловолокна по сравнению с первичным стекловолокном [10]](/articles/61c2dcfb8606de0019d92093/source/tiz8z8jsv1g6h6zk64hc5g.jpeg)
Таблица 4. Сохраненная прочность на разрыв переработанного стекловолокна по сравнению с первичным стекловолокном [10]
Области применения отходов композитной отрасли и восстановленных волокон
Вторичное использование переработанных (восстановленных) волокон уже сейчас применяется в автомобиле- и авиастроении. Например, в автомобильном секторе существуют различные области применения переработанных материалов в качестве компонентов экстерьера. В 2012 году BMW Group и Airbus договорились о сотрудничестве по переработке углеродных волокон и разработке методов повторного использования. Измельченные короткие волокна могут быть использованы для изготовления полиэфирного листового прессматериала (SMC), например, для производства задней стойки в серии BMW i7, которая показана на рисунке 3, или для изготовления рамы люка для Mitsubishi Rayon (Toyota).
![Рисунок 3. Задняя стойка кузова из полиэфирного листового прессматериала (SMC, в BMW 7 серии) [13]](/articles/61c2dcfb8606de0019d92093/source/x7wctgf7dg5f25yuz7zjk.jpeg)
Рисунок 3. Задняя стойка кузова из полиэфирного листового прессматериала (SMC, в BMW 7 серии) [13]
![Рисунок 4. BMW i3. До 95% используемых материалов подлежат вторичной переработке [1].](/articles/61c2dcfb8606de0019d92093/source/g97kyjgqwh65bp9e0b3q84.jpeg)
Рисунок 4. BMW i3. До 95% используемых материалов подлежат вторичной переработке [1].
Большие секции лопастей ветряных турбин могут быть повторно использованы в архитектурных или других конструктивных целях. Примеры применений были предложены студией SuperUse в Нидерландах. В городе Роттердам была построена детская игровая площадка площадью 1200 квадратных метров с различными элементами, такими как башня с горками, туннели, пандусы и горки. Для этого использовалось 5 выведенных из эксплуатации лопастей несущего винта.* Другими примерами являются город Тернёзен, где лопасти ротора также использовались для детской площадки и превращались в сиденья в общественном месте, или Алмере (также в Нидерландах) с двумя автобусными остановками. Другими примерами перепрофилирования являются пешеходный мост с использованием ветряных лопастей A29 в качестве основных балок (исследовательский проект Re-Wind) или навесы для велосипедов (рисунок 5).
![Рисунок 5. Примеры перепрофилирования лопастей ротора: навес для велосипедов [3]. Статья об этом применении лопастей ветряных турбин опубликована в Композитном мире №3 (96) 2021](/articles/61c2dcfb8606de0019d92093/source/7cjllnq4nyhi40djod11md.jpeg)
Рисунок 5. Примеры перепрофилирования лопастей ротора: навес для велосипедов [3]. Статья об этом применении лопастей ветряных турбин опубликована в Композитном мире №3 (96) 2021
Другим применением может быть мебель из лопастей ветряных турбин с истекшим сроком службы (рисунок 6). Оптимизация процессов переработки позволит обеспечить удовлетворительные уровни качества и цены по сравнению с первичными композитами, фактически создав рынок для переработанных композитов.
![Рисунок 6. Пример мебели, изготовленной из лопастей ветряных турбин с истекшим сроком службы [1]](/articles/61c2dcfb8606de0019d92093/source/wzbnq5eandfv7do0n0dyf7.jpeg)
Рисунок 6. Пример мебели, изготовленной из лопастей ветряных турбин с истекшим сроком службы [1]
Однако это всего лишь демонстрационные проекты, а не решение, особенно для больших объемов. Кроме того, потребуются текущее обслуживание и ремонт, а для продления срока службы потребуется анализ усталостной нагрузки с использованием данных SCADA в сочетании с проверками на месте. Другая проблема заключается в том, что волокна становятся короче в каждом последующем цикле переработки, что значительно сокращает области их применения.
Огромное количество отходов образуется в авиационной промышленности. Компании, специализирующиеся на разработке и переработке (например, Fokker и Toray), участвовали в проекте, по результатам которого было показано, что использование переработанного углеволокна экономически целесообразно. Boeing согласился сотрудничать с ELG Carbon Fiber для переработки излишков углеродного волокна в аэрокосмической отрасли. При этом образующийся в виде отходов материал собирается на заводах Boeing. Затем в ELG его обрабатывают в печи для удаления связующих полимеров. Наконец, продукт продается третьим лицам.
Кроме того, материалы ELG Carbon Fiber Ltd. (ELG) были использованы для изготовления двухосной тележки для British Rail с добавлением новых волокон в полотна из переработанного углеволокна. Потребовалось три года, чтобы отработать технологию производства, пройти все этапы тестирования и продемонстрировать возможность выхода переработанного углеволокна на рынок.
Таким образом, разработки экологически безопасных технологий переработки композитов, без сомнения, имеют решающее значение для выживания и жизнеспособности композитной отрасли в целом, и ожидается, что такая тенденция будет становиться все более заметной в текущем десятилетии [1, 2, 3, 13, 14].
Список использованных источников
- Krauklis, A.E.; Karl, C.W.; Gagani, A.I.; Jørgensen, J.K. Composite Material Recycling Technology—State-of-the-Art and Sustainable Development for the 2020s. J. Compos. Sci. 2021, 5, 28. ссылка
- Amaechi, C.V.; Agbomerie, C.O.; Orok, E.O.; Ye, J. Economic Aspects of Fiber Reinforced Polymer Composite Recycling. In Encyclopedia of Renewable and Sustainable Materials; Elsevier BV: Oxford, UK, 2020; pp. 377–397.
- WindEurope–Cefic–EuCIA. Accelerating Wind Turbine Blade Circularity. White Paper. May 2020. Available online: ссылка (accessed on 11 November 2020).
- The International Air Transport Association (IATA). Helping Aircraft Decommissioning. 2020. Available online: ссылка (accessed on 17 December 2020).
- Oliveux, G.; Dandy, L.O.; Leeke, G.A. Current status of recycling of fibre reinforced polymers: Review of technologies, reuse and resulting properties. Prog. Mater. Sci. 2015, 72, 61–99. [CrossRef]
- Jacob, A. Composites can be recycled. Reinf. Plast. 2011, 55, 45–46. [CrossRef]
- Pickering, S. Recycling technologies for thermoset composite materials—current status. Compos. Part A Appl. Sci. Manuf. 2006, 37, 1206–1215. [CrossRef]
- 76. Asmatulu, E.; Twomey, J.; Overcash, M. Recycling of fiber-reinforced composites and direct structural composite recycling concept. J. Compos. Mater. 2013, 48, 593–608. [CrossRef]
- 102. Maxime, L. Recycling Carbon Fibre Reinforced Composites: A Market and Environmental Assessment, Paper. 2014. Available online: ссылка (accessed on 2 December 2020).
- Liu, P.; Meng, F.; Barlow, C.Y. Wind turbine blade end-of-life options: An eco-audit comparison. J. Clean. Prod. 2019, 212, 1268–1281. [CrossRef]
- Jiang, J.; Deng, G.; Chen, X.; Gao, X.; Guo, Q.; Xu, C.; Zhou, L. On the successful chemical recycling of carbon fiber/epoxy resin composites under the mild condition. Compos. Sci. Technol. 2017, 151, 243–251. [CrossRef]
- Kennerley, J. Recycling Fibers Recovered from Composite Materials Using a Fluidised Bed Process. Ph.D. Thesis, University of Nottingham, Nottingham, UK, 1998.
- Türrahmen aus SMC für Mittelklassewagen. 2017. Available online: ссылка (accessed on 22 December 2020).
- Simple Flying. What Happens to Waste Carbon Fiber from the Aviation Industry? 2020. Available online: ссылка (accessed on 20 December 2020).