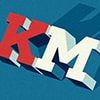
Энергоэффективная печь для плавления базальта
рубрика: технологии
Ежегодный рост производства и потребления базальтового непрерывного волокна, по данным источника [1], составляет 10–14%. Одним из наиболее энергозатратных этапов производства базальтового волокна является высокотемпературное плавление горной породы. Это обосновывает необходимость создания энергоэффективных плавильных реакторов по плавлению базальта.
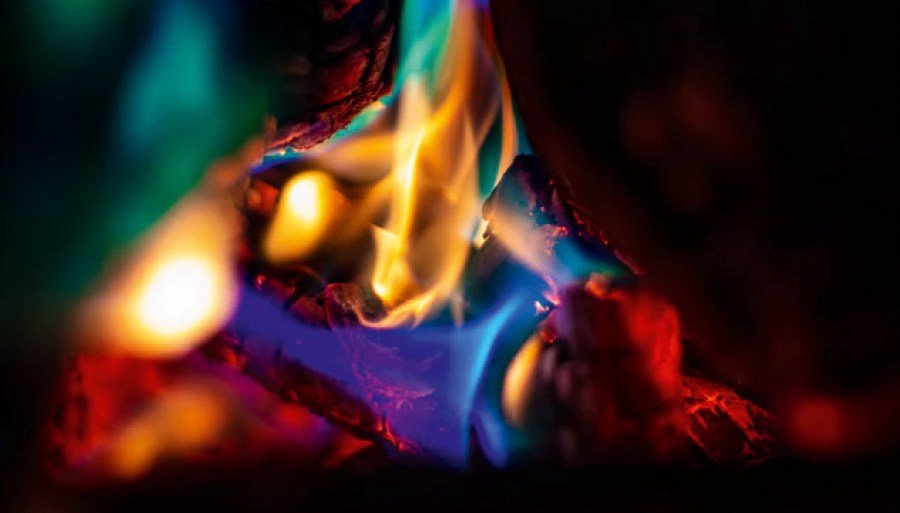
1. Существующие технологии
Сравнение затрат на производство одной тонны базальтового расплава, представленное в интернет-источнике [2], может быть актуализировано с учетом текущих цен на энергоресурсы.
Для расчётов приняты следующие условия:
- состав шихты одинаковый;
- учитываются энергетические ресурсы, необходимые только для процесса нагрева и плавления;
- принято, что стоимость природного газа составляет 4,859 руб/м3, стоимость электроэнергии — 4,43 руб./кВт•ч, стоимость кокса — 11,533 руб/т. Стоимость электроэнергии существенно отличается от 1,11 руб/кВт•ч в Иркутской области до 8,42 руб/кВт•ч в Чукотском автономном округе, что рассчитывается для Хабаровского края как среднее значение и перспективный регион для строительства предприятий по производству композиционных материалов.
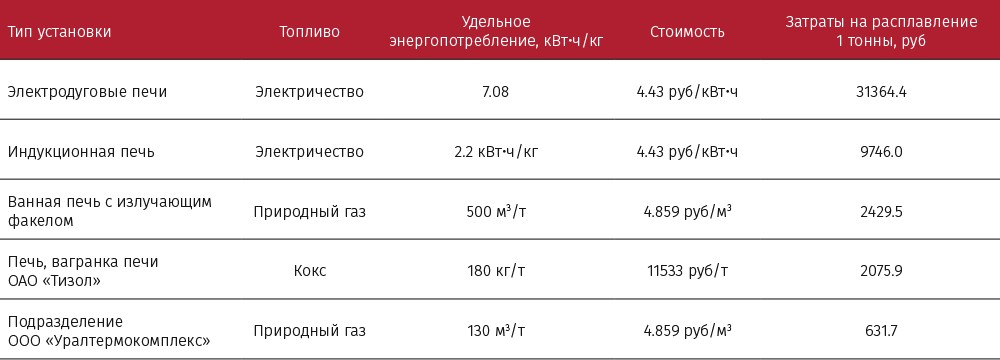
Таблица 1. Затраты энергии на плавление 1 тонны базальта
Результаты расчетов, приведенные в таблице 1, наглядно показывают существенные затраты на плавление базальта.
Теоретический минимум энергозатрат на процесс плавления базальта значительно ниже. При расчете теоретического минимума энергозатрат принимались теплоёмкости в соответствии со справочником [3]. Представлены в таблице 2.
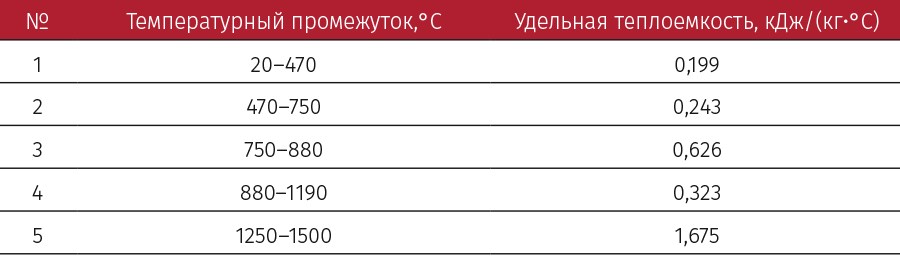
Таблица 2. Удельная теплоемкость базальта в зависимости от температуры
По результатам расчётов теоретический минимум затрат, необходимый для нагрева, плавления и перегрева базальта до температуры 1450°С (наиболее распространённая в действующих печах), составляет 1244 кДж/кг.
Общими принципами конструкций нового поколения должны быть: подогрев поступающих в агрегат материальных потоков отходящими тепловыми потоками; организация непрерывности процесса; применение эффективной футеровки; использование погруженного горения рассредоточенной продувки расплавов [4]; применение кислорода в качестве окислителя; удаление газовых включений из расплавов за счёт снижения давления над расплавом.
2. Предлагаемый вариант энергоэффективной печи
Наибольший вклад в повышение энергетической эффективности теплотехнического процесса плавления базальта вносит теплотехнический принцип погруженного факела, который является одним из способов осуществления тепломассообмена между двумя средами, одна из которых — жидкость (расплав), другая газ.
Принцип погруженного факела предполагает взаимодействие газа и жидкости. Основным отличием этого принципа является мощное механическое взаимодействие двух сред. Это достигается пропусканием горящего газа через весь объем жидкости, что приводит к существенному развитию поверхности газ — жидкость, усилению конвективной составляющей тепломассообмена. Таким образом интенсифицируется теплообмен.
Высокотемпературное барботажное горение внутри расплава создает сложную структуру, включающую твёрдые частицы, жидкость и газ. В ванне расплава образуется большая поверхность теплообмена между продуктами сгорания и расплавом материала. Интенсивное перемешивание расплава приведет к увеличению скорости плавления, а также к однородности технологического продукта. Кроме этого, барботаж расплава снижает общую температуру в пространстве печи над расплавом.
Следующим и ключевым является процесс осветления расплава. Способы осветления или дегазации расплавов известны [5]. Можно выделить основные:
- при атмосферном давлении с повышением температуры расплава;
- за счёт уменьшения высоты расплава;
- вакуумирование расплава.
Представленные выше теплотехнические принципы и технические решения позволили предложить конструкцию реактора (рисунок 1), на способ работы которого получен патент [6].
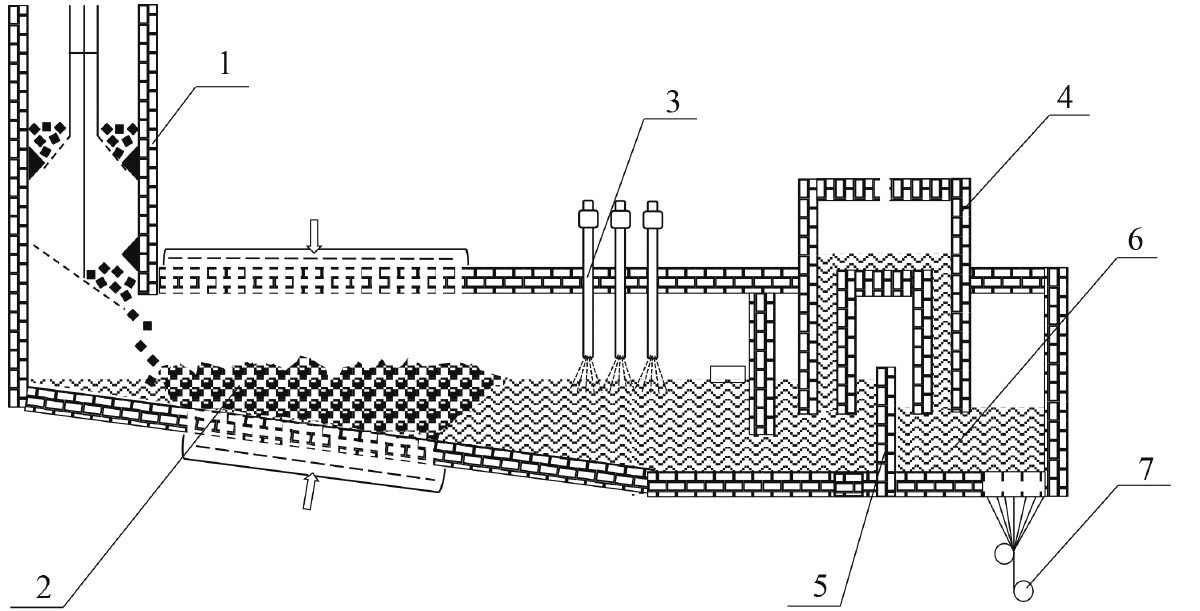
Рисунок 1. Принципиальная схема энергоэффективной печи по плавлению базальта. 1 — устройство для предварительного подогрева базальтовой шихты; 2 — барботажный слой расплава; 3 — устройство для подогрева расплава; 4 — камера осветления расплава; 5 — перегородка, отделяющая осветлённый расплав от неосветлённого; 6 — осветлённый расплав
В соответствии с рисунком 1 перспективная печь должна состоять из устройства 1 для предварительного подогрева базальтовой шихты, выполненного в виде шахты. Конструкция защищена патентом [7]. Задача данного устройства в противоточной схеме подогревать поступающий базальт отходящими из плавильной зоны реактора газами до температуры близкой к температуре плавления (1000–1150°С), которые проходят через перфорированные конуса.
3. Модель разрабатываемой печи
Реальная картина барботажа расплава осложняется множеством факторов, в том числе пузыри взаимодействуют друг с другом, что может приводить как к изменению их формы и траектории движения, так и к слиянию и дроблению. В связи с этим принципиально важным становится демонстрационная физическая модель.
Задача демонстрационных моделей — наглядно показать происходящие процессы. Поэтому при создании физической модели и для обеспечения наглядности конструкции было выбрано органическое стекло, а в качестве жидкости, моделирующей расплав базальта, был выбран глицерин. Поскольку при температуре 5–10°С он имеет вязкость близкую к вязкости базальта при температуре 1400°С. В соответствии с источником [8] вязкость глицерина при 10°С составляет 3,95 Па•с, вязкость расплавов базальта, по данным источника [9], может быть 3 Па•с при температуре 1450°С.
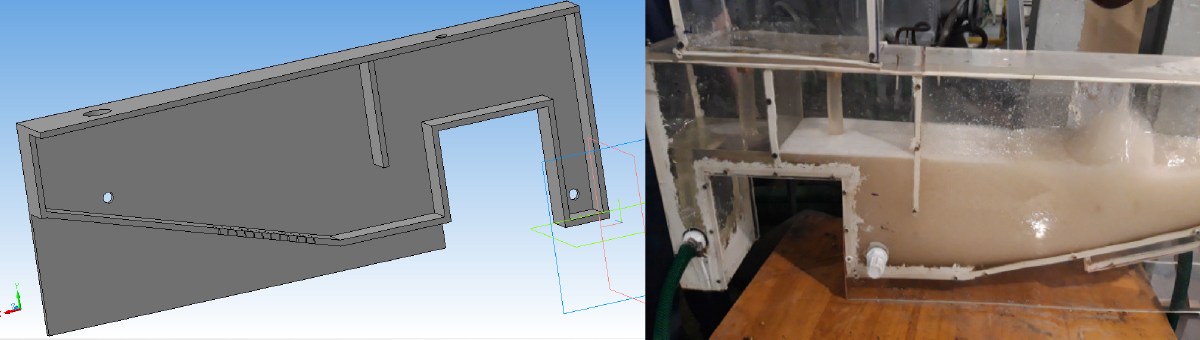
Рисунок 2. Экспериментальная установка
В модели, разработанной в НИУ «МЭИ» на кафедре Энергетики высокотемпературных технологий, предусмотрен перфорированный под (рисунок 2), с помощью которого на промышленных печах будет обеспечиваться интенсификация процесса плавления базальта и гомогенизация расплава. Кроме этого, за перегородкой предусмотрена часть реактора, предназначенная для осветления глицерина, которая позволит значительно сократить размеры агрегата за счёт высокоскоростного осветления расплава.
4. Оценка производительности
Известны [10] данные, полученные опытным путём, в соответствии с которыми применение барботажного режима увеличивает производительность плавильных печей фактически в два раза. С 1000÷1500 кг/(м2•сут) в обычных пламенных печах до 2500÷2 600 кг/(м2•сут) в печах, где осуществляется продувка сжатым воздухом с расходом 17 нм3/(м2•сут). В соответствии с результатами проведённых опытов и опубликованных в источнике [10], использование в качестве энергоносителя при барботаже горючей газовоздушной смеси заметно увеличивало температуру расплава, что позволило снизить температуру пламенного пространства от 1 450°С до 1400°С, увеличив срок службы печи.
В печах с излучающим факелом коэффициент теплоотдачи 700–1200 Вт/(м2•K), а при организации погруженного в расплав факела при теплообмене твердой частицы с минеральным расплавом достигает 3000–4000 Вт/(м2•K) [11]. Что позволяет предположить двукратное увеличение скорости теплообмена, а значит и скорость плавления.
Ещё одним фактором, позволяющим увеличить скорость плавления, является применение базальта меньшей фракции. На сегодняшний день в печи базальт подают размером 20–25 мм, применение фракции в 10 ±5 мм позволит сократить время плавления ещё в два раза.
Следующим ключевым отличием новой печи является подогрев шихты до температуры 1000–1150°С, то есть до температуры предельно близкой к началу плавления. Принимая, что на килограмм непрерывного базальтового волокна требуется 1,18 кг исходного базальта, то нагрев до 1150°С позволит подавать материал, содержащий 390 кДж, а это 27% от необходимого количества теплоты (1 438 кДж на 1,18 кг базальта). Таким образом, период нагрева до температуры начала плавления фактически вынесен за периметр ванны расплава, а значит производительность увеличится ещё ориентировочно на 27%.
Всё выше обозначенное позволит сократить время плавления в 5–6 раз. Возможность столь существенного увеличения производительности доказана на практике в чёрной металлургии, в частности в мартеновских печах стандартное время плавки составляет 5÷6 часов. В конвертерном процессе общая продолжительность плавки в 100–350 тонных конвертерах составляет от 40 до 50 минут [12].
Выше представленные аргументы позволяют оценить ожидаемую производительность перспективного реактора по плавлению базальта в 6250–7500 кг/(м2•сут).
5. Выводы
Растущие потребности в непрерывном базальтовом волокне и конкуренция на рынке требуют создания энергоэффективных печей по плавлению базальта. Создание таких печей возможно при комплексном подходе, обеспечивающем снижение тепловых потерь, в том числе за счёт подогрева до 1000–1150°С поступающего в печь базальта дымовыми газами, а также подачи в печь подогретых до 1000°С газообразного топлива и окислителя, организации барботажа расплава и осветления расплава за счёт создания разряжения.
В НИУ «МЭИ» на кафедре Энергетики высокотемпературных технологий продолжается разработка перспективной плавильной печи для базальта. Сотрудники кафедры заинтересованы в дальнейшей работе с индустриальным партнёром или инвестором. Следующим этапом развития работы может быть создание экспериментальной полупромышленной установки, в которой будет плавиться базальт при организации погруженного в расплав факела. Результаты высокотемпературных испытаний будут использованы для создания энергоэффективных промышленных печей нового поколения.
Благодарность
Работа выполнена в рамках проекта «Прорывные технологии энергоэффективных конструкций плавильных печей барботажного типа» при поддержке гранта НИУ «МЭИ» на реализацию программ научных исследований «Энергетика», «Электроника, радиотехника и IT» и «Технологии индустрии 4.0 для промышленности и робототехника» в 2020-2022 гг.».
Литература
- Оснос М. С., Оснос С. П. Базальтовые непрерывные волокна – основа для создания новых промышленных производств и широкого применения армирующих и композитных материалов / Журнал Композитный мир № 1. 2019 – С. 58-65.
- URL: www.termokomplex.ru 21.06.2020.
- Техническая энциклопедия: справочник физических, химических и технологических величин / главн. ред. Л. К. Мартенс. Том второй: Аэродинамика. Бумажное производство, 1928 – 882 с.
- Ключников А. Д., Кузьмин В. Н., Попов С. К. Теплообмен и тепловые режимы в промышленных печах, М.: Энергоатомиздат, 1990. – 176 с.: ил.
- Панкова Н. А. Исследование механизма процесса осветления стекломассы в промышленных условиях: Дисс. доктора тех. наук. М.: Государственный научно-исследовательский институт стекла. 1978. – 464 с
- Строгонов К. В., Назаров М. Н. 2019 Устройство для изготовления непрерывных базальтовых волокон (Москва: Патент № 2695188 RU)
- Строгонов К. В., Коркоц К. А. Патент 2019 Устройство для предварительного подогрева базальтовой шихты (Москва: Патент № 194480 РФ)
- Лещенко Н. Ф. Технология производства глицерина из жиров и масел и его применение М.: Пищепромиздат, 1998. – 189 с.
- Воронкович Е. Л., Папко Л. Ф. Технологические свойства базальтовых расплавов // IX Всероссийская научно-практическая конференция молодых учёных «Россия молодая» 18-21 апреля 2017 г. URL: science.kuzstu.ru
- Джигирис Д. Д., Махова М.Ф. 2002 Основы производства базальтовых волокон и изделий (М.: Теплоэнергетик) с. 412
- Ключников А. Д., Кузьмин В. Н., Попов С. К. Теплообмен и тепловые режимы в промышленных печах: Учебное пособие для вузов /. – М.: Энергоатомиздат, 1990. – 176 с.
- Воскобойников В. Г., Кудрин В. А., Якушев А. М. Общая металлургия. Учебник для вузов – 5-е изд., – М.: Металлургия, 1998.