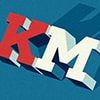
Оценка целесообразности применения 3D-печати в маломерном композитном судостроении
рубрика: технологии
В настоящее время все большее внимание специалистов привлекает возможность изготовления различных изделий с помощью 3D-печати. Публикуется немалое количество материалов, в которых утверждается преимущество этой технологии над многими традиционными методами изготовления как металлических, так и неметаллических изделий.
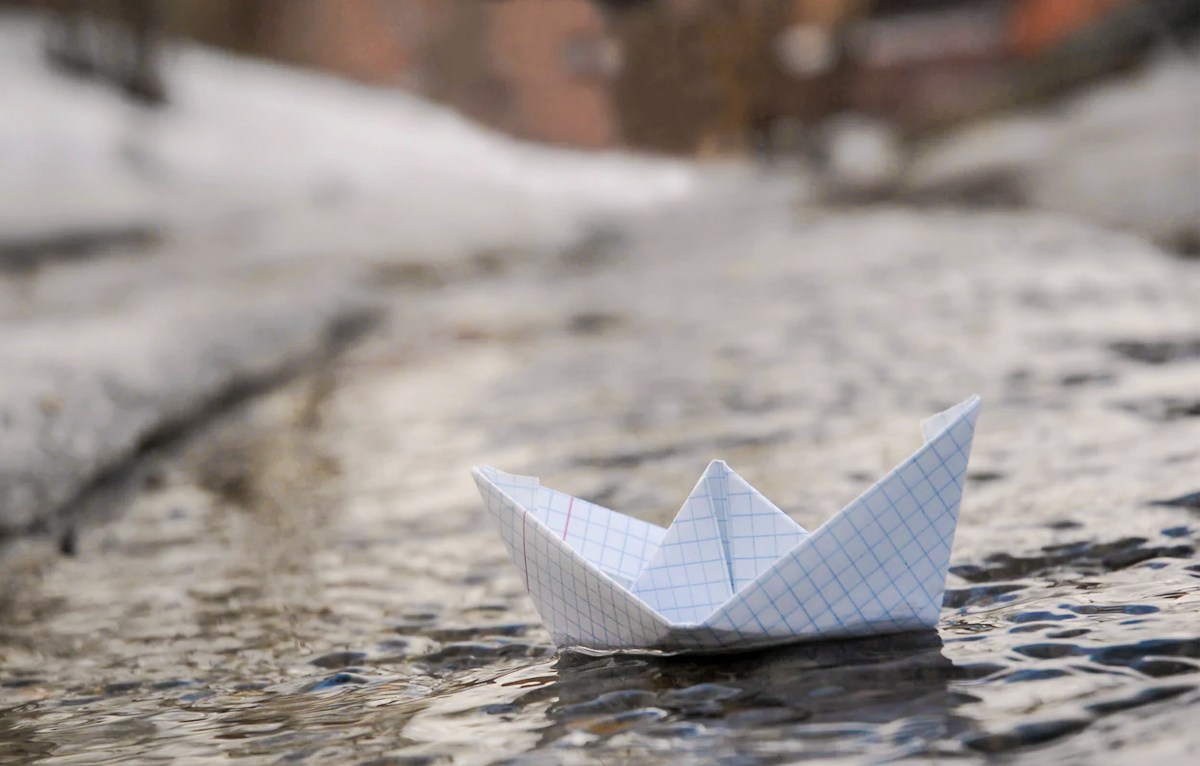
Источник: unsplash.com
В Интернете ведутся дискуссии между сторонниками и противниками новой технологии, отстаивающими полярные точки зрения. Постепенно эти дискуссии стали затрагивать вопросы целесообразности применения 3D-печати в области маломерного судостроения. По мере появления первых опытных образцов, изготовленных по технологии 3D-печати, интерес к этой теме стал только возрастать. Попробуем разобраться, какие выигрыши по сравнению с традиционными технологиями может дать применение нового метода. На сегодняшний день известно два направления по изготовлению продукции судостроительного назначения с помощью 3D-печати. Первым направлением является изготовление оснастки для последующего производства корпуса судна из композиционных материалов. Вторым направлением является изготовление собственно корпуса судна из композиционных материалов (рисунок 1).
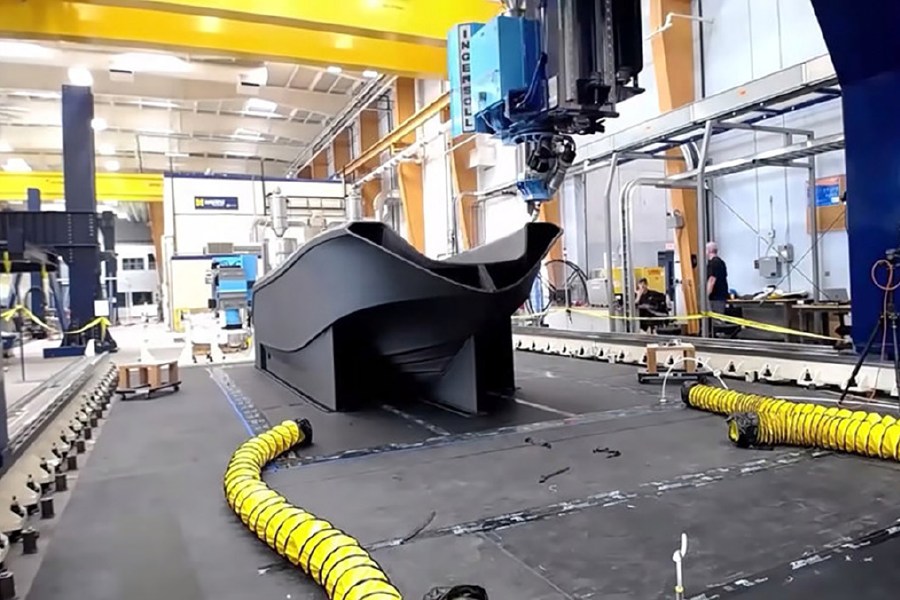
Рисунок 1. Изготовление корпуса катера с помощью 3D-печати
Рассмотрим опыт компании Thermwood, в которой была разработана технология создания оснастки для последующего изготовления корпусов катеров и лодок из композиционных материалов [1]. Специалистами компании был изготовлен портальный станок LSAM, который может работать как 3D-принтер и как фрезерный станок с числовым программным управлением (далее ЧПУ). Особенностью данного технологического процесса является то, что сначала принтер печатает элементы оснастки, а затем головка с ЧПУ обрабатывает их поверхность до необходимой чистоты. Компания Thermwood в сотрудничестве с университетом штата Мэн изготовила оснастку корпуса катера длиной 6,7 м,
состоящую из шести секций: четырех основных центральных секций со стенками толщиной около 4 см, а также кормовой части с транцем и носового элемента со стенками переменной толщины. Общий вид оснастки корпуса представлен на рисунках 2 и 3.
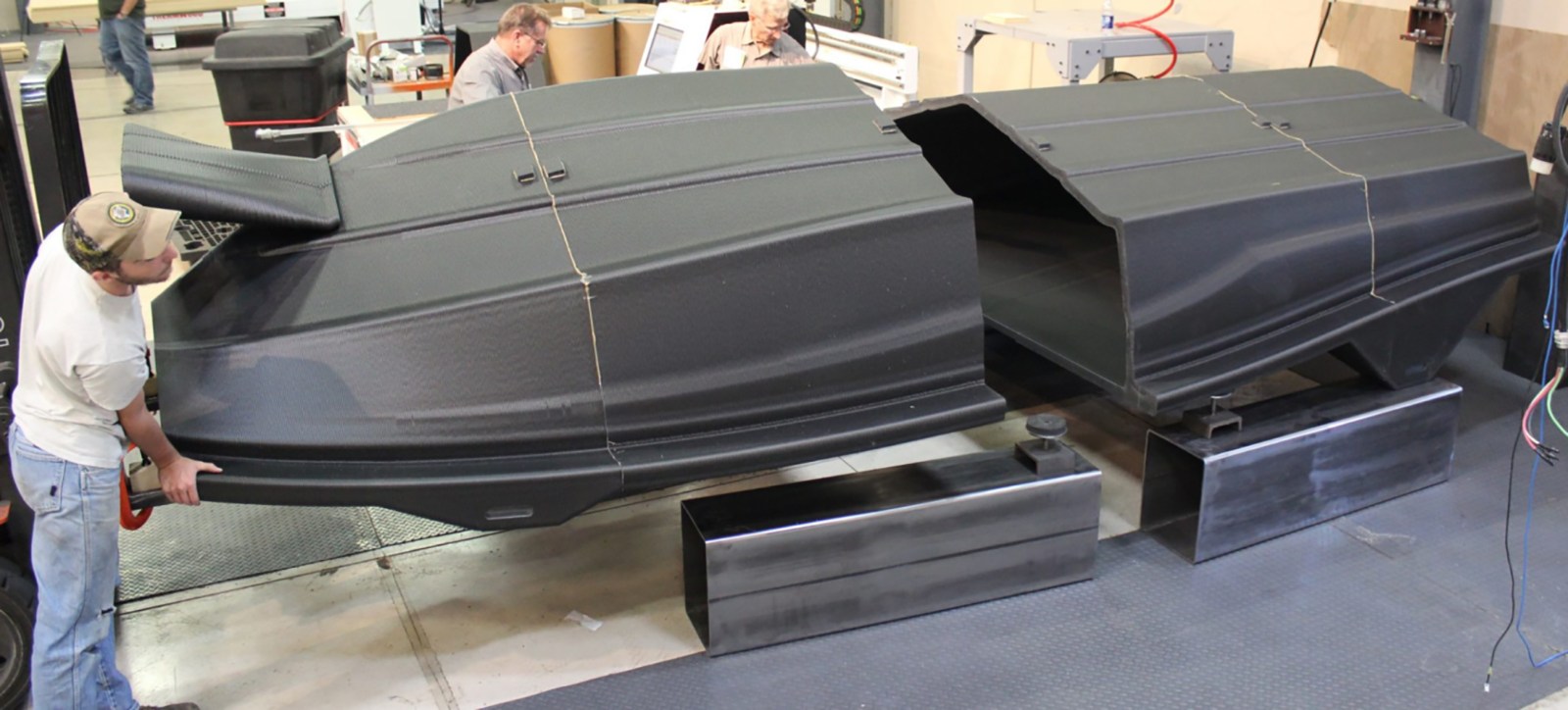
Рисунок 2. Стыковка и склеивание готовых секций оснастки катера, изготовленных с помощью 3D-печати
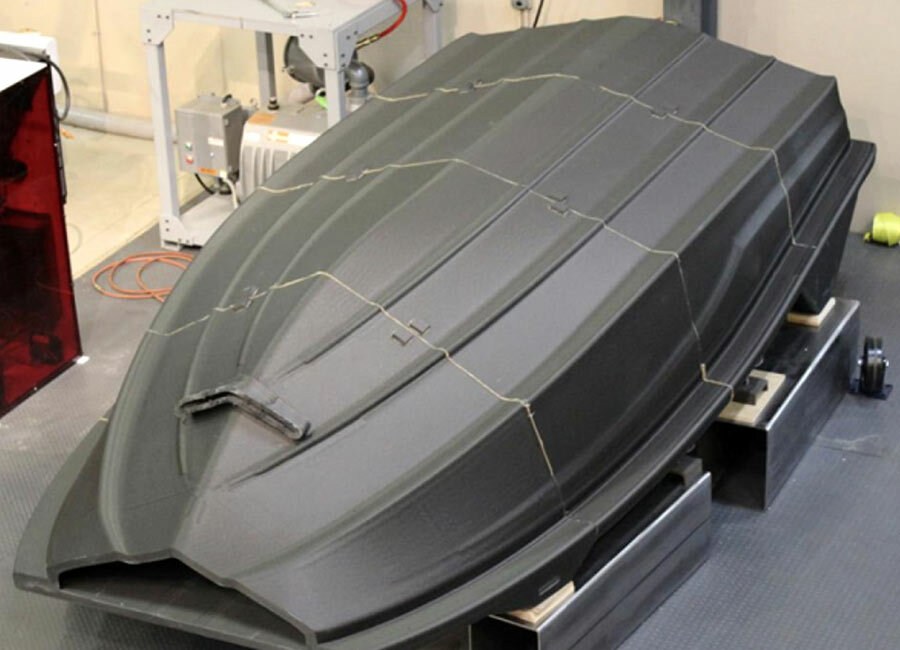
Рисунок 3. Готовая оснастка корпуса катера без носовой секции
Секции корпуса были соединены между собой с помощью многокомпонентного полиуретанового клея. После полимеризации клея фрезерный станок с ЧПУ обработал корпус как единую деталь, доведя ее поверхность до требуемого качества.
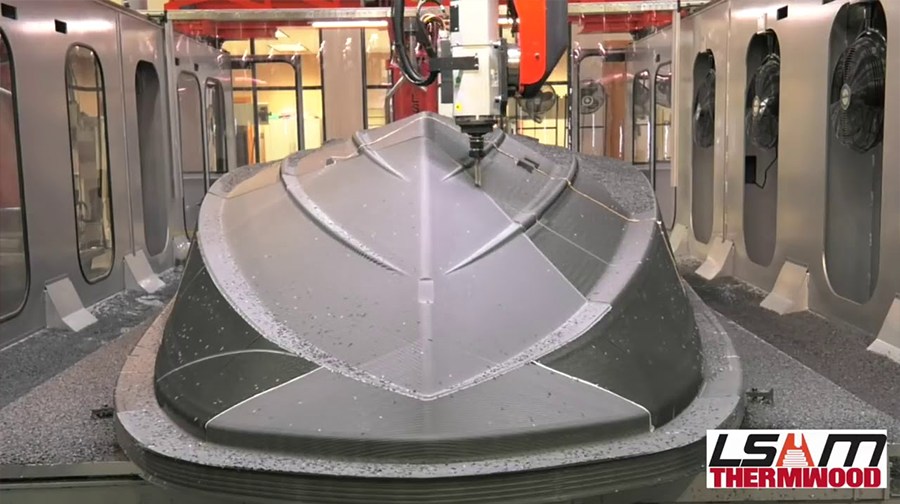
Рисунок 4. Обработка поверхности корпуса фрезой с ЧПУ
Обработка поверхности корпуса катера показана на рисунке 4. На печать ушло около 30 часов, а на обработку поверхностей — 50 часов. Весь процесс, от печати до готового изделия, занял порядка 10 дней. В качестве материала корпуса катера компания Thermwood использовала материал Techra PM Electrafil ABS LT1 3DP, состоящий из комбинации целлюлозных нано- и микроволокон с термопластичными материалами. Он хорошо себя показал при 3D-печати и обработке с использованием технологии LSAM. Кроме оснастки, на самом большом 3D-принтере в мире за 72 часа был изготовлен корпус катера 3Dirigo длиной 7,6 м на технологических опорах по скулам и в районе киля, которые впоследствии были отрезаны [2–3]. Форма корпуса катера была разработана специалистами компании Navatek, специализирующейся в дизайне корпусов судов. Имеется информация, что масса корпуса катера после сборки составила 2268 кг.
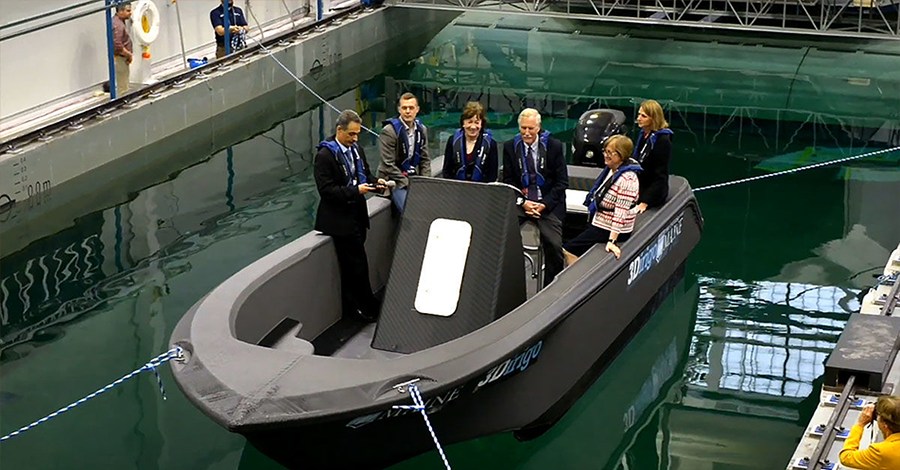
Рисунок 5. Готовый катер на воде. Презентация
После доработки и сборки катера, в том числе дооснащения его консолью и швартовными утками, а также подвесным мотором с дистанционным управлением (рисунок 5), катер прошел ходовые испытания на воде в «Морской инженерной лаборатории» Alfond W2, которые включали тесты на прочность корпуса. Катер 3Dirigo стал обладателем трех рекордов книги Гиннеса: как самый крупный в мире полимерный объект, полученный на 3D-принтере, самый большой твердотельный 3D-печатный объект и самой большой корпус катера на 3D-принтере [2–3].
Проанализировав изложенное выше, можно сделать следующие выводы:
- для изготовления крупных узлов, включая корпус катера, потребовалось изготовить соответствующее оборудование;
- для изготовления отдельных сборочных единиц, включая корпус катера, потребовалось разработать специальную технологию;
- линейные размеры одной сборочной единицы при изготовлении оснастки не превышают 3 м. Механические характеристики оснастки корпуса катера, равно как и характеристики ее долговечности, обеспечиваются клеевыми соединениями сборочных элементов между собой;
- в результате 3D-печати получен однотонный однослойный однородный корпус катера, имеющий толщину стенок около 4 см (40 мм), блоки плавучести в котором могут быть выполнены исключительно в виде внутренних полостей.
Рассмотрим современную классическую технологию изготовления корпуса маломерного судна из композиционных материалов. Напомним, что маломерным судном в мировой морской практике считается судно длиной до 24 м. В соответствии с отечественными нормативными документами маломерным считается судно длиной до 20 м. Вначале изготавливается оснастка первого порядка, представляющая собой натурный макет корпуса изготавливаемого судна, называемый «мастер-модель», «болван». На первом этапе из блоков склеенного твердого пенопласта, который подвергается механической обработке на координатном станке, изготавливается корпус судна в натуральную величину.
Если размеры корпуса судна превышают размеры рабочего стола станка, корпус изготавливается поэлементно, и в дальнейшем элементы склеиваются в единую конструкцию. Поверхность изготовленного корпуса подвергается оклейке несколькими слоями композиционного материала на основе стекловолокна и последующей отделке поверхности для обеспечения требуемого уровня шероховатости. Качество отделки в ряде случаев проверяется по световому лучу, излучаемому специальным прибором. Если тонкая линия луча не имеет существенных изгибов или разрывов на поверхности оснастки первого порядка, то качество ее отделки признается удовлетворительным. После этого изготавливается оснастка второго порядка, называемая матрицей. Оснастка второго порядка для маломерных судов, как правило, изготавливается из композиционных материалов на основе стеклянного волокна. Для судов более крупных размеров, а также в других отраслях, например, в авиационной промышленности, оснастка второго порядка изготавливается из металла, что существенно дороже. Она представляет собой форму, обратную мастер-модели. Чем более сложная форма корпуса судна, тем больше разъемов делается на оснастке второго порядка.
Классические композитные технологии позволяют сделать оснастку второго порядка для изделия абсолютно любой формы, включая сферу. Изготовление оснастки второго порядка начинается с установки на поверхность мастер-модели так называемых «гребней» в плоскостях, где на оснастке второго порядка должны быть разъемы. После этого поверхность мастер-модели и гребня покрывается разделительным составом. В малотоннажном судостроении формование оснастки второго порядка выполняется по стандартным композитным технологиям, чаще всего методом контактного формования. В тело оснастки второго порядка заформовывается необходимое количество механических или пневматических съемников. После приобретения отформованным участком оснастки необходимой твердости и прочности гребни вокруг нее снимаются. На следующий участок мастер-модели и вертикальную часть оснастки второго порядка, открывшуюся после снятия гребня, наносится разделительный состав. После этого производится формование следующего участка оснастки второго порядка. И так повторяется до полного покрытия поверхности мастер-модели. После окончательного затвердевания оснастки второго порядка, на ее поверхность наносится оребрение, как правило, из трубчатых ферм.
В разъемах оснастки второго порядка выполняются отверстия под болты и устанавливаются болтовые соединения. После этого оснастка второго порядка считается законченной. Она снимается с мастер-модели. Если предполагается тиражирование оснастки второго порядка для изготовления крупной серии изделий или повышения качества поверхности готового изделия, то с помощью первого комплекта оснастки второго порядка изготавливается фальш-изделие. Оно представляет собой поверхность готового изделия, изготовленную из того же композиционного материала, что и оснастка второго порядка, но имеющую существенно увеличенную, по отношению к изделию, толщину. Толщина фальш-изделия может достигать десятикратной величины изделия. Поверхность фальш-изделия отделывается до необходимого уровня гладкости и шероховатости, после чего фальш-изделие готово для тиражирования оснастки второго порядка. На оснастку второго порядка наносится разделительный состав и формуется изделие. В нашем случае — корпус маломерного судна. Для формования корпуса маломерного судна в настоящее время применяются три основных технологии: контактное формование, напыление, а также вакуумная инфузия. Эти технологии могут применяться в различных сочетаниях. Например, после нанесения на оснастку декоративного слоя и укладки нескольких первых слоев стеклоткани/стекломата методом контактного формования, специальной установкой напыляется слой рубленного ровинга, пропитанного связующим. А после прикатки напыленного слоя на него методом контактного формования укладывается еще несколько слов стеклоткани/стекломата, а также пенопласта/бальзы и других материалов. Чаще всего в подводной части корпус формуется однослойным. В районе надводного борта корпус имеет трехслойную или многослойную конструкцию с применением вспененных структур или же панелей бальзы.
Однако в конструкции ряда катеров и малых судов днищевая часть корпуса тоже имеет трехслойную конструкцию. Для получения трехслойных и многослойных структур сейчас широко применяются различные армирующие наполнители типа матов «Поликор». Для обеспечения необходимых характеристик прочности по поверхности и по толщине композиционного материала в настоящее время применяются различные мультиаксиальные ткани и другие наполнители. Широкое применение трехслойных конструкций и мультиаксиальных тканей в конструкции корпуса маломерного судна из композитов позволяет получать конструкции с высокой весовой эффективностью и приемлемыми характеристиками долговечности [4–5]. Разрез по ДП, вид сверху, слоистая структура, а также основные конструктивные узлы корпуса судна из композиционных материалов представлены на рисунках 6–8.
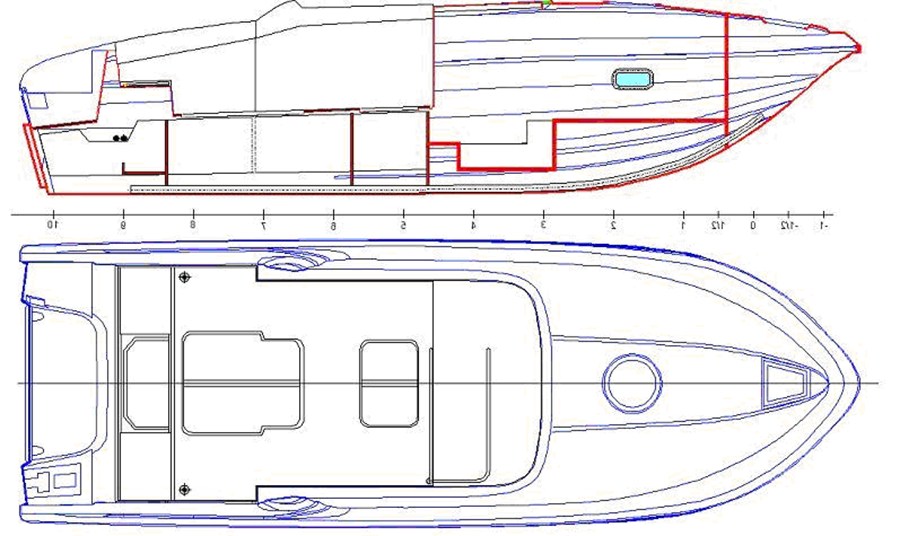
Рисунок 6. Корпус судна из композитов. Разрез по ДП и вид сверху
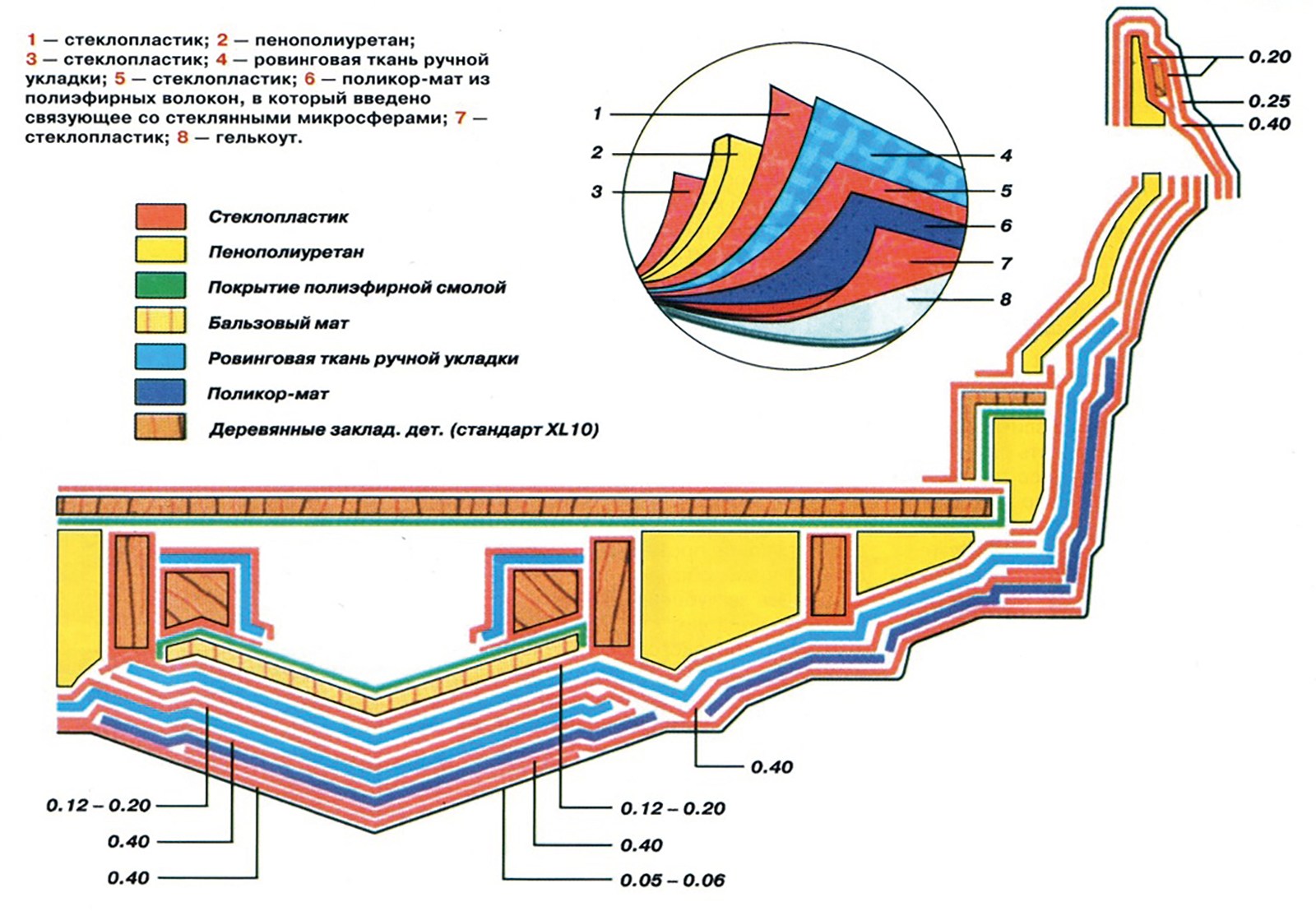
Рисунок 7. Слоистая структура корпуса судна из композитов
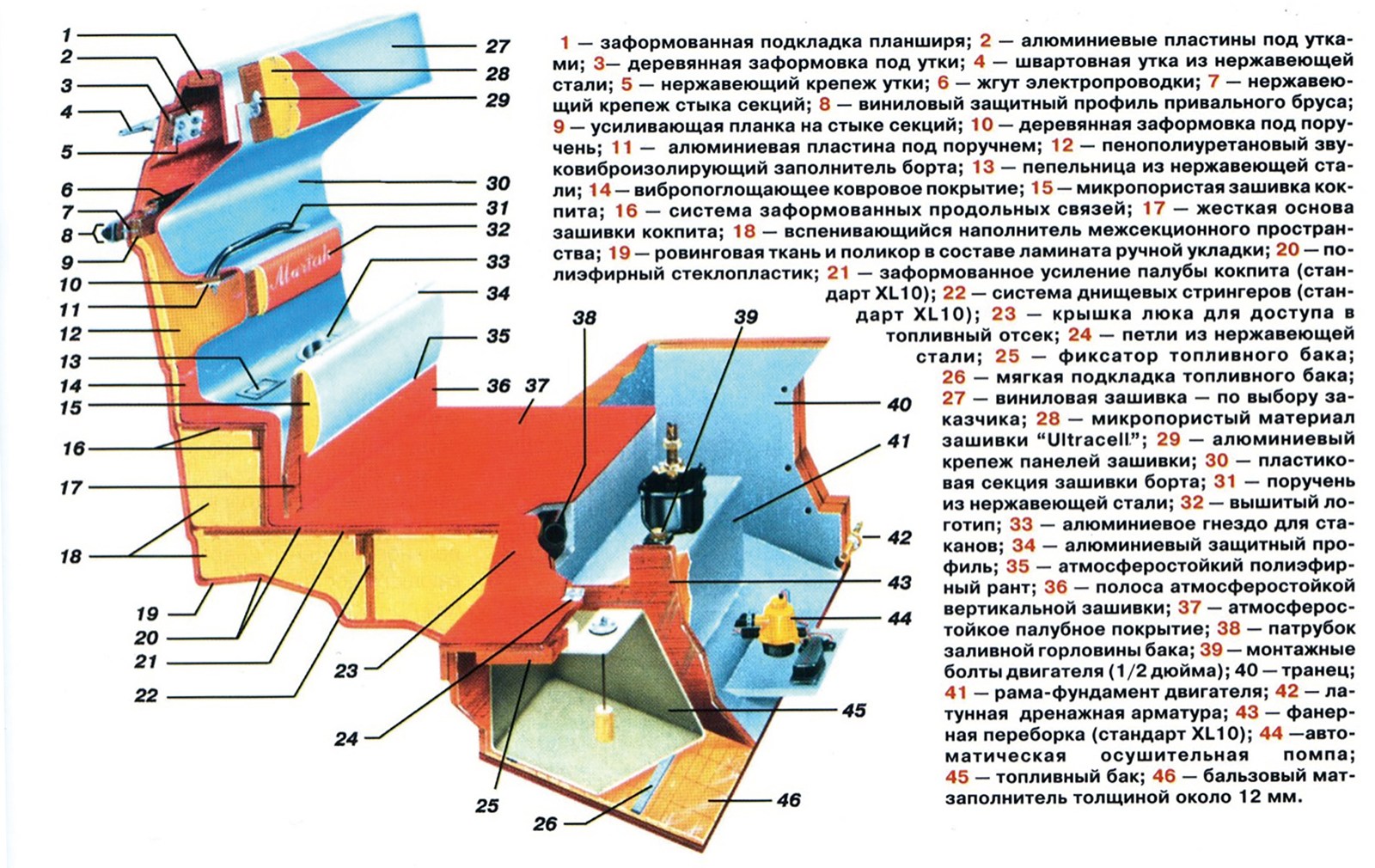
Рисунок 8. Основные конструктивные узлы корпуса судна из композитов
Проанализировав изложенное выше, можно сделать следующие выводы:
- изготовление корпуса катера из композиционных материалов по традиционной технологии включает три основных этапа: изготовление оснастки первого порядка — мастер-модели, изготовление оснастки второго порядка или матрицы и изготовление собственно изделия — корпуса катера;
- корпус катера из композиционных материалов имеет достаточно сложную конструкцию с точки зрения наличия в нем большого количества внутренних разнородных элементов, включая блоки плавучести, интегрированных в конструкцию, а также с точки зрения слоистой структуры, позволяющей обеспечивать необходимое изменение механических характеристик, как по площади поверхности катера, так и по его толщине;
- корпус катера имеет стойкое декоративное покрытие с разнообразными цветовыми решениями.
Проанализируем другие, более широко распространенные, существующие в настоящее время технологии 3D-печати, с точки зрения их применения в маломерном композитном судостроении. В статье [6], в частности, указывается, что для получения конечных изделий из пластиков, включая композиционные материалы, могут быть применены SLA-технология (лазерная стереолитография), SLS-технология (селективное лазерное спекание), FDM-технология (метод послойного наплавления материала). SLA-технология обеспечивает самую высокую прочность моделей и один из лучших показателей точности изготовления, а также идеальное качество поверхности изделий. Она дает возможность построения моделей сложной формы и структуры. При этом обеспечивает быстродействие 3D-принтеров. Оборудование, использующее SLA-технологию, имеет большой объем рабочей камеры (до 2,4 м). А выращенный из пластика прототип можно использовать как готовое изделие. Однако использование SLA-технологии потребует крупных первоначальных инвестиций. Оборудование предъявляет особые требования к помещению и условиям эксплуатации.
Все это обусловливает необходимость серьезного обучения технического персонала. SLS-технология обеспечивает высокие механические характеристики напечатанных моделей, так как используемый в одном из вариантов этой технологии полиамид — один из самых прочных пластиков. Кроме того, технология предусматривает использование большого разнообразия применяемых материалов и высокую скорость печати. Она дает возможность создания изделий сложнейших форм и фактур. Оборудование для SLS-технологии имеет достаточно большой размер камеры построения (до 1 м). Оно дает возможность печати как прототипов, так и конечных изделий для узлов и элементов. Необходимо отметить, что использование SLS-технологии обусловливает высокую стоимость оборудования и материалов, а также необходимость обработки шероховатых или пористых поверхностей, напечатанных на 3D-принтере с помощью SLS-технологии изделий. Эта технология также предъявляет особые требования к помещению и условиям эксплуатации. FDM-технология является самой доступной технологией 3D-печати. Она обеспечивает высокую скорость построения, а также возможность печатать крупные объекты (до 2 м). Изделия, полученные с помощью этой технологии, имеют наибольшую шероховатость поверхности, причем качество зависит от диаметра сопла и от расходных материалов. Имеется риск растекания пластика, так как изделия имеют повышенную чувствительность к перепадам температур [6].
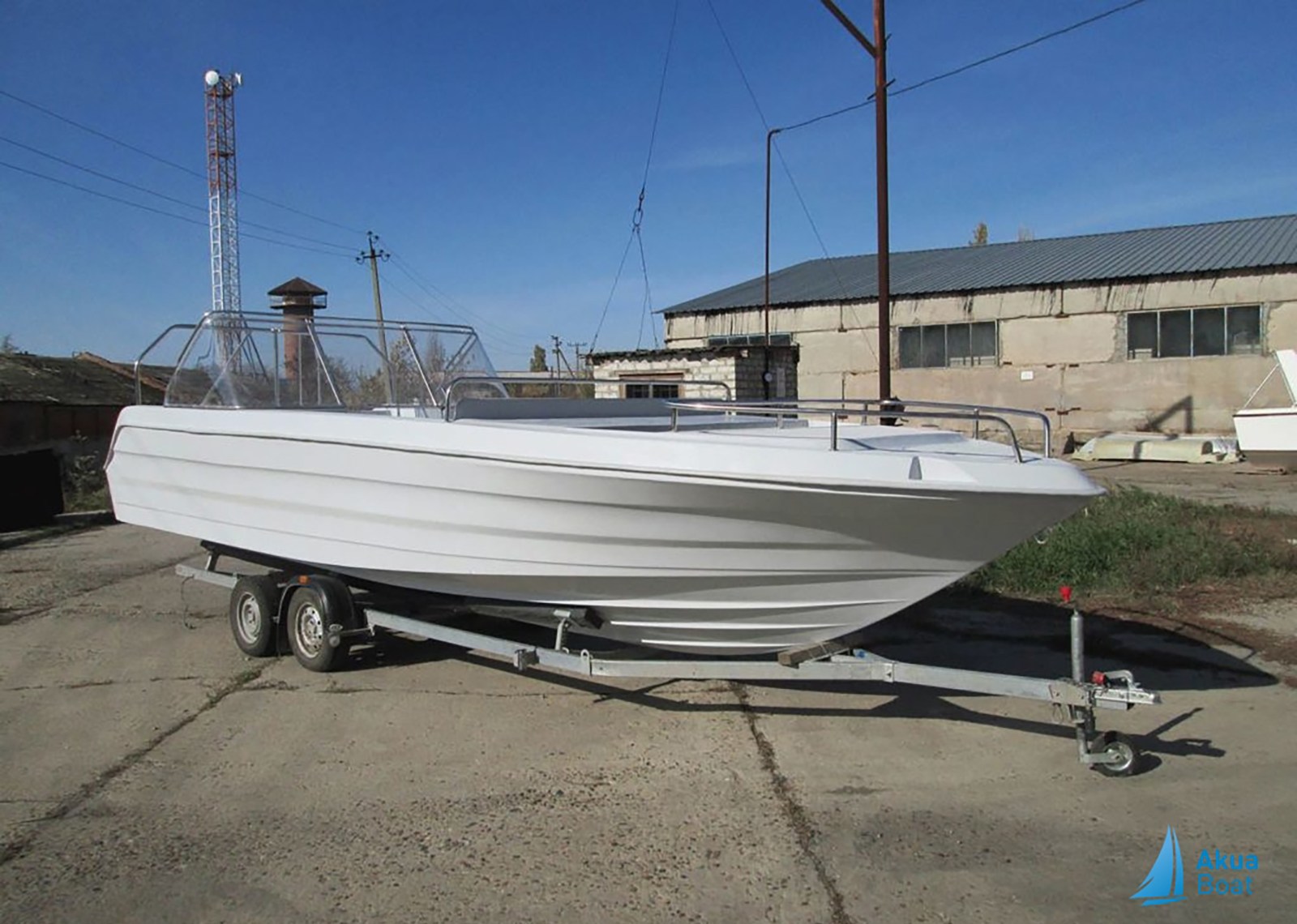
Рисунок 9. Катер из композиционных материалов «Касатка» ПРО750»
Анализ перечисленных технологий позволяет сделать вывод, что наиболее просто использовать технологии 3D-печати для изготовления мастер-моделей изделий (или фальш-изделий), в том числе получаемых соединением нескольких элементов. Естественно, экономическая целесообразность должна быть проанализирована и подтверждена. Для изготовления оснастки второго порядка (матриц) данные технологии подходят существенно меньше, в первую очередь, из-за ограничения линейных размеров получаемых на 3D-принтере изделий и их достаточно высокой сложности (разъемы, соединения, оребрение). Целесообразность изготовления корпусов катеров и лодок методом 3D-печати представляется достаточно сомнительной по следующим соображениям. Например, серийный отечественный катер «Касатка-ПРО750» производства компании Aquaboat, имеющий близкие размеры катеру 3Dirigo (длину 7,5 м, ширину 2,5 м, высоту 1,4 м, пассажировместимость 12 человек), имеет массу корпуса 800 кг (против 2268 кг у корпуса катера 3Dirigo) и цену полностью оснащенного и готового к продаже судна 620 000 рублей (порядка 8 100 USD) по состоянию на 1 февраля 2021 года [7]. Понятно, что столь большое различие в массе и конструкции при близких геометрических размерах и, как следствие, в цене, делает изделие, полученное с помощью 3D-печати неконкурентоспособным в России. Оценивая целесообразность применения 3D-печати, кроме прямых расходов на изготовление изделия (материалы, энергия, расход ресурса оборудования), необходимо учитывать также затраты на техническое обслуживание и ремонт оборудования (собственно принтера), приобретение сменно-запасных частей к нему, обновленного программного обеспечения, а также его амортизацию по действующим в России бухгалтерским нормативам.
В заключение необходимо отметить, что инновации имеет смысл применять только там, где они приносят выгоду. Не существует универсальной аддитивной технологии, которая могла бы с максимальной эффективностью решить все производственные задачи, так как у каждой 3D-технологии есть свои преимущества и недостатки. Поэтому при определении целесообразности применения 3D-печати в маломерном судостроении нужно исходить из поставленных перед нею задач. Сегодня 3D-печать не претендует на замену традиционных технологий. Ее целесообразно интегрировать в существующий производственный процесс только в том случае, если с ее помощью можно получить решения, зачастую недоступные традиционным технологиям, с целью сокращения производственного цикла и, как следствие, существенной экономии времени и издержек. По моему мнению, сейчас 3D-печать в маломерном композитном судостроении технологически подходит только для опытного и экспериментального производства при прототипировании, тестировании и отработке технологических решений при условии ее экономической эффективности.
Список литературы
- LSAM 3D Printed Boat Hull Pattern Video. — URL: источник
- University of Maine: 3Dirigo. — URL: источник
- 3Dirigo: самая большая лодка, напечатанная на 3D-принтере. — URL: источник
- Францев, М. Э. Проектный анализ конкурентоспособности судов из композиционных материалов / М. Э. Францев, В. К. Ханухов, Б. А. Царев // Морской вестник. — 2013. — № 15(10). — С. 9–15.
- Францев, М. Э. Проектная оценка эксплуатационных нагрузок и характеристик долговечности корпусов судов из композиционных материалов / М. Э. Францев // Морской вестник. — 2008. — № 4(28). — С. 93–98.
- Попадюк, С. Девять шагов к созданию аддитивного центра на предприятии / С. Попадюк // Аддитивные технологии. — 2019. — № 3. — С. 24–28.
- Прогулочный катер касатка PRO 750. — URL: источник