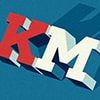
Переработка композитов: тенденции и опыт
рубрика: технологии
Что делать с отходами композитного производства и композитными изделиями с истёкшим сроком службы? Этот вопрос, являющийся одним из ключевых вопросов, стоящих перед композитной отраслью, на наш взгляд не обсуждается в должной мере. Композитные компании почти смирились с издержками, связанными с захоронением отходов, в то время как поставщики металлов рекламируют возможность повторного использования своей продукции в промышленности.
Оригинальная статья была опубликована в номере 3 (72) 2017 журнала "Композитный мир".

Источник: www.sunwindenergy.com
Однако сегодня на рынке существуют по крайней мере три причины, делающие возможным стимулирование роста переработки композиционных материалов, и в особенности рециклинг углеродного волокна:
- Директива Европейского союза End-of-life-vehicle (прекращение жизненного цикла транспортных средств) ELV требует, чтобы 85% от общего веса материалов, используемых в автомобиле, были использованы повторно или имели возможность вторичной переработки.
- Высокая себестоимость и высокие эксплуатационные издержки углеродного волокна делают его привлекательным с точки зрения утилизации, что создаёт рынок для переработанных волоконных продуктов, особенно в автомобилестроительном секторе.
- Новое поколение потребителей, озабоченных вопросами экологии, активно поддерживает применение рециклинга и производств с замкнутым контуром, а также ищет товары с использованием переработанных компонентов.
Технологии: разные подходы
«Одна из причин, по которым алюминий и сталь остаются серьёзными конкурентами композитов, — это возможность их вторичной переработки, что, в конечном итоге, ведёт к снижению общих затрат на производство», — говорит Эд Пилпел, старший технический советник Polyone Advanced Composites (Englewood, CO, US) и нынешний председатель комитета по переработке в Ассоциации американских производителях композитов (ACMA, Арлингтон, VA, США). «Но этим отраслям промышленности потребовалось 30–50 лет, чтобы достичь их сегодняшнего успеха в вопросах рециклинга. Индустрия композитов гораздо моложе, и у нас есть годы, — признаётся он, — но нам необходимо совершить качественный рывок в этом направлении».
Те компании, которые сейчас занимаются рециклингом, используют несколько технологий переработки. Первоначальные усилия были сосредоточены на утилизации и повторном использовании высококачественных отходов изделий из углеродного волокна, как правило, из аэрокосмической отрасли, поскольку они относительно просты в работе и дают качественные углеродные волокна с практически неизменёнными свойствами, даже в нарезанном виде. Источники отходов — это бракованные детали, обрезки, неиспользованные препреги, остатки волокон на бобинах и так далее.
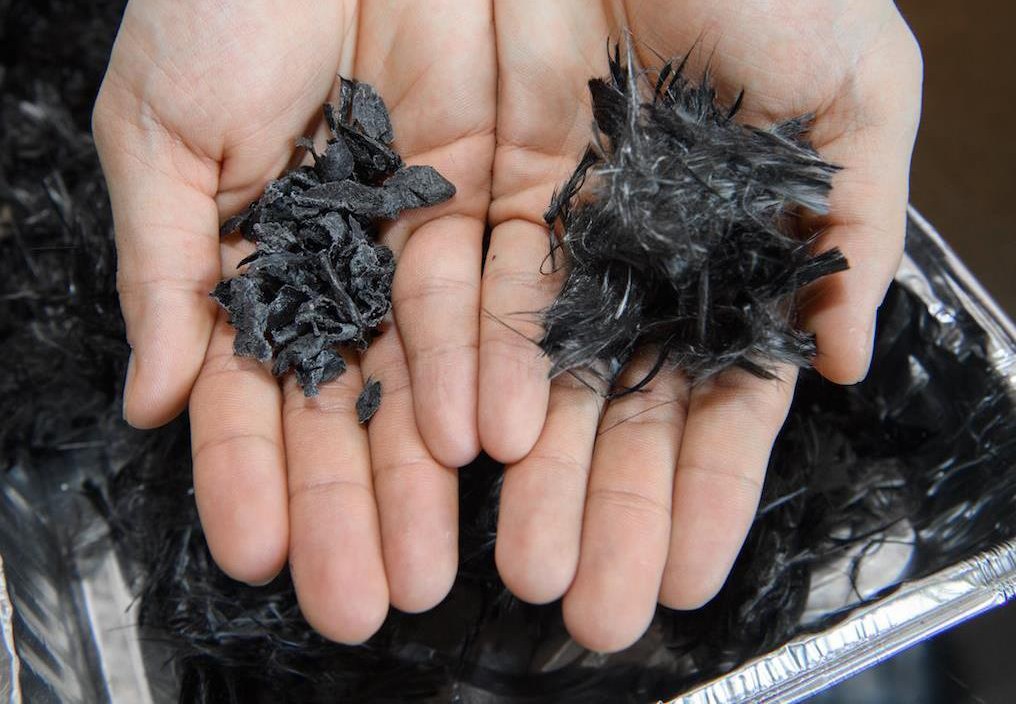
Современными коммерческими методами устранения смолы из углеродных волокон являются пиролиз (термическая обработка) и сольволиз (химическая обработка). Пиролиз требует большое количество тепловой энергии для выжигания смолы и может вызывать обугливание волокон, но это ничто по сравнению с энергией, необходимой для производства первичного углеродного волокна. Некоторые источники говорят, что сольволиз требует ещё больше энергии, чем термическая обработка, но зато он позволяет извлекать и волокна, и смолу. В обоих процессах восстановленные волокна хорошо перерабатываются в нетканые маты или термопластичные гранулы для литья под давлением и являются подходящим сырьём для применения в автомобильной промышленности.
Сложнее перерабатывать детали с закончившимся сроком службы (EOL), чтобы осуществить полный «замкнутый» цикл, когда материалы извлекаются из отработанных изделий, перерабатываются и используются повторно. Пиролиз и сольволиз можно применять для отверждённых отработанных отходов углекомпозита. Для деталей из стекловолокна обычно используется механическое дробление. Полученный измельчённый продукт может использоваться в качестве наполнителя для смолы, цемента и других смесей, либо сжигаться для получения энергии.
Для полноты картины стоит отметить, что на рынке есть по крайней мере две компании, предлагающие в качестве альтернативы перерабатываемые смолы, которые могут подвергаться растворению, что позволяет сохранять армирующие волокна неповреждёнными для дальнейшего использования.
Мировой опыт
«Три года назад мы совершили настоящий рывок, чтобы вывести эти материалы на рынок. Теперь мы получаем всё больше запросов о том, как использовать переработанное углеродное волокно. В настоящее время мы разрабатываем продукты для удовлетворения конкретных требований клиентов», — заявляет Фрэзер Барнс, управляющий директор ELG Carbon Fiber Ltd. (ELG CF, Косели, Уэст-Мидлендс, Великобритания), «дочки» немецкой компании по рециклингу металлов ELG Haniel (Дуйсбург, Германия).
ELG CF перерабатывает при помощи запатентованного процесса пиролиза более 2000 тонн отходов в год, используя в качестве сырья как отходы производства, так и отверждённые детали.
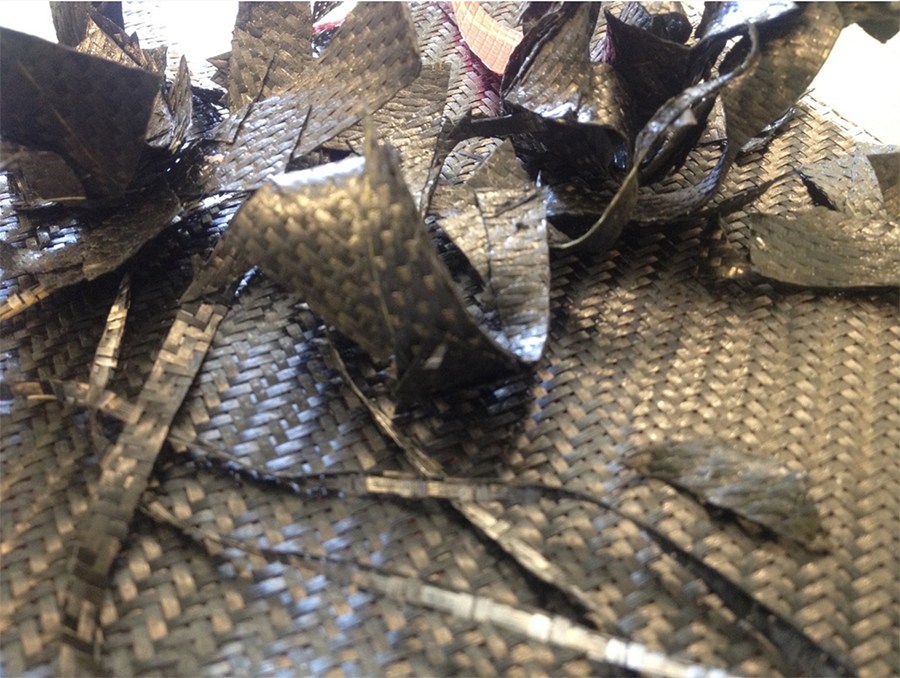
В США Carbon Conversions (Lake City, SC, US) также использует пиролиз и может обрабатывать весь ассортимент отходов композитного производства, утверждает Кит Грэхем, вице-президент по развитию бизнеса Carbon Conversions. Это отходы разной природы: промежуточные продукты, отходы сухого волокна, «мокрые» неотверждённые препреги, пултрузионные отходы, детали с истёкшим сроком службы от коммерческих аэрокосмических компаний и так далее.
«Мы создали надёжный бизнес, чтобы использовать отходы из различных отраслей и преобразовывать их в разнообразные продукты», — добавляет Грэм. Hexcel (Stamford, CT, США) недавно приобрела миноритарную долю в компании. Компания успешно продемонстрировала автомобильные детали, включая часть днища автомобиля для автомобильного OEM. Грэхем отмечает, что Carbon Conversions активно продвигает переработку композитов: «Для развития этой отрасли нам нужно создавать перерабатываемые, стабильные и качественные материалы».
CFK Valley Recycling (Wischhafen, Germany), входящая в группу Karl Meyer Group, является крупнейшим в Европе переработчиком композитов, использующим пиролиз, и принимает автомобильные, аэрокосмические и другие отходы. Тим Радемакер, управляющий директор компании, говорит: «В связи с ростом использования лопаток ветряных турбин, изготовленных из углеродного волокна, количество отходов от ветроэнергетики значительно возросло». Компания CFK Valley Recycling производит 1000 тонн переработанных волокон в год, а партнёрская компания CarboNXT (Wischhafen, Germany) изготавливает из измельчённых волокон различные виды нетканых материалов. Измельчённое углеродное волокно из вторичного сырья используется в качестве наполнителя для изготовления композитного материала на основе полиуретана для заднего и переднего бампера на новом родстере Mercedes AMG GTC.
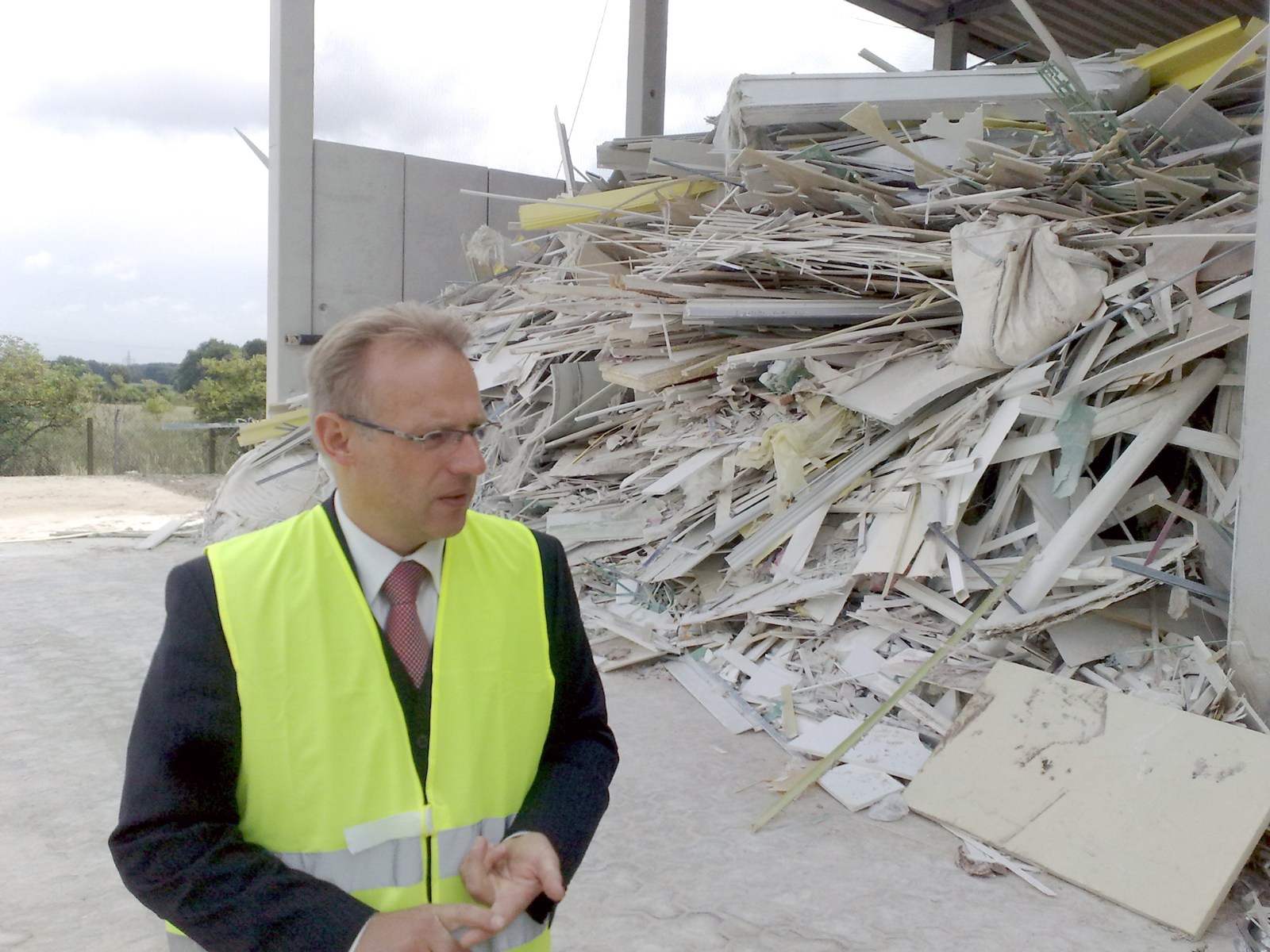
Adherent Technologies Inc. (ATI, Альбукерке, Нью-Мексико, США) начала свою деятельность по переработке 20 лет назад. Президент компании доктор Рон Оллред и доктор Ян-Майкл Госау, инженер-проектировщик и эколог, выбрали процесс влажной химии, который они называют хемолизом, в котором используется жидкость для переноса раствора и катализатор в сочетании с небольшим нагревом и давлением. Таким образом можно перерабатывать детали с истёкшим сроком службы и восстанавливать как углеродные волокна, так и смолу, не производя выбросы в атмосферу. Восстановленную смолу можно повторно использовать в качестве топлива или в качестве технологических химикатов в других отраслях промышленности. Недавно ATI установила партнёрство с инвестиционной группой DLC Capital (Мельбурн, штат Виктория, Австралия), принадлежащей Дамиану Кессарио, для коммерциализации технологии переработки. DLC Capital и ATI сотрудничали в течение многих лет и в настоящее время создали композитную компанию V Carbon (Лондон, Великобритания), которая будет восстанавливать углеродное волокно, а затем использовать волокна для производства деталей.
Новый участник сообщества по переработке отходов — компания Vartega (Golden, CO, US), возглавляемая Эндрю Макси, инженером, чей интерес к углеродному волокну пришёл из велоспорта: «Мы — новые игроки, но всё ускоряется, возможности для рециклинга растут». Vartega в настоящее время имеет пилотный масштабный, запатентованный процесс низкоэнергетического процесса сольволиза, который перерабатывает неотверждённый препрег и обрезки отверждённого препрега. Теперь Vartega работает с компанией TFP, Schenectady, NY, US, которая преобразует извлечённые волокна в нетканые маты и вуали. Компания провела исследования и опубликовала характеристики по извлечённому волокну. Прочность на растяжение и модуль восстановленного волокна сопоставимы с контрольными элементами первичного волокна.
«Мы некоммерческая организация, наша миссия состоит в том, чтобы вдохновлять и возглавлять сообщество по утилизации», — заявил генеральный директор компании Боб Ларсен из Composite Recycling Technology Center (CRTC, Порт-Анджелес, Вашингтон, США).
Расположенный в регионе с высокой концентрацией композитных производств, в непосредственной близости от Boeing и других компаний Boeing Tier, CRTC заинтересован в экономических эффектах, которые дает как снижение безработицы, так и рациональное использования ресурсов. CRTC совмещает деятельность по переработке углеродного волокна с масштабным и недорогим производством. CRTC покупает остатки (обрезки) первоклассного неотверждённого препрега от компаний-партнёров, в том числе Toray Composites (America) Inc. (Tacoma, WA, US), и превращает его в новые изделия, такие как ракетки для pickleball.
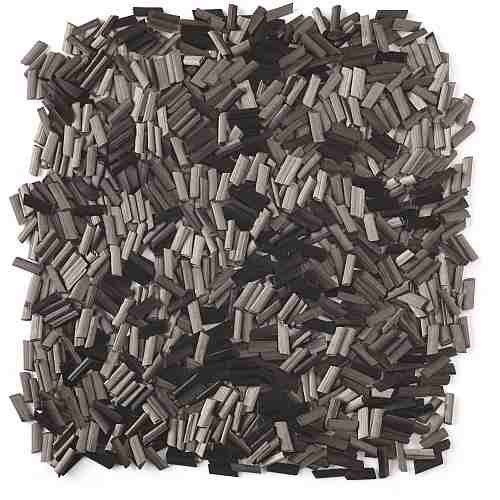
Procotex — грануры из углеродных волокон
Procotex (Dottignies, Belgium, дочерняя компания Dolintex NV) — это ещё одна компания, которая перерабатывает только отходы углеродного волокна — в первую очередь от плетения, ткачества и резки. С 1965 года Procotex был производителем льняного волокна, а со временем начал перерабатывать натуральные и синтетические волокна. Компания вышла на рынок технического волокна в 2011 году, когда приобрела компанию Apply Carbon SA (Lacuidic, Франция), специалиста по фрезерованию и прецизионной резке углеродных волокон, арамидных и других технических волокон, в том числе базальта, используемого в композитах. Бруно Даши, директор по продажам Procotex, говорит, что компания перерабатывает более 1000 тонн отходов углеродного волокна в год для производства измельчённого углеволоконного вторсырья. Для решения проблемы пыли, имеющейся при работе с измельчённым углеволокном, Procotex разработал новый продукт в виде гранулята, которое легко дозировать/диспергировать в экструдер без пыли. Бруно Даши говорит: «Переработанные углеродные волокна привлекательны для автомобильной промышленности уже потому, что полезные свойства могут быть достигнуты по гораздо более низкой цене. По этой причине у нас всегда под рукой большой запас необработанного материала. Мы видим свою задачу в поддержании стабильного предложения и качества, для нужд автомобильной промышленности».
Adesso Advanced Materials (Уху, Китай, Кембридж, Великобритания и Принстон, Нью-Джерси, США) и Connora Technologies (Хейуорд, Калифорния, США) благодаря стратегическому партнёрству разработали перерабатываемые термореактивные смолы, которые после отверждения могут быть легко подвергнуты разложению и удалены из армирующего каркаса, оставляя волокна неповреждёнными и пригодными для повторного использования. Бо Лян, председатель и главный исполнительный директор Adesso, говорит, что его фирменный отвердитель Cleavamine и смола Recycloset образуют крепкие связи при отверждении, но при этом легко расщепляются слабым раствором кислоты. Восстановленная смола нейтрализуется, а термопластичный осадок можно повторно использовать в качестве упрочняющего агента в адгезивах или формовочных компаундах. Adesso в настоящее время участвует в нескольких крупных программах, включая перерабатываемые печатные платы (ПХД) для технологии Shengyi; велосипед из углеродного волокна производства Pardus (торговая марка Taishan Sports, Сан-Матео, Калифорния, США); автомобильные детали для Wuhu на основе Chery Automobile Co. Ltd., в партнёрстве с ELG CF.
Разработка бизнес-кейса
«Утилизация композитов — это лабиринт с множеством барьеров, которые включают в себя технологии, государственные и отраслевые требования, стандарты и образование. Вы должны начать с базового бизнес-кейса», — говорит Эд Пилпел. Например, самый простой шаг компании — превратить свои отходы в энергию на заводе, избегая затрат на захоронение мусора и окупив небольшую часть первоначальной стоимости материала. Большую отдачу от материальных затрат можно получить, если отходы будут преобразованы в новые изделия или возвращены в производственный процесс компании. «Нам нужно найти скрытые возможности переработанных материалов», — добавляет он, указывая, в качестве примера, на успешную переработку шин в США, когда измельченные отходы шин использовались в процессе изготовления новых.
Понятно, что если производители автомобилей будут массово применять углеродное волокно в транспортных средствах, то это может привести к проблемам с поставками. Высококачественные переработанные углеродные волокна могут помочь преодолеть возможный разрыв в поставках. Комитет по рециркуляции ACMA работает с ISRI (Institute of Scrap Recycling Industries, Вашингтон, округ Колумбия, США) и IACMI для создания инфраструктуры рециклинга с надёжной логистикой и разработки стандартов для переработанных волокон.
В то же время ситуация с отходами композитов на основе стекловолокна, выглядит более сложной, так как низкая стоимость стекловолокна снижает экономическую целесообразность рециклинга.