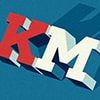
Разъёмные соединения стеклопластиковых трубопроводов
рубрика: технологии
Созданный в 2016 году комплекс ГОСТов «Трубы и детали трубопроводов из реактопластов, армированных волокном» заложил прочные нормы деятельности стремительно растущей композитной отрасли. Введены в действие основополагающие стандарты [1–2], утверждены технические условия изготовления композитных труб, регламентированы методы их испытаний и контроля качества.
Насколько герметичны герметичные соединения?
Всего разработано 39 проектов стандартов и 7 сводов правил (рисунок 1).
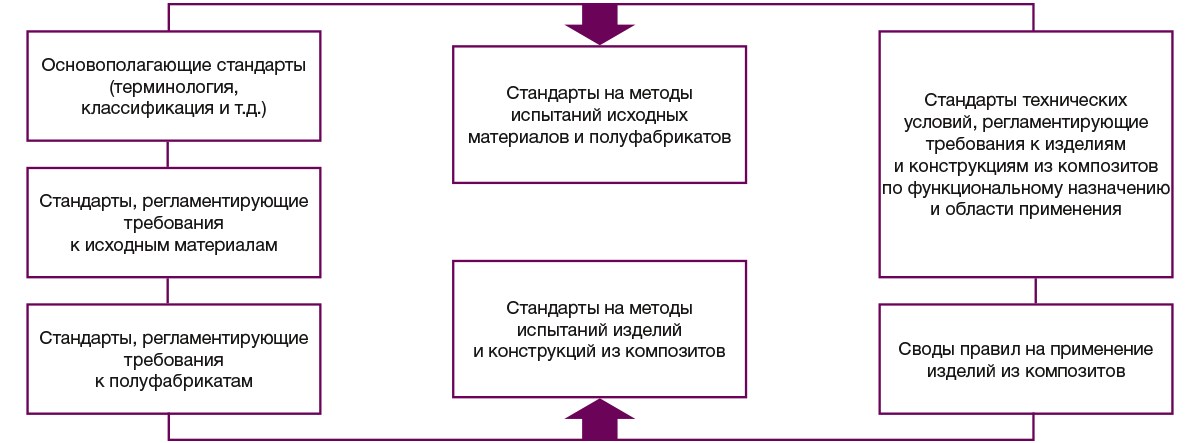
Рисунок 1. Система нормативных технических документов Союза производителей композитов
Данная система нормативной документации охватывает широкий круг требований к композитным трубопроводам для водоснабжения, водоотведения, дренажа и канализации, то есть решает актуальные задачи, стоящие перед трубостроителями, успешно освоившими указанные направления деятельности. Однако возможности применения композитов гораздо шире, и развитие перспективных рынков коррозионностойких труб для химической промышленности, труб высокого давления для транспорта жидких и газообразных углеводородов, иных агрессивных газов и паров требует дальнейшего расширения нормативной базы, поскольку здесь предъявляются существенно более жёсткие требования к надёжности оборудования и герметичности соединений. При участии Союзкомпозита введены в действие технические условия на трубы и фитинги для внутрипромысловых трубопроводов [3], на химостойкие композиты для ремонта и футеровки технологических трубопроводов.
Настоящий обзор посвящён неотъемлемому элементу трубопроводных систем — разъёмным соединениям, и сосредоточен преимущественно на вопросах, ждущих решения от разработчиков стандартов. Важность проблемы адаптации многочисленных нормативных требований, наработанных в разных отраслях промышленности, к композитным трубопроводам объясняется разнообразием конструкций и классов герметичности соединений, а также массовостью их применения, из-за которой около 90% утечек и эмиссии рабочих сред в атмосферу приходится именно на неподвижные разъёмные соединения [4]. Так почему же их называют герметичными?
Строго говоря, абсолютная непроницаемость разъёмных соединений недостижима, и в качестве условного её критерия служит нагрузка на уплотняющих поверхностях, по достижении которой, при заданном давлении рабочей среды, прибор перестаёт регистрировать протечку. Удельное давление на уплотнение, соответствующее прекращению протечки, именуется давлением обжатия [5]. Естественно, определённая подобным образом степень герметичности зависит от чувствительности измерительного оборудования, и поэтому находит применение более строгий способ ранжирования герметичности, основанный на измерении величины протечки в предположении, что минимальное её значение превышает порог чувствительности регистрирующего прибора. Последнее обстоятель-ство имеет существенное значение не только для оценки точности полученных результатов, но и приемлемости их для практических целей [6]. Таким образом, герметичность соединений — это их способность обеспечивать допустимую величину утечки, определяемую из условий нормальной работы различных систем и оборудования, безопасности людей, охраны окружающей среды [7]. Разумеется, понятие герметичности применимо не только для разъёмных, но и для бандажных, неразъёмных муфтовых или резьбоклеевых соединений, равно как для самих стеклопластиковых труб, поскольку микротрещины в клеевых швах и в матрице полимерного композита служат источником утечки транспортируемой среды, что особенно проявляется под высокой нагрузкой [8].
Допустимая величина утечки может различаться на много порядков. Например, принятый в химическом машиностроении отраслевой стандарт [9] делит соединения на пять классов герметичности, характеризуемых величиной протечки воздуха при разнице давлений в 0,1 МПа. Первому (высшему) классу соответствует течь от 2∙10−2 до 0,2 см3/год, а пятому — от 2∙103 до 4∙105 см3/год. Параллельно для измерения величины протечки используется принятая в вакуумной технике внесистемная единица расхода м3∙Па/с (Вт), а её количественное значение определяется различными способами — в гелиевой камере, галогенным щупом, люминесцентно-гидравлическим или пузырьковым методом и другими. В машиностроении широко применяются различные манометрические способы испытаний на герметичность, а в особых случаях используется масс-спектроскопия или радиоактивные газовые изотопы [10]. Ориентировочные границы применимости разных методов испытаний разъёмных соединений трубопроводов на герметичность и общие требования к их проведению устанавливает ГОСТ [11].
Методы количественного определения герметичности наиболее детально разработаны для фланцевых соединений, но и здесь, вследствие широчайшего разнообразия конструкций и материалов уплотнений, отсутствует единая система стандартизации. Так, действующий в химической и нефтеперерабатывающей промышленности ГОСТ [12] регламентирует расчёт усилия смятия прокладки, обеспечивающее герметичность соединения, то есть предполагает достижение полного отсутствия протечки, а не оценку её величины. Подобный метод издавна был принят в ASME, чьи стандарты герметичности фланцев предусматривают обеспечение потребного давления обжатия (именуемого «фактор у») и заданного прокладочного коэффициента — «фактора m», показывающего, во сколько раз механическое давление фланцев на прокладку выше давления рабочей среды, при котором происходит разгерметизация соединения.
Серия статей [13–15] рассказывает об эволюции стандартов герметичности фланцевых соединений, принятых в разных странах. Наиболее современный метод представлен в EN 13555, где для классов герметичности применяется логарифмическая шкала (таблица 1).
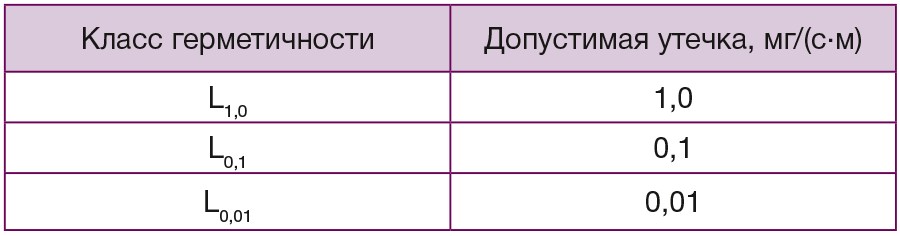
Таблица 1. Классы герметичности по EN 13555
Указанная в таблице наибольшая допустимая утечка определяется гелиевым методом и выражается в расходе газа, приходящегося на единицу длины периметра прокладки. Испытания проводятся при давлении гелия в соединяемой полости 4 МПа (или 1 МПа), причём в циклах нагрузки и разгрузки устанавливаются различные значения давления на прокладку Qmin(L) и Qsmin(L), обеспечивающие заданный класс герметичности. Величина Qmin(L) соответствует такому давлению обжатия, когда при увеличении нагрузки прокладка заполняет неровности соединения и достигается требуемый класс герметичности. Значение Qsmin(L) находится при последующем снижении нагрузки и показывает, в каком диапазоне нагрузок прокладка поддерживает герметичность требуемого класса. Пример графического представления результатов подобных испытаний показан на рисунке 2.
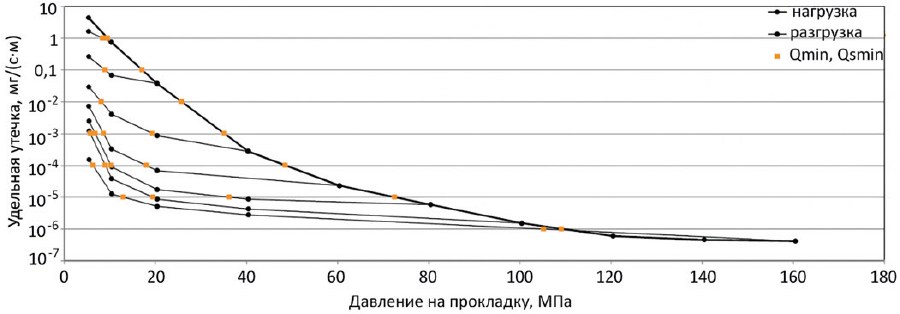
Рисунок 2. Испытания соединения на герметичность по EN 13555
Достоинством данного метода является то, что благодаря количественным измерениям протечки он предоставляет возможность обоснованного сравнения фланцевых соединений различного типа, выбора оптимальной конструкции и материала уплотнения. Однако самоуплотняющиеся соединения, широко применяющихся в стеклопластиковых трубопроводах, ещё ждут разработки количественного метода определения степени герметичности.
Муфтовые и раструбные соединения
Муфтовые (рисунок 3а) и раструбные (рисунок 3б) соединения превосходно себя зарекомендовали в композитных трубопроводах, применяемых для водоснабжения и канализации, поскольку при минимальной материалоёмкости обеспечивают быструю и надёжную стыковку труб большого диаметра, допускают их некоторые перекосы, несоосности и взаимные подвижки, неизбежно возникающие в процессе эксплуатации. Важным преимуществом данных соединений является цельность структуры трубы и соединительных участков, которые нуждаются лишь в механообработке, а не в отдельном изготовлении с последующей склейкой или приформовкой.
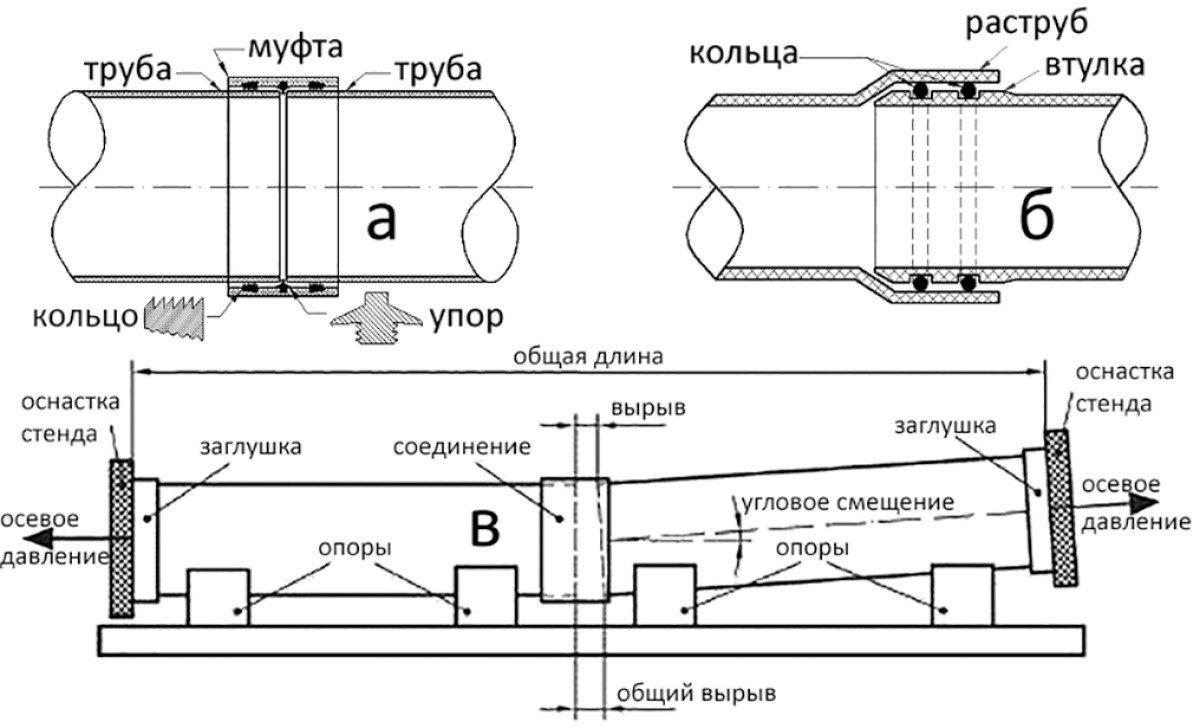
Рисунок 3. Муфтовые и раструбные соединения
За герметичность соединений отвечают самоуплотняющиеся кольца, расположенные в пазах точного размера и контактирующие с калиброванным участком сопрягающейся детали. Давление обжатия в данных соединениях невелико, но достаточно для обеспечения герметичности при работе под вакуумом, а давление рабочей среды дополнительно распирает уплотнение в зазоре, увеличивая натяг. Обычно для уплотнений применяется EPDM — этилен-пропилен-диеновый синтетический каучук, сохраняющий упругость в течение всего срока эксплуатации, который для трубопроводов систем водоснабжения составляет 50 лет [16].
Согласно ГОСТу [2] муфты с кольцевыми уплотнениями полагается испытывать на герметичность под номинальным давлением PN, причём в качестве имитатора труб используются короткие стальные оправки, качество поверхности, размеры и поля допусков которых, очевидно, должны отвечать требованиям к калиброванным участкам композитной трубы. Узел считается герметичным, если в течение 5 минут выдержки под давлением оно не упадёт более чем на 0,05%, не будут визуально обнаружены трещины, просачивание воды на поверхность и подтекание из-под уплотнений.
Более жёстким испытаниям муфтовые и раструбные соединения, не имеющие фиксатора, который предотвращает осевое смещение деталей, подвергаются совместно с трубами по стандарту [17], где эти соединения неудачно названы «подвижными» (в уплотнительной технике так именуются сальники валов и штоков арматуры, торцовые кольца насосов и т.п.) При испытаниях проверяется герметичность соединения, имеющего заданное осевое смещение («вырыв») и нарушения соосности труб (рисунок 3в). Испытания проводятся под статическим давлением воды 1,5PN и 2PN, а также при циклическом его изменении от атмосферного до 1,5PN. Соединение признаётся герметичным, если после серии испытаний отсутствует видимая течь.
Выпускаются также раструбные соединения с дополнительным пазом, куда через отверстие в стенке трубы после сборки вводится гибкий фиксатор. Перед сборкой поверхности уплотнения тщательно очищаются и на них наносится монтажная смазка, облегчающая скольжение деталей при обжатых кольцах. Трубы стягиваются с помощью такелажных приспособлений и мягких ленточных зажимов, предотвращающих появление опасных контактных напряжений на композитной стенке (рисунок 4).
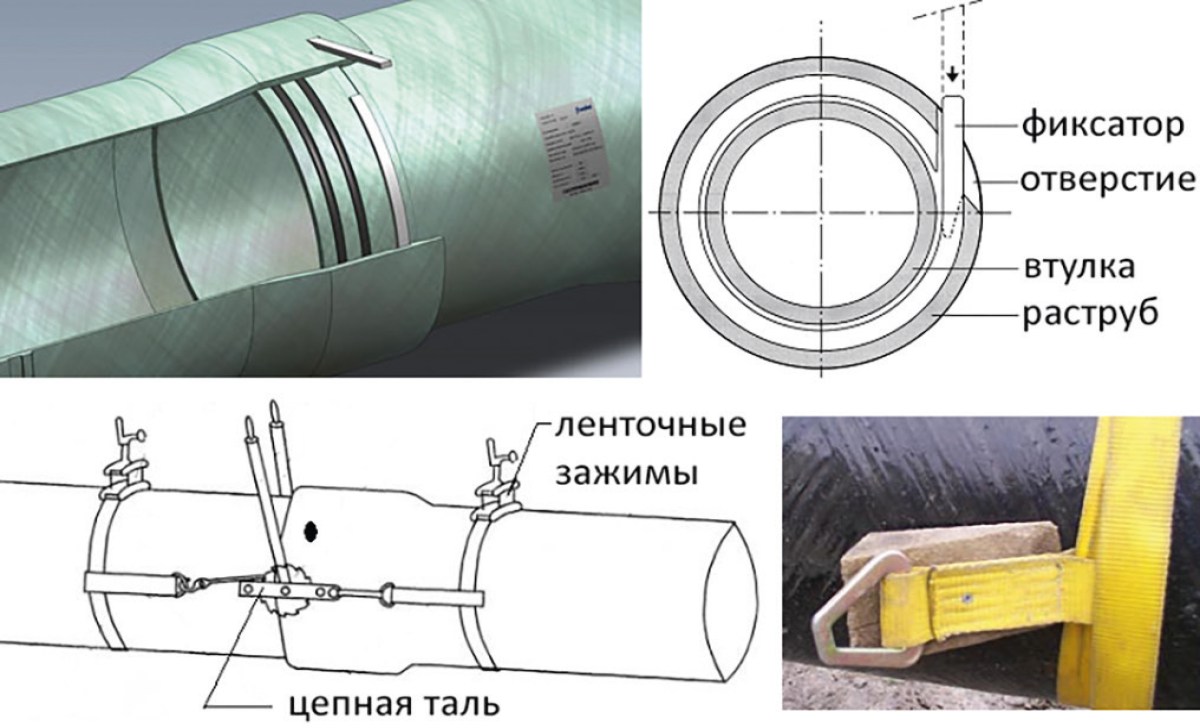
Рисунок 4. Раструбное соединение с фиксатором
Канализационные трубы большого диаметра допускается заталкивать в раструб нажимом экскаваторного ковша через деревянные прокладки с противоположного торца. Хотя наличие фиксатора в большинстве случаев повышает надёжность соединения, устраняя возможность утечки вследствие недопустимого вырыва, в канавке фиксатора при повышенных нагрузках могут возникать трещины [18]. Это указывает на необходимость расчёта и компенсации осевых смещений при проектировании трубопровода как с подвижными, так и с зафиксированными соединениями. Стойкие к растяжению соединения с эластомерным уплотнительным кольцом испытываются на прочность и герметичность по ГОСТ [19].
Конструкция самоуплотняющихся муфтовых соединений оказалась настолько удачной, что они нашли применение во внутрипромысловых композитных трубопроводах для транспортировки нефти, попутного газа и газового конденсата под давлением до 4 МПа [3], а также в полевых мобильных нефтепродуктопроводах, где успешно конкурируют с быстроразъёмными соединениями иных типов. Каждое раструбно-ниппельное соединение внутрипромысловых труб подвергается испытанию на прочность и герметичность под давлением 1,5 PN, а выборочно — под давлением 4 PN. Часть изделий из партии испытывается под нагрузкой всплытия, для чего пара труб подвешивается за узел соединения, заполняется водой и дважды нагружается давлением 2,5 PN. Проводятся также испытания соединений на герметичность при воздействии циклического изгиба, на стойкость к коррозионной среде, на разрушающее давление и др. Комплекс испытаний [3] гарантирует надёжную работу композитных трубопроводов в суровых условиях нефтепромыслов.
Ценный опыт эксплуатации внутрипромысловых композитных трубопроводов показывает, что муфтовые и раструбные соединения имеют большие перспективы в химической и нефтеперерабатывающей промышленности, однако их широкое внедрение требует совершенствования нормативной базы, особенно для стеклопластиковых газопроводов, транспортирующих горючие, токсичные и агрессивные летучие продукты. Одной заменой материала прокладки проблему герметичности разъёмных соединений тут не решить. Следует учитывать, что проверить на герметичность объект, работающий под давлением газовой среды, жидкостью практически невозможно [6], однако даже не имеющий аналогов в ISO стандарт ASTM на армированные эпоксидные трубы и фитинги для газопроводов [20] не предусматривает пневматических испытаний на герметичность, отсылая к отраслевым нормам промышленной безопасности.
Действительно, в данных отраслях широко используются пневматические испытания оборудования и трубопроводов методом замера падения давления воздуха или азота с последующим пересчётом на рабочий газ. По результатам испытаний находится коэффициент герметичности, соответствующий величине падения давления в единицу времени, который затем сравнивается с нормативным значением [21]. Пример расчёта допустимого падения давления при опрессовке соединений сжатым воздухом представлен в ГОСТ [11]. Подобный метод, особенно если выразить найденную протечку газа в единицах массы и отнести её к периметру уплотнительного кольца (а ещё лучше — к номинальному диаметру трубы!), может послужить удобным приближением к EN 13555 для количественной оценки степени герметичности самоуплотняющихся разъёмных соединений композитных труб. Если принять меры к сокращению заполненного газом объёма и его термостатированию, то метод не должен столкнуться с непреодолимыми метрологическими сложностями.
Резьбовые соединения
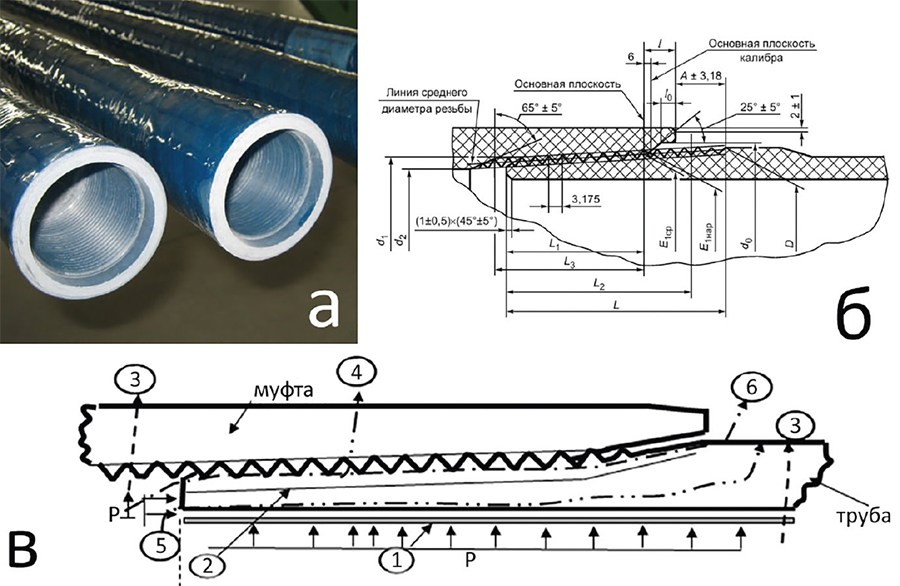
Рисунок 5. Коническое резьбовое соединение композитных труб
Хотя резьба стеклопластиковых фитингов выглядит как трубная (рисунок 5а), размеры её не совпадают с ГОСТ [22]. Резьбовые соединения композитных труб были разработаны в США группой представителей трубных и нефтяных компаний в 1959 г., и стандарт [23] на соединения и методы их испытаний оказался первым в области композитного трубостроения, принятым ASTM в качестве национального [24]. Стандарт перекрывает широкий ряд размеров — от 1½ до 20” включительно, с целью увеличения сдвиговой прочности шаг резьбы увеличен до 8 ниток на 1”, а угол профиля — до 60° (рисунок 5б). Такая же резьба принята в ГОСТ [25] на трубы диаметром от 50 до 200 мм, предназначенные для транспортирования нефтепродуктов, газового конденсата и химических реагентов, для обсадных колонн, а также для водоснабжения. Соединения должны сохранять герметичность при температуре рабочей среды до плюс 110°С и давлении от 3,5 до 27,6 МПа (трубы диаметром свыше 100 мм рассчитаны на меньшее PN). Выпускаются также насосно-компрессорные стеклопластиковые трубы под цилиндрическое резьбовое соединение с уплотнительными кольцами по ГОСТ [26], обеспечивающее их стыковку с металлическими фитингами трубопроводных систем.
Важным условием обеспечения герметичности является правильная затяжка конической резьбы. Операция должна выполняться с помощью ленточных или цепных ключей; применение обычных трубных ключей не допускается из-за риска повреждения композитной стенки трубы. Для проверки натяга и соответствия размеров резьбы стандарту служат калибры. При необходимости для уплотнения резьбы могут применяться трубные компаунды или анаэробные герметики, предотвращающие утечку независимо от величины натяга.
Согласно требованиям [25], соединения вначале подвергаются статическим прочностным гидравлическим испытаниям по ГОСТ [27] под давлением не менее 1,5PN. Продолжительность выдержки составляет от 120 до 600 с, а при квалификационных испытаниях — 24 ч. Образцы считаются прошедшими испытания, если не возникли трещины, сопровождающиеся постепенным падением давления, либо разрывы с резким падением давления. Затем насосно-компрессорные и обсадные трубы испытываются на герметичность при совместном действии постоянного внутреннего давления 1,5PN и внешней нагрузки. Согласно п. 9.8 [25] данная нагрузка должна действовать перпендикулярно оси, но в таблице 18 она называется осевой и рассчитывается на глубину погружения обсадной трубы 3000 м.
Метод нагружения в [25] не описан, указано только, что в ходе и после испытаний сборные узлы не должны иметь протечек или трещин. По-видимому, стандарт в этом разделе требует доработки, причём желательно не только конкретизировать методику испытаний, но и увеличить их объём.
Последнее связано с тем, что соединения из композиционных материалов могут быть подвержены усталостной деградации, приводящей к накоплению микротрещин и снижению степени герметичности в ходе эксплуатации. Если циклические нагрузки представляют опасность для архинадёжных бандажных соединений [28], то тем более — для находящихся под натягом резьб с нарушенной при нарезании структурой композита! На рисунке 5в, заимствованном из работы [29], показаны возможные пути утечки продукта через резьбовое соединение: 1 — барьерный слой, 2 — резьба, 3 — протечка через микротрещины стенки, 4 — протечка сквозь стенку вследствие растрескивания резьбы, 5 — протечка вдоль волокон с торца трубы, 6 — протечка вдоль витков резьбы. Появление данных протечек может быть особенно опасным для находящихся под воздействием вибраций газопроводов компрессорных станций. Подобные резьбовые соединения желательно испытывать не только под статической нагрузкой, но и проверять до потери герметичности на вибростенде, как это предусматривает ГОСТ [30]. Герметичность резьбовых соединений стеклопластиковых трубопроводов для транспортировки опасных жидкостей также желательно испытывать на внутреннее пульсирующее давление по данному стандарту, который в свою очередь требует адаптации к особенностям композиционных материалов. Даже напорные канализационные трубы на основе полиэфирных смол испытываются на устойчивость к колебаниям внутреннего давления в диапазоне от 0,75PN до 1,25PN [19], а ответственные композитные резьбовые соединения и подавно нуждаются в более строгой проверке.
Фланцевые соединения
Конструкции уплотнительных поверхностей фланцев по ГОСТ [31] отличаются разнообразием, благодаря чему в самом широком диапазоне условий эксплуатации достигается потребная герметичность соединений. Так, например, давление обжатия прокладки может меняться от десятков кПа для эластомерных плоских прокладок до сотен МПа для колец овального сечения из нержавеющей стали, а прокладочный коэффициент m — от 0,5 до 6,5 соответственно [12, 32]. Большой запас осевой сжимающей нагрузки требуется как для обжатия прокладки до потребной степени герметичности, так и для создания достаточной силы трения между прокладкой и фланцем, предотвращающей смещение уплотнения под воздействием давления среды (рисунок 6а).
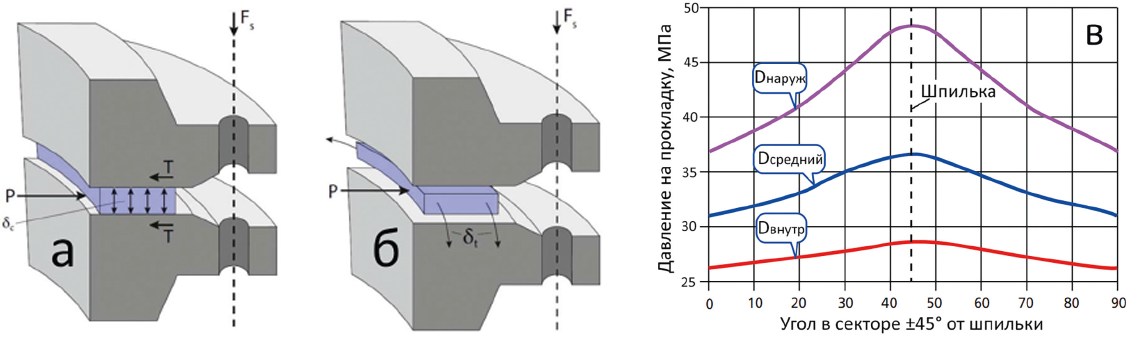
Рисунок 6. Нагрузки на прокладку [33] и распределение давления на её поверхности [34].
Снижение нагрузки ниже допустимого значения может привести не только к уменьшению степени герметичности соединения, но и к выдавливанию и разрыву прокладки (рисунок 6б), то есть к серьёзной аварии. Запас «фактора m» необходим и потому, что сжимающее давление распределено по поверхности прокладки неравномерно (на рисунке 6в представлен пример для соединения с четырьмя шпильками). Методы расчёта прочности фланцевых соединений и условий длительного обеспечения их герметичности, давно разработанные и стандартизованные в разных отраслях промышленности и энергетики [5, 12], постоянно развиваются и совершенствуются благодаря появлению новых материалов — в частности, композиционных. Однако основные задачи, стоящие перед технологом, остаются прежними: выбор типа фланца, материала и толщины прокладки, момента затяжки резьбы.
Типы и строение композитных фланцев
Полимерные композиционные материалы, применяемые в трубопроводах, выдерживают сравнительно малые контактные и срезающие напряжения, а чрезмерный изгиб соединений чреват межслоевым растрескиванием ламината. Вкупе с невысокой температурной стойкостью стеклопластиков данные факторы ограничивают допустимые типы соединения преимущественно круглыми плоскими фланцами и фланцами исполнения 1 по ГОСТ [35].
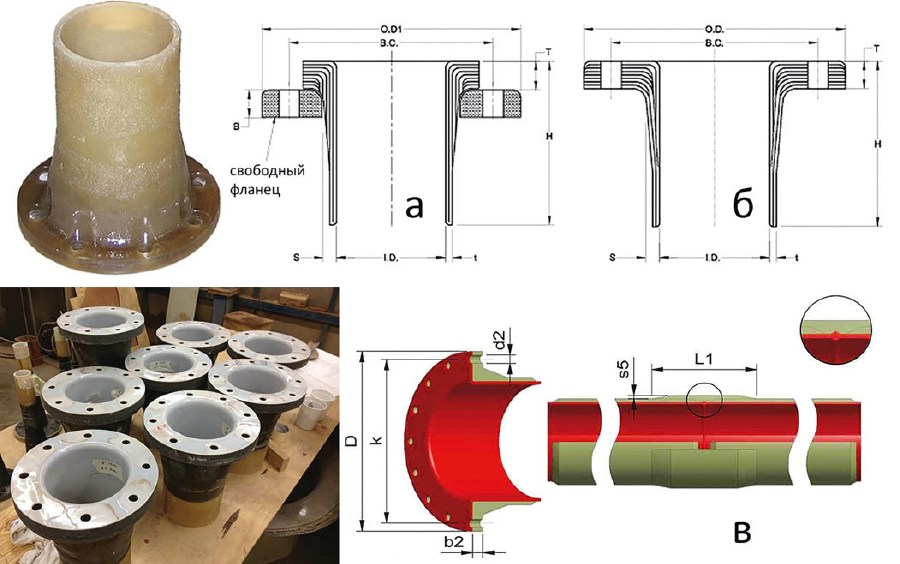
Рисунок 7. Типы композитных фланцев
ГОСТ [2] допускает применение двух видов подобных соединений: свободный фланец с накидным кольцом (рисунок 7а) и фиксированный фланец (рисунок 7б), выполняемый вместе с патрубком. Данный стандарт допускает различные технологии изготовления фланцев, а поскольку структура композиционного материала имеет решающее значение для обеспечения прочности элементов соединения, то строение фланца непременно следует учитывать при выборе подходящей модели. Фланцы с патрубком требуют трудоёмкой ручной выкладки стеклохолста и потому дороги, но обладают наивысшей статической и усталостной прочностью, устойчивы к растрескиванию в области шейки [36]. Крепёжные отверстия в таких фланцах обычно выполняются сверлением, дабы избежать снижающего прочность скопления связующего, нередко возникающего при их формовании. Фланцы с хаотичным армированием, выпускаемые по высокопродуктивной и малоотходной технологии горячего прессования, более дёшевы. При этом они не имеют пустот, обладают стабильной химической стойкостью и достаточно высокой прочностью. Иногда их изготавливают с коротким отрезком трубы под склейку. Прессованные по технологии RTM и из препрега SMC коррозионностойкие фланцы (рисунок 8), которые давно успешно применяются за рубежом [36–37], вполне заслуживают признания промышленности и упоминания в ГОСТе. Заслуживает также изучения возможность прессования из химостойких премиксов BMC разъёмных полуфланцев и ниппелей для соединений малого прохода и высокого давления по ГОСТ [38].
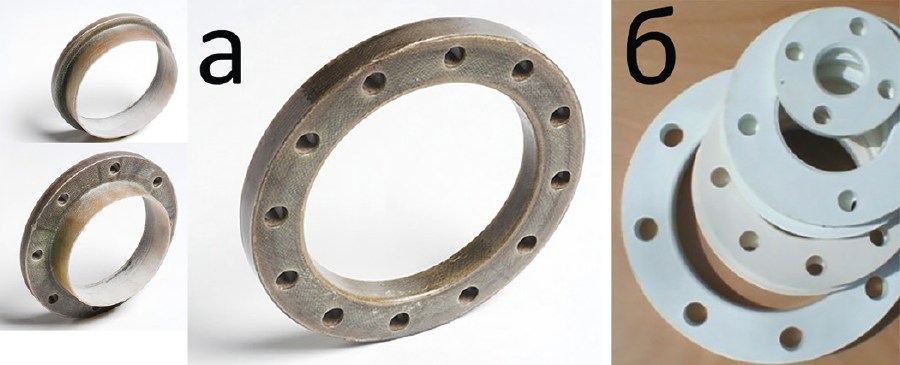
Рисунок 8. Фланцы, прессованные по технологии RTM (а) и из препрега SMC (б)
Хотя накидное кольцо свободного фланца часто выполняют стальным, кольца из химостойкого композита, полученные намоткой стеклянного жгута между прессованными матами, с успехом заменяют нержавеющие. Весьма перспективны комбинированные фланцевые кольца из препрега SMC, дополнительно армированные стеклохолстом непосредственно в процессе прессования. Немаловажно, что прессование при необходимости позволяет придать уплотнительной поверхности фланца невысокий концентрический рельеф, способствующий лучшему обжатию и удержанию мягкой прокладки. Выпуск подобных комплектующих, способных существенно сократить стоимость композитных фланцевых соединений, выгоден только в крупной серии, поэтому возможности их производства тесно связаны с широким внедрением композитов в химическую промышленность.
Не меньшую важность, чем строение композитного фланца, имеет способ его стыковки с трубой. ГОСТ [19] для установки фланцевых переходников канализационных труб рекомендует применять бандажное соединение, а безнапорные отводы меньшего диаметра приформовывать с помощью седловидных насадок. ГОСТ [2] допускает три возможных вида соединения: муфтовое клеевое, ламинированное бандажное и разъёмное с помощью ремонтного хомута. В [39] представлены результаты сравнения трёх вариантов адгезионного соединения фланцевого буртика с композитной трубой и бандажного присоединения к ней фиксированного фланца с патрубком. Ламинированный бандаж показал наиболее высокую стойкость к растягивающим, изгибающим и ветровым нагрузкам, а также к сложному нагружению при тепловом расширении трубопровода. Вместе с тем отмечается, что клеевые соединения более дёшевы, а по технологичности существенно превосходят ручное ламинирование, особенно в полевых условиях. Разработано множество модификаций муфтовых клеевых соединений, обеспечивающих быструю и надёжную стыковку фланцевых патрубков с трубой (например, [29]), показана их пригодность для трубопроводов высокого давления [40]. Особый случай представляют трубопроводы с термопластичным лейнером, применяющиеся для транспортировки особо агрессивных сред. Плоский фланец таких трубопроводов также плакирован по всей площади полимером, и при стыковке с трубой вначале выполняется сварка лейнера, а затем накладывается бандаж (рисунок 7в).
Особняком также стоят соединения двойных композитных трубопроводов для опасных продуктов и промышленных стоков. Внутренняя напорная труба в таких системах заключена в лёгкую стеклопластиковую оболочку, а в зазоре располагаются сигнализаторы утечки продукта. Клеевые или резьбовые фитинги напорной трубы дополнительно помещаются в химостойкий контейнер, имеющий фланцевый разъём (рисунок 9).
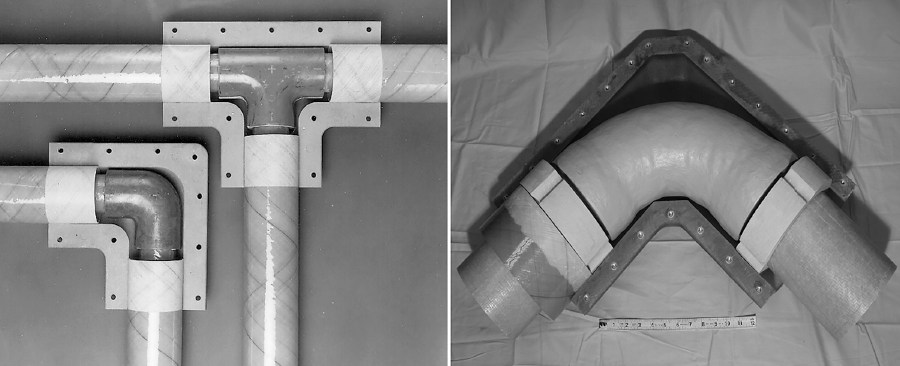
Рисунок 9. Стеклопластиковые контейнеры для фитингов двойных трубопроводов [41]
Подобные контейнеры изготавливаются по методу RTM либо контактным формованием, соответствуют DN от 75 до 400 мм и подвергаются пневматическим испытаниям под давлением от 100 до 30 кПа соответственно [41].
Материал и толщина прокладки
Для подключения композитных трубопроводов к стальным фланцам резервуаров и арматуры размеры прокладок должны соответствовать ГОСТ [42-43]. ГОСТ [2] нормирует размеры и характеристики только уплотнительных колец и упоров муфтовых соединений, а требования к плоским прокладкам, моментам затяжки фланцев и предельным отклонениям уплотнительных поверхностей должны указываться в технических условиях производителя.
Герметизация стеклопластиковых фланцев в системах водоснабжения обычно выполняется с помощью прокладок из листовой резины, для нефтепродуктов и многих растворителей годятся плоские полиуретановые прокладки с твёрдостью по Шору порядка 60–70 А, для агрессивных продуктов с успехом применяются ленты из растянутого (экспандированного) фторопласта, а при повышенных температурах — ленты из терморасширенного графита. При выборе материала прокладки следует руководствоваться не только его химической стойкостью и способностью заполнить неровности и компенсировать перекосы уплотнительных поверхностей, но и отсутствием ползучести, которая особо опасна при низких значениях давления обжатия и прокладочного коэффициента m, характерных для композитных фланцев. Давление обжатия различных материалов, приведённое в ГОСТ [12], составляет 2 МПа для резиновых прокладок, 4 МПа — для прокладок из терморасширенного графита и 10 МПа — для фторопласта-4 толщиной 1–3 мм. Поскольку предел прочности на сжатие полиэфирных стеклопластиков редко превышает 200 МПа, то для них желательней применять не листовой, а мягкий растянутый фторопласт. Плоские прокладки и ленты из данного материала предназначены для гладких фланцев, работающих под давлением до 4 МПа, имеют давление обжатия около 10 МПа и требуют «фактор m» порядка 1,5–2,5 [44]. Высокое потребное давление на прокладку ограничивает возможность использования растянутого фторопласта с обычными композитными фланцами номинальным давлением до 1 МПа (рисунок 10), но применение высокопрочных стеклопластиков горячего прессования способно поднять возможное значение PN до 1,6–2,5 МПа, поскольку материал прокладки это позволяет.
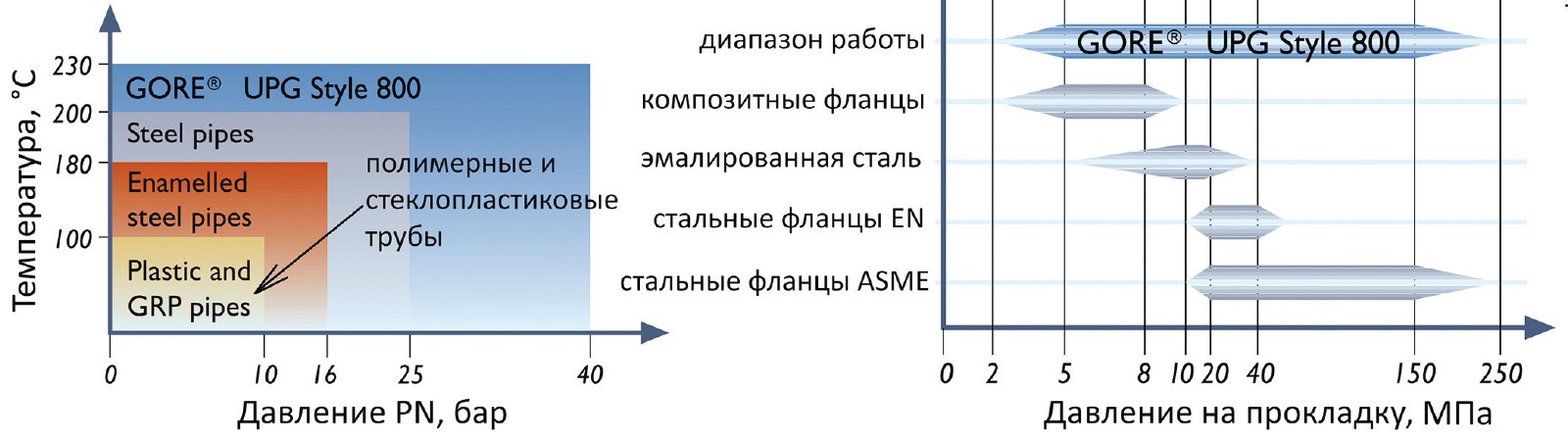
Рисунок 10. Применимость прокладок из растянутого фторопласта для композитных фланцев [44]
Остальные указанные в ГОСТ [12] значения «фактора у» мягких материалов находятся в допустимом для композитов диапазоне и много меньше предельного давления на прокладку, которое, например, для резины составляет около 20 МПа, а для терморасширенного графита превышает 100 МПа.
Важное значение для длительного сохранения потребной степени герметичности фланцевого соединения имеет толщина прокладки. Общим правилом здесь является выбор прокладки минимально возможной толщины, поскольку в данном случае минимальна площадь внутреннего торца, нагруженного давлением среды (рисунок 6).
Это даёт следующие преимущества:
- повышенную стойкость к выдавливанию;
- лучшую стойкость к температурным циклам;
- меньшую утечку;
- меньшую сжимаемость и возможность приложить более высокую нагрузку сжатия;
- меньшую неравномерность распределения давления по площади;
- меньшую стоимость прокладки [45].
Впрочем, очевидно, что податливые прокладки большей толщины лучше заполняют неровности поверхностей и компенсируют перекосы фланцев, а с учётом прочностных ограничений и большого диаметра композитных соединений разумным будет выбор минимально допустимой толщины порядка 3 мм, а не 1–1,5 мм, как рекомендовано в [45] для стальных фланцев с выступом. Для сравнения: принятый для стальных фланцев ГОСТ [42] устанавливает толщину прокладок из фторопласта-4 и прокладочной ленты от 1 мм для DN 10-32 до 3 мм для DN 350-500.
В соединениях трубопроводов высокого давления применение тонких прокладок особо желательно. Перспективным решением, позволяющим минимизировать толщину, не перегружая композитные фланцы чрезмерной затяжкой, может стать применение жидких полимеризующихся герметиков с целью создания уплотнения [46], однако для принятия этой технологии в качестве стандартной требуется большой объём исследований и длительные опытно-промышленные испытания. Традиционно же в соединениях высокого давления применяются фланцы типа шип паз, создающие весьма высокие контактные напряжения на уплотнительных поверхностях. Поскольку изготовление узкого выступа на плоскости композитного фланца проблематично, то выполняются только канавки для упругих кольцевых прокладок прямоугольного, круглого либо линзовидного сечения. В российских стандартах пока отсутствуют требования к уплотнениям композитных фланцев подобного типа, и разработка таких нормативов важна для широкого применения стеклопластиковых труб в газонефтепроводах и в химическом производстве, где особо востребована их коррозионная стойкость [36].
Момент затяжки гаек
Итак, плоские композитные фланцы создают низкое давление на прокладку, которое обычно не более, чем на порядок превышает номинальное PN. При этом болты должны воспринимать усилия не только от стягивания фланцев, но и от давления рабочей среды, действия внешних сил, изгибающих моментов и температурных деформаций, а прокладка — сохранять герметичность как при номинальном, так и при испытательном давлении. По данной причине контроль момента затяжки гаек стеклопластикового соединения выполняется весьма тщательно, и производители фланцев указывают допустимый его диапазон в технической документации.
Для примера на рисунке 11 графически представлены допускаемые диапазоны момента на ключе для плоских фланцев фирмы Fiberbond [47] и для наглядности выполнена линейная аппроксимация средних значений, а в таблице 2 приведены требования АО «АЗНТ» [48]. В обоих случаях данные указаны для сухой резьбы; в случае применения смазки согласно ГОСТ [12] величина момента снижается на 25%.
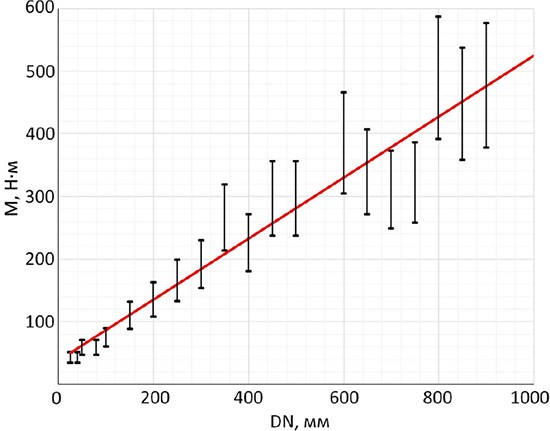
Рисунок 11. Момент затяжки шпилек композитного фланца с плоской резиновой прокладкой (PN = 1 МПа) [47].
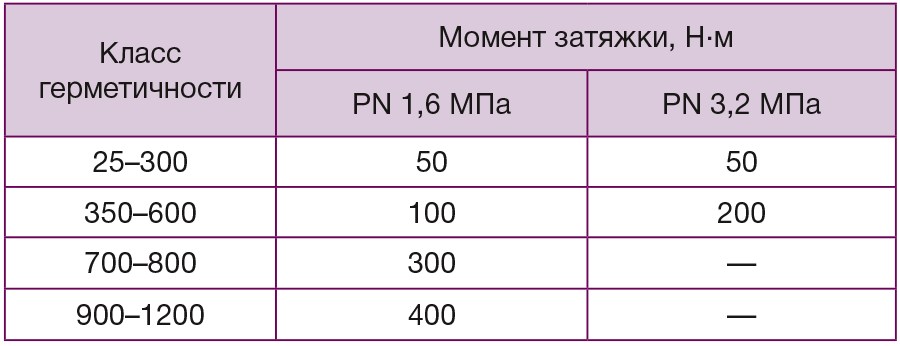
Таблица 2. Рекомендуемые моменты затяжки шпилек стеклопластиковых фланцев [48]
Сравнение показывает, что при DN до 700 мм фланцы АЗНТ требуют примерно вдвое меньшего момента затяжки, нежели Fiberbond, хотя и рассчитаны на большее давление. Судя по руководствам [47–48], разница объяснятся тем, что АЗНТ применяет прокладки по ГОСТ [42], тогда как Fiberbond — прокладки увеличенного диаметра в полный размер фланцев, с отверстиями под крепёж. Данный пример подтверждает необходимость разработки технических условий на стеклопластиковые фланцы с учётом размеров и свойств прокладок, поскольку на прокладке с чрезмерно широким полем уплотнения может не достигаться необходимое контактное давление [49]. Уменьшение наружного диаметра прокладки обеспечивает её обжатие при меньшей нагрузке и сокращает опасные сминающие напряжения в районе крепёжных отверстий фланца. Решение задачи расчёта момента затяжки фланцевых соединений и подбора оптимальной прокладки облегчают компьютерные программы — такие, как KLINGERexpert или «Новомет».
Помимо величины момента на ключе, для обеспечения герметичности большое значение имеет режим затяжки шпилек, число которых в соединениях большого прохода достигает нескольких десятков. Хотя порядок их затяжки должен быть определён техническими условиями, при установке мягких прокладок велик риск получить сильную неравномерность нагрузки по окружности фланца. По данной причине рекомендуется осуществлять одновременную затяжку минимум четырёх шпилек за один шаг и применять в процессе сборки соединения осевые ограничители сжатия [49–50].
Согласно ГОСТ [19] фланцевые соединения композитных труб подвергаются гидравлическим испытаниям на стойкость к изгибу и внутреннему давлению при 1,5PN и 2PN, на циклические колебания давления от атмосферного до 1,5PN и кратковременной опрессовке под давлением 2,5–3PN. Проводятся также пневматические манометрические испытания на герметичность под вакуумом до 0,08 МПа. Подобный объём испытаний предусматривает и ГОСТ [51], где подробно описаны методы проведения испытаний на стойкость соединений к давлению при одновременном воздействии осевой нагрузки или изгиба, а также прочностных испытаний композитных фланцев на стойкость к моменту затяжки болта. В целом нынешние испытания объединяют проверку механической прочности и герметичности фланцевого соединения, критерием работоспособности которого служит видимое отсутствие повреждений или течи. Для применения композитных фланцев в составе магистральных и технологических трубопроводов, подвергаемых опрессовкам по ГОСТ [11] и подобным проверкам, целесообразно применять методы пневматических испытаний с количественным определением степени герметичности соединения.
Хомуты и бугели
Как видим, перенос традиционных, тщательно отработанных и всесторонне стандартизованных конструкторско-технологических решений для стальных резьбовых и фланцевых соединений в мир полимерных композитов влечёт ряд проблем. Сравнительно с самоуплотняющимися муфтами соединения оказываются громоздкими, требуют приформовки патрубков, изготовления резьб с нехарактерной для композитов точностью, а фланцы к тому же — большого числа крепёжных деталей, тщательного контроля при сборке с мягкими прокладками и регулярного обслуживания в процессе эксплуатации. Хорошо известно, что механическое повторение в композиционных материалах стальных конструкций представляет типичную ошибку проектировщика, и данные примеры только подтверждают это общее правило.
Как же достигнуть потребной в нефтяной и химической промышленности высокой герметичности и безотказности разъёмных соединений композитных трубопроводов? Оказывается, давно известны соединения, сочетающие удобство муфт и герметичность фланцев. О них и пойдёт речь в последнем разделе.
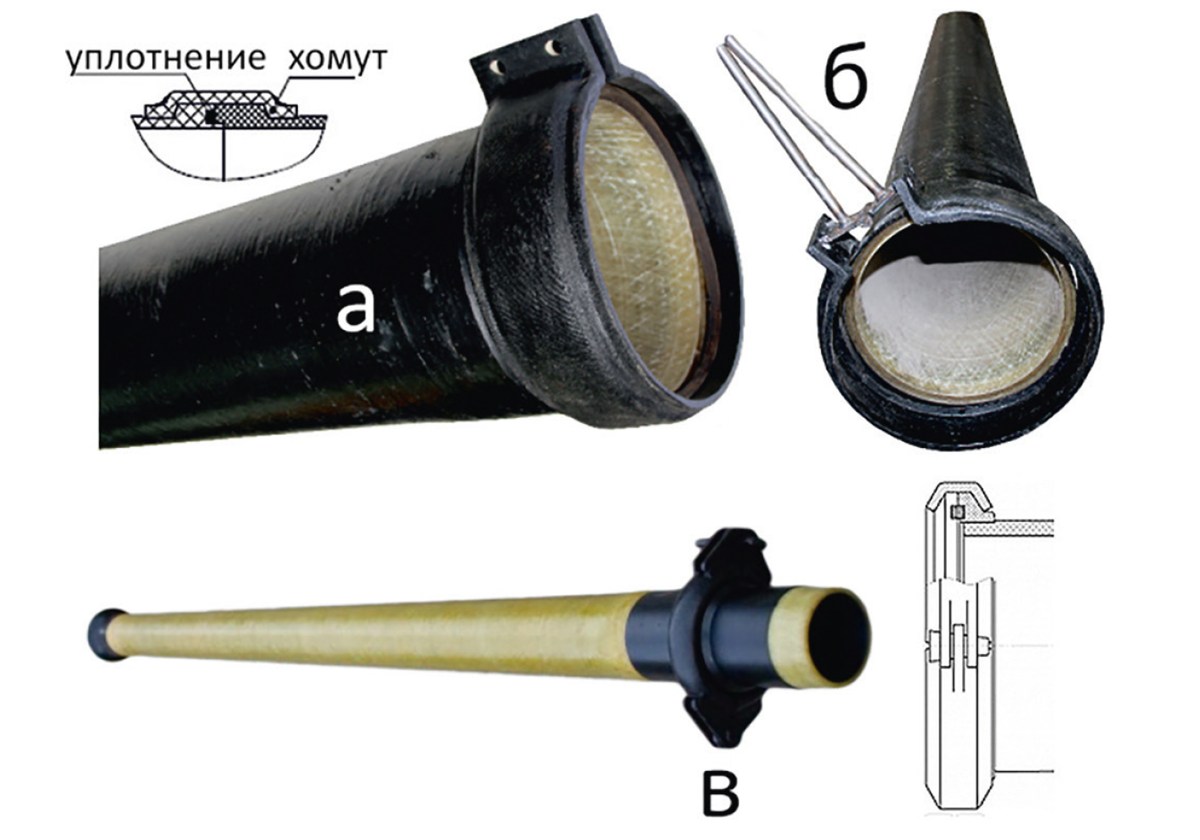
Рисунок 12. Стеклопластиковый хомут и бугельное быстроразъёмное соединение [52]
Во многих случаях резьбовое или фланцевое соединение с успехом может быть заменено металлическим или стеклопластиковым хомутом. Например, НПП «Алтик» выпускает хомут собственной конструкции, который, подобно бугелю, стягивает невысокие скошенные буртики у труб для дегазации угольных шахт (рисунок 12а). Газонепроницаемость стыка обеспечивает расположенная в торцовом пазе упругая прокладка, благодаря малой площади которой при стяжке хомута достигается высокое давление обжатия. В комплекте с партией труб поставляется монтажный разжимной ключ (рисунок 12б). В стеклопластиковых трубах для гидромониторов, работающих под давлением до 16 МПа, устанавливаются стандартные бугельные быстроразъёмные соединения, имеющие аналогичные уплотнения (рисунок 12в).
Ремонтные хомуты, применение которых для стеклопластиковых труб предусматривает ГОСТ [2], вполне могут служить для стационарного соединения труб большого диаметра, особенно в тех случаях, когда необходимость осевой подвижки, выполняемой при сборке муфт и раструбов, вызывает затруднения в ходе монтажа (и, что не менее важно, демонтажа!) трубопровода. Подобные соединения выпускает, например, фирма Victaulic. Показанные сверху на рисунке 13 соединения типа 230, нестойкие к растяжению, пригодны для стыковки стальных, полимерных и стеклопластиковых труб и выдерживают давление от 1,4 до 2,8 МПа в зависимости от диаметра и исполнения [53].
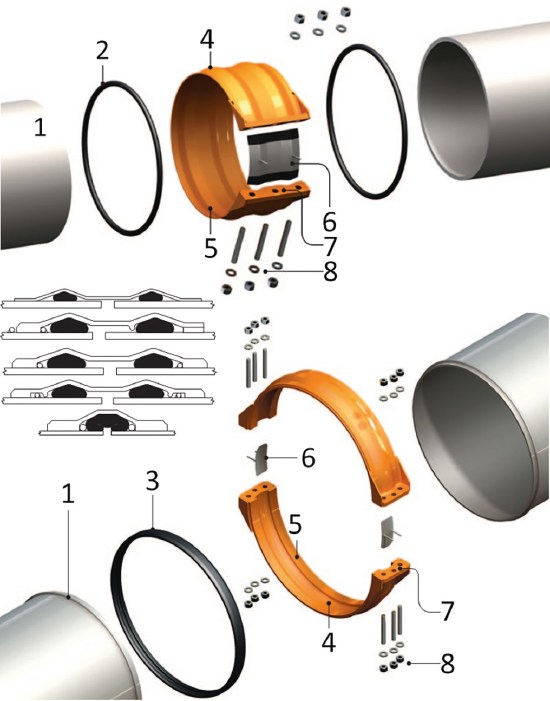
Рисунок 13. Хомуты для труб большого диаметра: 1 — труба, 2 — кольцо круглого сечения, 3 — фасонное кольцо, 4 — канавка под уплотнение, 5 — посадочный бурт, 6 — уплотнительные пластины, 7 — стяжные фланцы, 8 — крепёж [53]
Типоразмеры хомутов перекрывают диапазон DN от 200 до 3600 и обеспечивают их пригодность почти для всей номенклатуры стеклопластиковых труб по ГОСТ [19] (таблица 3). Специально предназначенные для низконапорных композитных труб похожие соединения типа 229S выдерживают давление 170 кПа.
Выпускается также ряд стойких к растяжению подобных соединений (рисунок 13, внизу). Они предназначены для труб из углеродистой и нержавеющей стали, к которым приваривается невысокое фиксирующее кольцо. Широкое применение стеклопластиковых муфт с гибким фиксатором (рисунок 4) показывает возможность использования указанных соединений с композитными трубами, имеющими неглубокий паз для пружинного фиксирующего кольца, которое, например, может быть выполнено из стеклопластика горячего прессования либо армированного термопласта. Это существенно расширит возможности применения хомутов для напорных композитных труб большого прохода. Кольцевые уплотнения хомутов, которые изготавливаются из EPDM, силиконовой резины, изопрена, нитрила, неопрена или фторопластового эластомера, пригодны для широкого ряда химических и нефтяных продуктов, однако следует учитывать, что контакт рабочей среды с уплотнением происходит на наружной поверхности трубы, которая может не иметь барьерного слоя в структуре композита. Открыты для коррозии и торцы труб. Это указывает на необходимость применения соединительных частей, обладающих должной химической стойкостью.
Для напорных стеклопластиковых труб, работающих под давлением до 1 МПа, предназначены соединения типа 296-А [54], имеющие DN от 25 до 300. Бугели изготавливаются из алюминиевого сплава, аналогичного АК7пч, а самоуплотняющиеся прокладки — из химостойких эластомеров. Стойкость соединений к осевому растяжению достигается посадкой в канавки, выполненные на соединительных частях трубы. Основным отличием данной конструкции от соединений подобного типа, предназначенных для стыковки стальных труб, является увеличенная ширина бугелей В, обеспечивающая высокий запас прочности на срез крепёжного участка композитной трубы (рисунок 14).
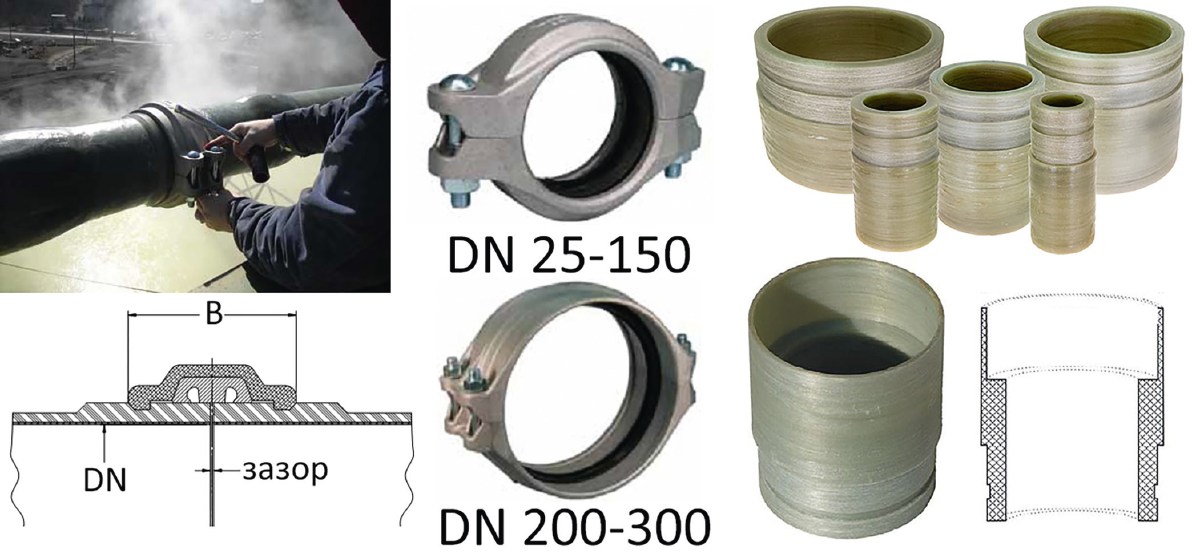
Рисунок 14. Самоуплотняющиеся бугели и стеклопластиковые соединительные части труб
Производитель нормирует размеры канавки и наружный диаметр посадочного патрубка, который весьма близок к наружному диаметру стеклопластиковых труб по ГОСТ [19] (таблица 4). Благодаря последнему во многих случаях концевые участки композитной трубы могут быть выполнены с незначительным утолщением для обработки под посадку бугеля. При необходимости обеспечения высокой коррозионной стойкости соединения (либо размещения его в произвольном месте трубы) патрубки с канавкой могут быть изготовлены отдельно (рисунок 14, справа).
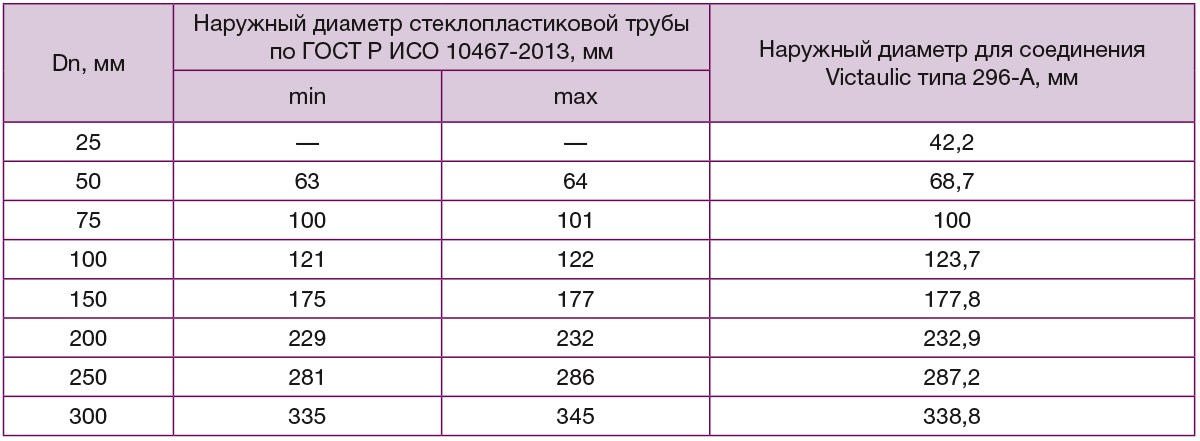
Таблица 4. Применимость бугелей типа 296-А для композитных труб
Соединения Victaulic принципиально отличаются от стандартных бугельных по ГОСТ [55], поскольку не нуждаются в скошенных буртиках на ниппелях, при обжатии которых создаётся осевое усилие и возникают опасные для композитов высокие контактные напряжения, и оснащены, подобно муфтам, самоуплотняющимися упругими кольцами. Данный тип соединения правильней именовать «бугельным с канавкой», либо, как часто делают, «соединением с обжимными муфтами». Быть может, нужный термин когда-нибудь появится в стандарте [1].
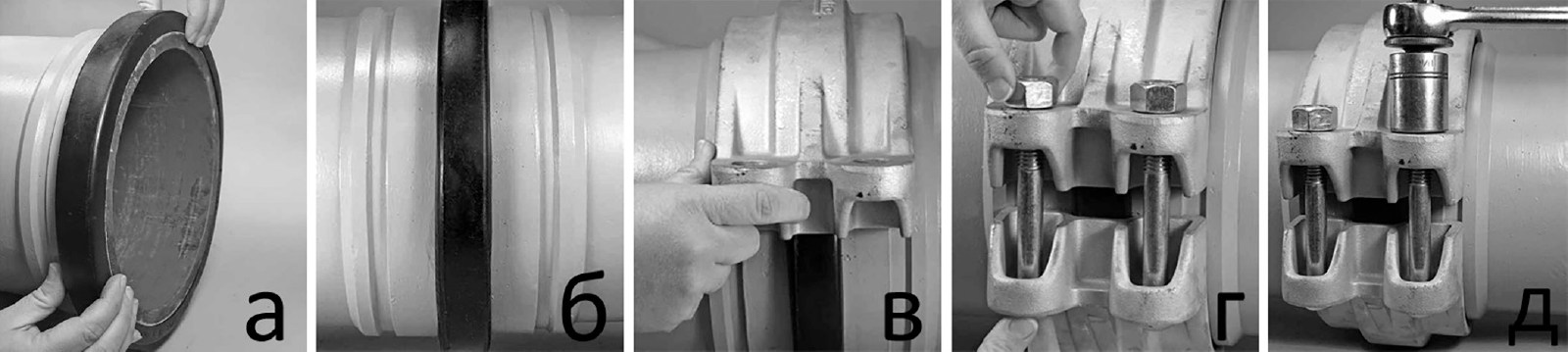
Рисунок 15. Сборка бугелей на композитной трубе [56]
Сборка бугелей не требует, в противоположность фланцам, тщательного контроля. После нанесения монтажной смазки кольцо полностью сдвигается на трубу (рисунок 15а), а при стыковке переводится в рабочее положение (рисунок 15б). Бугели помещаются поверх кольца (рисунок 15в), устанавливаются болты (рисунок 15г) и осуществляется их поочерёдная затяжка (рисунок 15д) до полного соприкосновения поверхностей разъёма [56]. Применение моментного ключа не требуется [57]. Бугели с плоским стыком обеспечивают соединение, по жёсткости подобное фланцевому, а бугели с косым стыком — более податливое соединение, допускающее ограниченный люфт труб.
При сборке бугеля по всему периметру уплотнения равномерно создаётся давление обжатия более высокое, чем у колец в муфтовых и раструбных соединениях и, вероятно, в среднем сопоставимое с требуемым ГОСТ [12] для резиновых прокладок фланцев. При использовании колец прямоугольного сечения одно это обеспечило бы близкую к фланцевому соединению степень герметичности, но форма их такова, что стык дополнительно уплотняется под давлением рабочей среды. Вдобавок соединение не требует осевой подвижки трубы при сборке, является устойчивым к растяжению, но благодаря упругости колец допускает, подобно муфтовому, некоторые перекосы, несоосности и взаимные смещения труб. Таким образом, бугели с канавкой объединяют достоинства фланцев и муфт, но лишены их недостатков.
Перечисленная комбинация свойств обеспечивает, помимо быстроты и удобства монтажа, следующие преимущества разъёмных соединений данного типа:
- компенсацию температурных и механических деформаций трубопровода без появления опасных напряжений: соединения применяются в сложных технологических системах с переменным температурным режимом;
- сейсмическую и ударную стойкость: соединения применяются в высотных зданиях, на особо опасных промышленных объектах, в корабельных трубопроводах;
- гашение вибраций и шума: соединения применяются в насосных и компрессорных станциях (где в отличие от ламинированных и резьбовых стыков не будут склонны к усталостной деградации композита).
Соединения Victaulic уже около века устанавливаются в стальных трубопроводах, где с успехом заменяют сварку, фланцы, резьбу, а с недавних пор бугели пришли на смену ламинированным бандажам в композитных трубах [58]. Выпускаются также различные стойкие к растяжению соединения для труб из термопластичных полимеров, в том числе прессованные из премикса ВМС и специально предназначенные для химически агрессивной окружающей среды (тип 171).
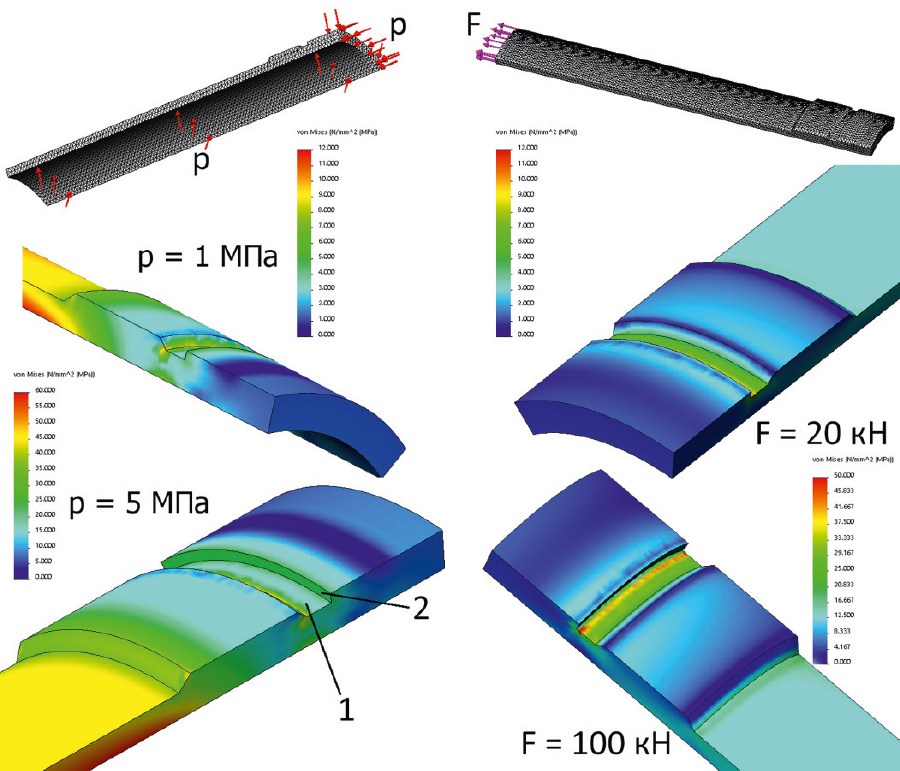
Рисунок 16. Оценка прочности соединительного участка композитной трубы
Номенклатура соединений для стеклопластиковых труб пока сравнительно невелика и настоятельно требует расширения в область более высоких PN. Ориентировочные оценки, выполненные для соединения типа 296-А проходом DN200 и PN 1 МПа, показывают его высокую стойкость к нагрузкам, вызванным внутренним давлением и осевым растяжением. Расчёт выполнен по осесимметричной модели в изотропном приближении для стеклопластика с модулем упругости около 1,4 ГПа и пределом прочности на растяжение 130 МПа. Оценки показывают, что при номинальном давлении соединительный участок работает с запасом прочности порядка 20, которой сокращается примерно до 4 при давлении 5 МПа. Конструкция обеспечивает большой запас прочности и при работе на срез: напряжения в районе поверхности 2 достигают 40-50 МПа только при растягивающей трубу нагрузке 100 кН, которая много больше силы, создаваемой давлением 5 МПа на торце трубы (рисунок 16). Очевидно, усиление соединительного участка и бугеля обеспечит потребную стойкость к высокому давлению, а прочность на срез, если потребуется, можно повысить, используя прессованные из плетёных преформ патрубки. Нет оснований сомневаться в применимости данных соединений для композитных труб с PN порядка 3,2–6,3 МПа, а возможность подняться к более высоким давлениям требует изучения.
О высокой герметичности самоуплотняющихся бугелей свидетельствует их пригодность для горючих и агрессивных газов и паров, однако количественное определение степени герметичности данных соединений и разработка нормативов их использования на взрывопожароопасных производствах представляет актуальную и важную задачу.
Список литературы
- ГОСТ Р 54559-2011. Трубы и детали трубопроводов из реактопластов, армированных волокном. Термины и определения
- ГОСТ Р 54560–2015. Трубы и детали трубопроводов из реактопластов, армированных стекловолокном, для водоснабжения, водоотведения, дренажа и канализации. Технические условия
- ГОСТ Р 56277-2014. Трубы и фитинги композитные полимерные для внутрипромысловых трубопроводов. Технические условия
- Божко Г. В. / Разъёмные герметичные соединения / Вестник ТГТУ. 2010. т. 16. № 2. с. 404–420
- Волошин А. А., Григорьев Г. Т. / Расчет и конструирование фланцевых соединений: Справочник. 2 е изд., перераб. и доп. / Л.: Машиностроение, Ленингр. отделение. 1979. 125 с.
- Продан В. Д. / Герметичность разъемных соединений оборудования, эксплуатируемого под давлением рабочей среды / Тамбов: Изд-во ФГБОУ ВПО «ТГТУ». 2012. 280 с.
- Огар П. М. / Контактные характеристики и герметичность неподвижных стыков пневмогидротопливных систем двигателей летательных аппаратов / Автореферат дисс. д.т.н. Самара. 1997.
- Mertiny P., Gold A. /Quantification of leakage damage in high-pressure fibre-reinforced polymer composite tubular vessels // Polymer Testing. 2007. v. 26. Pp. 172-179.
- ОСТ 26.260.14-2001. Сосуды и аппараты, работающие под давлением. Способы контроля герметичности.
- ГОСТ 24054-80. Изделия машиностроения и приборостроения. Методы испытаний на герметичность. Общие требования.
- ГОСТ 25136-82. Соединения трубопроводов. Методы испытаний на герметичность.
- ГОСТ Р 52857.4-2007. Сосуды и аппараты. Нормы и методы расчёта на прочность. Расчёт на прочность и герметичность фланцевых соединений.
- Montero F. J. /Tightness in Gasketed Flanged Unions. Part 1: The Background and the Challenges // Valve World. 2012. Sept. Pp. 1-2.
- Montero F. J. /Tightness in Gasketed Flanged Unions. Part II: New Standards for Calculation and Testing. The early attempts in the USA and Germany / Valve World. 2012. Nov. Pp. 163-164.
- Montero F. J. / Tightness in Gasketed Flanged Unions. Part III: New Standards for Calculation and Testing. The European Standards // Valve World. 2013. Feb. Pp. 84-85.
- СП 40-102-2000. Проектирование и монтаж трубопроводов систем водоснабжения и канализации из полимерных материалов. Общие требования.
- ГОСТ Р 55876-2013. Трубы и детали трубопроводов из реактопластов, армированных стекловолокном. Методы испытаний. Испытания на герметичность подвижных соединений.
- Fahrer A., Gibson A.G., Tolhoek P. / A study of the failure behaviour of key-lock joints in glass fibre reinforced plastic pipework / Composites Part A: Applied Science and Manufacturing. 1996. Vol. 27. № 6. Pp. 429-435.
- ГОСТ Р ИСО 10467-2013. Трубопроводы из армированных стекловолокном термореактопластов на основе ненасыщенных полиэфирных смол для напорной безнапорной канализации и дренажа. Общие технические требования.
- ASTM D2517–06. Standard Specification for Reinforced Epoxy Resin Gas Pressure Pipe and Fittings.
- Нагиев Р. А., Иванов К. В., Муртазина Э. И. / Научно-технический аспект мероприятий по обеспечению герметичности оборудования в химической, нефтехимической и нефтегазоперерабатывающей промышленности / Евразийский Научный Журнал. 2015. № 9. C. 10 13.
- ГОСТ 6211-81. Основные нормы взаимозаменяемости. Резьба трубная коническая.
- ASTM D1694. Standard Specification for Threads for Glass Fiber Reinforced Thermosetting Resin Pipe.
- Sullivan D. Curran P.E. Fiberglass Pipe. Past, Present and Future / Fiberglass Tank & Pipe Institute. 2013.
- ГОСТ Р 53201-2008. Трубы стеклопластиковые и фитинги. Технические условия.
- ГОСТ 633-80. Трубы насосно-компрессорные и муфты к ним. Технические условия.
- ГОСТ 24157-80. Трубы из пластмасс. Метод определения стойкости при постоянном внутреннем давлении.
- Mertiny P., Ursinus K. / A methodology for assessing fatigue degradation of joined fibre-reinforced polymer composite tubes // Polymer Testing. 2007. Vol. 26. Pp. 751–760.
- Takashi S., Toshiharu I., Pushpendra K., Shinichi T., Yoshinori N. / Screw joint parts for high pressure & low cost FRP pipes / Proceedings of International Conference and Exhibition on Reinforced Plastics. Mumbai, India. 2011.
- ГОСТ 27456-87. Соединения трубопроводов резьбовые. Порядок испытаний на вибропрочность.
- ГОСТ 54432-2011. Фланцы арматуры, соединительных частей и трубопроводов на номинальное давление от PN 1 до PN 200. Конструкция, размеры и общие технические требования.
- Gasket Handbook. A Technical Guide to Gasketing & Bolted Joints / Lamons. 2013.
- Kasprzyk J., Sieczkowski R. / Blow out safety in flange connections / Valve World. 2011. Sept. Pp. 1 2.
- Wacker R. Primary flange forces / Valve World. 2016. March. Pp. 1-2.
- ГОСТ 12815-80. Фланцы арматуры, соединительных частей и трубопроводов на Ру от 0,1 до 20,0 МПа. Типы. Присоединительные размеры и размеры уплотнительных поверхностей.
- Маллинсон Дж. / Применение изделий из стеклопластика в химических производствах / М.: «Химия». 1973. 240 c.
- Fiddes D. E., Lazarou J. / Press moulded flanges for GRP pipe systems / Composites. 1972. № 11. Pp. 254–258.
- ГОСТ Р 50073-92. Соединения трубопроводов разъемные фланцевые. Технические условия.
- Fiberglass reinforced plastic (FRP) piping systems: a comparison of two joining methods — the adhesive bonded joint VS the butt & strap method / EDO Specialty Plastics — Engineering Series. Oct. 2001.
- Mertiny P., Ellyin F. / Joining of fiber-reinforced polymer tubes for high-pressure applications / Polymer Composites. 2006. Vol. 27. № 1. Pp. 99-109.
- FiberGlass Systems. Secondary Containment Pipe and Two-Piece Fittings / www.frpsolutions.com
- ГОСТ 15180-86. Прокладки плоские эластичные. Основные параметры и размеры.
- ГОСТ 28759.6-90. Прокладки из неметаллических материалов. Конструкция и размеры. Технические требования.
- Specma seals handbook. Gasket and seals product guidelines and manuals. 2016 / www.specmaseals.se
- Rotar M. / What gasket thickness should I use in my flange system? / Valve World. 2014. Nov. Pp. 1 2.
- Ряховский О. А., Малышева Г. В., Воробьев А. Н. / Новый способ герметизации стыка фланцев корпусов при высоком внутреннем давлении / Известия ВУЗов. Машиностроение. № 5. с. 29–33.
- Fiberbond Recommended Flange Torques / www.fiberbond.com/docs/TorqueCharts.pdf
- Руководящий документ по монтажу стекловолоконных трубопроводов производства АО «АЗНТ». 2012.
- Епишов А. П. / Герметизация фланцевых соединений: кажущаяся простота. 2013. / www.sealing.su
- РД ЭО 0198-2000. Техническое обслуживание и ремонт систем и оборудования АС. Сборка фланцевых соединений. Общие технические требования.
- ГОСТ Р 55875-2013. Трубы и детали трубопроводов из реактопластов, армированных стекловолокном. Методы испытаний. Испытания болтового фланцевого соединения.
- НПП «Алтик». / Стеклопластиковые трубы промышленного назначения. 2012. / www.altik.su
- Victaulic Style 230 Non-Restrained Flexible Coupling 60.01. / www.victaulic.com
- Victaulic Style 296-A Coupling for Fiberglass Reinforced Plastic Pipe / www.victaulic.com
- ГОСТ Р 55429-2013. Соединения трубопроводов бугельные разъемные. Конструкция, размеры и общие технические условия.
- FRP/GRP Pipe Coupling Style 296A Installation Manual / www.victaulic.com
- Dole D. Joining FRP pipe with grooved couplings / Energy-Tech Magazine. 2014. / www.energy-tech.com
- Raymond C. Coupling for Fiberglass: An Alternative to Curing / Power Engineering. 2013. № 9. Pp. 50–52.