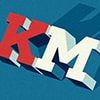
Утилизация композитов: проблемные аспекты и перспективные решения
рубрика: технологии
Развитие отрасли производства композитных материалов с 2013 года относится к приоритетному направлению развития промышленности РФ. Реализация этой программы приносит свои плоды. За последние годы наблюдается уверенный рост объёмов производства и потребления ПКМ различного типа, создаются стандарты и своды правил по их применению в ведущих отраслях (строительстве, авиации, специальном и транспортном машиностроении, производстве товаров народного потребления и так далее), расширяется объём научных и экспериментальных исследований в области композитов.
По оценкам экспертов, общий объём производства изделий из полимерных композиционных материалов (ПКМ) в России к 2020 году достигнет 120 тысяч тонн. Но даже такой объем займет незначительную долю от мирового композитного рынка, на котором доминирует Китай (28%), США (22%), ЕС (14%) [1].
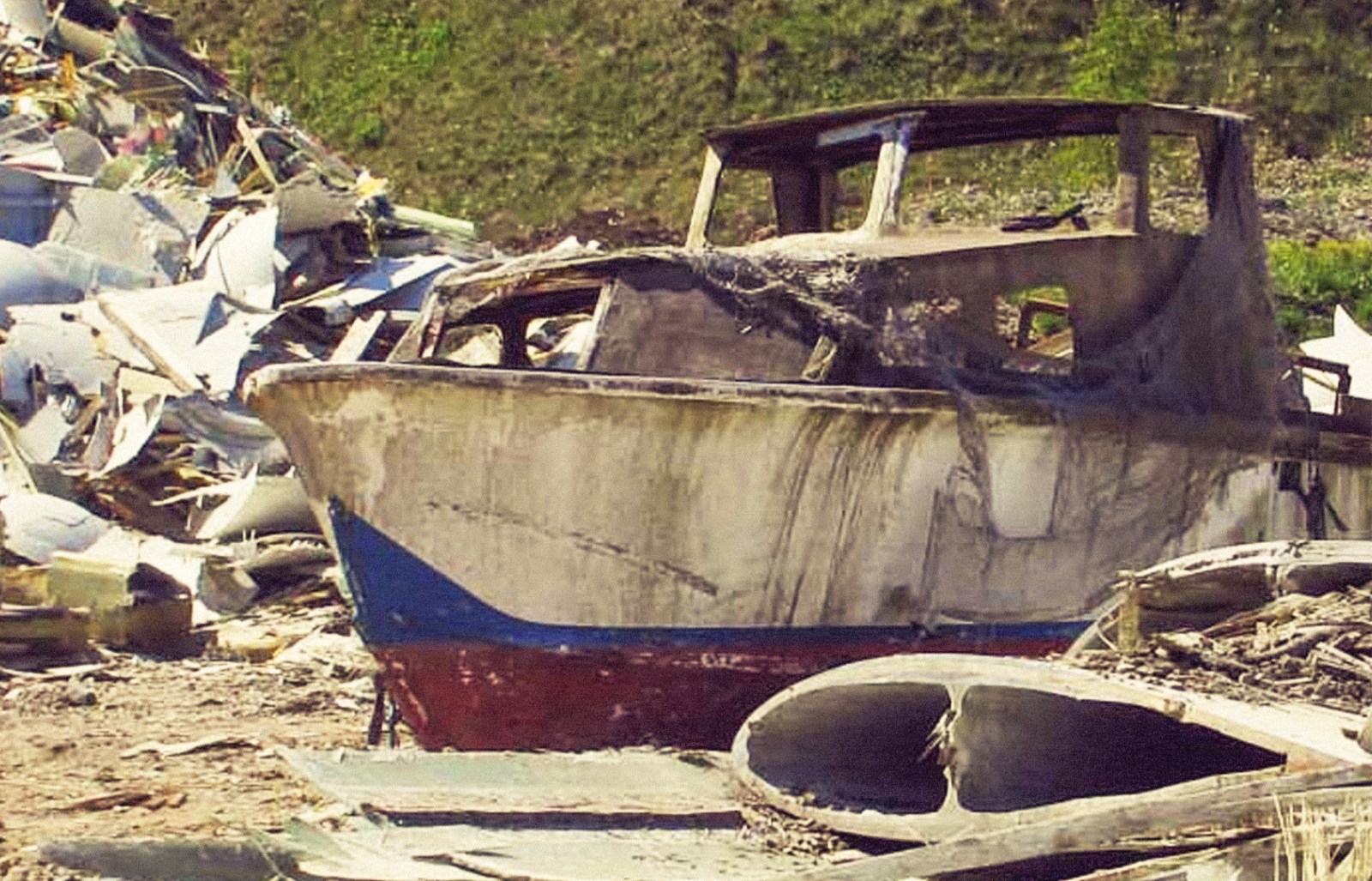
Увеличение производства и потребления ПКМ неизменно влечёт за собой рост отходов, возникающих как на этапе производства, так и по окончании срока службы изделий. В связи с этим вопрос утилизации и/или переработки ПКМ с каждым днём становится все более острым. Ряд стран и международных организаций настаивают на рассмотрении в качестве стратегического направления развитие безотходных технологий, производств замкнутого цикла. Такой подход не требует отсутствия отходов как таковых, но предполагает минимизацию их количества, предусматривает их использование в сопутствующих продуктах или возможность повторного применения с параллельной разработкой наиболее рациональных программ рециклинга.
Согласно европейскому законодательству (Директива Европейского Парламента и Совета Европейского Союза 2008/98/ЕС) существует приоритетность методов управления отходами, исходя из которой способ складирования по приоритету ниже сжигания. Наиболее приемлемым вариантом утилизации ПКМ с сопутствующим повышением энергоэффективности композитного производства является их переработка с целью повторного использования полученных при этом продуктов.
Такая иерархия целесообразна не только с точки зрения охраны окружающей среды, но и при рассмотрении вопросов экономии ресурсов: складирование отходов не позволяет получать экономическую выгоду от материалов, характеризующихся относительно высокой стоимостью и энергозатратностью производства исходных компонентов.
Полимерные композиты позволяют создавать уникальные комбинации полезных свойств, востребованных для каждого конкретного приложения: высокая прочность, химическая и биологическая стойкость удачно сочетаются с низким удельным весом конечных изделий, их долговечностью и низкими затратами на эксплуатацию.
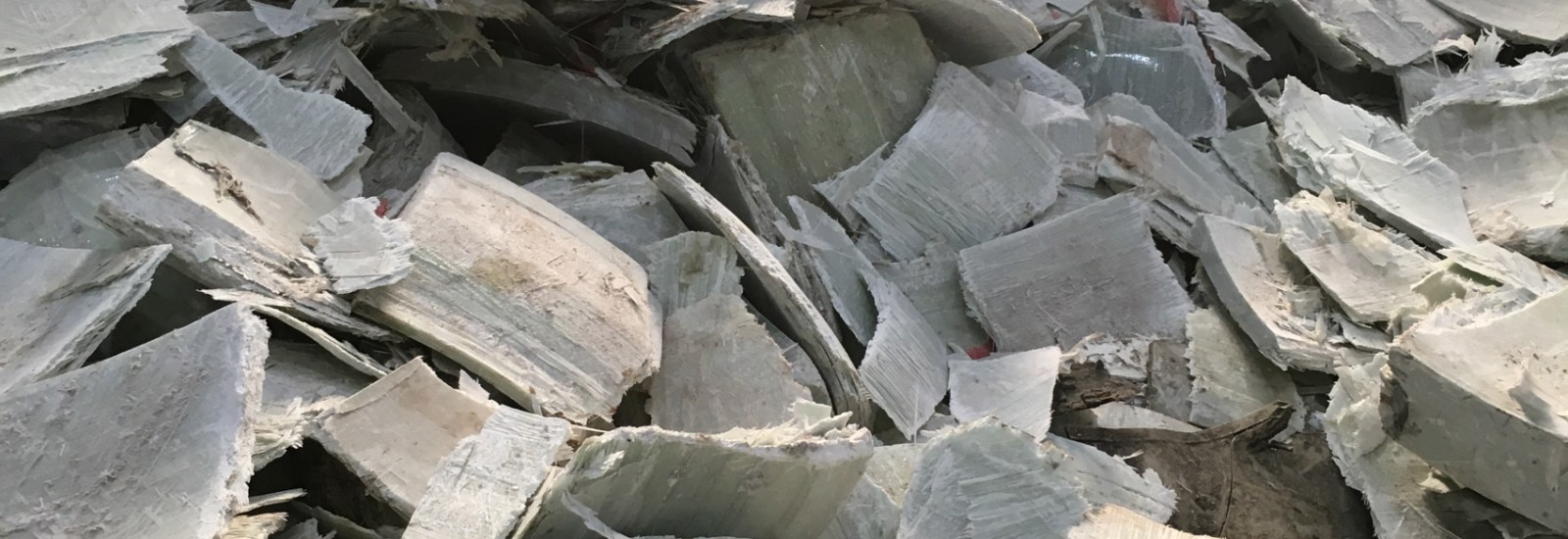
Малая подверженность композитов к разрушению под действием факторов окружающей среды является неоспоримым преимуществом при рассмотрении аспектов эксплуатации и обслуживания. Но при этом проблема утилизации отработанных изделий из ПКМ на фоне ежегодно растущего производства становится всё более актуальной.
Складированные на полигонах отходы композитных материалов разлагаются крайне медленно и оказываются фактором, загрязняющим окружающую среду.
Из всего разнообразия композитных материалов в данной статье рассматриваются, в первую очередь, армированные непрерывными либо дисперсными волокнами композиции на основе термореактивных либо термопластичных связующих.
Среди волокон наиболее широко используются углеродные, базальтовые, стеклянные, реже — арамидные, органические, борные и так далее. Рассматривая наиболее распространенные волокна, следует отметить сложную технологию производства и потребность в большом количестве химических реагентов для получения заданного качества волокна в случае со стекло- и углеволокном (в отличие от базальтовых волокон).
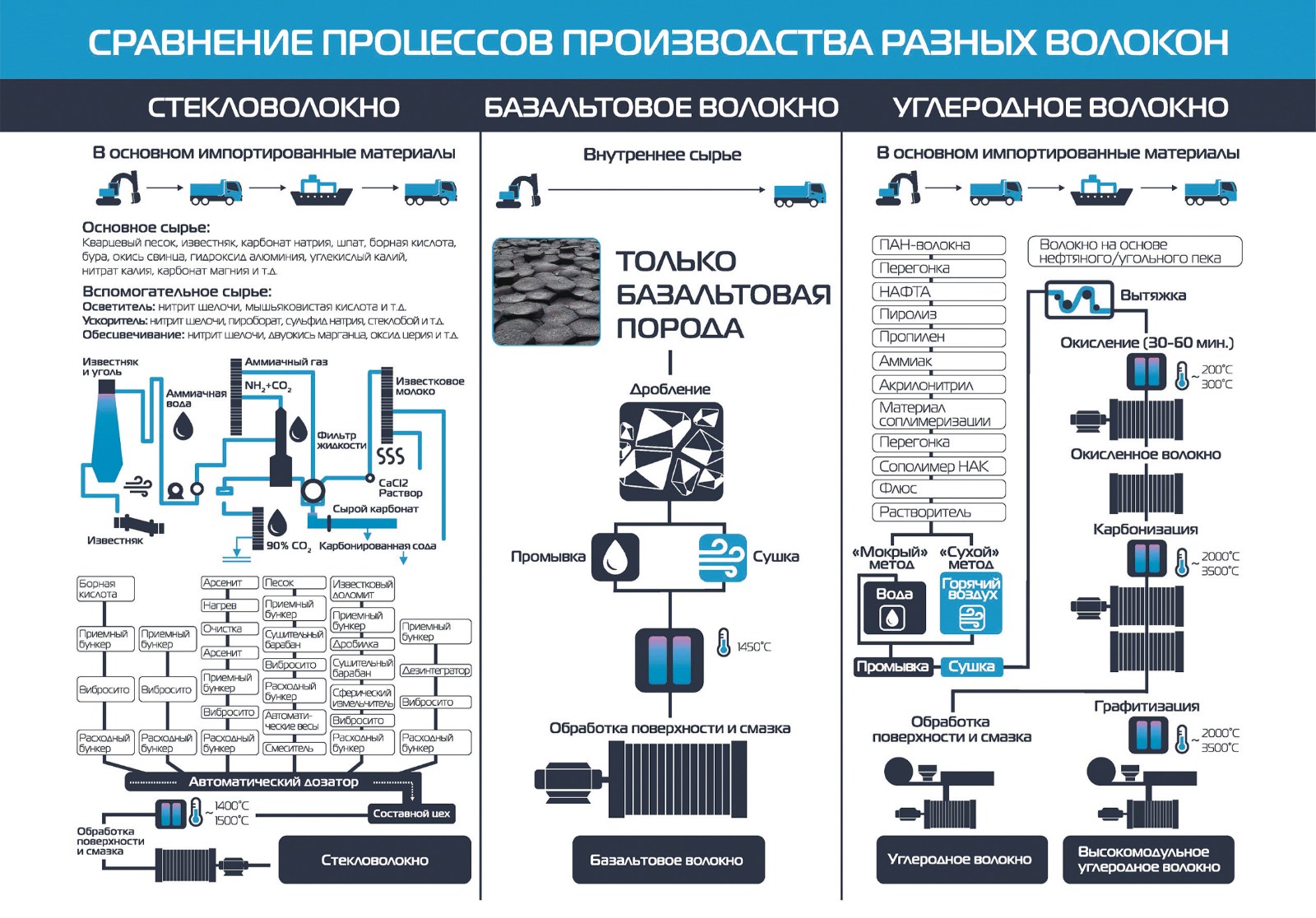
Попадание отходов стекло- и углеволоконной промышленности в окружающую среду негативно сказывается на ее состоянии, а высокая энергозатратность производственного процесса стимулирует повышенный интерес к развитию способов вторичного использования отработанных волокон в качестве основного/дополнительного армирующего материала в менее нагруженных изделиях.
Среди термореактивных смол наибольшее распространение получили эпоксидные, полиэфирные, фенолформальдегидные, винилэфирные, кремнийорганические составы. Данный тип связующих характеризуется прочной структурой и трудно поддается переработке, однако современные исследования показывают, что деполимеризованное связующее может быть повторно использовано в синтезе смол.
К термопластам относятся хорошо изученные и сравнительно легко перерабатываемые полиэтилены, полиамиды, полиуретаны, поливинилхлориды и другие соединения. Способность этих материалов к многократному размягчению под воздействием относительно невысоких температур способствует их широкому применению в качестве вторичного сырья. Однако перечисленное относится только к исходным компонентам композитов либо чистым отходам производства, в то время как для решения задачи утилизации отработавших срок изделий должны быть одновременно учтены свойства и особенности каждого компонента — как связующего, так и наполнителя.
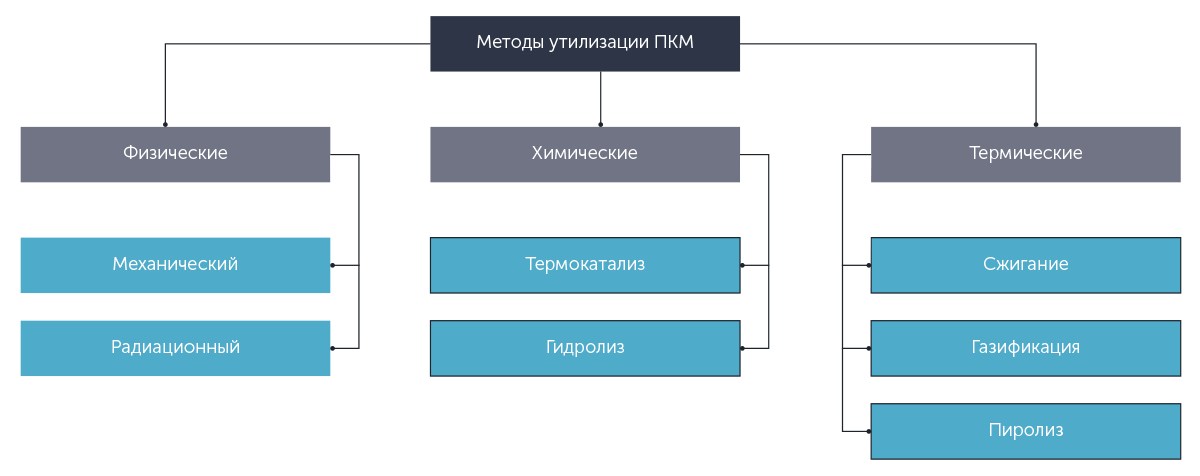
Анализ европейского опыта в области рециклинга отходов позволяет выделить 3 основных группы методов по утилизации ПКМ:
- основанные на физических способах переработки полимеров;
- основанные на химическом разложении связующего с частичным/полным сохранением волокон;
- основанные на термическом полном/частичном разложении полимеров и волокон.
Физические способы переработки могут быть применимы практически к любым типам композитов, а также характеризуются минимальным воздействием на окружающую среду. Относящийся к этой группе механический метод основан на измельчении ПКМ, при этом получаемые при измельчении фракции могут быть разной крупности в зависимости от способа дальнейшего применения.
Отходы на основе реактопластов, переработанные таким методом, пригодны для использования в качестве наполнителя для создания новых изделий и материалов. Измельченные волоконно-армированные термопласты могут добавляться в небольшом количестве наравне с первичным сырьем при формовке термопластичных композитов.
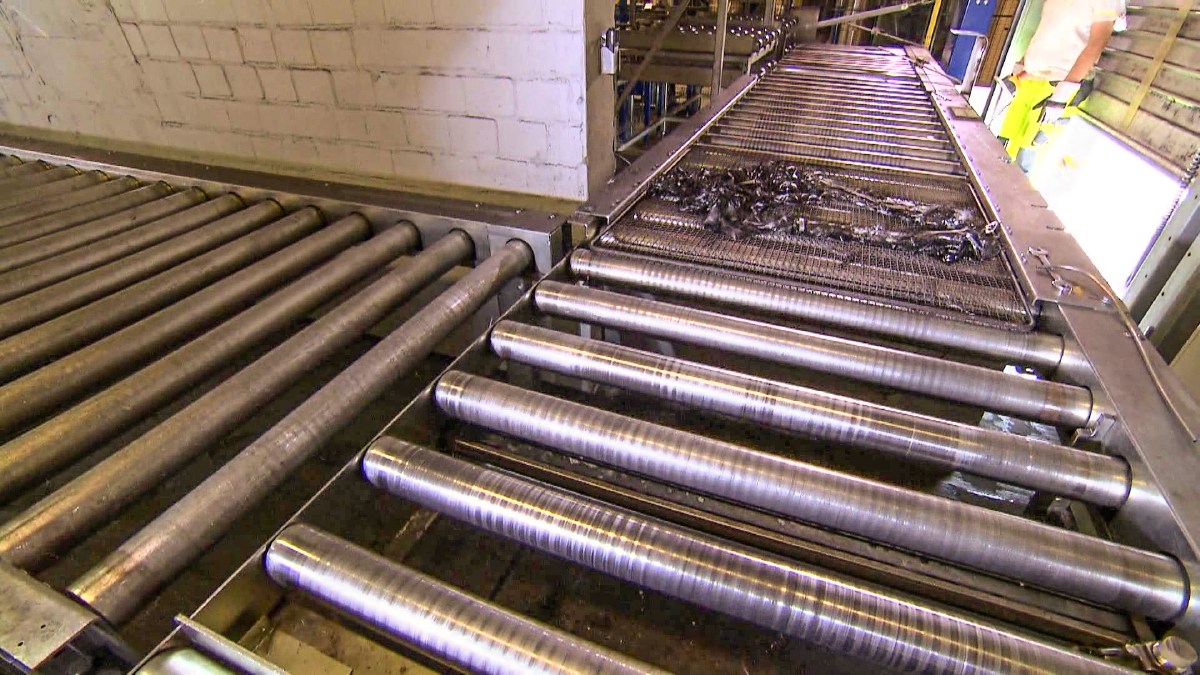
Механический метод характеризуется сравнительной простотой, отсутствием выбросов и, как следствие, негативного воздействия на окружающую среду. Кроме того, он универсален: этим способом можно перерабатывать практически любые композиции. Однако стоит учитывать энергоёмкость процесса измельчения ПКМ, армированных высокопрочными волокнами.
Радиационные методы основаны на разрушении полимера при помощи высокоэнергетического излучения и так же применимы практически для любых ПКМ. Суть методов заключается в разрушении полимерной матрицы, при этом природа армирующего материала практически не имеет значения. В случае с композитами, армированными углеродным волокном, волокно может быть частично или полностью сохранено без ущерба для его физико-механических характеристик.
Группа химических методов рециклинга является часто встречающейся за рубежом и характеризуется высокой энергетической эффективностью. Химическое воздействие, подобранное непосредственно для конкретной комбинации волокна и матрицы, позволяет получить на выходе максимально возможное количество продукта, пригодного для повторного использования в различных целях, с минимальными затратами времени и ресурсов. В группе термокаталитических методов выделяются методы сольволиза и окисления в псевдоожиженном слое как наиболее перспективные направления, получившие распространение в странах со значительным объёмом производства полимеров.
Сольволиз применим для полимерных композитов на основе реактопластов (в частности, эпоксидных смол). Рециклинг методом сольволиза позволяет получить на выходе не только очищенное от полимера волокно с приемлемыми характеристиками прочности, но и продукты разложения связующего, пригодные для использования при синтезе эпоксидов. Процесс окисления ПКМ в псевдоожиженном слое проходит посредством подачи горячего газа через слой дисперсного наполнителя (например, кварца) в закрытую камеру, в которую помещён подлежащий утилизации материал. Такой способ позволяет окислить полимерное связующее, нарушив химическую связь поверхности волокна с его частицами, после чего поток горячего газа уносит окисленные частицы связующего, защитных покрытий, красок и так далее, оставляя в камере очищенное волокно.
Переработка гидролизом применима для термопластов (в частности, полиуретанов). В качестве полезного продукта при использовании этого метода может быть получен высокомолекулярный спирт, практически не уступающий по качеству первичному, в дальнейшем используемый как компонент для синтеза эластичных пен.
Группа термических методов включает в себя три ключевых направления, отличающихся друг от друга требованиями к содержанию кислорода в атмосфере камеры. Пиролиз, проходящий в бескислородной среде, на сегодняшний день является самым распространенным способом утилизации армированных композитов. Метод позволяет не только получить очищенное от полимера волокно с приемлемыми для последующего использования характеристиками, но и использовать тепловую энергию, получаемую при деструкции полимера, а также некоторые полезные компоненты его распада. К особенности метода относится требование по термостойкости волокон: пиролиз осуществляется при повышенной температуре (от 300 до 1500°С в зависимости от разновидности), следовательно, применим для термостойких базальтовых, стеклянных и углеволокон. Получаемые на выходе армирующие материалы чаще всего представляют собой измельченные волокна и пригодны для повторного использования в задачах армирования малонагруженных термопластов, бетонов, в качестве сырья для теплоизоляционных материалов и армирующей добавки для композитов различного назначения на основе реактопластичной матрицы.
Газификация протекает при дефиците кислорода и представляет собой способ разложения полимерных композитов с получением газов, используемых для производства тепло- и электроэнергии. Применение этого метода исключает возможность сохранения волокон и не исключает вероятность попадания газообразных продуктов разложения в атмосферу.
Сжигание композитов проводят при содержании кислорода, превышающем стехиометрическое соотношение. Согласно директиве 2008/98/EC этот метод применим только к тем компонентам, к которым невозможно применить другие, более предпочтительные методы утилизации.
В действительности полезным продуктом сжигания в большинстве случаев является только образующаяся тепловая энергия, в то время как сам материал полностью разрушается. Однако существующие исследования в области сжигания ПКМ позволяют говорить о возможности сохранения армирующего компонента, представленного в виде термостойких волокон.
Исследования технологического университета Вены (Австрия) показывают перспективность травления поверхности волокон, способного ликвидировать последствия воздействия высоких температур и вернуть волокно, прошедшее процедуру сжигания, в производство композитов [2]. Данные выводы были сделаны на основании экспериментальных исследований, при которых волокна, предварительно прошедшие термическую обработку, подвергли травлению. Большинство исследованных волокон продемонстрировало потерю прочности почти в 2 раза, однако показатели прочности двух образцов, включая базальтовое волокно, после травления достигли значений, составляющих более 80% от исходной прочности. Дальнейшее изучение такого подхода может увеличить выход полезного продукта при утилизации ПКМ методами сжигания.
При рассмотрении проблемы утилизации ПКМ необходимо не только разрабатывать методы переработки композитов, но и изначально закладывать возможность рециклинга в изделия. Существующие наработки в области синтеза биосмол, пригодных для повторного использования, а также специфика армирующих материалов природного происхождения (базальтовые, льняные, конопляные и другие волокна) открывают широкие возможности для создания изделий с нужными механическими характеристиками при заранее решенной проблеме переработки.
Исходя из результатов, полученных компанией, среди множества вариантов восстановления чистого волокна из отверждённого ПКМ именно обогащённое базальтовое волокно может быть полностью переплавлено для получения нового волокна с такими же физико-механическими свойствами. Отходы производства (обрезки, остатки ткани) компания измельчает и перерабатывает в маты, в дальнейшем используемые при создании малонагруженных композитных изделий методом прессования.
Список использованных источников
- Подпрограмма «Применение композиционных материалов и изделий из них в Калужской области» государственной программы Калужской области «Экономическое развитие в Калужской области», стр. 2
- basalt.today/ru/2016/10/7697/
- basalt.today/ru/2017/03/9679/
- basalt.today/ru/2018/01/14594/