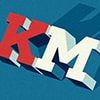
Изготовление композитных элементов декора зданий по технологии вмазывания формовочного компаунда в форму
рубрика: технологии
Заглавной темой настоящей статьи выбрана, на первый взгляд, одна из самых архаичных технологий изготовления изделий из искусственного камня, но при этом имеющая свои неоспоримые преимущества.
Речь пойдет о создании из композитов элементов внешнего декора зданий (фризов, карнизов, пилястр, руст, колонн, наличников и других). Существует несколько технологий изготовления этих элементов из искусственного камня. Но самые красивые и более представительные изделия получаются именно по примитивной технологии «вмазывания». Дело в том, что благодаря малому содержанию связующего (полиэфирной смолы) в поверхностном слое, текстура лицевой стороны у изделия получается наиболее похожей на натуральный камень, открывающей всю красоту наполнителя (мрамор, кварц и др.), а это сегодня особенно востребовано.
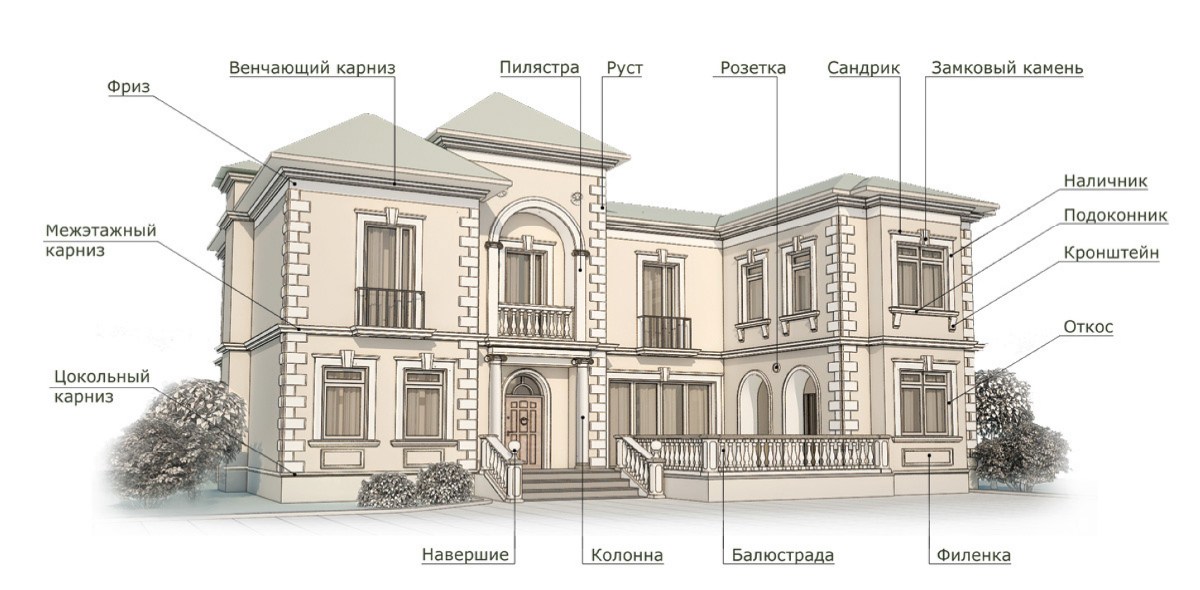
Рассмотрим принцип данной технологии на примере изготовления основания колонны. Другие элементы декора производятся аналогично. И первой стадией практически любого композитного производства является изготовление формы будущего изделия.
Изготовление формы из силикона
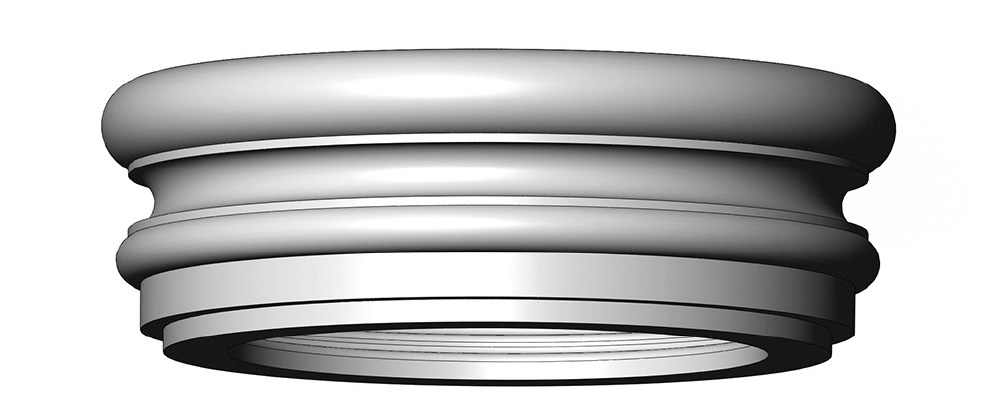
Рисунок 1. Готовое изделие, сложенное из 4-х четвертинок
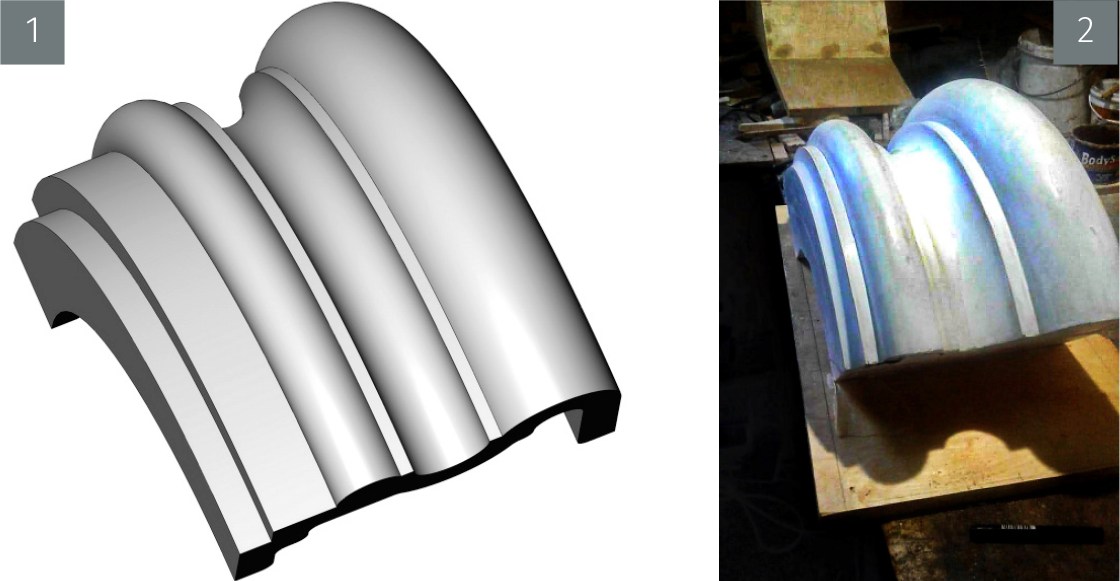
Рисунок 2. Четвертинка, которую возьмем как модель для изготовления силиконовой формы: 1 — графическая модель, 2 — готовый элемент.
Для изготовления формы нужна мастер-модель — 1/4 или 1/3 часть основания колонны. Четырех (или трех) таких моделей достаточно, чтобы собрать целое изделие. Модель можно или готовую купить в магазине, или специально заказать, например, из вспененного полиуретана.
Более дорогой вариант — спроектировать свою 3D модель и вырезать её на станке с ЧПУ. Этот вариант наиболее целесообразен и экономически оправдан при уже налаженном производстве, когда необходимо в целях удовлетворения потребностей заказчиков оперативно вносить изменения в дизайн изделий.
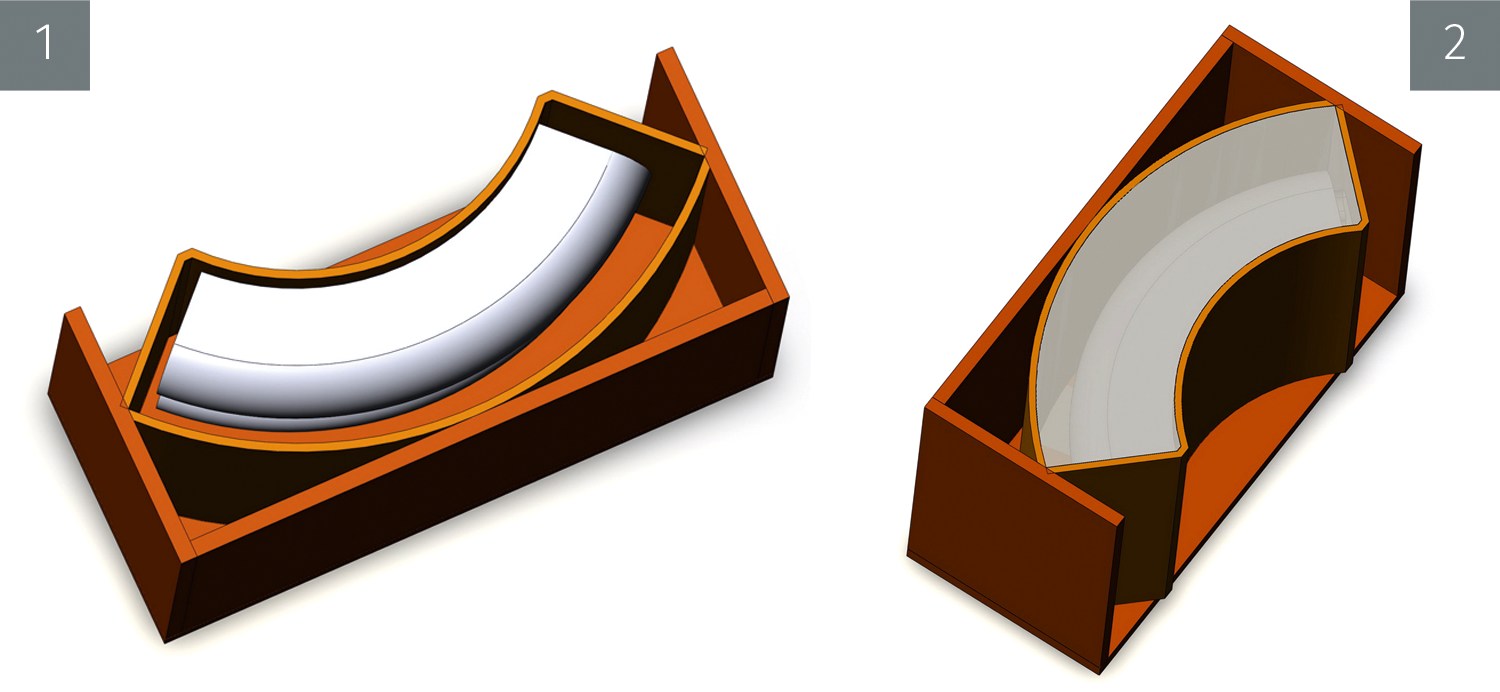
Рисунок 3. Поддерживающий внешний короб с пластиковыми перегородками и мастер-моделью
Из ламинированной ДСП или фанеры необходимо сделать внешний короб (с двумя открытыми поверхностями), в нем, как показано на рисунке 3.1, разместить пластиковые перегородки представляющие собой:
- два согнутых листа, образующих внешнюю и внутреннюю скругленные стенки,
- два ровных листа, образующих боковые косые стенки.
Внутренний согнутый лист пластика закрепляем. В эту конструкцию вставляем мастер-модель, внутренняя полость которой предварительно заполнена скульптурным пластилином. Закрепляем мастер-модель любым способом на внутреннем согнутом листе пластика так, чтобы она не лежала на дне короба, и при заливке силикон равномерно бы затек с трех сторон модели. Например, её можно приклеить к данной перегородке термопистолетом на обычный термоклей. Обратите внимание, что во время работы нужно будет попеременно убирать или наружные стенки короба, или внутренние перегородки, поэтому удобнее сделать всю конструкцию сборно-разборной, например, на саморезах.
Перед заливкой силиконом необходимо обработать внутренние стенки короба, а также поверхность модели разделителем. На производстве мы используем антиадгезионный спрей для силиконов и полиуретанов. Разделитель распыляется на все поверхности так, чтобы он просто смочил их, а не стекал потеками.
Затем согласно инструкции готовим силиконовую смесь. Например, в своем производстве мы применяем двухкомпонентную силиконовую смесь, смешиваемую в пропорции 1:1.
Для получения качественной формы с точным оттиском поверхности мастер-модели, из заливочной силиконовой смеси необходимо удалить пузыри, например, с помощью вакуумной камеры-дегазатора. Такие установки уже производят в России.
При наличии дегазатора: помещаем в него тару с силиконовой смесью сразу после смешения и начинаем вакуумирование. Смесь как бы «вскипает», идет активное пенообразование и, в случае, если тара была изначально заполнена смесью более чем на 2/3, пена может перелиться. Поэтому рекомендую использовать ёмкость для смешения объёмом хотя бы на 1/3 больше, чем необходимо заливочной смеси. Или готовить смесь порциями. В камерах-дегазаторах есть специальное окошко, предназначенное для контроля за процессом вакуумирования. Сильное и быстрое пенообразование можно регулировать с помощью специального вентиля. Примерно через 2–3 минуты весь воздух выходит, пенообразование прекращается, и смесь можно заливать в форму.
Если дегазатора нет: перемешенный силикон сначала наносим на модель кисточкой. Это создаст лицевой слой без пузырей, а потом, не дожидаясь застывания данного слоя, сразу выливаем оставшуюся силиконовую смесь в форму, как и в первом случае. Конечно, в толще силиконовой формы будут пузыри, но в данном случае это не критично.
На рисунке 3.2 показано как выглядит поддерживающий короб с мастер-моделью, залитой силиконовой смесью.
После полимеризации и отверждения силикона (2–5 часов, в зависимости от марки материала) три пластмассовые (внутреннюю скругленную и обе косые) перегородки с мастер-моделью убираем. Получится как на рисунке 4.

Рисунок 4. Поддерживающий внешний короб с внешней скругленной пластиковой перегородкой и отвержденной силиконовой формой
Затем, как показано на рисунке 5, привинчиваем боковую стенку из ДСП к поддерживающему коробу. В результате мы получаем готовую силиконовую форму, лежащую в коробе. И уже в нее вмазывают декоративную смесь, а потом заформовывают слой стекломата. После расформовки готовой четверти, лишний, торчащий по бокам стеклопластик (из стекломата и смолы) срезают угловой шлифовальной машиной (болгаркой) с лепестковым абразивным кругом.
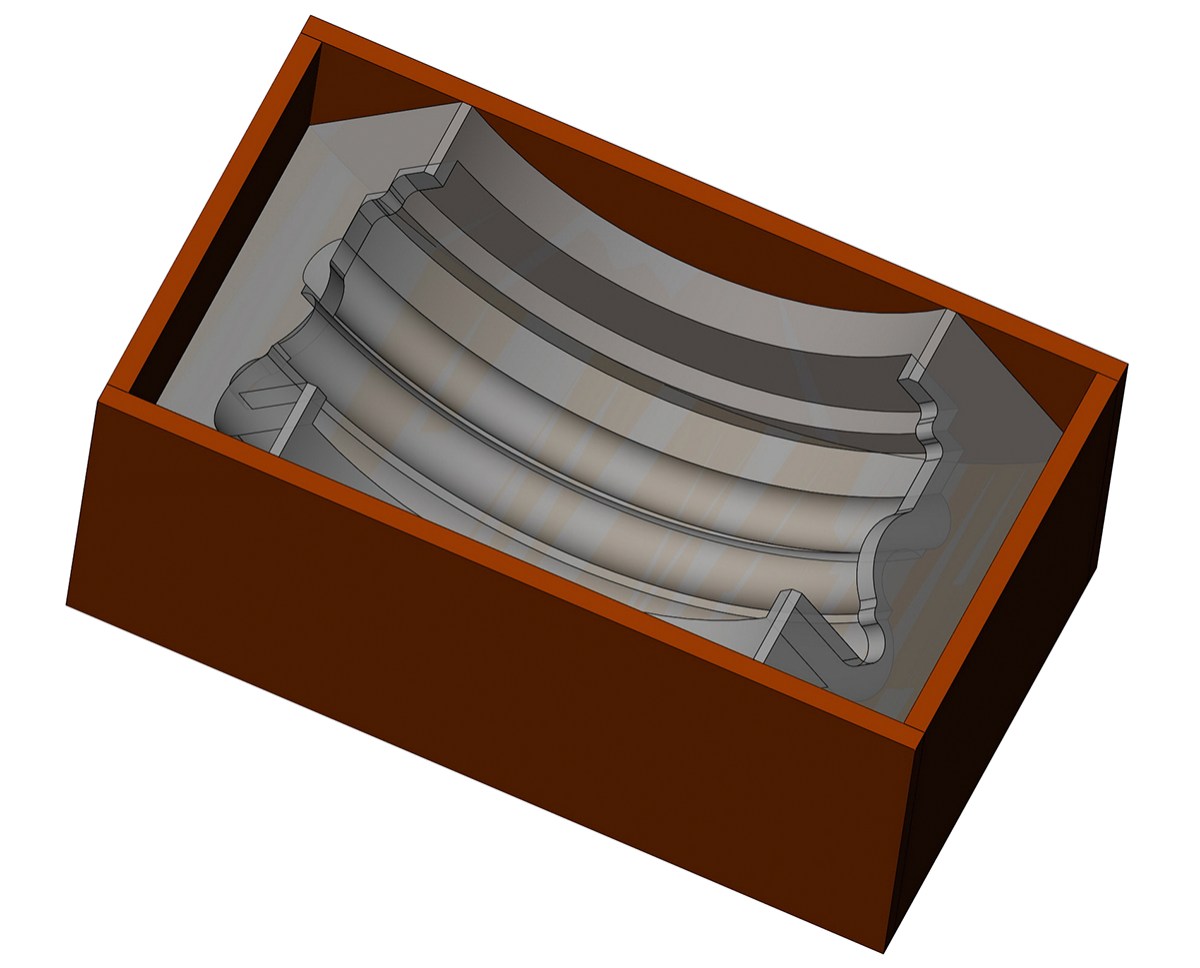
Рисунок 5. Готовая силиконовая форма в поддерживающем коробе
При постоянном контакте с входящей в формовочную декоративную смесь полиэфирной смолой силикон немного разбухает. Для того чтобы это исключить, рекомендую использовать более дорогие марки силиконовых смесей с платиновыми катализаторами. Но для тренировки вполне подойдут и менее дорогие. Разница только в сроке службы.
Соответственно, изготовление силиконовых форм для иных декоративных архитектурных элементов предусматривает аналогичные, описанным выше, стадии. Не забывайте заранее продумывать оптимальные конструкции поддерживающих коробов/перегородок, без которых мягкая форма просто не выдержит веса заливаемой смеси и деформируется, а также необходимость использования структурного пластилина для заполнения внутренних полостей.
Формы изготавливаются эластичными, чтобы и обеспечить лёгкий съем со сложных по геометрии и рельефу поверхностей, и получить на изделии ту самую уникальную, схожую с натуральной текстуру, так как частички наполнителя при вмазывании немного вдавливаются в форму, а затем слегка выступают на лицевом слое элемента.
Технология приготовления формовочных смесей и техника их вмазывания в форму
Для приготовления формовочной смеси нужны следующие материалы:
- смола для первого слоя — атмосферостойкая нетиксотропная предускоренная литьевая изофталевая полиэфирная смола на основе неопентилгликоля;
- смола для второго внутреннего слоя — нетиксотропная предускоренная литьевая ортофталевая полиэфирная смола;
- смола для стекломата — тиксотропная предускоренная конструкционная ортофталевая полиэфирная смола;
- отвердитель — пероксид метилэтилкетона (например Butanox® М50, или аналог);
- коллоидный диоксид кремния: АЭРОСИЛ® марки 200 или более высоких марок: 300, 380;
- кварцевая мука фракции 50 мкм или близкая к ней;
- мраморная крошка (или кварцевый крашенный белый песок) фракции 0,2–0,4 мм или близкой к ней;
- мраморная крошка (или кварцевый крашенный белый песок) фракции 1–1,5 мм или близкой к ней;
- пигмент жидкий белый для полиэфиров RAL 9003 или подобный;
- пигмент жидкий бежевый для полиэфиров RAL 1017, 1018, 1034 или подобный;
- стекломат эмульсионный плотностью 450 г/м²;
- хлористый метилен (метиленхлорид).
Из расчета: на 10 кг литьевой смолы для каменной смеси (как для внешнего слоя, так и для внутреннего) необходимо 50 г АЭРОСИЛ®, с помощью весов производим дозировку нужных компонентов. Затем в отдельную емкость отливаем 2 кг смолы и при постоянном перемешивании (строительной мешалкой) постепенно добавляем АЭРОСИЛ®. После того, как смесь станет вязкой (как кефир) в ёмкость доливаем еще 1 кг смолы и продолжаем вмешивать до конца весь отмеренный АЭРОСИЛ®, тщательно разбивая все комочки. Полученную однородную смесь возвращаем в ёмкость с исходной отмеренной смолой и перемешиваем всё той же мешалкой. Теперь можно при постоянном перемешивании добавить жидкий белый (или бежевый) пигмент в количестве ориентировочно 200–400 г, до полного закрашивая смолы. Полученный компаунд можно хранить достаточно продолжительное время, поэтому можно заранее подготовить нужное для формования всей партии количество смолы, которое затем использовать для приготовления смеси с камнем. Единственное обязательное условие — герметичность тары (наличие плотной крышки), иначе смола загустеет.
Для приготовления смеси с каменным наполнителем необходимо 1,3 кг приготовленного ранее компаунда (смола с «АЭРОСИЛ»® и пигментом) отлить в отдельную тару, куда вмешать 4,8 кг кварцевой муки. Затем отвешиваем 3,5 кг песка фракции 0,2–0,4 мм и 0,4 кг песка фракции 1–1,5 мм. Добавляем при постоянном перемешивании в емкость с компаундом и кварцевой мукой вначале 15 г отвердителя, а затем весь песок. Получаем 10 кг густой каменной смеси. Ее сразу вмазываем резиновыми шпателями в подготовленные силиконовые формы первым слоем. Время жидкого состояния смеси, при температуре в помещении и температуре смеси 20–22°С и пока ее можно наносить, составляет 20–25 минут, оно зависит от марки смолы и количества добавленного отвердителя. Отвердитель можно добавлять от 10 до 30 г на кг смолы. Если будет замечено, что даже при 10 г отвердителя смола слишком быстро отверждается, советую потребовать от поставщика более долгоживущую смолу, со временем гелеобразования не менее 20–25 минут. Если полученная смесь слишком густая (зависит от марки сыпучих материалов), можно долить немного смолы и тщательно перемешать, и впоследствии готовить смесь, как написано выше, но с этой поправкой.
В результате получаем равномерно окрашенное белое, или бежевое изделие. Если необходимо получить разводы: отдельно готовим, как описано выше, белую и бежевую формовочные смеси, а затем сливаем их вместе и делаем пару оборотов мешалкой. Получится неполное смешивание цветов, полосатая смесь. При использовании данной смеси на лицевой поверхности формуемого изделия получаются красивые разводы.
Аналогично описанной технологии готовится формовочная каменная смесь и для внутреннего слоя, только берем более дешевую ортофталевую литьевую смолу. Внутренний слоя наносится, когда первый слой на формах затвердеет настолько, что будет устойчив к механическим повреждениям (например, проколов шпателем).
Не дожидаясь отверждения внутреннего слоя, следует смешать 1 кг конструкционной смолы с 15 г отвердителя. Данной смолой необходимо с помощью большой кисти пропитать уложенные на внутренний слой искусственного камня предварительно раскроенные куски стекломата. Через 2–3 минуты пропитанный стекломат становится пластичным. Этой же кистью выбиваем пузыри воздуха из-под стекломата, чтобы он надежно соединился с каменной массой. Пропитанным стекломатом необходимо накрыть весь внутренний каменный слой, при необходимости, смешивая с отвердителем дополнительные порции связующего.
После того, как данная сэндвич-структура затвердеет (в зависимости от марки используемых смол: через 2–3 часа), расформовываем изделие: вначале извлекаем из поддерживающего короба изделие с силиконовой формой, затем снимаем с него силикон, и возвращаем форму в короб. Изделие кладем ровной стороной на ровную поверхность, чтобы его не перекосило. И выдерживаем его в таком состоянии при комнатной температуре до полного отверждения. Это примерно 4–6 часов.
Обрезаем на изделии торчащие края стеклопластика, при необходимости — подравниваем стыковые поверхности. Это лучше всего делать угловой шлифовальной машиной с алмазным отрезным и зачистным (чашка) дисками, можно резать специальным корундовым кругом для камня. Так как содержащаяся в составе искусственного камня кварцевая мука придает ему особую твердость, обычный круг не может обработать этот материал.
Обратите внимание на лицевую поверхность изделий: если она блестит, и при формовании было замечено, что формовочная каменная смесь не достаточно густая, для следующего изделия можно попробовать добавить меньше смолы, пропорционально уменьшив при этом количество отвердителя, «Аэросила»® и пигмента, но оставив прежнее количество сыпучих материалов.
Так как смесь содержит немного крупной фракции песка 1–1,5 мм, лицевая поверхность будет с выщерблинами (под старину). Если необходимости в данном эффекте нет — просто замените крупный песок таким же количеством мелкого.
Если лицевая поверхность изделий блестит, можно немного отшлифовать её скотч-брайтом (нетканым абразивным материалом), но гораздо легче обработать поверхность специальной смесью: к 4 кг хлористого метилена добавить 1 кг жидкого индустриального масла (например, «веретенку»). Данную тщательно перемешенную смесь наносят на лицевую сторону изделия с помощью ветоши и через 2–3 минуты удаляют остатки смеси сухой тряпкой. Метиленхлорид разъедает на поверхности пленку смолы и делает поверхность матовой, но без масла — будут видны разводы. Масло в таком количестве не дает блеск, оно выравнивает белесые разводы от метиленхлорида и делает поверхность равномерно матовой.
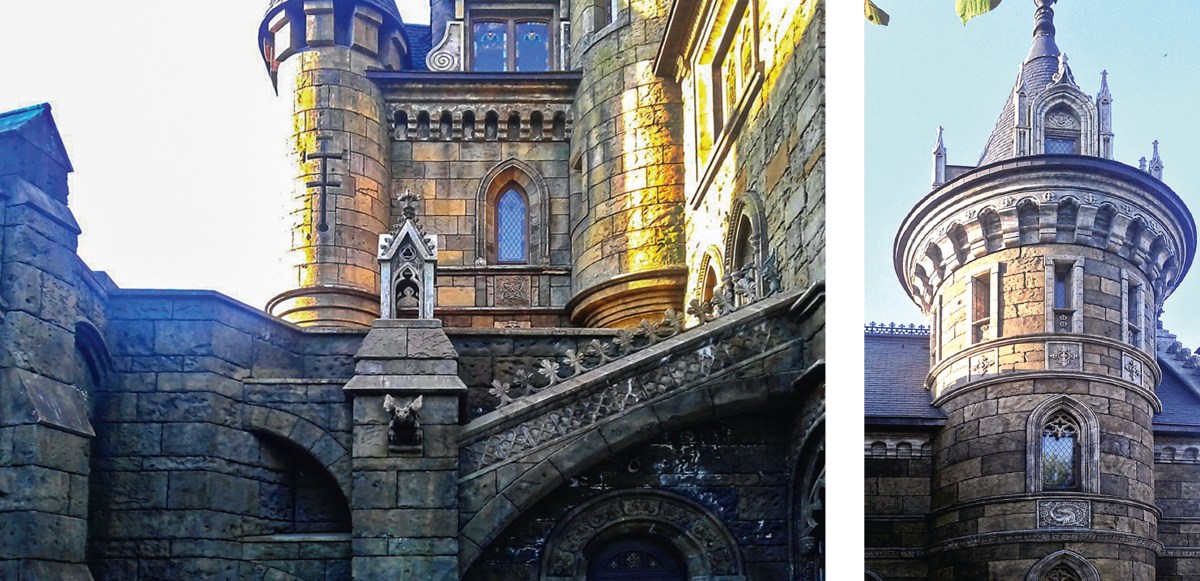
Облицовка замка Гарибальди (Самарская обл.) выполнена из композита по технологии вмазывания формовочной каменной смеси в форму
В статье описана базовая технология. На практике в зависимости от требуемых результатов, а также производственных условий могут варьироваться количества исходных веществ. Но для первоначального расчета требуемого сырья и материалов можно воспользоваться приведенными соотношениями. В дальнейшем по мере отработки технологии данные подлежат уточнению, исходя из реального расхода.