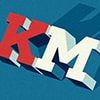
Инновационные технологии ремонта и защиты насосов c применением полимерных композитных материалов
рубрика: технологии
Ремонтные композитные системы позволяют восполнять потерю металла и воссоздавать первоначальный профиль деталей насосов, защищать их от дальнейших повреждений и при этом быстро возвращать оборудование в эксплуатацию. Поэтому все больше предприятий выбирают полимерные технологии холодного отверждения для ремонта и защиты оборудования.
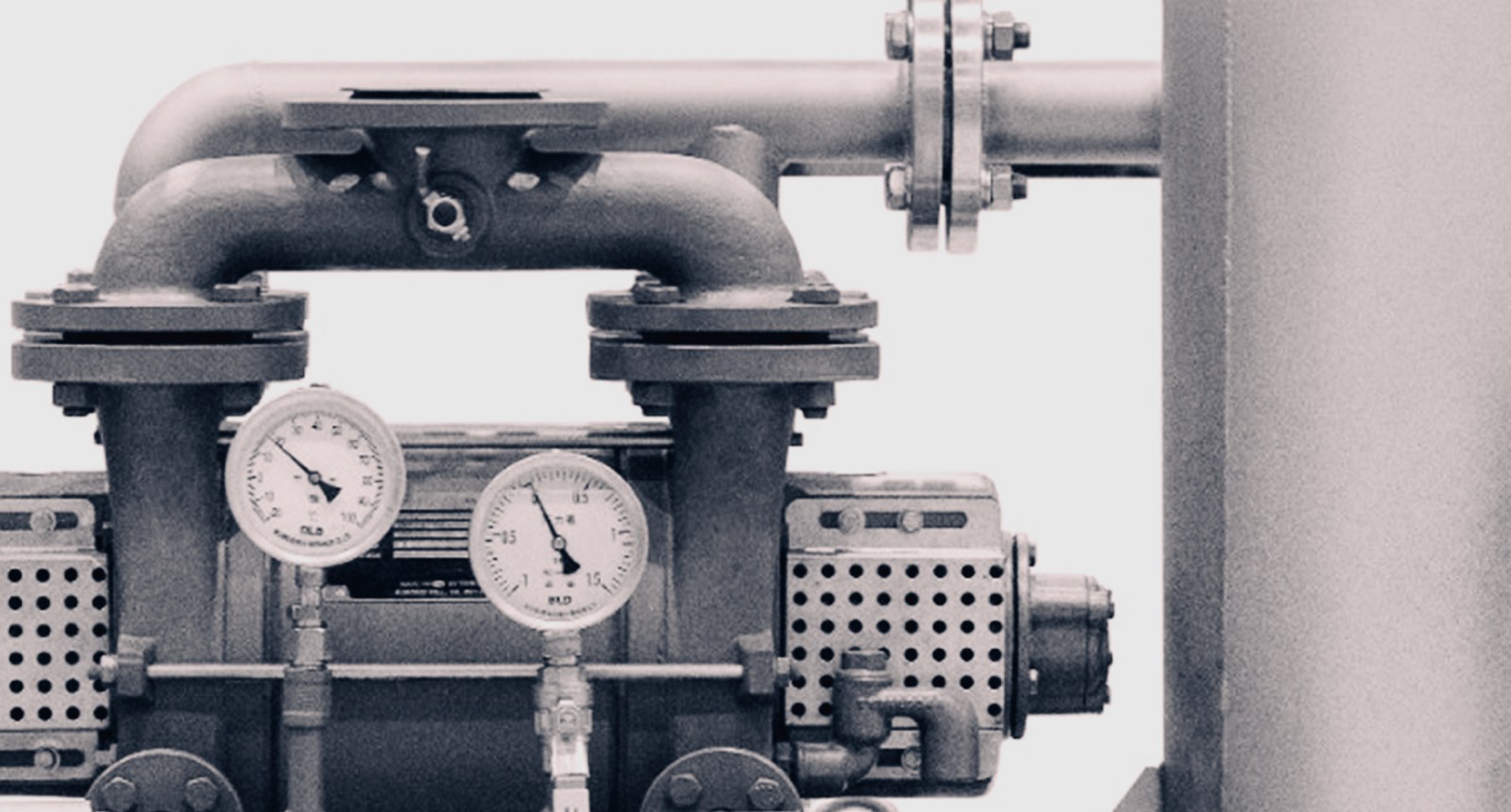
В процессе перекачивания жидкостей и твердых фракций насосное оборудование постоянно находится под воздействием механических нагрузок. В силу самой природы насосных систем конструкторы, проектировщики, подрядчики и эксплуатационники постоянно сталкиваются со следующими серьезными проблемами:
- эрозия каналов, по которым перемещаются жидкости;
- возникновение коррозии и эрозии на основных компонентах насоса,
- таких как лопасти, корпусы и валы;
- кавитационный износ деталей;
- изменение критических зазоров между деталями
Эти проблемы постепенно приводят к падению напора, уменьшению скорости потока, снижению КПД и неизбежному росту операционных расходов.
Изначально повреждение приводит к образованию на поверхностях неровностей и язвин, которые увеличивают трение и приводят к падению эффективности системы, а также к повышенным эксплуатационным затратам. Однако проблемы коррозии-эрозии, если их вовремя не устранить, могут поставить под угрозу целостность компонента и, в конечном счете, привести к полному отказу оборудования.
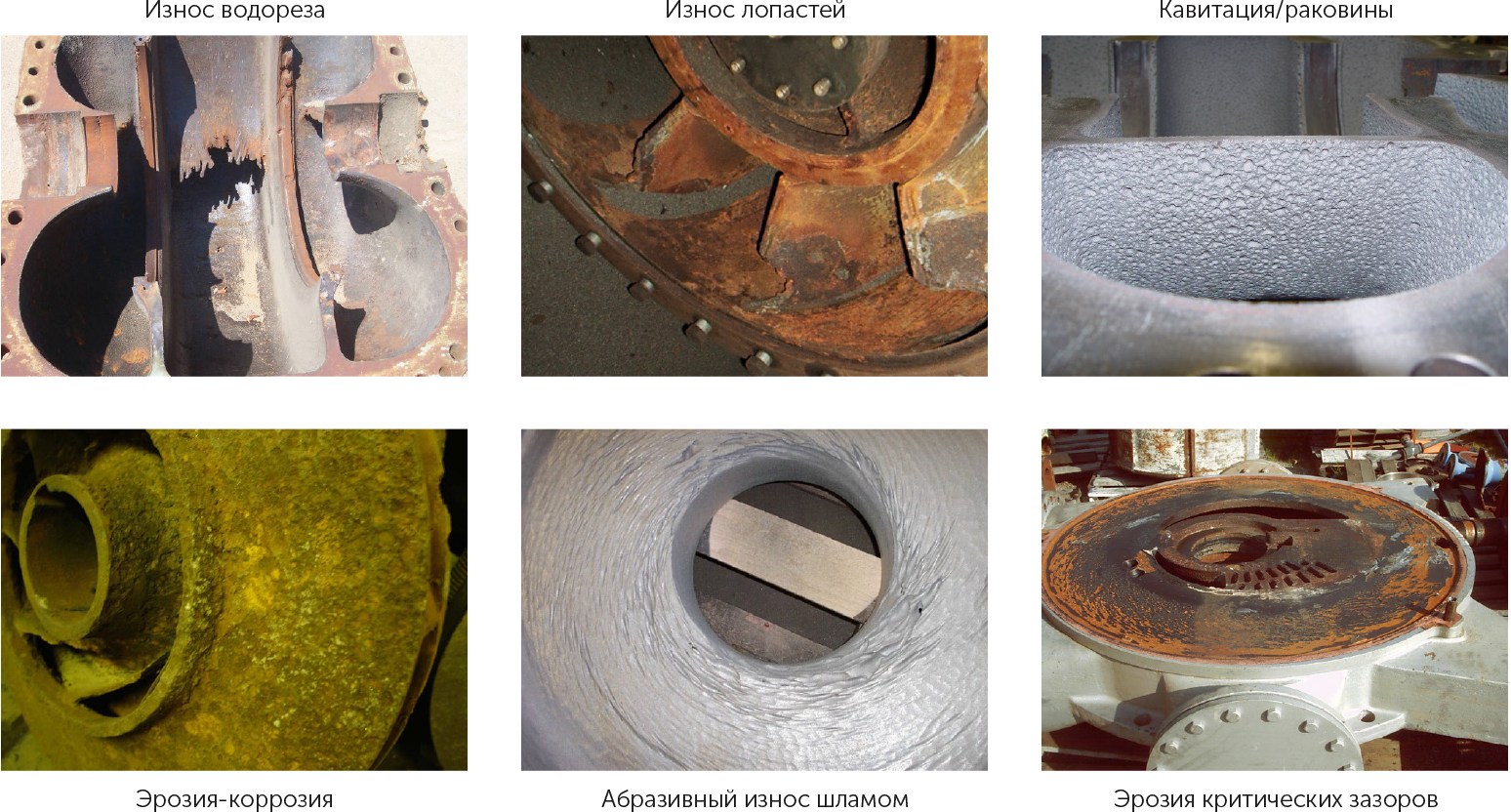
Очевидным решением обычно является замена изношенного оборудования, что связано с высокими расходами, а временны̀е затраты могут составлять недели или даже месяцы. С другой стороны применение огневых работ, включая сварку и наплавление покрытий, может привести к термическому напряжению оборудования и создать проблемы с электрохимической коррозией. Но что наиболее важно, ни один из способов не решает основную проблему.
Ремонтные композитные системы позволяют восполнять потерю металла и воссоздавать первоначальный профиль деталей насосов, защищать их от дальнейших повреждений и при этом быстро возвращать оборудование в эксплуатацию. Поэтому все больше предприятий выбирают полимерные технологии холодного отверждения для ремонта и защиты оборудования.
Продление срока службы и сокращение расходов
Эпоксидные системы представляют собой простой и экономически выгодный способ восстановления исходного профиля и защиты компонентов от повреждения в будущем, а также гарантируют возврат оборудования в эксплуатацию в течение нескольких дней. После нанесения покрытия насос будет иметь улучшенную защиту от эрозии/коррозии, повышенную производительность и увеличенный срок службы.
Ремонт
Пастообразные эпоксидные материалы, не содержащие растворителей, обеспечивают превосходную защиту от коррозии, позволяют воссоздать точные контуры и могут наноситься тонким или толстым слоем за одну операцию. Они образуют прочную адгезионную связь с любыми металлическими поверхностями, а также не подвержены усадке, расширению и не деформируются в процессе отверждения — значительное преимущество по сравнению с композитными материалами, содержащими летучие органические соединения.
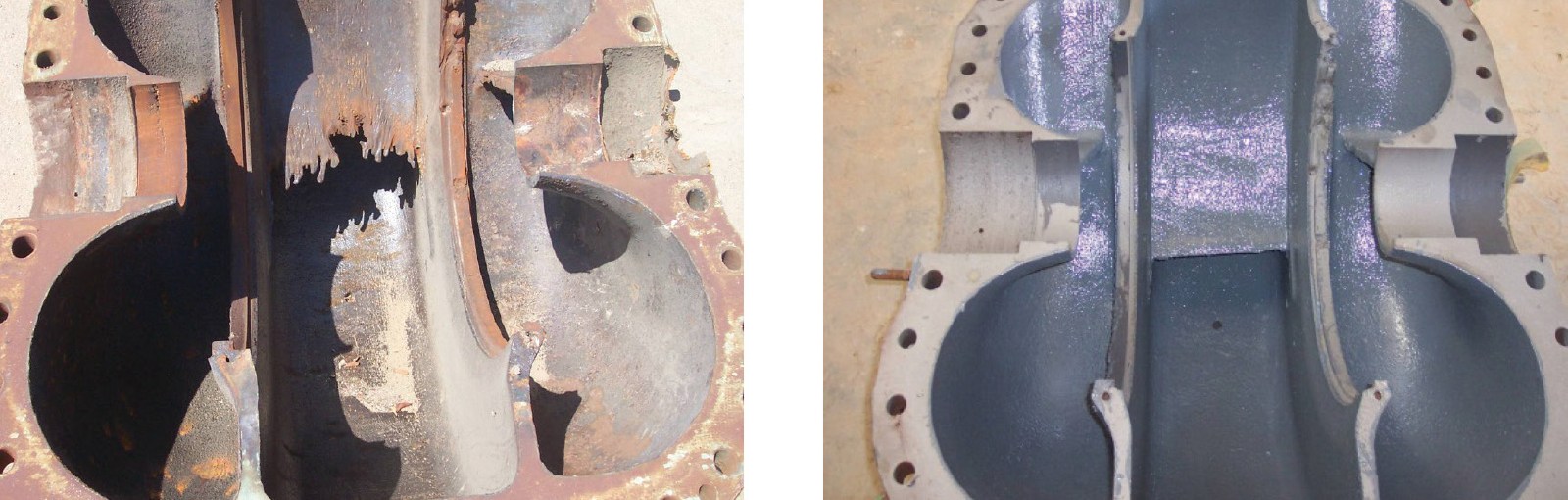
Восстановление геометрии водореза — до и после ремонта
Во множестве случаев, когда металлические детали и корпус подвержены значительной эрозии-коррозии, пастообразные композиты с керамическими наполнителями широко используются для восстановления точных контуров и размеров поверхностей. Помимо обеспечения превосходной защиты от коррозии этот материал значительно замедляет скорость эрозийных процессов вследствие высокого процента керамонаполнителей в его составе.
Для тех областей, которые подверглись сильному износу с существенной потерей металла, вплоть до образования сквозных отверстий и трещин в результате ударных воздействий, решением является создание каркасной основы. Это позволит восстановить механическую прочность поврежденной части оборудования. Для создания каркасной основы (армирования) болтовые крепления соединяются со стальными пластинами или сеткой. Следующим шагом является заполнение каркаса композитным материалом до восстановления исходного профиля детали.
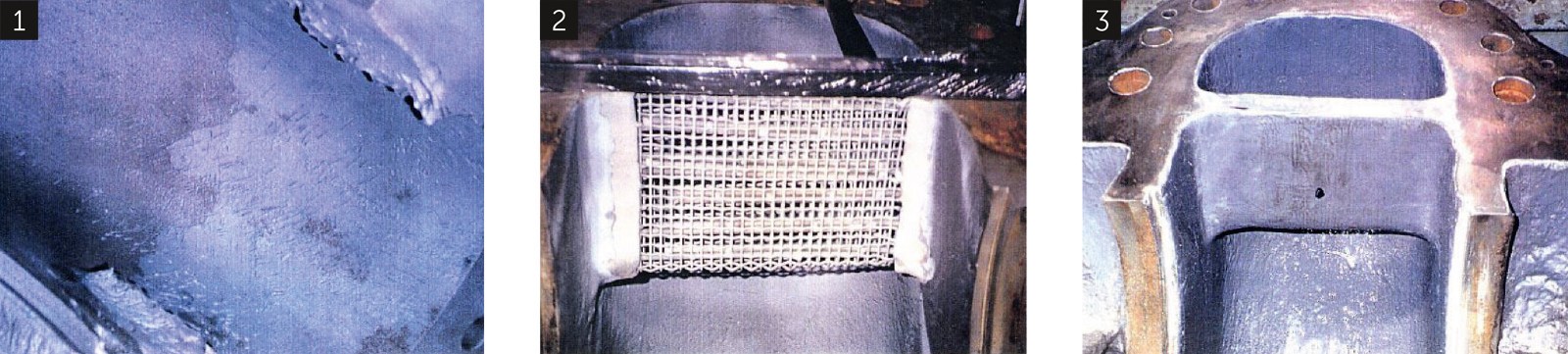
1 — критическое повреждение стенки корпуса насоса; 2, 3 — восстановление исходной геометрии с использованием армирования и композитного материала
Долговременная защита
Снижение производительности или КПД оборудования напрямую связано с физическими и механическими дефектами, влияющими на его функционирование. Единственным способом значительного снижения воздействия эрозии и коррозии является изоляция металлических поверхностей от перекачиваемых жидкостей. Эта задача решается нанесением защитного покрытия на внутренние компоненты насоса.
При работе с текучими средами в различных операционных условиях (химически активные материалы, повышенные температуры, среды с высоким содержанием твердых фракций) решением выступают защитные системы, предназначенные для эксплуатации в условиях постоянного погружения при температурах до +160°C и устойчивые к широкому спектру химически агрессивных веществ.
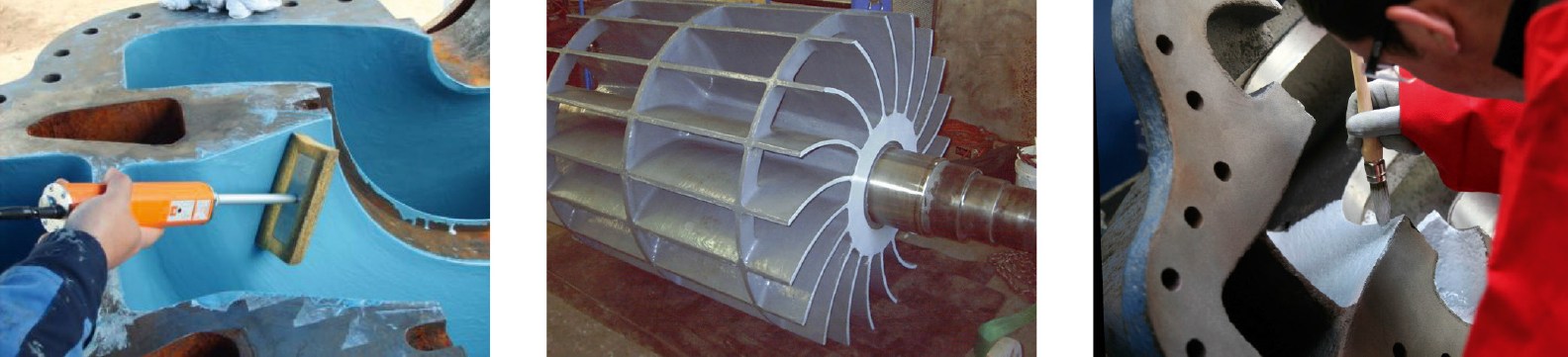
Нанесение защитного эпоксидного покрытия
Аналогично пастообразным ремонтным материалам защитные покрытия предназначены для холодного нанесения и не содержат растворителей. Это позволяет избежать усадки и снижает риски для здоровья и безопасности, характерные для альтернативных методов ремонта и защиты.
Решения для повышения КПД
Обратившись к основным понятиям о жидкостях и влиянию шероховатости поверхности на поток, определено что при низких скоростях потока жидкость перемещается слоями, параллельными стенкам гидравлического канала, при этом перемешивания слоев не происходит. Такой режим течения называется ламинарным. Когда скорость жидкости достигает определенной величины, течение становится хаотичным и появляются неустойчивые завихрения. Такой режим течения, коренным образом отличающийся от ламинарного, называется турбулентным.
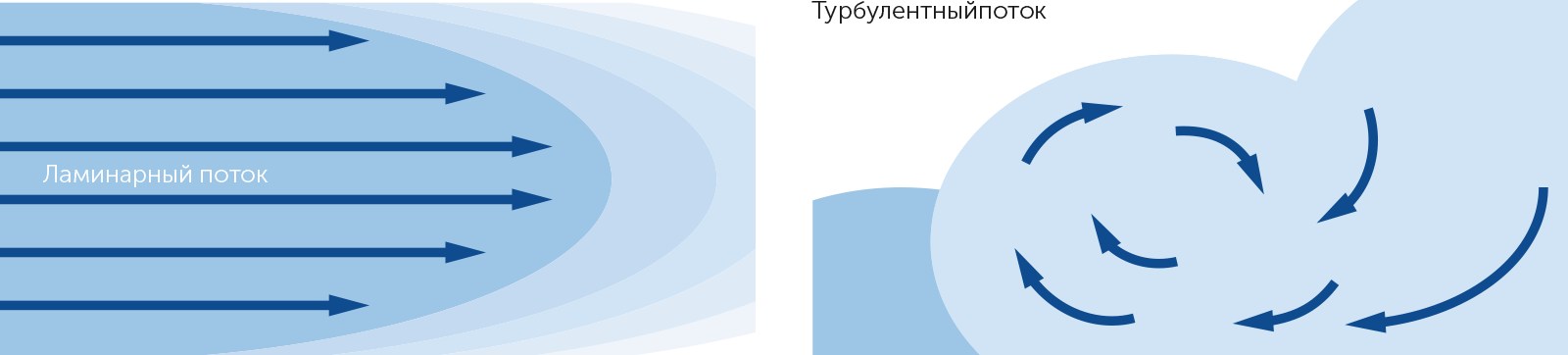
В классической теории гидродинамики считается, что молекулы жидкости, находящиеся на поверхности стенок канала, неподвижны. Из-за торможения слоев жидкости, соприкасающихся с неподвижным пристеночным слоем, в канале устанавливается градиент скорости потока от стенок к центру. По мере удаления от стенки канала эффект торможения ослабевает. Действующая на пограничный слой сила вязкого трения, известная также как внутреннее трение или сопротивление трения пограничного слоя, становится причиной потери напора в каналах с ламинарным течением жидкости. Пограничным называется слой жидкости, непосредственно прилегающий к неподвижной поверхности, скорость перемещения которого определяется силой вязкого трения.
Чем выше шероховатость поверхности стенки, тем толще пограничный слой. При определенной скорости потока, называемой критической, этот слой становится нестабильным, и ламинарный поток превращается в турбулентный. В таком режиме отдельные объемы жидкости перемещаются независимо друг от друга, образуя завихрения и поперечные потоки. Турбулентность приводит к дополнительным потерям энергии, помимо потерь, связанных с сопротивлением трения в пограничном слое.
В случае относительно гладких поверхностей толщина пограничного слоя может быть достаточно большой, чтобы скрыть выступы шероховатости, в этом случае поверхность считается гидравлически гладкой.
Если оборудование изготовлено из чугуна, шероховатость поверхности можно увидеть даже невооруженным глазом, но с помощью сканирующего электронного микроскопа это видно более четко. Турбулентное течение может приводить к ударным воздействиям, когда поток жидкости бомбардирует поверхность оборудования, ускоряя тем самым эрозию металла.
Еще одним негативным следствием турбулентности является кавитация — процесс образования и схлопывания пузырьков газа в жидкой среде. Возникающие при этом ударные волны обладают столь разрушительной силой, что буквально разъедают металл, что приводит к образованию глубоких язв на поверхности.
Эти повреждения усугубляются коррозией и абразивным воздействием, а в результате КПД снижается еще больше.
Потери энергии, обусловленные силой вязкого трения и шероховатостью поверхности и усугубленные эрозией-коррозией, можно уменьшить, если на внутренние поверхности оборудования, работающего с жидкими средами, нанести защитное покрытие.
Использование защитного покрытия Belzona 1341 (Supermetalglide), разработанного для создания идеально гладких поверхностей. Степень гладкости и толщина слоя являются критическими факторами, определяющими высокую эффективность покрытия, так как они снижают сопротивление трения, не меняя характеристики потока.
Не меньшее значение имеет уникальный химический состав покрытия Belzona 1341. В виду гидрофобных свойств покрытия вода просто соскальзывает с его поверхности, а сочетание смазывающих добавок и износостойких наполнителей в составе покрытия сводит к минимуму абразивный износ.
Повышение производительности по результатам независимых испытаний, проведенных в Британской национальной инженерно-технической лаборатории (N.E.L.): Испытания насоса проводили с использованием стандартной системы с замкнутым контуром, при этом во всем рабочем диапазоне насоса (10–125%) определяли значения трех показателей — расхода, напора и мощности, которые использовали для построения точной кривой производительности насоса. В качестве средств измерений использовали приборы, откалиброванные с помощью рабочих эталонов, прослеживаемых до государственных первичных эталонов.
Для испытаний покрытия Belzona 1341 был выбран одноступенчатый центробежный насос торцевого всасывания с 10-дюймовыми всасывающим и нагнетательным патрубками.
Было установлено, что насос без покрытия, работающий со скоростью 1300 об/мин, способен перекачивать 875 м3 в час при напоре 26,5 м с максимальным общим КПД, достигающим 83,5% (общий КПД определяется как соотношение гидравлической мощности насоса к механической мощности на валу).
Увеличение срока службы 10 вакуумных насосов в 6 раз
Крупная мануфактурная компания искала решение для борьбы с интенсивным износом и значительным снижением производительности 10-и жидкостно-кольцевых вакуумных насосов производства Siemens, находящихся в эксплуатации приблизительно 12 месяцев.
После разборки одного из насосов было обнаружено, что интенсивная работа оборудования по перекачке технологических сред с большим содержанием твердых примесей привела к значительному эрозионному и коррозионному повреждению компонентов насоса.
Решение Belzona
Для восстановления ротора было решено использовать материалы Belzona 1311 (Ceramic R-Metal) и Belzona 1321 (Ceramic S-Metal), чтобы устранить воздействие коррозии и значительно снизить степень эрозии. Для восстановления распределительных пластин ротора использовали материал Belzona 1111 (Super Metal) с последующей механической обработкой для восстановления критических допусков.
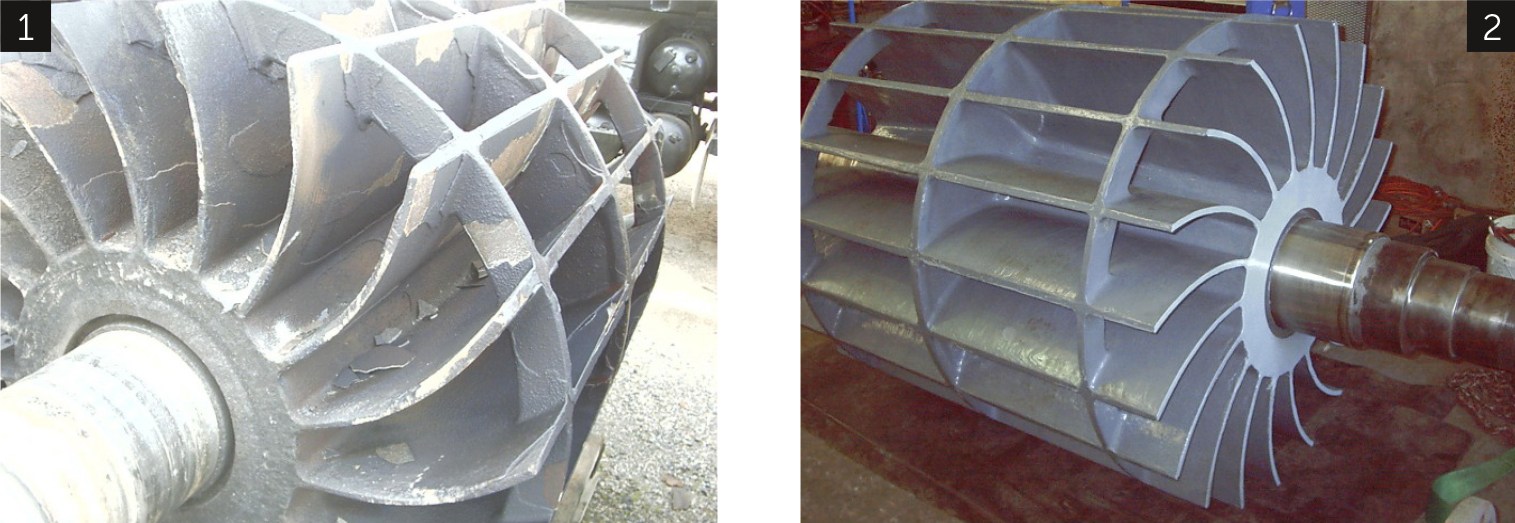
1 — Ротор до нанесения систем Belzona; 2 — После нанесения систем Belzona 1311 и Belzona 1321
Внутренняя проверка насоса через 13 месяцев эксплуатации доказала, что покрытия Belzona находятся в превосходном состоянии и обеспечивают полную защиту насоса. Следует заметить, что изменений в технологический процесс не вносилось, и насос без защитного покрытия был практически уничтожен меньше, чем за 12 месяцев эксплуатации. Все 10 насосов станции были отремонтированы с использованием указанных технологий с увеличением среднего срока службы до 6 лет без необходимости капитального ремонта. Благодаря решению Belzona оператор станции смог полностью избежать замены насосов.
Сохранение прироста производительности центробежного насоса после 3,5 лет эксплуатации
В данном примере компания, предоставляющая услуги в сфере водоснабжения, столкнулась с резким 11%-ым снижением производительности 2-х насосов производства компании KSB по причине сильного износа под воздействием коррозии и кавитации. В дополнение к эрозии, вызванной кавитацией, общая и контактная коррозия привели к протечке в местах установки компенсационных колец, что и привело к значительной потере эффективности.
Было принято решение восстановить посадочные места компенсационных колец с помощью технологии формования с использованием самих колец в качестве формообразователей. Сначала насос из литейного чугуна подвергли абразивоструйной обработке для достижения требуемого стандарта подготовки поверхности, а кольца обработали антиадгезионным составом, чтобы впоследствии их можно было снять. Затем на подготовленную область посадочных мест постепенно нанесли материал Belzona 1111 (Super Metal). Непосредственно после этого рабочее колесо насоса с предустановленными обработанными компенсационными кольцами было установлено на место, а все излишки материала Belzona, выступившие из-под формовочных поверхностей, были удалены. Правильная высота и выравнивание сформированной части были достигнуты благодаря правильной установке и позиционированию подшипников.
Идентичную методику использовали для восстановления второй половины корпуса насоса.
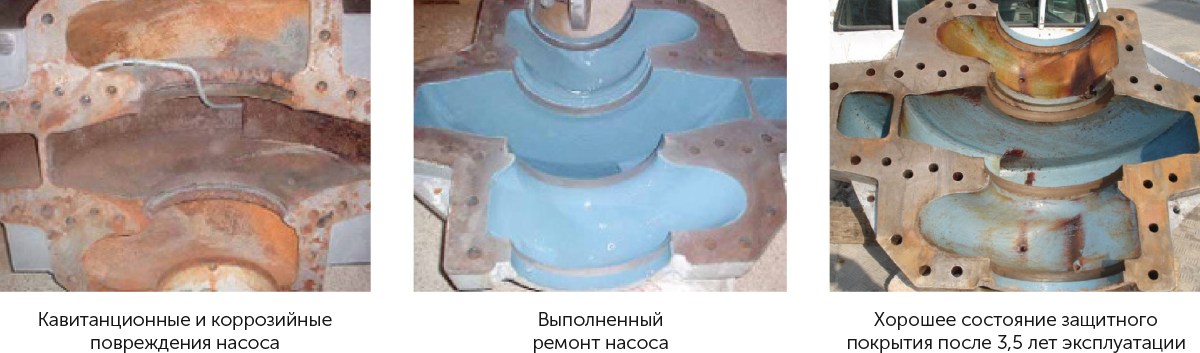
В качестве финального защитного покрытия был использован материал Belzona 1341 (Supermetalglide) для предотвращения коррозии и замедления эрозийных процессов. В результате по завершении ремонта показатель прироста производительности составил 12%. При повторной инспекции, после трех с половиной лет эксплуатации оборудования зафиксировано сохранение прироста производительности на 9%.
Полимерные материалы находят широкое применение в области ремонта оборудования и механизмов, при этом сокращая время простоя, устраняя потребность в дорогостоящей замене поврежденного, изношенного оборудования и его частей. Ремонт металлических деталей с применением «технологий холодного отверждения» позволяет избежать применения огневых работ, следовательно, и потенциальных проблем, связанных с термическим напряжением металла и электрохимической коррозией.
Композитные технологии так же можно использовать для нового оборудования с целью повышения его КПД и снижения потребления электроэнергии. Уникальные характеристики этих материалов обеспечивают повышение КПД на 3–8% для новых насосов и до 20% для эксплуатируемого оборудования.
Статья была опубликована в номере 1 (82) 2019