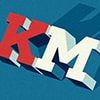
Нет автоклава, нет печи, нет проблем!
рубрика: технологии
Производство изделий без использования автоклава (БИA) появилось в качестве способа производства структур следующего поколения, в частности, для авиакосмической промышленности. Что же заставляет производителей внедрять БИA, особенно если учесть, что они уже инвестировали большой капитал в системы с использованием автоклава? Причина кроется в двух основных факторах — деньгах и размерах деталей. Обычные системы отверждения с использованием автоклава являются дорогостоящими, дорогими в обслуживании и имеют ограниченные размеры.
Производители, работающие в области авиакосмической промышленности, а также в других отраслях, все больше используют технологию БИA с отверждением деталей только в печи. Производство изделий без использования автоклава является менее капиталоёмким и менее дорогостоящим, особенно при увеличении размеров и количества деталей. Некоторые из последних достижений привели к дальнейшему совершенствованию технологии, позволяя проводить отверждение без использования автоклава и без использования печи. Из разрабатываемых технологий можно назвать общее нагревание/охлаждение с использованием жидкости и индукционное нагревание. Эти технологии обладают такими же преимуществами, как и технология БИA, а также дополнительными, такими как: меньшее количество этапов, меньшее количество материала и более короткий производственный цикл.
Преимущества технологии «без использования автоклава» (БИA)
Технология БИA наиболее широко используется производителями, работающими в области авиакосмической промышленности. Однако, убедившись в том, что эта технология не обладает недостатками технологии с применением автоклава, производители начали внедрять методы БИA и в других областях промышленности, начиная от производства возобновляемых источников энергии до автомобильной промышленности и производства бытовой электроники. Таким образом они надеются улучшить свои продукты, повысить производительность, сократить время изготовления изделия, а также уменьшить капитальные затраты, эксплуатационные расходы и затраты на рабочую силу.
Автоклавы являются капиталоёмким оборудованием. Цена одного автоклава часто выражается шестизначным числом. Эта стоимость может быть значительно более высокой, особенно в авиакосмической промышленности, в которой крупногабаритные детали требуют использования больших автоклавов и ценников с большими цифрами. «В 2007 г. в NASA решили подсчитать, во что обойдется приобретение автоклава, имеющего диаметр 40 футов, и оказалось, что стоимость такого приобретения составит 100 миллионов долларов, включая установку», — говорит Джон Рассел (John Russell), технический директор Отдела производства и промышленных технологий Научно-исследовательской лаборатории военно-воздушных сил. «Для деталей, изготавливающихся в небольшом количестве, это неоправданно высокая стоимость».
Дейл Брозиус (Dale Brosius) — президент компании Quickstep Composites в г. Дейтон, штат Огайо, говорит, что для автоклава характерно большое время оборота и производственного цикла, вследствие чего, дорогостоящее оборудование простаивает в течение длительного времени, что ведет к дальнейшему увеличению расходов производителей. Это относится как к новым деталям, так и к ремонту деталей. «Конфигурация аппаратов для сварки и нагревателей является более экономичной, благодаря фокусированному и локализованному нагреванию ремонтируемой детали», — говорит Эрик Кастерлайн (Eric Casterline), президент компании HEATCON Composites Systems в Сиэтле. «При использовании технологии БИA не требуется нагревания всей детали (автомобиль, самолёт и т.д.) при проведении ремонтных работ».
Кроме того, технология БИA позволяет ускорить производство деталей. «Длительное успешное применение полимеров, армированных углеволокном, потребует использования методов, позволяющих повысить скорость производства, что невозможно при использовании автоклава», — говорит Дейл Брозиус. «Например, производительность при производстве истребителя следующего-поколения должна увеличиться до одного самолета в день, что намного превышает производительность за всю историю их производства». Он добавил также, что в дальнейшем самолеты Boeing 737 необходимо будет выпускать со скоростью 45 самолетов в месяц, что намного больше скорости производства самолетов Boeing 787, которая составляет 15 самолетов в месяц. «Для производства более легких самолетов, в большей степени топливосберегающих, и самолетов следующего поколения, необходимо будет использовать намного большее количество деталей, изготовленных из композитных материалов» — говорит Дейл Брозиус. «И это отражается на всех уровнях цепочек поставок изделий, изготовленных из композитных материалов».
«Для промышленности время отверждения является самым узким местом» — говорит Майкл Раушер (Michael Rauscher), главный технический директор компании NONA Composites в г. Дейтон, штат Огайо. В названии этой компании фигурирует аббревиатура, обозначающая название технологии, с применением которой производятся предлагаемые этой компанией изделия (no oven, no autoclave — без печи, без автоклава). «Для повышения производительности и снижения стоимости мы должны изменить время отверждения» — говорит он. «Это такая важная проблема для производителей, что в поисках новых процессов, типа БИA, компании посылают сотрудников даже на торговые выставки» — говорит Бенжамин Людтке (Benjamin Luedtke), технический директор компании Quickstep Composites.
Это не означает, что технология БИA является единственно верным решением проблемы, связанной с дальнейшим внедрением композитных материалов. На каждом сегмента рынка требуется сертификация новых продуктов и материалов, и эта сертификация означает затраты капитала и времени. По шкале строгости испытаний авиакосмическая область стоит на первом месте, так как в ней для одобрения нового материала и/или процесса требуются годы, затем идет автомобильная промышленность, производство возобновляемых источников энергии и другие расширяющиеся рынки, такие как рынок бытовой электроники и медицинского оборудования. «Если объёмы невелики, то сертификация нового процесса может не требоваться» — говорит Дейл Брозиус.
БИA — Развитие и области применения
Французская компания RocTool американская штаб-квартира которой располагается в г. Шарлотт, штат Северная Каролина, находилась в передних рядах разработчиков инновационных систем типа БИA. При изготовлении деталей для авиакосмической промышленности, а также деталей салона автомобиля, таких как текстурированные детали отделки салона новой модели автомобиля Mini Cooper, эта компания использует индукционное нагревание. Быстро растущей частью бизнеса этой компании является производство бытовой электроники, в котором компания RocTool получила отраслевую награду, будучи частью компании Motorola Mobility, за изготовление из композитного материала задней крышки нового смартфона Motorola Moto X.
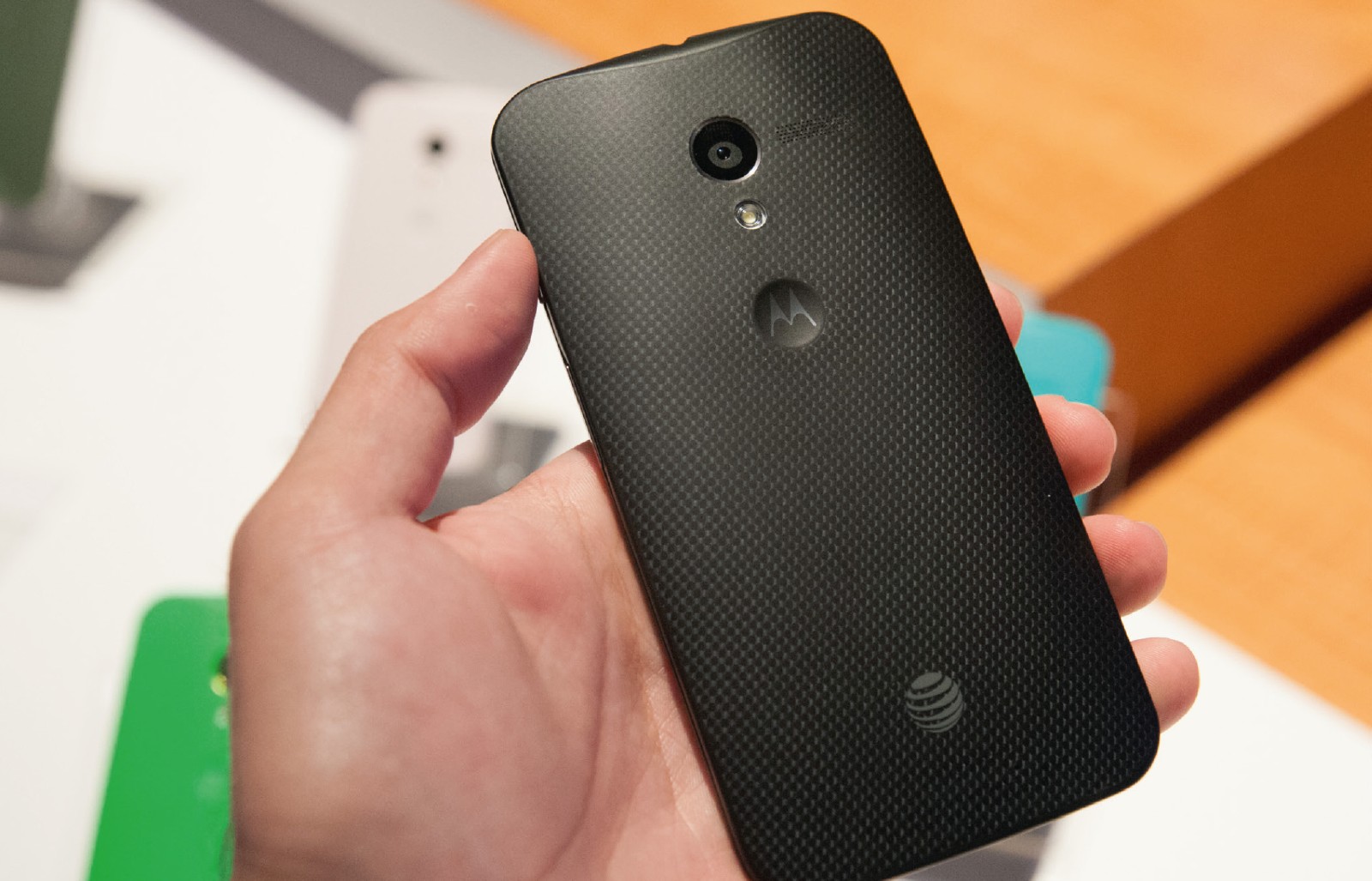
Для изготовления задней крышки нового смартфона Motorola Moto X из композитного материала компания RocTool использует процесс общего нагревания/охлаждения. Производственная мощность составляет 50 000 единиц в день и позволяет проводить различные виды финишная обработки, такие как окрашивание с получением глянцевой и матовой поверхности, а также поверхности мягкой на ощупь.
В 2000 г. эта компания начала изменять методы БИA с использованием процесса резистивного нагревания, при котором электричество проходит через волокно и нагревает смолу. Затем компания RocTool разработала свою систему Cage System® с использованием катушек индуктивности, расположенных вокруг литейной формы и служащих для нагревания всей ее поверхности. «Это был интересный процесс, однако мы были ограничены в материалах, которые могли использовать» — говорит Мэтью Буланжер (Mathieu Boulanger), директор по развитию бизнеса компании RocTool.
Четыре года назад эта компания выпустила систему 3iTech®, в которой индукционные катушки встроены в каналы, благодаря чему обеспечивается очень быстрое нагревание инструмента.
Компания BUFA Composite Systems и их дистрибьютор в России — ГК «ЕТС» в 2014 г. начали первые коммерческие поставки токопроводящей пасты, содержащей углеродное волокно, для изготовления подогреваемой остнастки.
В июне компания RocTool анонсировала выпуск системы формования с использованием светоиндукционной обработки (LIT). Эта система состоит из металлической негативной формы для вакуумного формования и силиконовой позитивной формы. Для армирования однонаправленным или плетеным волокном его помещают в негативную форму для вакуумного формования, которую накрывают позитивной формой, а затем в литейную форму подают сжатый воздух, пока давление не достигнет значения 420 psi. Система LIT нагревается до температуры 280°C за 45–90 секунд в зависимости от типа материала и детали. Затем с помощью воды осуществляется охлаждение литейной формы и детали, которое занимает 1–2 минуты. «Система LIT не требует предварительного нагревания, обеспечивает хорошую пропитку поверхности смолой, не требует инжекции смолы, позволяет изготавливать тонкостенные изделия и обеспечивает хороший контроль температуры» — говорит Мэтью Буланжер.
Он обращает внимание на то, что для каждой из указанных разработок компания RocTool даже не рассматривала возможность использования автоклавов или печей. «Мы нацелены на уменьшение количества этапов, и с этих позиций технология БИA является лучшим выбором» — говорит Мэтью Буланжер. Компания RocTool продолжает улучшать свои процессы, демонстрируя возможность применения различных температур (необходимых для изготовления различных деталей), и увеличивать производительность. «Если при каком-либо изменении технологии время производственного цикла составляет более 30 минут, то мы даже не рассматриваем возможность его использования» — говорит Мэтью Буланжер. «При большинстве наших технологий время производственного цикла составляет от двух до восьми минут. И самое важное заключается в том, что если в начале нашей деятельности нашу компанию считали экзотической, то в настоящее время людям удобно работать с нами».
Между тем, компания Quickstep Composites для отверждения композитных материалов использует технологию общего нагревания/охлаждения, которая, главным образом, применяется в авиакосмической промышленности. При использующемся в этой компании процессе с применением теплопередающей среды (HTF) ламинат помещают в жёсткую или полужёсткую форму, плавающую в теплопередающей среде. Литейная форма с ламинатом отделена от циркулирующей жидкости гибкой мембраной; при этом жидкость можно быстро нагреть, а затем охладить для отверждения ламината.
«В то время как при обычном процессе отверждения с использованием автоклава отверждение происходит при давлении 100 psi и требует больше времени для производственного цикла, применяемый в компании Quicstep процесс с использованием теплопередающей среды позволяет осуществлять точный контроль температуры в ходе процесса отверждения» — говорит Бенжамин Людтке. Для снижения стоимости повторной сертификации в этом процессе используются существующие предварительно пропитанные материалы, сертифицированные для применения в процессах с использованием автоклава. В одной из систем с применением предварительно пропитанных материалов, использование данного процесса позволило сократить время производственного цикла с 20 до 4 часов. «Так как данный процесс позволяет точно контролировать и быстро изменять температуру литейной формы, то он уменьшает продолжительность процесса, расход энергии, объем капиталовложений и общую стоимость производства компонента» — говорит Бенжамин Людтке.
В 2010 г. компания Quickstep объединилась с компанией Vector Composites для реализации научно-исследовательского проекта с целью демонстрации способности проводить отверждение однонаправленного предварительно пропитанного эпоксидной смолой CYCOM 977-3 материала в соответствии с авиакосмическими стандартами. Эти процессы были приняты, и в настоящее время начался следующий этап этого проекта — подготовка к испытаниям деталей, изготовленных из ламината. Предполагается, что результаты испытаний будут получены к лету 2015 г.
Кроме того, компания Quickstep начала работы в автомобильной промышленности с использованием разработанного ею процесса переноса распыляемой смолы (RST — resin spray transmission) — автоматизированной системы быстрого отверждения, для получения композитных материалов, имеющих поверхность класса А. «Для создания деталей с использованием технологии БИA мы проводим совместную работу с несколькими европейскими компаниями» — говорит Бенжамин Людтке.
Взгляд в будущее
Технология БИA продолжает развиваться с целью решения проблем применения, связанных с размерами и качеством деталей, стоимостью производства и временем отверждения. Происходит также ее внедрение в различные отрасти промышленности, включая авиакосмическую промышленность, автомобильную промышленность, производство возобновляемых источников энергии, производство бытовой электроники и даже производство сельскохозяйственных машин и оборудования. Однако, для удовлетворения растущей потребности в композитных материалах в различных отраслях промышленности производителям необходимо большее количество пластика, армированного углеродным волокном. «Огромное количество углепластика потребляет авиакосмическая промышленность, и не так уж много остается остальным» — говорит Бенжамин Людтке. «Вследствие отсутствия у них доступа к высококачественному углеволокну, компании обращаются к натуральным волокнам, таким как джут и пенька, а также к натуральным смолам, получаемым из таких источников как кукуруза, соя и даже скорлупа орехов кешью».
Эрик Кастерлайн добавляет, что для расширения области применения технологии БИA важным фактором является обучение. «Необходимо пересмотреть программы обучения для среднего и высшего звена руководства, повышения технического мастерства и, возможно, промышленной стандартной сертификации технического персонала» — сказал он.
Применение технологии без использования автоклава в военной промышленности
Возможно, наиболее успешной демонстрацией крупного производства без использования автоклава является изделие Научно-исследовательской лаборатории военно-воздушных сил Lockheed Martin X-55A Advanced Composite Cargo Aircraft — грузовое воздушное судно, изготовленное с применением передовых композитных материалов.
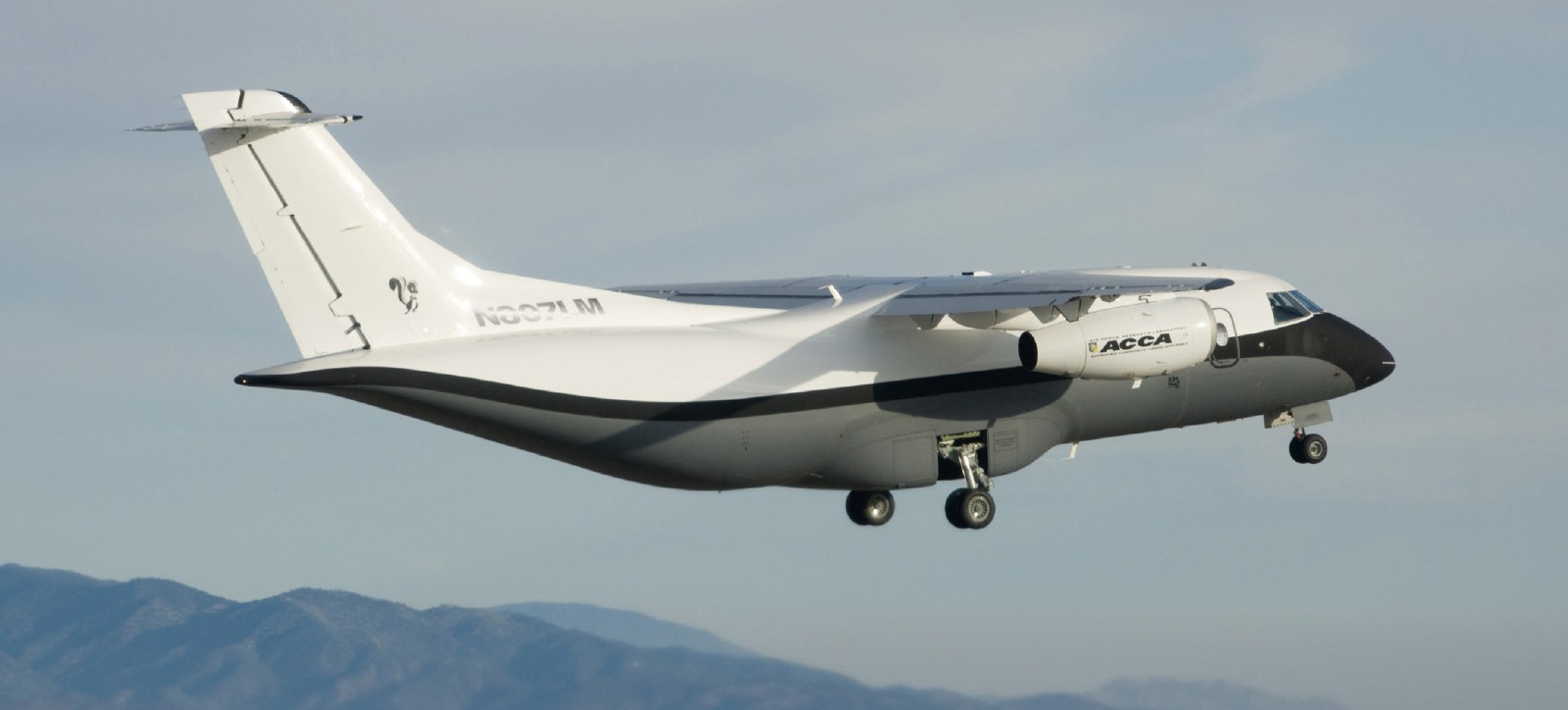
Lockheed Martin X-55A Advanced Composite Cargo Aircraft
Используя применённое в самолете Dornier 328 уменьшение места позади кабины, чтобы избежать новых расходов, связанных с управление полётами, при создании самолета Lockheed Martin был использован изготовленный из композитного материала фюзеляж длиной 60 футов, состоящий из восьми частей. Это позволило компании изготовить репрезентативный военно-транспортный самолёт всего за 18 месяцев, уложившись в бюджет, равный 50 миллионов долларов.
После успешного завершения данного проекта, другие компании последовали этому примеру. «В компании Boeing был изготовлен самолет Phantom Eye, при строительстве которого широко использовалась технология БИA» — говорит Джон Рассел, технический директор Отдела производства и промышленных технологий Научно-исследовательской лаборатории военно-воздушных сил. «Производители самолётов коммерческой авиации также намерены использовать технологию БИA, так как они понимают, что детали большего размера невозможно изготовить в существующих в настоящее время самых больших автоклавах».
Управление министерства обороны (США) по перспективным исследованиям и разработкам (DARPA) проводит испытания, в результате которых в конечном итоге можно будет уменьшить количество образцов, которое необходимо для сертификации деталей, предназначенных для применения в авиакосмической области. Результаты этих испытаний можно будет рассматривать в качестве «Святого Грааля» для производителей, работающих в оборонной промышленности. «Если мы сможем сократить количество испытаний без увеличения риска, то это облегчит компаниям поиск новых материалов» — говорит Джон Рассел.
Несмотря на все усилия в области научных исследований и разработок, затраченные в военной и оборонной промышленности, большинство организаций занимает выжидательную позицию. «Большинство решений зависит от федерального бюджета» — говорит Джон Рассел. «Проведены исследования, связанные с изготовлением самолета-разведчика, бомбардировщика и истребителя следующего поколения. Министерство обороны США решит, будет ли оно строить новый самолёт или отремонтирует старые». Затем Рассел сказал, что если военному министерству потребуется новый самолёт взамен C-5s и C-17s или взамен B-52 и B-1, то использование технологии БИA будет правильным решением, из-за больших размеров проектируемых новых самолётов. «Однако если это будет самолёт-истребитель, то я не вижу необходимости использования технологии БИA» — сказал он. «Детали этого самолета достаточно небольшие для того, чтобы использовать существующие автоклавы, имеющиеся в промышленности».