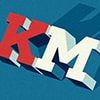
Изготовление композитной оснастки без использования печи и автоклава
рубрика: технологии
Композитная оснастка, способная выдерживать температуру 177°C, была изготовлена без использования печи или автоклава. Процесс инфузии и отверждения проходил с высокой скоростью и не требовал последующего отверждения. Для выяснения соответствия между формой конечного продукта и формой мастер-модели при использовании материалов, процессов отверждения и мастер-модели из пенополиуретана без применения печи и автоклава (NONA) был проведен анализ размеров мастер-модели и композитной оснастки. Кроме того, анализ размеров проводился для оценки стабильности размеров оснастки. Анализ размеров показал термостабильность оснастки и ее хорошее соответствие форме пенополиуретанового шаблона.
Герметичность оснастки в условиях наличия вакуума была приемлемой как до, так и после циклического воздействия температуры. Полученная путем инфузии эпоксидная деталь успешно прошла отверждение на оснастке. Проведенное нами пробное изготовление показало возможность использования оснастки, изготовленной из композитного материала с помощью NONA-технологии, для производства крупногабаритных деталей из композитных материалов.
1. Введение
Крупногабаритные конструкции из композитных материалов, такие как используемая в NASA система запуска космических кораблей (SLS), имеют такие размеры, при которых затруднено применение современных автоклавов. Необходима новая технология, позволяющая сохранить рабочие характеристики композитного материала и одновременно освобождающая инженера-технолога от ограничений, накладываемых на размеры оборудования, необходимого для проведения процесса отверждения смолы. Значительный прогресс в этой области был достигнут благодаря разработке композитных материалов и процессов, не требующих использования автоклава.
В результате работ, проводившихся в соответствии со вторым этапом программы NASA «Малобюджетные инновационные исследования» компанией Cornerstone Research Group, была дана оценка уровня готовности для использования в технологии и на производстве (TRL/MRL) уникальной, двухкомпонентной системы на основе эпоксидной смолы, предназначенной для инфузии сухой углеродной преформы при комнатной температуре с последующим отверждением без дополнительного нагревания, позволяющим обеспечить при температуре 177°C рабочие характеристики композитного материала в течение нескольких часов [1–3]. Эта технология получила название процесса технологической обработки композитных материалов без использования печи и автоклава (NONA). Целью данной исследовательской работы являлось доказательство возможности использования этой технологии более масштабно, в частности, предполагалось изучить возможность использования конечного изделия в качестве оснастки для отверждения композитного материала. В конечном итоге планировалось получить оснастку для изготовления в масштабе 1:10 отделяющегося лепесткового обтекателя (состоящего из двух участков: сводчатого и цилиндрического). Уменьшенная модель детали обтекателя имела следующие размеры: 192 см в длину, 81 см в ширину и 41 см в высоту. С помощью такой оснастки в NASA могут изготовить четыре лепестка для создания уменьшенного прототипа обтекателя, предназначенного для использования в системе запуска космических кораблей, а также убедиться в возможности применения оснастки из композитного материала для производства таких лепестков.
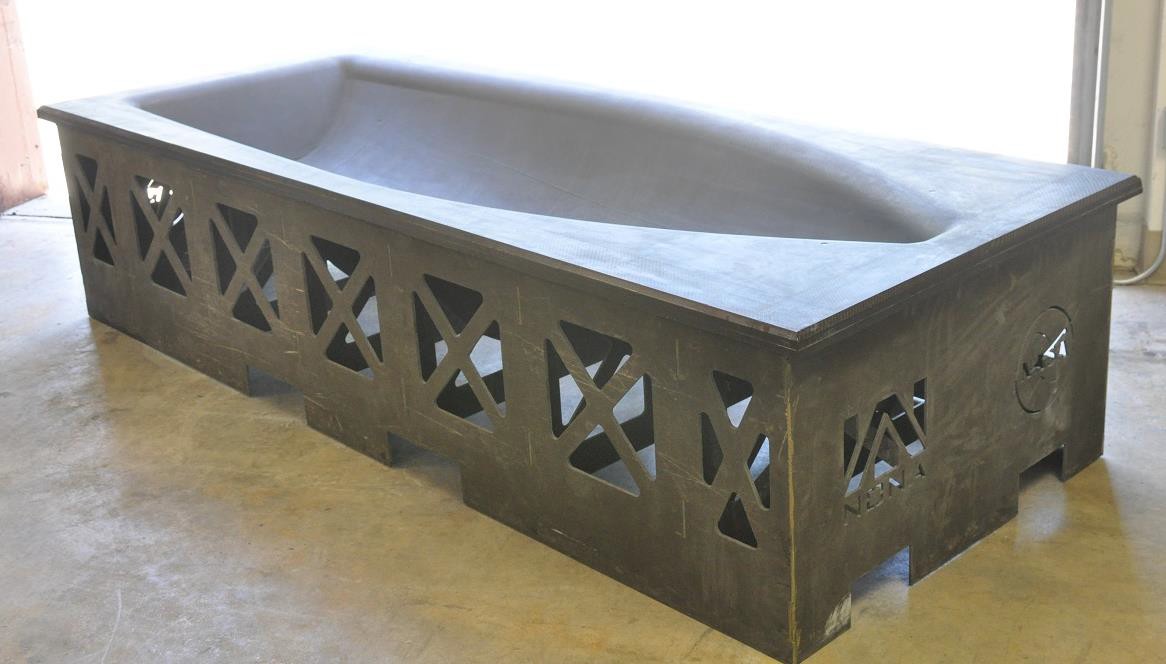
Рисунок 1. Оснастка со сводчатым участком, изготовленная из композитного материала без использования печи и автоклава
1.1. Предпосылки программы
В конце 2013 г. компания CRG создала компанию NONA Composites, LLC для коммерциализации технологий, разработанных на этапе I программы SBIR, и для поставки смол, технологий и композитной оснастки производителям деталей из таких материалов. Данная исследовательская работа по изготовлению оснастки была проделана компанией NONA Composites при участии нескольких производителей оснастки из композитных материалов, имеющих промышленное значение. Для изготовления эффективно работающей оснастки потребовалось проведение двух испытаний.
2. Проведение экспериментов
2.1. Изготовление мастер-модели
Мастер-модель была приобретена у компании General Plastics. Она была изготовлена из термостойкого пенополиуретана FR-4718. Этот пенополиуретановый материал был выбран для изготовления мастер-модели вследствие его низкой теплоёмкости и теплопроводности, а также высокой термостойкости. Кроме того, в компании General Plastics на модель снаружи наносилось покрытие из серой винилэфирной грунтовки Duratec и проводилась финишная обработка изделия. Это покрытие было выбрано на основании имеющегося опыта по нанесению этого материала на пенополиуретан FR-4718, рекомендаций продавца и способности материала к отверждению без подведения дополнительного тепла. Мастер-модель была помещена на стальную опорную плиту с целью закрепления на твердой вакуумонепроницаемой поверхности.
При изготовлении первой части оснастки покрытие Duratec треснуло, в результате чего была нарушена герметичность мастер-модели. При второй попытке изготовления оснастки мастер-модель покрыли тефлоновой пленкой с нанесенным на нее клеем Tooltec CS5 производства компании Airtech. Для создания фланца, предназначенного для защиты от утечек, по периметру был сформирован ограничитель из пенополиуретана. Кроме того, было изготовлено деревянное основание, к которому прикрепили пенополиуретановую мастер-модель с целью создания легкой конструкции, обладающей повышенной прочностью и служащей для предотвращения изгиба или искривления всего пенополиуретанового изделия при проведении отверждения по NONA-технологии. На рисунке 2 показана мастер-модель после повторной отделки.
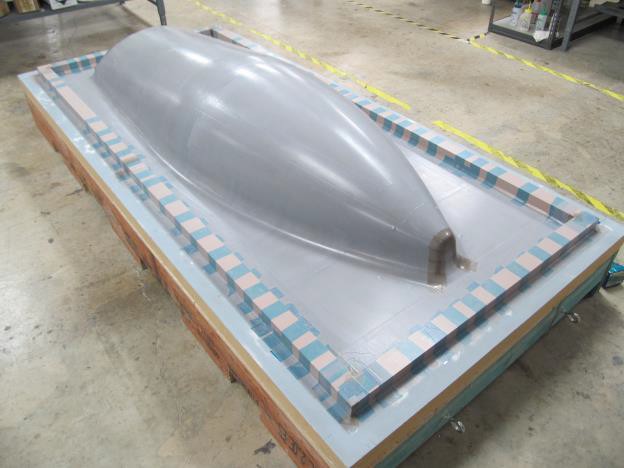
Рисунок 2. Мастер-модель с основанием, отремонтированной поверхностью и пленкой Tooltec
2.2. Основные материалы и процессы
При проведении этой исследовательской работы для оценки влияния различных параметров укладки слоёв и процессов на рабочие характеристики обработанной детали были изготовлены два листа сводчатой формы. При изготовлении всех изделий из композитных материалов, описанных в этой статье, использовалась производимая компанией NONA Composites полимерная система RT-177 (аналогичная производящейся компанией CRG смоле NONA-001 [1–2], о которой сообщалось ранее) — двухкомпонентная эпоксидная смола, разработанная для процессов с применением NONA-технологии. Она состояла из компонентов, имеющих запатентованный состав, и вводилась путем инфузии при комнатной температуре с использованием обычного процесса вакуумной инфузии. При каждой инфузии двухкомпонентная смола смешивалась вручную, подвергалась дегазации в дегазационной установке производства компании Laco Technologies до значения абсолютного давления 13.3 Па в течение 10 минут, и во время инфузии поддерживалась температура ниже 30°C. При массе партии менее одного килограмма температуру можно было регулировать путем периодического перемешивания смолы. При инфузии партии массой более одного килограмма, как, например, для изготовления этих оснасток, с целью поддержания низкой температуры использовали ванну со стоячей холодной водой и проводили периодическое перемешивание смолы. Для уплотнения волокон и уменьшения пористости ламината к содержимому вакуумного мешка в течение инфузии прикладывали абсолютное давление менее 133 Па.
Ткань из углеволокна, использованная для укладки слоёв при изготовлении оснастки, представляла собой различные комбинации плетения 2×2 твил (3k Toho TENAX) и 12k стандартного модуля углеволокна в ткани 2×2 твил (2D-670-12k-2/2TW-UNC). Укладка слоёв при изготовлении первой части оснастки осуществлялась в 28 слоев, квазиизотропно с использованием ткани из углеволокна 3k, 2×2 твил. Укладка слоёв осуществлялась по схеме [0]15 с использованием ткани 12k твил. Для инфузии и формования методом вакуумного мешка использовали коммерчески доступные компоненты. Использовали специальные трубки, жидкие среды, клапаны и вакуумные мешки, предназначенные для применения при высокой температуре (177 °C), так как во время процесса отверждения с применением NONA-технологии происходило образование тепла.
2.2.1. Изготовление части оснастки. Испытание 1
Способ инфузии, сходный с описанным здесь, был использован при строительстве корпусов крупных судов.
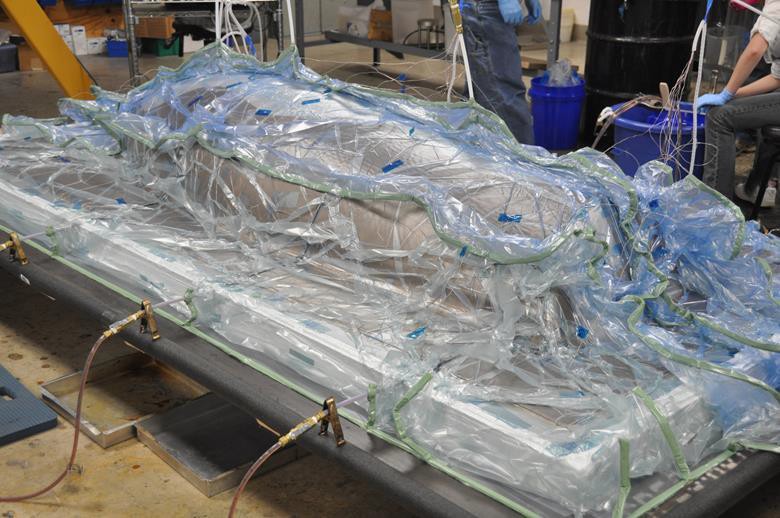
Рисунок 3. Получения первой части оснастки методом инфузии. Испытание 1
Как показано на Рисунке 3, смола поступала с каждой стороны через четыре впускных отверстия из ведер со смолой, расположенных по одному с каждой стороны; при этом вдоль верхнего выступа детали находились три отдельные области воздействия вакуума. Инфузия проходила хорошо и продолжалась в течение примерно 30 минут, считая от начала и до момента закрытия всех клапанов.
2.2.2. Изготовление части оснастки. Испытание 2
Уложенные слои ткани уплотняли с помощью вакуума в течение, по крайней мере, одного часа каждый раз после укладки 4-го, 9-го и 15-го слоя. Для разглаживания складок ткани из углеволокна во время уплотнения использовали валики. Образование складок является обычным; однако недостаток 45° волокон может вызвать проблемы, так как многочисленные слои могут вести себя как один большой слой. Для обеспечения герметичности основного мешка в условиях наличия вакуума, а также для обеспечения того, чтобы липкая пленка Tooltec не отклеивалась от пенополиуретановой мастер-модели, использовали два вакуумных мешка. Основной мешок был прикреплен к верхней части пенополиуретанового выступа, добавленного для защиты от утечек. Второй мешок был прикреплен к внешнему периметру мастер-модели за пределами границы пленки Tooltec. Скорость утечки, равная 0.71 торр./мин (0.028 дюймов ртутного столба/мин), была зарегистрирована за период времени, равный 16 минутам, после того, как вся установка находилась под постоянным воздействием вакуума в течение более 24 часов. Для изготовления этой оснастки был использован метод расходящегося потока. В четыре канала подачи смолы она поступала из двух ведер. Каждый канал перед вхождением в деталь разветвлялся в середине линии подачи Airtech Omega перпендикулярно выступу детали. На пенополиуретановом выступе внешнего фланца располагался непрерывный периметр спиральной трубки для подачи смолы с помощью двух вакуумных линий, расположенных на противоположных концах. Этот способ был использован для обеспечения хорошей вентиляции, и в то же время он позволял провести подачу смолы в деталь в течение 30 минут. 35 кг смолы при использовании NONA-технологии смешивались и подвергались дегазации в процессе подачи в два питательных ведра. Смола в питательных ведрах имела температуру ниже 30°C, которая поддерживалась с помощью ледяной бани и периодического перемешивания. Общее время инфузии, начиная от момента открытия линий подачи смолы и заканчивая моментом закрытия всех клапанов, составляло 48 минут, хотя смола достигала мёртвой зоны на периметре через 20 минут.
В обоих испытаниях с изготовлением детали был использован очень дешевый изоляционный материал для изоляции со стороны мешка с целью сохранения выделяющегося тепла в ламинате в течение отверждения, что является критичным для процесса отверждения при использовании NONA-технологии.
Предварительно отвержденные детали из углеволокна/эпоксидной смолы проходили машинную обработку с целью получения основания решётчатого типа, позволяющего увеличить жёсткость оснастки и облегчить работу со сводчатой частью инструмента. Решётчатая конструкция была собрана и затем приклеена ко второму листу с помощью пастообразного клея Henkel Hysol® EA 9394, как и влажная укладка слоёв углеволоконной ткани и эпоксидной смолы Henkel Hysol® EA9396. Склеенное и ламинированное собранное основание проходило отверждение при комнатной температуре в течение трех дней, после чего с ним начиналась работа.
2.3. Определение размеров
Определение размеров мастер-модели и второй части оснастки проводилось компанией Exact Metrology с помощью системы лазерного сканирования для определения координат ROMER Absolute Arm SI 3D. В течение каждого сканирования определялись координаты более 2.9 миллионов точек. Все сканирования проводились в условиях окружающей среды при нахождении деталей в свободном состоянии. Небольшие металлические резьбовые метки закреплялись на мастер-модели перед использованием с целью изготовления второй оснастки для сравнения шаблона с отвержденной оснасткой, а также с оснасткой, подвергавшейся циклическому воздействию тепла.
2.4. Изготовление детали с помощью инфузии и оснастки, изготовленной с применением NONA-технологии
Полностью собранная оснастка, изготовленная с помощью NONA-технологии, была использована для изготовления детали обтекателя из композитного материала, полученного путем инфузии смолы, с целью проверки оснастки на герметичность в условиях наличия вакуума. Перед заливкой и отверждением детали поверхность оснастки полировали с помощью наждачных кругов 3M ScotchBrite®, обеспечивали герметичность с помощью герметика Henkel Frekote® B-15 и отделяли с помощью разделительного состава Henkel Frekote® 55-NC. В области детали проводилась укладка четырех слоев 12K углеволокна 2×2 твил и проводилась подготовка к инфузии. После успешной проверки герметичности в ламинат вводилась эпоксидная смола Momentive Epon™ 862 и отвердитель Epikure™ W. Для отверждения ламината в течение 6.5 часов проводился цикл нагревания и охлаждения с выдерживанием в течение 1.5 часов при температуре 177°. После отверждения деталь извлекали из формы и осматривали.
3. Результаты
3.1. Оснастка при испытании 1
Что касается профиля отверждения во время изготовления оснастки при испытании 1, то средняя величина температуры всей детали была равна 158°C ±15°C. Средняя величина температуры оснастки в области обработанной детали была равна 163°C ±8°C. Максимальная температура составляла 182°C и наблюдалась на фланце возле впускного отверстия для смолы.
Деталь извлекалась из формы без проблем, и большая часть оснастки не имела пустот; однако имелись очевидные проблемы. Изогнутый участок между внешним фланцем и границей корпуса в носовой и хвостовой части характеризовался пористостью по всей толщине ламината. Имелось несколько областей поверхностного выкрашивания возле зоны вытяжки, однако, оказалось, что они создают проблемы только эстетического характера. Покрытие Duratec на поверхности мастер-модели имело пузыри и трещины во многих местах. Большие трещины размером более 6 мм в глубину располагались крестообразно в куполообразной области детали. Раковины имелись, главным образом, на изогнутом участке по границе корпуса там, где ламинат имел пористость. При обследовании покрытия Duratec было обнаружено, что в некоторых областях толщина составляла менее 0.25 мм, в то время как толщина, рекомендованная компанией Hawkeye Industries (производитель покрытия Duratec), составляет 0.51–0.76 мм.
Кроме того, имелись проблемы, связанные с профилем отверждения детали. В то время, как в некоторых областях детали температура достигала более 180°C, имелись и такие, в которых она составляла только 120°C. Средняя величина температуры, регистрировавшейся с помощью 24 термоэлементов, располагавшихся на детали, составляла 158 +/-15°C. Отрезок времени между максимальными значениями температуры составлял более 29 минут, с первым максимальным значением (165°C), наблюдавшимся в середине цилиндрической части через 140 минут после инфузии, и последним максимальным значением (136°C), наблюдавшимся в носовой части через 170 минут после инфузии.
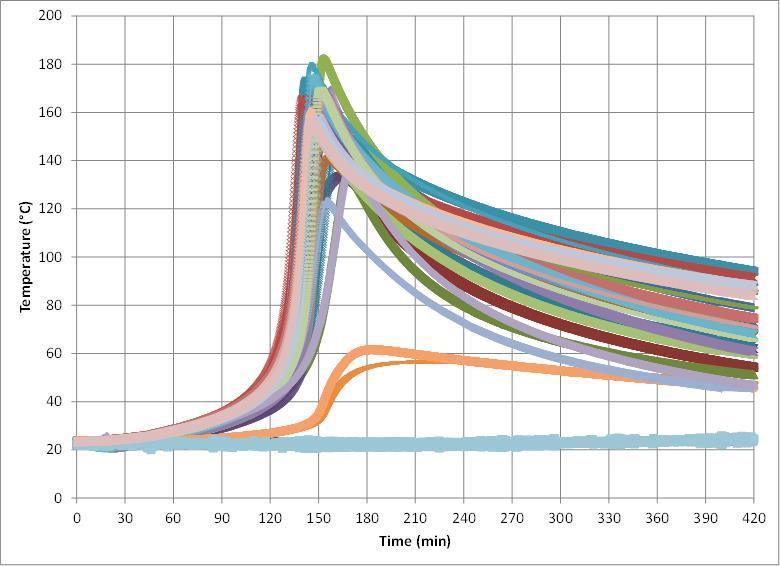
Рисунок 4. Температурный профиль для первого листа при его отверждении во время проведения первого испытания (нижние кривые показывают комнатную температуру (синего цвета) и температуру пенополиуретановой литейной формы (оранжевого цвета)
На Рисунке 4 показан температурный профиль, полученный при использовании 32 термоэлементов. Четыре термоэлемента располагались на шаблоне или при комнатной температуре. Большой разброс значений температуры и большие временные промежутки между максимальными значениями могут приводить к возникновению проблем, связанных с качеством ламината и значениями допуска на размер. В случае этой детали отверждение носовой и хвостовой части произошло через 20–30 минут после того, как большая часть детали уже прошла отверждение. Ламинат в этих областях отставал от оснастки и имел пористость на всем протяжении этих областей. Пористость, вероятно, увеличивалась, когда воздух из треснувшего пенополиуретанового шаблона проходил в еще не отвержденные участки. На Рисунке 5 показана пористость в области, где носовая часть граничит с фланцем.
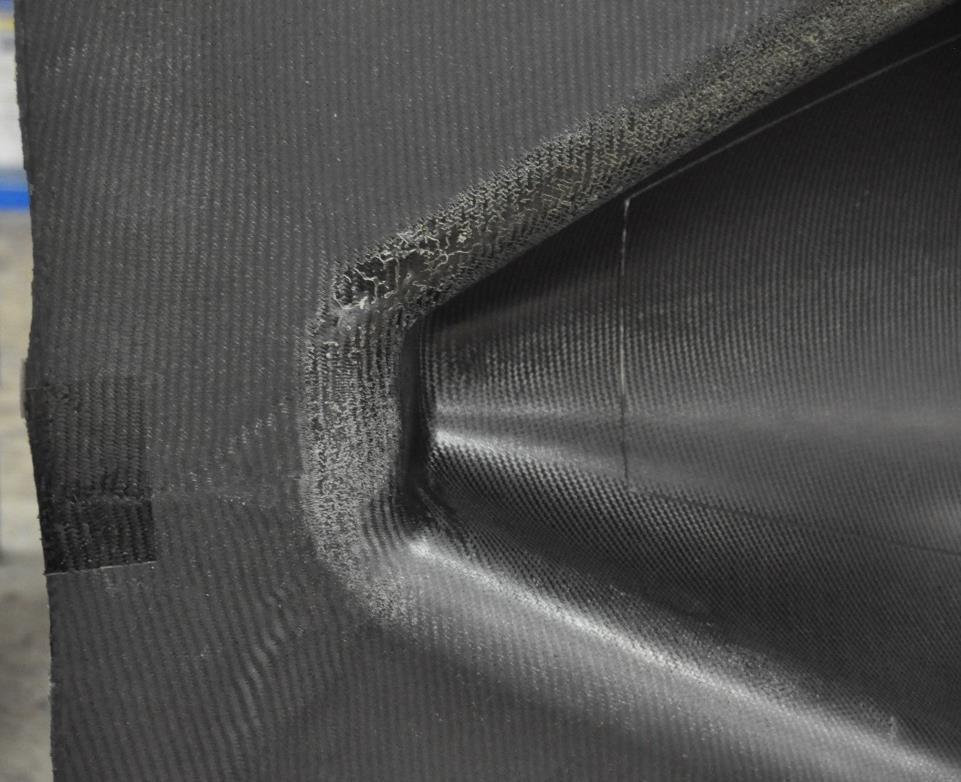
Рисунок 5. Области видимой пористости на первой оболочке
Вакуумная проверка герметичности проводилась на оснастке с целью проверки области внутри внешнего фланца. Значительная пористость в носовой и хвостовой части была обнаружена с помощью аудиодетектора утечки. Предполагается, что именно в этих областях происходит нарушение герметичности, обнаруживаемое при проведении проверки.
3.2. Оснастка при испытании 2
Первое испытание было необходимо для идентификации проблем, возникающих при использовании современной NONA-технологии в случае, когда площадь изделия составляет 4.6 м2, и не являющихся такими очевидными при площади изделия, равной 0.93 м2, при которой проводились последние разработки. При проведении второго испытания оснастки стояла задача выяснения следующих вопросов:
- Закрепление пенополиуретанового шаблона на основании: Необходимо было повысить жёсткость мастер-модели из пенополиуретана. Основание было использовано для фиксации пенополиуретанового шаблона с целью предотвращения чрезмерного коробления в течение формования методом вакуумного мешка и отверждения с использованием NONA-технологии.
- Использование пленки Tooltec для исправления дефектов поверхности покрытия Duratec: Трещины в пенополиуретановой мастер-модели заделывались с помощью шпатлёвки AdTech P-17 SMCR, а затем для обеспечения герметичности вся поверхность покрывалась клеем Tooltec CS5 с целью предотвращения утечки при проведении отверждения даже при условии образования новых трещин.
- Защита кромки: Для обеспечения защиты оснастки от повреждения при его использовании был сформирован внешний фланец. Изогнутый фланец может уменьшить риск расслаивания при ударе.
- Использование более тяжелой ткани из углеволокна: Использование углеволокна 12K твил обеспечивает хорошую драпируемость и позволяет больше углеволокна поместить в одном слое, за счет чего уменьшается объем работы.
- Изменение схемы подачи смолы: Для достижения лучшей вентиляции детали с целью уменьшения количества и объема пустот, а также для увеличения объёма волокна было изменено направление потока. При проведении второго испытания смола поступала в деталь через четыре участка, расположенных на верхней/средней части детали и выходила во внешнее кольцо вакуума на нижнем/внешнем периметре.
- Улучшение изоляции: Улучшенная изоляция (за счет изменения теплопроведения, конвекции и излучения) позволяет получить более правильный температурный профиль и детали более высокого качества. При проведении первого испытания степень изоляции была недостаточной, что привело к появлению градиентов отверждения в детали. Степень изоляции коррелировала с успешным получением предварительно изготовленных деталей, имеющих ограниченную кривизну. Чем выше степень кривизны, тем лучше требуется изоляция.
- Утилизация смолы: Вся неиспользованная смешанная смола (включая материал, попавший в ловушку для смолы) смешивалась с песком для безопасного отверждения и утилизации.
- Определение допуска на размер: Для обеспечения возможности измерения допусков на размер с помощью координатно-измерительной машины к мастер-модели были добавлены элементы базирования. Шаблон сканировали перед укладкой слоёв. Затем шаблон был вновь сканирован после отверждения с использованием NONA-технологии для определения влияния процесса отверждения на стабильность размеров. Оснастку сканировали после отверждения, а также после окончания термодинамического цикла при температуре 177°C.
Температура оснастки, изготовленной с помощью NONA-технологии, а также температура пенополиуретановой мастер-модели определялась с помощью 32 термоэлементов. Большинство термоэлементов располагалось непосредственно на поверхности вакуумного мешка, и только пять на пенополиуретановой детали, а также в окружающей среде. Температурный профиль был лучше, чем при первом испытании. Первый термоэлемент показал максимальное значение, равное 165°C, через 165 минут после инфузии, а последние термоэлементы, расположенные на детали (в области хвостовой части и плоской области периметра), показали максимальное значение, равное 161°C и 160°C, соответственно, через 177 минут после инфузии. При первой попытке инфузии было зарегистрировано время запаздывания, равное 30 минутам, за которые достигалось максимальное значение температуры для всей оснастки, а при второй инфузии время запаздывания составляло всего лишь 12 минут. Средняя величина температуры для всех термоэлементов, расположенных на оснастке, составляла 162.5 ±3.8°C, а средняя величина температуры для термоэлементов, расположенных в области оснастки, но характеризующих температуру детали (7 термоэлементов), составляла 163.7 ±0.9°C. Наибольшее зарегистрированное значение температуры составляло 169.0°C и было отмечено у внешнего фланца периметра. Наименьшее значение температуры, зарегистрированное на оснастке, изготовленной с помощью NONA-технологии, составляло 150.5°C и было отмечено в носовой части за пределами детали.
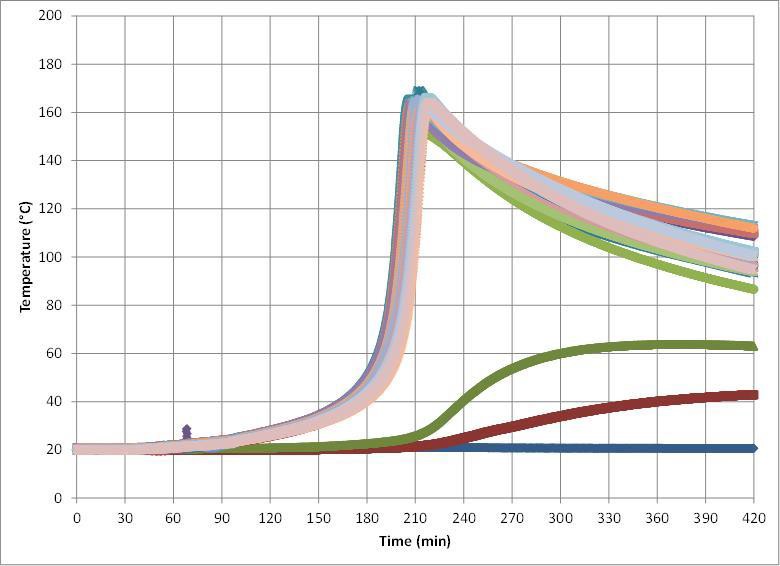
Рисунок 6. Температурный профиль для оснастки, отвержденной при проведении второго испытания (нижние кривые показывают комнатную температуру (синего цвета) и температуру пенополиуретановой литейной формы (красного и зеленого цвета)
На Рисунке 6 можно видеть плотное расположение кривых, отражающих температуру детали, а также запаздывание температуры пенополиуретановой модели в ходе отверждения с использованием NONA-технологии. На Рисунке 7 отражены показания термоэлементов, расположенных в различных областях лицевой части оснастки, и можно видеть небольшие различия максимальных значений температуры и времени достижения этих значений.

Рисунок 7. Максимальные значения температуры и времени достижения максимального значения, зарегистрированные термоэлементами, расположенными в разных участках детали
При достижении максимального значения температуры детали система начинала охлаждаться. Изоляционный материал удаляли, когда температура детали составляла от 40 до 50°C. Жидкая среда представляла собой только смолу без признаков утечки воздуха или других проблем. После удаления жидкой среды было обнаружено, что инфузия детали прошла хорошо, однако имелись большие складки в тех местах, в которых ткань из углеволокна образовала комки в процессе уплотнения и формования методом вакуумного мешка. Как было сказано ранее, складки разглаживались при уплотнении с помощью валика, однако при использовании ткани 12k уплотнение проходило не вполне успешно. Самая большая складка образовалась на гребне хвостовой части. Складки являются обычным явлением для позитивной мастер-модели, в которую ткань скорее заталкивается, чем распределяется в ходе процесса формования методом вакуумного мешка. В этих местах каждый слой следует аккуратно уложить для предотвращения образования складок. Если этого не сделать, то функциональность детали будет низкой.
Обращенная к оснастке сторона детали, изготовленная с использованием NONA-технологии, была увлажнена в большинстве участков. Внешний фланец для защиты от утечек был хорошо выражен и имел приятный внешний вид (Рисунок 8).

Рисунок 8. Вторая часть оснастки, изготовленная при проведении второго испытания.
Вдоль гребня на цилиндрическом участке имелись немногочисленные области диаметром менее 2.54 см с некоторой пористостью поверхности. Оказалось, что эти области имеются только на поверхности и отсутствуют в толще ламината этой области. На большом изогнутом участке также имелись некоторые складки ткани с небольшим количеством скопившейся смолы. Следует заметить, что эти складки не выглядели как шероховатость на поверхности оснастки. Контур оснастки был сохранен, однако вследствие того, что складки ткани слегка разглаживались от поверхности оснастки, смола могла скапливаться между тканью и оснасткой.
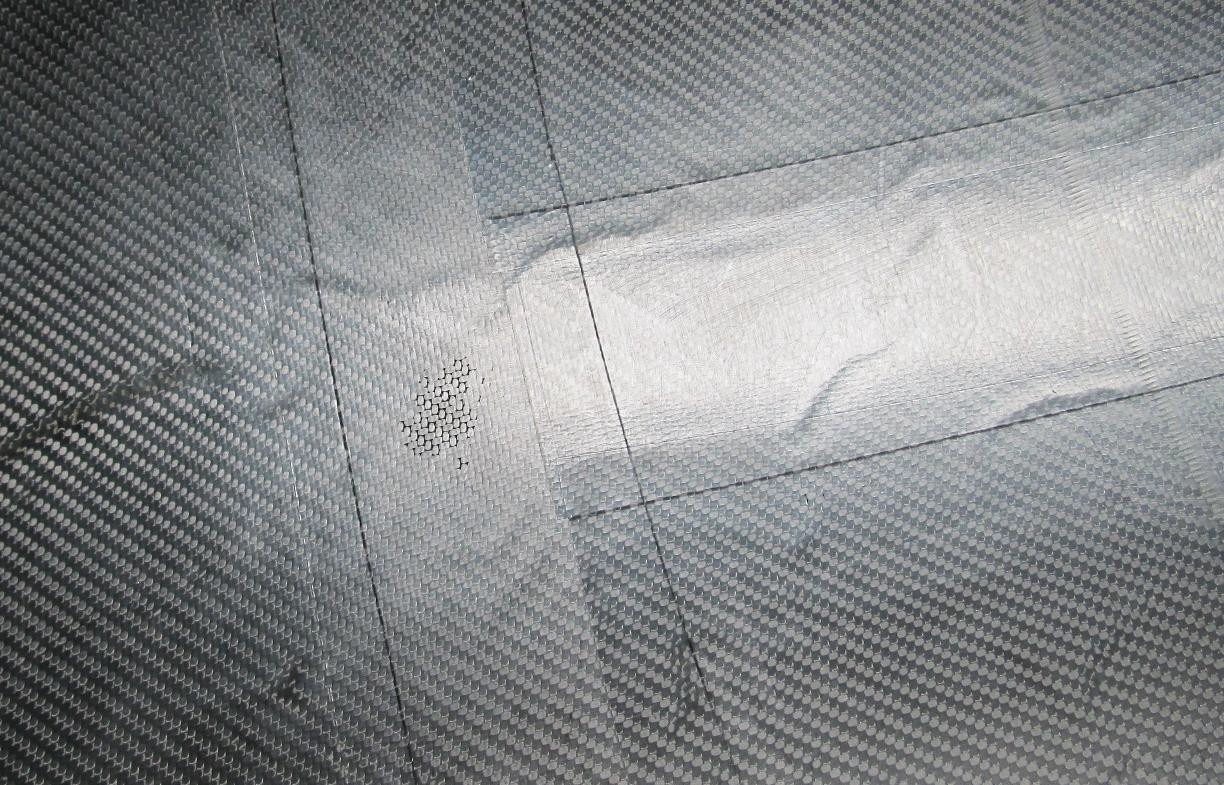
Рисунок 9. Поверхность оснастки с оспинами и складками
На Рисунке 9 показана поверхность с оспинами и складками. Измерения показали, что конечная толщина в плоской области составляет 0.965 см, что очень близко к целевому значению толщины, равному 0.953 см.
Проверка степени герметичности в условиях наличия вакуума проводились при комнатной температуре. Для проведения испытания вся поверхность, начиная с места, расположенного на расстоянии 2.54 см внутрь внешнего периметра, заключалась в вакуумный мешок. Скорость утечки, составляющая 0.46 торр/мин (0.018 дюймов ртутного столба/мин), измерялась в течение более 24 минут с использованием цифрового вакуумметра. Такая скорость утечки является более чем достаточной для большинства случаев применения предварительной пропитки и инфузии.
3.3. Точность размеров и термостойкость
Результаты анализа размеров, полученные после второй попытки изготовления мастер-модели и оснастки, показали предполагаемое искривление отвержденной оснастки, а также хорошую термостойкость отвержденной оснастки и мастер-модели. У отвержденной части оснастки по сравнению с мастер-моделью наблюдалось искривление типа «spring-in», при котором боковые стенки смещались вовнутрь, а донная часть смещалась наружу. Размерный эффект этого смещения составлял приблизительно −2.8 мм в центральной области сводчатой части возле границы фланца и +1.9 мм в центральной области сводчатого участка возле донной части оснастки (верхняя часть мастер-модели), как показано на Рисунке 10.
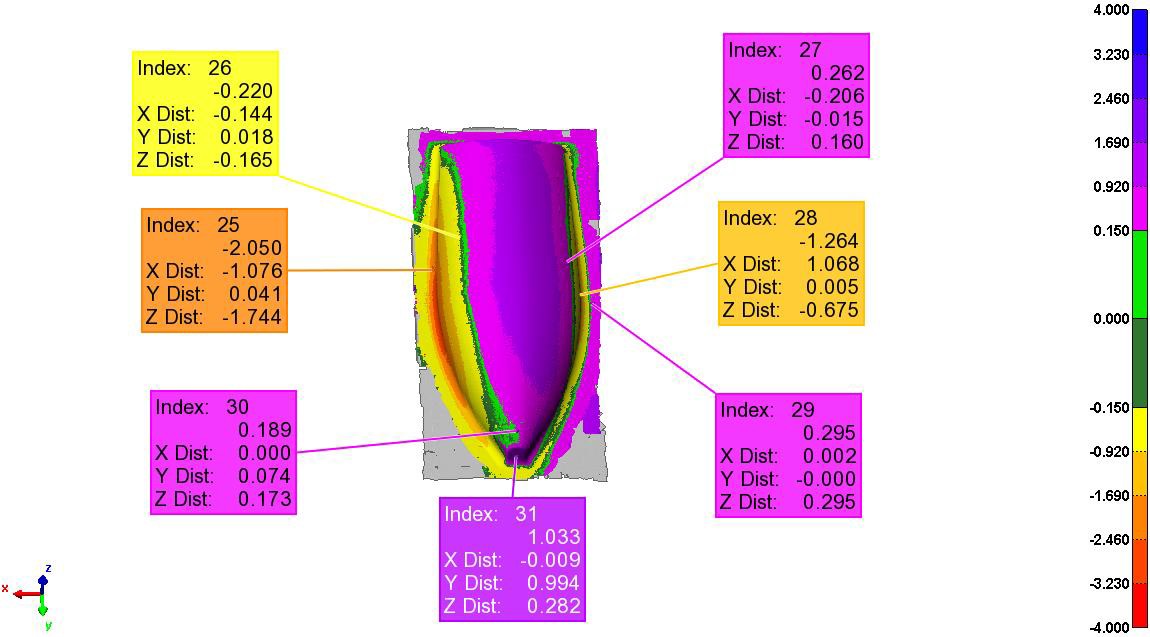
Рисунок 10. Анализ отклонений с использованием координатно-измерительной машины (CMM), при сравнении мастер-модели с отвержденной частью оснастки, вид спереди (данные представлены в мм)
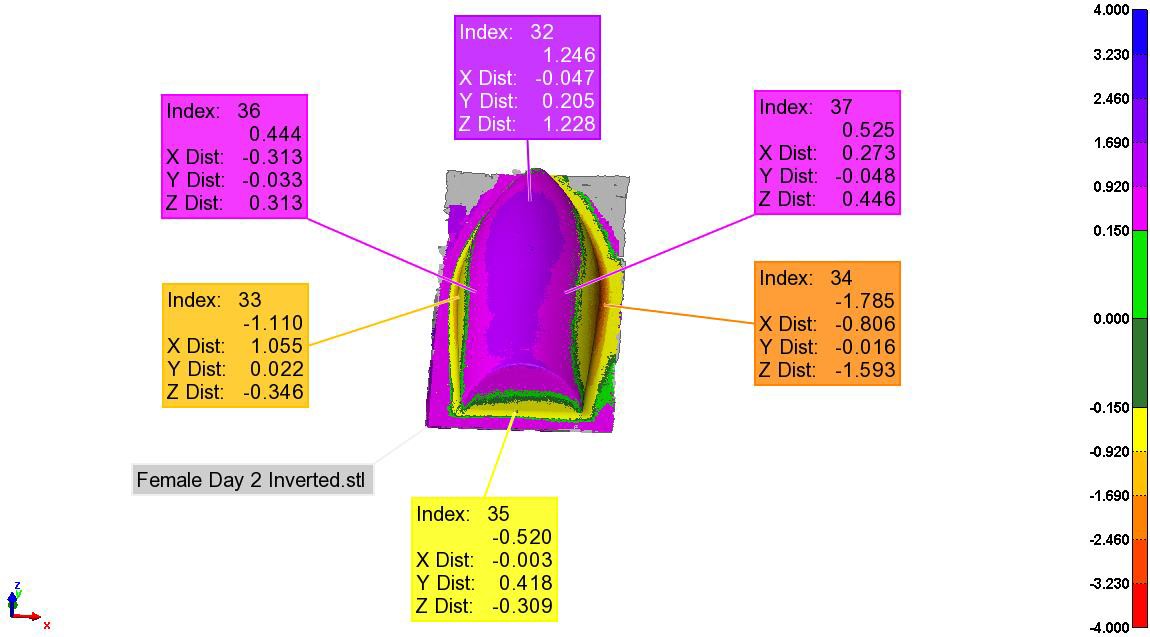
Рисунок 11. Анализ отклонений с использованием координатно-измерительной машины (CMM), при сравнении мастер-модели с оснасткой после термодинамического цикла, вид сзади (данные представлены в мм).
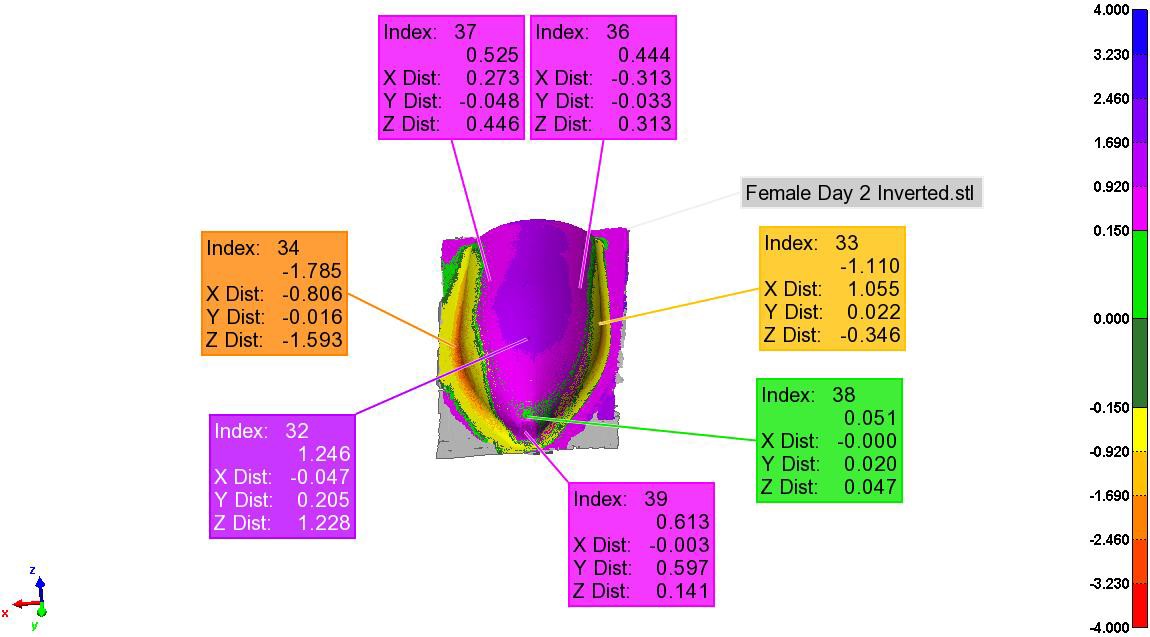
Рисунок 12. Анализ отклонений с использованием координатно-измерительной машины (CMM), при сравнении мастер-модели с оснасткой после термодинамического цикла, вид спереди (данные представлены в мм).
Это искривление связано с разницей в величине усадки при отверждении и разницей в величине коэффициента теплового расширения во внеплоскостном (z) направлении ламината по сравнению с плоскостным (x-y) направлением. Это происходит вследствие того, что над специфическими свойствами ламината во внеплоскостном направлении преобладают свойства смолы, а в плоскостном направлении преобладают свойства волокна, особенно в толстых ламинатах. Дальнейший анализ эффекта искривления показал, что угловое изменение на 1° в центральной области сводчатой части мастер-модели при условии сходного искривления оснастки обеспечит отклонение на 4.9 мм для боковых частей и на 6.5 мм для верхних. Проведенные ранее многочисленные исследования по поводу искривления изделий из композитных материалов позволяют предположить, что угловое изменение на 1–2° способно компенсировать это изменение размеров [4–6]. Описанные попытки изготовления изделий позволяют предположить, что угловое изменение менее чем на 1° позволяет компенсировать эффект искривления. Возможным объяснением этой компенсации является относительно небольшое количество времени, в течение которого деталь подвергается воздействию максимальной температуры. Последние исследования показали необходимость увеличения угловой компенсации при увеличении температурного воздействия.
Полностью собранная оснастка подвергалась циклическому воздействию тепла с выдерживанием при температуре 120 и 177°C и дальнейшим медленным охлаждением до комнатной температуры. Анализ отклонений с использованием координатно-измерительной машины проводился повторно для определения эффекта (при его наличии) циклического воздействия температуры на точность размеров оснастки. После нагревания размеры оставались приблизительно такими же, какими они были до нагревания оснастки, что указывает на термостойкость смолы при использовании NONA-технологии, а также на стабильность размеров оснастки.
Размеры пенополиуретановой мастер-модели мало изменились после отверждения с использованием NONA-технологии, что свидетельствует о термостойкости изделия при отверждении с использованием NONA-технологии. В большинстве участков мастер-модели наблюдалось увеличение размеров, приблизительно, на 0.5 мм (Рисунки 13 и 14).
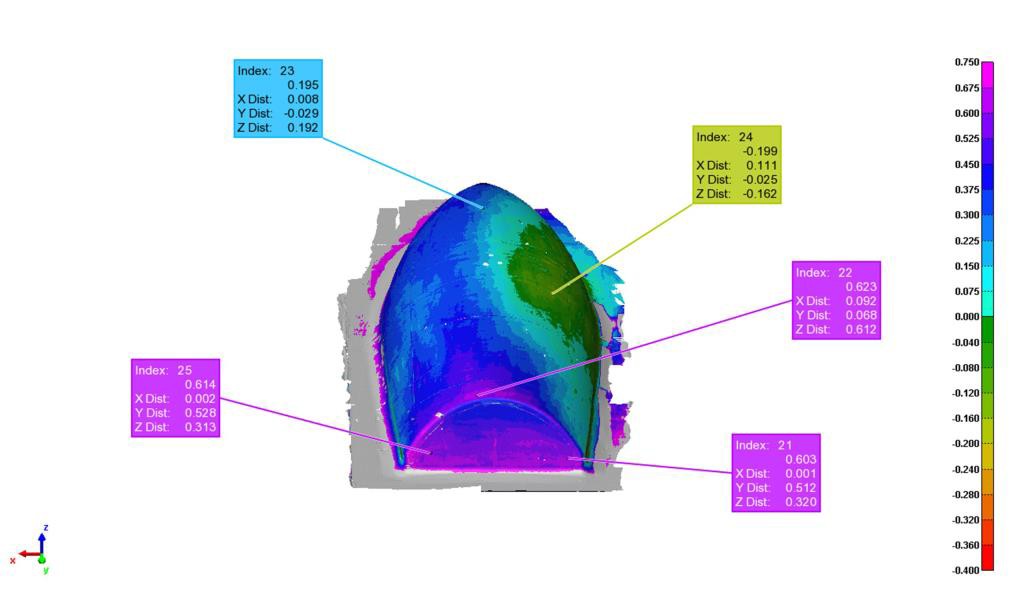
Рисунок 13. Анализ отклонений с использованием координатно-измерительной машины (CMM), при сравнении мастер-модели до и после отверждения, вид сзади (данные представлены в мм).
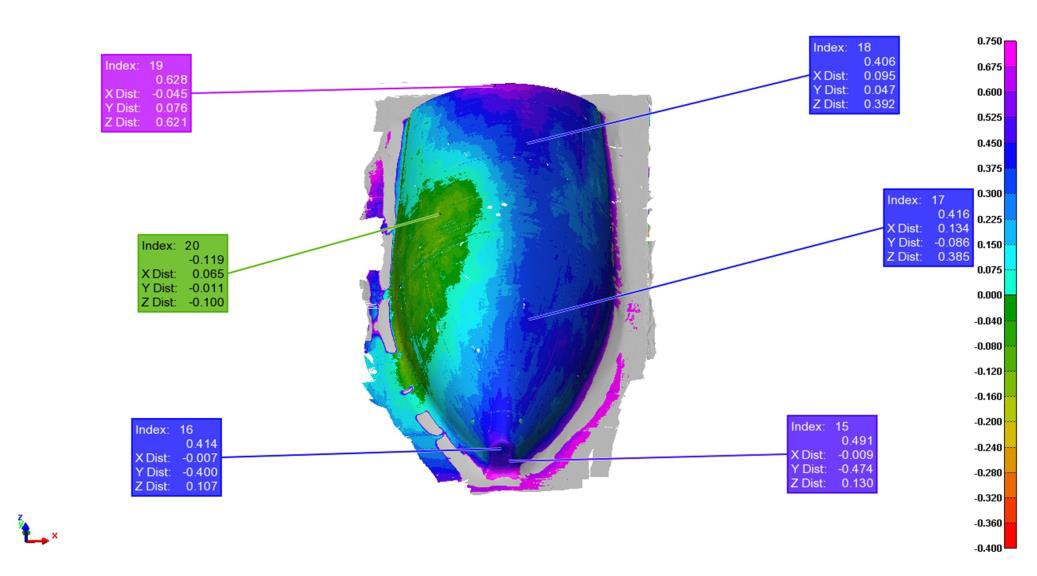
Рисунок 14. Анализ отклонений с использованием координатно-измерительной машины (CMM), при сравнении мастер-модели до и после отверждения, вид спереди (данные представлены в мм).
Изменение размеров после отверждения с использованием NONA-технологии также потенциально может быть вызвано смещением липкой пленки Tooltec во время отверждения с использованием NONA-технологии.
3.4. Использование оснастки
Полученная путем инфузии углеволоконная деталь, отвержденная под действием тепла на второй оснастке, имела гладкую поверхность с небольшой видимой пористостью, проявлявшейся только в небольших отдельных местах, что свидетельствует об отсутствии большой утечки при отверждении детали после инфузии (Рисунок 15).
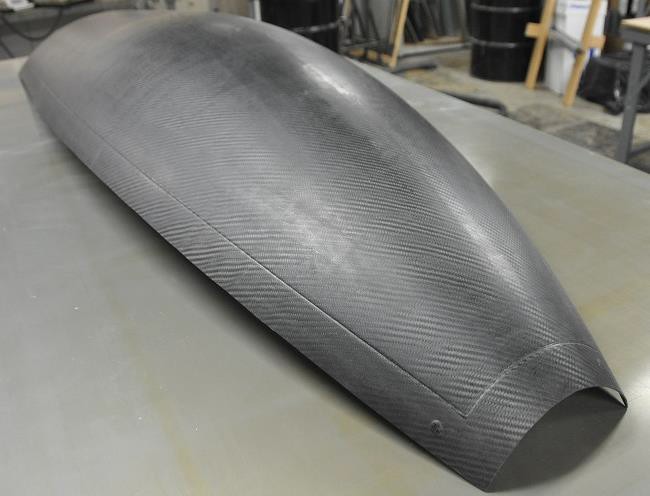
Рисунок 15. Отвержденная, полученная путем инфузии деталь из углеволокна, изготовленная с помощью оснастки при использовании NONA-технологии.
Оснастка была отправлена в Центр космических полётов НАСА им. Маршалла для проведения дальнейших испытаний с использованием автоклава, в котором создавалось давление и происходило нагревание, необходимое для отверждения предварительно пропитанных материалов.
4. Заключение
Проведено успешное изготовление крупногабаритной, обладающей хорошими рабочими характеристиками композитной оснастки при отсутствии внешних источников тепла или давления. Преимуществом этого процесса изготовления являлось также использование дешевого пенополиуретанового инструмента, который легко обрабатывался и был значительно легче мастер-моделей такого же размера, изготовленных из других материалов. Проведено исследование нескольких процессов для определения влияния укладки слоёв, инфузии и изоляции на качество конечной детали, и полученные результаты можно использовать в дальнейших исследовательских работах по изготовлению крупногабаритной композитной оснастки. Полученные в данном исследовании положительные результаты показали возможность изготовления крупногабаритной оснастки и полученных путем инфузии при температуре 177°C деталей, изготовленных с помощью стандартных процессов инфузии.
5. Литература
- Barnell, T., Rauscher, M., Doudican, B., and Sutter, J. «No-oven, no-autoclave processing for NASA composite structures.» SAMPE 2013 Conference Proceedings. Wichita, KS, Oct 2124, 2013. Society for the Advancement of Material and Process Engineering.
- Barnell, T., Rauscher, M., Doudican, B., Karst, G., and Sutter, J. «Evaluation of no-oven, no-autoclave composite manufacturing.» SAMPE 2013 Conference Proceedings. Long Beach, CA, May 6-9, 2013. Society for the Advancement of Material and Process Engineering.
- Barnell, T., Karst, G., Rauscher, M., and Sutter, J. «No-oven, no-autoclave composite tooling.» SAMPE Journal. January/February 2013, Vol. 49, No 1.—pages 48-54.
- Nelson, R. H. and Cairns, D. S., «Prediction of dimensional changes in composite laminates during cure», Proceedings of 34th International SAMPE Symposium, Reno, NV, May 8-11, 1989. pp. 2397-2410.
- Rennick, T.S., and Radford, D.W., «Components of manufacturing distortion in carbon fibre/epoxy angle brackets», Proceedings of 28th International SAMPE Technical Conference, November 4-7, 1996. pp. 189-197.
- Fernlund, G. and Poursartip, A., «The effect of tooling material, cure cycle, and tool surface finish on spring-in of autoclave processed curved composite parts», Proceedings of ICCM12 Conference, Paris, France, July 1999, paper 609, ISBN 2-9514526-2-4.