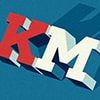
Разработка высокотемпературной технологии производства углеродного волокна с учетом эффективности энергопотребления
рубрика: технологии
В идеальном случае при проектировании высокотемпературной технологии производства таких материалов как углеродное волокно должна учитываться эффективность использования энергии. Однако, хотелось бы определить, что это значит. При анализе благоприятных возможностей, имеющихся при промышленном производстве современных прогрессивных материалов, очень важно установить несколько основополагающих принципов.
Во-первых, при разработке технологий производства прогрессивных материалов очень редко обращают достаточно внимания на необходимость сделать процессы не только функционально простыми и ясными, но и эффективными. В гораздо большей степени внимание разработчиков фокусируется на технических достоинствах производимых материалов, а также на их конечных физических свойствах. Эффективность энергопотребления становится предметом рассмотрения на более поздних этапах разработки технологического процесса, когда остро встает вопрос о стоимости продукции. Технологический путь, первоначально разработанный в исследовательской лаборатории, может даже стать препятствием для обеспечения истинной эффективности процесса при выводе технологии на промышленный уровень.
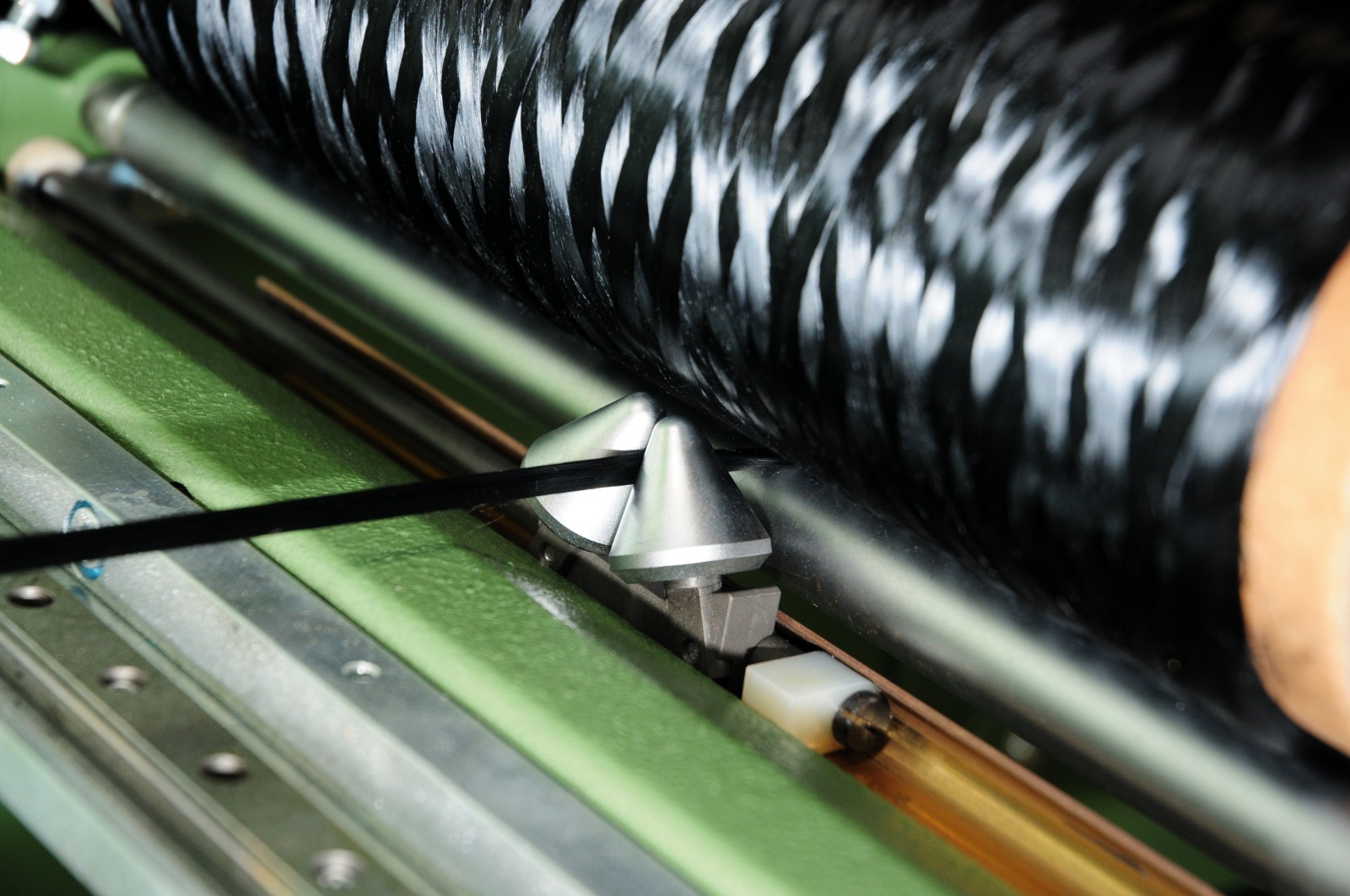
Во-вторых, такие высокотемпературные процессы, как оксидация или карбонизация углеродного волокна, являются печально известными расточителями энергии. Представьте себе процесс ковки стали и плавки алюминия. А теперь учтите, что эти процессы — весьма скромные потребители тепла по сравнению с технологиями, требующими температуры порядка 2000–3000°C — диапазон температур, при которых в настоящее время изготавливаются некоторые наиболее передовые материалы. Проще говоря, обеспечение условий проведения высокотемпературных реакций требует затрат энергии; при этом необходимы средства для надежной поддержки рабочих температур, а также для предотвращения потерь энергии. Это вечная проблема. Возможности для увеличения эффективности процесса имеются, но часто это отражается на стоимости продукции и требует определенных жертв.
Объемы производства:
от крошечных количеств до тонн
Путь от начала создания технологического процесса (на испытательных стендах) до широкомасштабного промышленного производства труден и тернист. Для этого, прежде всего, необходимо увеличить масштаб технологии, разработанной в лабораторных условиях. Как правило, первый шаг перехода к энергетически эффективной технологии совершается при скачке от миниатюрного лабораторного процесса к непрерывному производственному. На каждом последующим шаге наращивания масштабов производства обязательно ставится цель включения в процесс средств сохранения энергии и минимизации ее потерь при поддержании на прежнем уровне свойств материалов.
Обычно технологии изготовления современных перспективных материалов разрабатываются в лабораториях промышленных компаний или исследовательских институтов. При этом всё внимание разработчиков сосредотачивается, как правило, на качестве продукции; в случае углеродного волокна это особенно критично. Цель работы при этом заключается в обеспечении функциональных характеристик продукции: прочности, твердости поверхности, тепло- и электропроводности. Причем часто именно исследование способов достижения этих необходимых свойств финансируется различными грантами и фондами поддержки научных исследований. Основная причина, по которой необходимо обеспечить целевые свойства, заключается в последующем применении продукции: качество продукции должно быть как можно выше, независимо от того, предназначен ли материал для гражданских или оборонных целей.
Процесс разработки прогрессивных материалов часто определяется имеющимся в распоряжении исследователей лабораторным оборудованием. Обычно в лабораториях используется испытательное оборудование гораздо более скромного масштаба, чем тот, который характерен для оборудования, рассчитанного на производство товара отдельными партиями. На начальном этапе время и энергоресурсы, необходимые для выполнения процесса изготовления материала, совсем не соответствуют времени и энергоресурсам, характерным для полностью разработанной и отлаженной высокоэффективной промышленной технологии.
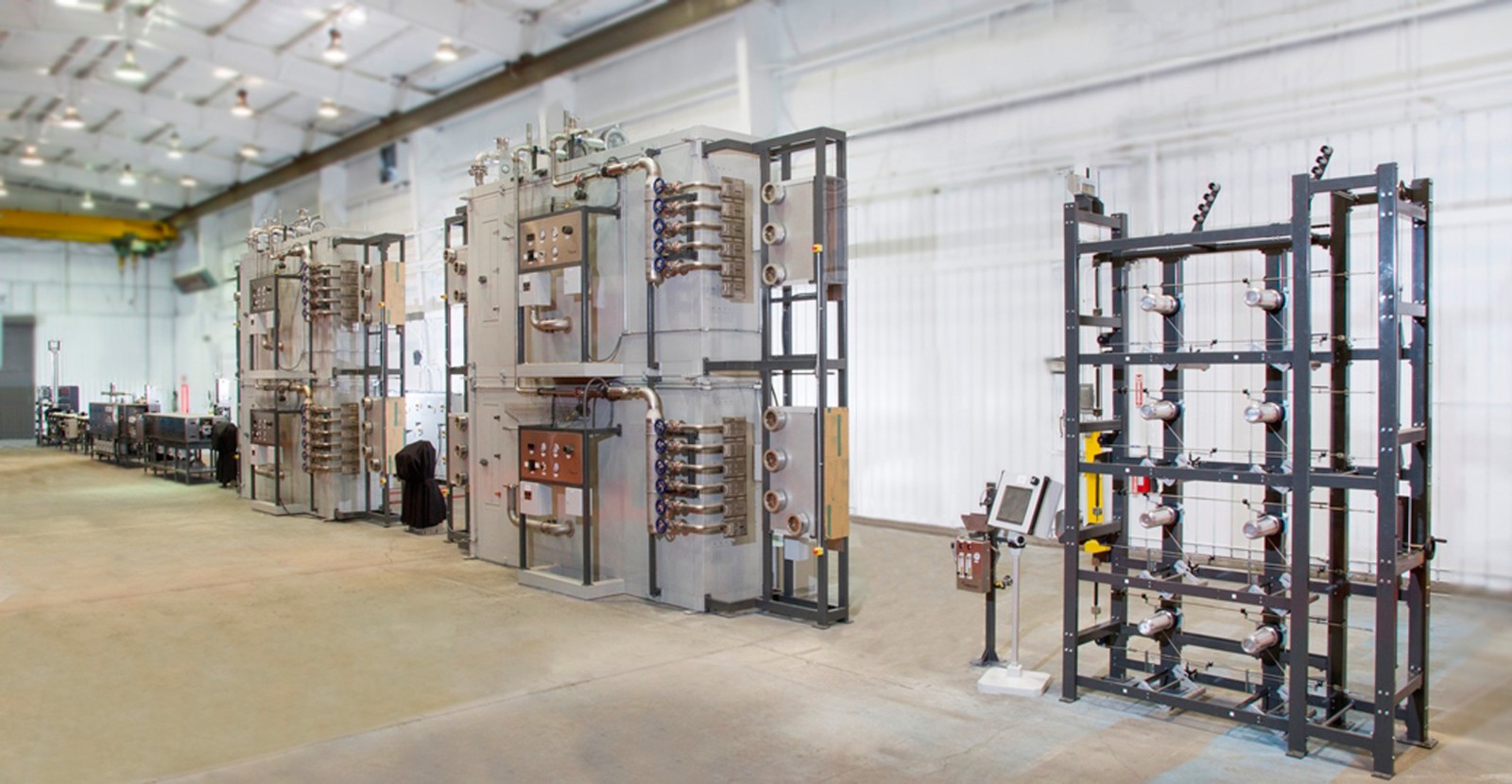
По мере увеличения масштабов производства все большую роль в обеспечении эффективности реакций играет наличие возможности нагревать и охлаждать массу материала, а также возможности вводить газы в твердые материалы или, наоборот, удалять их. Часто именно эти факторы особенно важны при определении скорости реакции преобразования и, соответственно, объема выхода продукции и эффективности технологического процесса. Нередко именно за счет этих факторов возникают технологические ограничения, из-за которых увеличивается общее время обработки материала, что, в свою очередь, влияет как на выход продукции, так и на общий объем энергопотребления в производственном процессе.
С точки зрения эффективности использования энергии, производство товара отдельными партиями оказывается в невыгодном положении. Особенно сильно снижает эффективность энергопотребления необходимость нагревания и охлаждения всей массы продукции, корпусов реакторов, конструктивных и огнеупорных элементов. В тех случаях, когда требуются особенно высокие температуры и большие скорости нагревания/охлаждения, например, при графитизации углеродного волокна, возможно применение водяного охлаждения оборудования; при этом качество работы оборудования повышается, а вот эффективность энергопотребления существенно падает.
Широкомасштабное производство
Наиболее эффективны тепловые процессы, которые разработаны для случаев нагревания и охлаждения минимально возможных объемов материала. В идеале это означает, что обработка веществ, участвующих в реакции, ведется непрерывным способом, без заключения материала в контейнеры. Возможна разработка таких непрерывных технологических процессов, в которых для повышения эффективности нагревания материала и сведения к минимуму необходимого для этого количества энергии (чтобы оно не выходило за минимум технологического энергопотребления) будет использоваться подбор оптимальной скорости перемещения материала и профилей изменения температуры. Расширение возможностей управления выходом производственного процесса предполагает такие решения, которые обеспечивают минимизацию температурных градиентов загруженного материала с целью максимального усиления взаимодействия между газообразными и твердыми веществами и интенсификации обновления запасов газов.
Кроме того, эффективность термических процессов можно повысить с помощью соответствующего выбора огнеупорных элементов и их конструктивных особенностей. В системах, рассчитанных на производство товара отдельными партиями, конструкция огнеупорных элементов должна учитывать необходимость временного содержания материала в контейнерах при определенной температуре и требования к оптимальной скорости нагревания и охлаждения. Если подобрать удачную конструкцию огнеупорных элементов, то можно найти лучшее решение по экономии энергоресурсов и скорости подъема и снижения температуры; однако при этом время охлаждения увеличивается и, соответственно, увеличивается общая продолжительность производственного цикла. При менее удачных конструкциях скорость охлаждения может быть более оптимальной, но эффективность энергопотребления при этом снижается; кроме того, при этом приходится учитывать другие ограничения, например, ограничения на температуру корпусов. С другой стороны, при использовании водяного охлаждения оборудования можно подобрать оптимальную скорость охлаждения и свести к минимуму требования к габаритным и весовым параметрам огнеупорных элементов, но требования к эффективности энергопотребления в этом случае практически игнорируются.
В то же время, в непрерывных производственных процессах этапы нагревания, выдержки и охлаждения пространственно разделены. Поэтому, оптимизации процесса управления температурой и выполнения требований к эффективности процесса на каждой из его стадий можно добиться, установив по длине печи огнеупорные элементы различной конструкции. Кроме того, поскольку огнеупорные элементы изначально нагреты, а затем все время подвергаются воздействию температуры, можно использовать гораздо более подходящую конструкцию огнеупоров, которая обеспечивает более высокую продуктивность независимо от потерь эффективности, которые могут произойти на этапах нагревания и охлаждения в печи, рассчитанной на производство товара отдельными партиями.
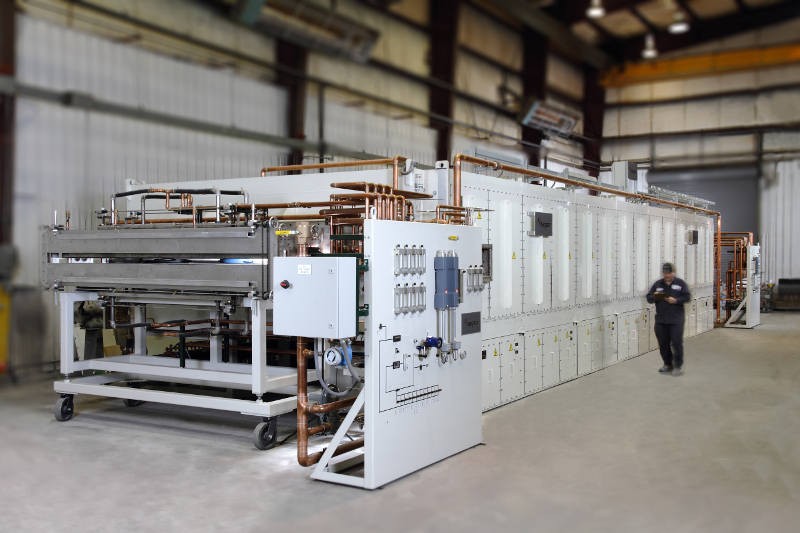
Источник: Harper International
Потери тепла, определяемые конструкцией выходных устройств, также очень отличаются друг от друга при производстве отдельными партиями и при непрерывном производстве; этот фактор имеет особенно большое значение при энергозатратных технологиях обработки углеродного волокна. Одна из основных проблем состоит в том, что возможности утилизации отходящего тепла на выходе печи при производстве партиями весьма ограничены. Поскольку в таких установках отходящее тепло практически соответствует температуре материала при загрузке, внести значение температуры непосредственно в процесс невозможно. Имеющиеся возможности сводятся или к образованию сложных связей между многочисленными элементами оборудования, каждый из которых принадлежит к различным частям технологического маршрута, или к использованию теплообменников, с помощью которых можно передавать тепло на другие технологические линии, расположенные в различных производственных помещениях.
В случае же непрерывного технологического процесса, напротив, имеется целый ряд возможностей для регенерации и утилизации тепла. Первая из них — применение газового потока внутри системы для увеличения утилизации тепла в ходе изготовления углеродного волокна; встречный поток газа, поступая в технологическую линию, обеспечивает дополнительное охлаждение продукции и впоследствии, после выхода из печи, участвует в предварительном прогреве поступающих материалов. Кроме того, благодаря своему участию в реакции направленный технологический поток газа делает состав газа в определенных точках печи более предсказуемым. В тех случаях, когда скоростью реакции можно управлять (непосредственно через химический состав поступающего в систему газа или путем удаления газообразных продуктов), естественно, можно минимизировать потребление газа и, следовательно, потери тепла, связанные с использованием газа. В системах производства отдельными партиями потоки нельзя контролировать достаточно точно, и поэтому для достижения заданной производительности технологического процесса могут потребоваться гораздо более высокие скорости циркуляции газа.
При улучшенной конструкции оборудования возможность утилизации тепла, исходящего от носителей продукта, можно дополнительно использовать для минимизации их влияния на эффективность работы систем. Существует уникальная конструкция, при которой можно даже организовать потоки материалов таким образом, чтобы материалы на выходе охлаждались благодаря близости к холодным входящим реагентам, которые при этом подвергаются предварительному прогреву.
В процессе обработки определенных видов материалов, в том числе углеродного волокна, в отработанных газах могут содержаться отходы материалов, обладающие энергетическим потенциалом. Например, обработка материалов с целью удаления из них растворителей или масла, как и термическая обработка с целью удаления органических присадок или связующих веществ, может привести к образованию таких сбросных потоков, что, если конструкция оборудования позволяет, можно извлечь пользу из их энергетического потенциала путем их сжигания и использования образующегося тепла в основном технологическом процессе для предварительного прогрева. В некоторых конкретных случаях значительная часть общего термического потенциала технологического процесса способствует значительному росту эффективности энергопотребления и, в связи с этим, снижению стоимости продукции, ровно как и снижению количества экологических проблем благодаря уменьшению потока отработанных газов.
Следует отметить, что непрерывный технологический процесс специально организован таким образом, чтобы извлечь максимальную пользу из возможности утилизации энергии. При производстве отдельными партиями отработанные газы, имеющие энергетический потенциал, образуются только на определенном этапе производственного цикла. Таким образом, соответствующий источник энергии доступен только на определенном этапе технологического процесса, и стоимость его инкорпорации может быть выше установленной. С другой стороны, при непрерывном производстве поток отработанного газа формируется на определенном этапе процесса постоянно и стабильно. В то же время, в линию постоянно вводятся новые холодные материалы, которые необходимо прогревать до температуры реакции; при этом система может находиться в равновесии и работать устойчиво, эффективно используя весь поток отработанных газов.
Образцовая модель: углеродное волокно
Технология переработки полимерного волокна в углеродное была спроектирована по образцу ранее разработанных схем. Углеродное волокно является перспективным современным материалом, однако оно было предметом исследований со времен Томаса Эдисона. Первая попытка изготовить углеродное волокно в промышленных масштабах была предпринята в начале семидесятых годов прошлого века. Первая установка для соответствующей конверсии была менее 1000 мм шириной и выдавала порции продукции менее 100 раз в год. В этой системе производство волокна обходилось более чем в 150–200 кВт·час на килограмм изготовленного углеродного волокна.
В результате последовательной работы по приближению масштабов производства к промышленным современная установка для изготовления углеродного волокна имеет ширину порядка 3000–4200 мм. Производительность одной установки в настоящее время достигает 2500 тонн в год. Также, благодаря увеличению использования отработанной энергии в технологическом процессе, усовершенствованию оборудования, выражающемуся в экономичных размерах и более прогрессивной конструкции огнеупорных элементов, и улучшению качества основного сырья (т.е., применению полимеров с лучшей способностью конвертироваться в углеродное волокно), потребление энергии не превышает 20 кВт·час на килограмм готового углеродного волокна.
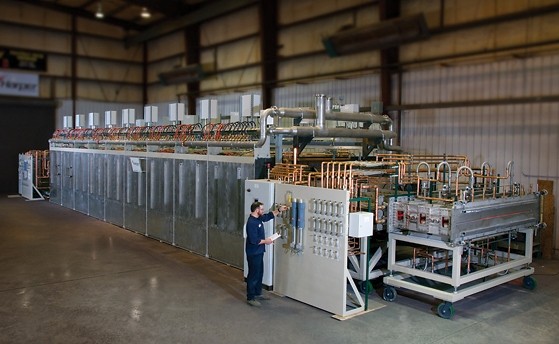
Источник: Harper International
Термический процесс производства углеродного волокна во многих отношениях повторяет оптимальную модель, которую можно использовать так же как руководство для повышения эффективности других термических процессов. В частности, производство углеродного волокна на основе полиакрилонитрила осуществляется в полностью бесконтейнерном режиме; движущая сила транспортировки продукции от одного этапа технологической линии к другому обеспечивается самим волокном. При этом, благодаря исключению необходимости прогрева вспомогательного оборудования, технологический процесс обладает всеми преимуществами эффективного энергопотребления непрерывной технологии и прочих усовершенствований, повышающих производительность. В качестве фактора снижения эффективности системы можно назвать только потери тепла, связанные с использованием буферного газа для поддержания необходимого состава и давления атмосферы. Методы снижения атмосферных потерь путем улучшения герметичности печи в настоящее время находятся в стадии разработки.
Компания Harper International уверенно выбрала в качестве средства определения параметров масштабирования такой проверенный способ, как эмпирическое тестирование на демонстрационном (полунепрерывном) уровне. Схема технологии, ориентированной на производство продукции отдельными партиями, может быть определена более точно путем тщательного планирования экспериментов на разнообразных печах, работающих в полунепрерывном и непрерывном режимах. Данные по масштабированию процесса, полученные в ходе таких экспериментов, могут быть использованы для уточнения технологической схемы и определения таких устройств непрерывного действия для коммерческого применения, которые обеспечили бы наилучший баланс между качеством и количеством готовой продукции с одной стороны и эффективностью энергопотребления и снижением производственных расходов с другой стороны.
Статья была опубликована в номере 6 (57) 2014