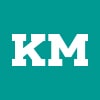
"Труды ВИАМ" №6 (112) 2022
рубрика: наука
Обзор статей по композитной тематике из электронного научного журнала "Труды ВИАМ" №6 (112) 2022
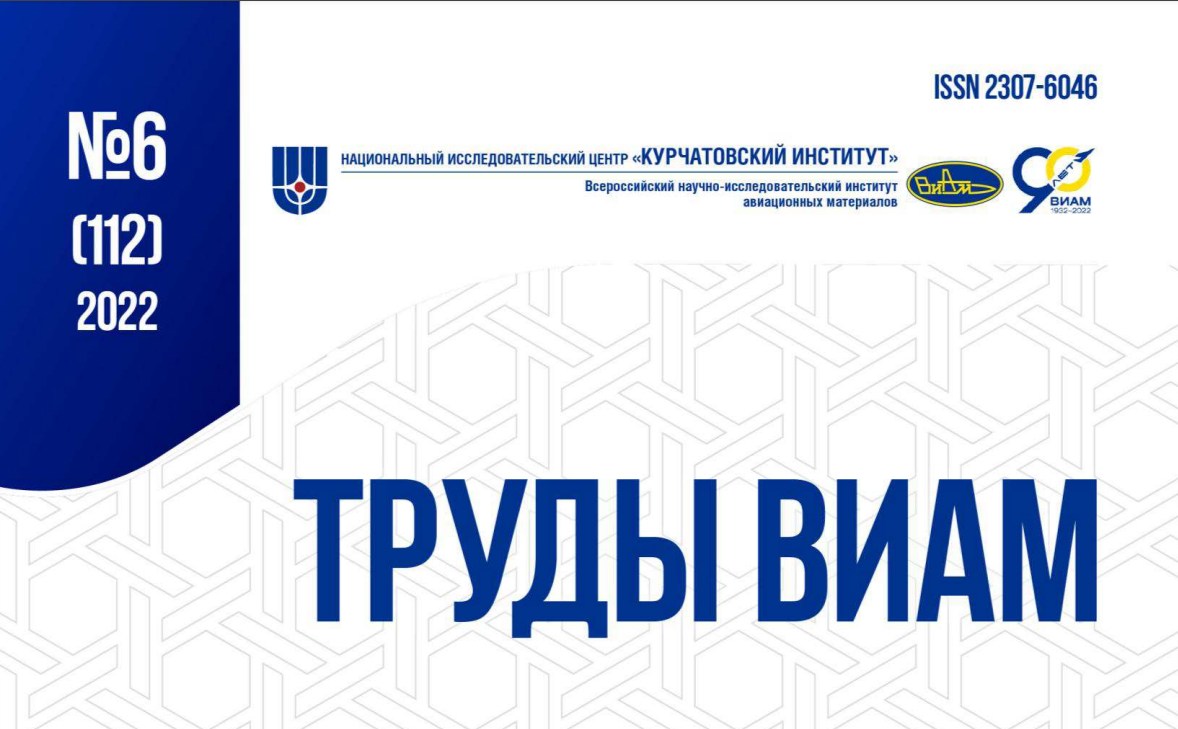
И. Н. Гуляев, А. М. Сафронов, Р. А. Сатдинов
СРАВНЕНИЕ ОНЛАЙН- И ОФЛАЙН-ТЕХНОЛОГИЙ ИЗГОТОВЛЕНИЯ ПРЕПРЕГОВ И СВОЙСТВ УГЛЕПЛАСТИКОВ
Проведено сравнение технологических свойств препрегов, произведенных по онлайн- и офлайн-технологиям, а также физико-механических свойств углепластиков марок ВКУ-29/ВТкУ-3 и ВКУ-39/ВТкУ-2.200 на основе расплавного связующего ВСЭ-1212.Оценены преимущества и недостатки рассматриваемых технологий изготовления препрегов и их влияние на свойства углепластиков. Показано, что различие в технологии получения полуфабрикатов (препрегов) не оказывает влияния на конечные свойства углепластиков, изготовленных автоклавным формованием.
В настоящее время во всех отраслях промышленности, в том числе и в авиационной, наблюдается увеличение спроса на полимерные композиционные материалы (ПКМ), в которых комплекс высоких прочностных, диэлектрических и теплофизических характеристик хорошо сочетается с экономической эффективностью их использования. Современные ПКМ изготавливают на основе различных наполнителей: стеклопластики – на основе стеклянных, органопластики – на основе арамидных, углепластики – на основе углеродных. Новейшие ПКМ отвечают все возрастающим требованиям к уровню упруго-прочностных характеристик и эксплуатационной стабильности, обеспечивающих работоспособность конструкций, и современным экологическим требованиям к технологиям переработки.
Ранее для изготовления препрегов использовали растворную технологию, т. е. пропитку осуществляли путем протяжки армирующего наполнителя через раствор связующего в легко удаляемых растворителях типа ацетона или спирто-ацетоновой смеси с последующим их удалением в сушильной камере. При этом в атмосферу выбрасывалось большое количество вредных веществ. Несмотря на сушку при повышенной температуре, в препрегах, изготовленных по растворной технологии, содержится значительное количество летучих веществ, наличие которых при условии их неудаления в процессе формования может привести к существенным отклонениям от регламентируемых физико-механических свойств в ПКМ. Наличие летучих веществ в составе препрега затрудняет определение массовой доли связующего в процессе пропитки, что приводит к существенному его отклонению от заданного содержания. Кроме того, использование растворной технологии изготовления препрегов делает невозможным применение в составе связующих термопластичных добавок и модификаторов, что также негативно сказывается на деформационных свойствах ПКМ и стойкости их к растрескиванию [6–10].
Применение расплавных связующих при изготовлении препрегов позволяет избежать указанных недостатков. Полимерное связующее в расплавленном состоянии путем каландрования совмещается с армирующим наполнителем непосредственно в пропиточной машине. При этом расплав практически не содержит летучих веществ. Содержание связующего можно регулировать зазорами между валками пропиточных машин, на которых изготавливают препреги, что обеспечивает снижение разброса по содержанию связующего в препреге в пределах ±2 %. Отсутствие растворителя и равномерность наноса связующего положительно влияют на свойства материалов при изготовлении в дальнейшем изделий из ПКМ. Кроме того, по указанной технологии можно изготавливать препреги на основе однонаправленных жгутов, что невозможно сделать при использовании растворных пропиточных машин [11–15].
Создание ПКМ нового поколения требует решения ряда задач: от разработки термостойких связующих, позволяющих создавать ПКМ с повышенной (до 400 °С) рабочей температурой, и производства современных волокнистых стеклянных и углеродных тканых наполнителей различной текстильной формы, обеспечивающих получение требуемых прочностных характеристик, до разработки технологии их совмещения для получения полуфабриката и/или формирования композиционных материалов [16].
Расширение области применения ПКМ и увеличение объемов их потребления требуют совершенствования технологий изготовления препрегов, в том числе направленного на сокращение времени их производства, при этом обеспечивая получение полуфабрикатов со стабильными свойствами, что в конечном итоге должно привести к снижению стоимости готовых изделий [17].
Производство препрегов по расплавной технологии осуществляется как непрерывно при одновременном изготовлении пленки связующего и совмещении в каландрах (онлайн-технология), так и в раздельных процессах формирования пленки связующего на отдельном узле нанесения пленок (коутере) и последующего совмещения ее в пропиточной машине с армирующем наполнителем (офлайн-технология).
К. И. Донецкий, М. Н. Усачева, А. В. Хрульков
МЕТОДЫ ИНФУЗИИ ДЛЯ ИЗГОТОВЛЕНИЯ ПОЛИМЕРНЫХ КОМПОЗИЦИОННЫХ МАТЕРИАЛОВ (обзор). Часть 1
В настоящее время полимерные композиционные материалы (ПКМ) широко применяют вместо таких традиционных материалов, как сталь или дерево. Для крупногабаритных деталей из ПКМ процесс инфузии становится наиболее востребованным и часто используемым. По этой технологии изготавливают корпуса кораблей, лопасти ветроэнергетических установок, крылья самолетов. Цель данного обзора – рассмотрение различных видов инфузии, их достоинств, недостатков и перспектив применения.
Многообразие конструкторских решений и требований по эксплуатации оборудования вызывает у технологов стремление усовершенствовать технологию инфузии и осуществлять разработку различных модификаций и усовершенствованных вариантов данного процесса.
В настоящее время полимерные композиционные материалы (ПКМ) все чаще применяют вместо таких традиционных материалов, как сталь или дерево. В НИЦ «Курчатовский институт» – ВИАМ разработана целая серия материалов для авиационной промышленности (изготавливают детали для планеров самолета и двигателей), исследованы их свойства, проведены испытания в различных климатических зонах [1–6]. Одной из основных тенденций при этом является стремление отказаться от автоклавной технологии, которую сейчас успешно применяют в авиационной промышленности, и перейти к безавтоклавной, открывающей широкие возможности при изготовлении крупногабаритных деталей недорогостоящим способом [7, 8].
В авиационной промышленности процесс инфузии применяют при изготовлении деталей крыла таких самолетов, как Bombardier CSeries (в настоящее время Airbus A220) и МС-21 [9]. В судостроение и производство лопастей ветроэнергетических установок данный процесс также внедрен для изготовления крупных конструкционных композитных деталей [10, 11]. Использование технологии пропитки преформ жидкой смолой, с одной стороны, обеспечивает требуемое качество наполнителя в будущем композиционном материале, а с другой стороны, дает возможность отказаться от дорогостоящего процесса автоклавной технологии. Следует также отметить, что компания «Юматекс» запустила в 2021 г. завод по производству ПАН-прекурсора, что позволяет использовать при производстве композитных конструкций отечественные наполнители, тем самым снижая зависимость от импортных компонентов [12]. Многие исследователи и компании занимаются усовершенствованием технологии инфузии. В научно-технической литературе и патентных источниках рассматривается большое количество инфузионных методов, которые составляют подгруппу группы Liquid Composite Molding [13].
М. Н. Усачева, А. В. Хрульков
БИОДЕГРАДАЦИЯ АРМИРОВАННЫХ ПОЛИМЕРНЫХ КОМПОЗИЦИОННЫХ МАТЕРИАЛОВ (обзор)
Рассматривается биологическое повреждение термопластичных и термореактивных армированных полимерных композиционных материалов (ПКМ), углеродных и стеклянных волокон и смол микроорганизмами и грибами. Показано, что биодеградация влияет на структурную целостность материала, его физические и механические свойства. Рассмотрены условия благоприятного развития микроорганизмов, механизм биодеградации, некоторые виды бактерий и грибов, поражающие ПКМ, и механизмы образования биопленок.
Армированные волокном полимерные композиционные материалы (ПКМ) находят широкое применение в транспортной, медицинской, авиационной и космической промышленности [1–7]. Композиционные материалы имеют двухфазную структуру: армирующее волокно и основу – матрицу из смолы. Большое количество волокон содержится в единице объема армированного ПКМ в качестве средства увеличения прочности материала, так как именно волокно определяет данный показатель.
Структурная целостность композиционного материала является ключом к его долговечности и отличным характеристикам. Ряд факторов может влиять на целостность ПКМ, включая адгезию между волокном и матрицей, распределение и ориентацию волокон и реакцию каждого его компонента на условия окружающей среды, в том числе на влажность и температуру. Несовершенство одного компонента композита или локальное разделение компонентов могут вызывать прогрессирующее расслоение, отслоение или отделение волокон от матриц, что приводит к снижению прочности и жесткости. К таким факторам относят структурные дефекты: ослабление межфазных связей между волокнами и матрицей, расслоение и разделение компонентов [8].
Предполагается, что биологическое повреждение композиционных материалов может существенно повлиять на их структурную целостность, физические и механические характеристики. Поскольку в составе ПКМ есть несколько химически и физически различных компонентов, локальные химические изменения, возникающие в результате роста и метаболизма микроорганизмов, ускоряют повреждение составных компонентов. На поверхности или в пустотах в ПКМ могут концентрироваться питательные вещества, создавая благоприятную среду для развития микроорганизмов. Волокна могут служить капиллярами для улучшения движения и распределения влаги и химических веществ внутри ПКМ, а также увеличивают распространение микроорганизмов внутри структуры [9].
К сожалению, изучению биологической деградации армированных ПКМ уделяется мало внимания. Ранее считали, что ПКМ, как и пластмассы, устойчивы к разрушению микроорганизмами, поскольку материалы не могли их обеспечить необходимыми питательными веществами [10]. Однако материалы, которые являются биологически инертными или для которых требуется длительный период разрушения, могут быть восприимчивы к механизмам разрушения, вызванным биологической активностью микроорганизмов. Например, длительное время полагали, что корпуса лодок, выполненные из стеклопластика, не подвержены коррозии, биообрастанию или деградации, характерным для обычных материалов. Однако в настоящее время признано, что на всех инженерных материалах колонизируются микроорганизмы, включая бактерии, в течение нескольких часов после нахождения в природных водах [11]. Биодеградации подвержены материалы, из которых изготовлены корабли, самолеты, канализационные трубы, медицинские изделия и космические станции.
Очень мало известно о биодеградации синтетических полимерных материалов, поскольку они не так давно стали широко распространены и к тому же достаточно медленно деградируют в природных условиях. Различия в углеродных цепях, конформациях и стереохимии у материалов указывают и на большие их различия в биодеградации. Высокая молекулярная масса приводит к снижению растворимости, что является неблагоприятным фактором для атаки микроорганизмов, так как для бактерии необходимо, чтобы субстрат (материала) ассимилировался через клеточную мембрану и затем разложился под действием клеточных ферментов. Во время разложения ферменты микроорганизмов разрушают длинные полимерные цепочки, образуя более короткие – олигомеры, димеры и мономеры, которые достаточно небольшие, чтобы пройти через мембрану бактерии и использоваться в качестве источника углерода и энергии [12].
Флемминг обнаружил, что материалы не обязательно должны легко распределять и накапливать влагу и быть полностью заселены микроорганизмами, чтобы деструктировать под их воздействием и удовлетворять потребность в питательных веществах [13]. В ходе жизнедеятельности микроорганизмы выделяют ряд экзоферментов, которые взаимодействуют с материалом, тем самым разрушая его [14]. Деградация ПКМ под воздействием внешних и биологических факторов делает более доступными те фракции материала, которые изначально не были «легкодоступными» для микроорганизмов. На этой стадии развивается биопленка, ускоряющая процесс биодеградации [15].
Биологическое повреждение композиционного материала может значительно повлиять на его физическую целостность и усталостные характеристики. Поскольку существует несколько химически и физически разных компонентов в его составе, локализованные химические изменения, возникающие в результате роста и метаболизма микроорганизмов, способствуют ускорению повреждения отдельных компонентов. В определенных местах или пустотах в армированных ПКМ могут концентрироваться питательные вещества, обеспечивая создание благоприятной среды для развития микробов. Микробная активность и продукты их жизнедеятельности, в свою очередь, увеличивают повреждение материалов. Волокна проводят влагу и химические вещества внутри ПКМ и способствуют распространению бактерий и грибов внутри структуры. Незначительные химические изменения в локализованных областях могут резко снизить эксплуатационные характеристики материала и ослабить физические свойства композита [16].
Способность полимеров подвергаться биоразрушению существенно зависит от условий эксплуатации ПКМ. Возникновение и развитие микроорганизмов и грибов определяется множеством факторов внешней среды: температурой, кислотностью, влажностью, наличием света, степенью аэробного состояния и давлением. Микроорганизмы и грибы более интенсивно разрушают материалы и изделия в регионах с относительно высокой температурой воздуха, повышенной влажностью и большим количеством органической пыли (тропики и субтропики) [17].
На ПКМ неблагоприятно воздействуют анаэробные, аэробные бактерии и грибы. После аэробного воздействия полимер разлагается на CO2, H2O и микробные биомассы; после анаэробного – на органические кислоты, CO2, CH4 и микробные биомассы [12]. Микроорганизмы растут и образуют биопленку. Окружающая среда на границе раздела «биопленка–материал» радикально отличается от основной среды с точки зрения pH, содержания кислорода, а также органических и неорганических веществ [18]. Более того, ПКМ подвержены разложению из-за проникновения влаги и осмотического образования пузырей, несмотря на то, что данные факторы изучены и могут быть устранены с помощью надлежащих процедур производства и обслуживания [19].
М. И. Валуева, И. В. Зеленина, А. В. Начаркина, К. Р. Ахмадиева
ТЕХНОЛОГИЧЕСКИЕ ОСОБЕННОСТИ ПОЛУЧЕНИЯ ВЫСОКОТЕМПЕРАТУРНЫХ ПОЛИИМИДНЫХ УГЛЕПЛАСТИКОВ. ЗАРУБЕЖНЫЙ ОПЫТ (обзор)
Представлен обзор научно-технической информации в области технологических особенностей процесса получения высокотемпературных углепластиков на основе термореактивных полиимидных связующих. Приведены параметры формования и проведен их сравнительный анализ, области применения и рекомендуемые температуры эксплуатации высокотемпературных полиимидных углепластиков, разработанных и выпускаемых зарубежными компаниями, продукция которых успешно внедрена на практике в элементы конструкций изделий авиационно-космической техники.
Создание перспективной техники основано на применении лучших достижений современного материаловедения – как в области самих материалов, так и технологических решений. В настоящее время сложно представить себе изделия, в которых не применялись бы полимерные композиционные материалы (ПКМ), позволяющие повысить весовую эффективность конструкций при обеспечении необходимых прочностных и функциональных характеристик. Благодаря высокой прочности, низкой плотности, химической и термической стойкости одну из ведущих позиций занимают углепластики [1–3].
Температура эксплуатации ПКМ определяется выбранным типом полимерного связующего и для стандартных высокопрочных углепластиков может достигать 180 °С. Однако для решения задач высокотемпературного применения ПКМ, в частности, углепластики должны обладать повышенной термоокислительной стабильностью, обеспечивающей максимальный уровень сохранения свойств при воздействии повышенных температур, величина которых определяется назначением конструкции и может составлять от 200 до 400 °С [4–13].
Одной из основных областей применения высокотемпературных материалов в мировой практике является авиационно-космическая отрасль. В том числе на европейском рынке рост спроса на высокотемпературные ПКМ стимулируют компании Dassault Aviation, BAE Systems, Airbus Group. Производителями различных классов связующих для высокотемпературных ПКМ за рубежом являются компании Cytec Solvay Group, Toray Advanced Composites, Hexcel Corporation, Renegade Materials Corporation, Teijin, Evonik, UBE Industries Ltd, Nexam Chemical [14].
В данной статье представлен обзор научно-технической информации в области технологических параметров процесса получения углепластиков на основе высокотемпературных термореактивных полиимидных связующих. Полиимидные материалы в дополнение к устойчивости к воздействию повышенных температур (250–320 °С) характеризуются высоким значением кислородного индекса, обладают пожаробезопасностью и радиационной стойкостью, что делает их перспективными материалами для применения в конструкциях изделий космической техники, судостроении и др. [11–13].