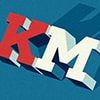
Ещё раз о монолитности конструкций из полимерных композиционных материалов
рубрика: наука
Изменяемость свойств композиционных материалов при длительном воздействии эксплуатационных нагрузок — факт известный, а потому представление о том, как долго материал сохранит характеристики прочности и жесткости, достигнутые в изготовленном изделии, для конструктора крайне важно.
В готовой конструкции прочность, жёсткость и долговечность композиционного материала определяется технологической предысторией его создания, а их изменение в процессе нагружения оказывается следствием протекания процессов повреждения, особенно при наличии длительной циклической составляющей в нагрузке [1].

Источник: www.sdcolortechs.com
В силу физико-механических особенностей и условий работы в армированном пластике чаще всего в первую очередь исчерпываются линейно-упругие свойства связующего. Поэтому в минимеханике процессов разрушения полимерного композиционного материала (ПКМ) для связующего устанавливается критерий начальной линейности, по которому можно определить пределы нагрузок, обеспечивающих линейную упругую деформацию упругого пластика. Важность его подтверждается экспериментально: комбинация нагрузок, вызывающая только линейную упругую деформацию связующего в армированном пластике, при циклическом нагружении обеспечивает не менее 107 циклов до разрушения [2]. Напомним, что по нормам лётной годности гражданских вертолётов установлено базовое число циклов нагружений для конструкций из стали, равное 2×107, а из алюминиевых и магниевых сплавов — 5×107 циклов.
Существует и критерий монолитности, поскольку монолитность материала — первейшая функция связующего. Ныне уповают на то, что разрушение связующего может и не вызвать разрушения армированного пластика в целом, но важно, что при этом уменьшается его несущая способность из-за неравномерности нагружения волокон и герметичность. Работа армированного пластика, потерявшего монолитность, в условиях циклического нагружения обеспечивает долговечность уже не более 105 циклов. Очевидна потеря, существенная для конструкций летательных аппаратов.
Принято потерю монолитности рассматривать с двух позиций: с позиции разрушения связующего между волокнами или слоями и с позиции разрушения контактного слоя «волокно — связующее». Наш опыт касается разрушения связующего.
Этот опыт свидетельствует о том, что достижение требуемой механической надёжности конструкций ответственного назначения из композитов связано с преодолением дефектов, без которых не обходится поиск бездефектных технологий изготовления таких, часто крупногабаритных изделий. При этом в зависимости от вида, характера и места расположения, величины и степени концентрации дефектов их влияние на качество изделия из ПКМ может быть различным [3].
Первой актуальной проблемой для конструкций типа оболочек является обеспечение заданной геометрической формы и точности стыковочных поверхностей при изготовлении и в процессе хранения изделия. В процессе изготовления таких конструкций методом намотки в структуре материала возникают технологические напряжения (структурные, усадочные, температурные), величина которых зависит от природы связующего, толщины изделия, степени анизотропии упругих и теплофизических характеристик отдельных слоёв материала, температуры отверждения [4]. Превышение технологических напряжений прочности материала в радиальном (трансверсальном) направлении инициирует зарождение и рост межслоевых расслоений, качественно влияющих на свойства материала в дефектных зонах. При этом резко снижается несущая способность оболочки [5].
Опыт изготовления и эксплуатации тонкостенных подкрепленных оболочек диаметром 500 мм из углепластика и стыковочными шпангоутами из углестеклопластика показал, что первоначальная некруглость шпангоута (сразу после снятия с оправки) достигает 1,5 мм. В процессе хранения оболочек отмечено увеличение этого отклонения до 2,15 мм. Это приводит к сложности в стыковке отсеков, особенно если стык должен быть ещё и герметичным. Такое нарушение одного из основных параметров, определяющих качество изделия, является следствием напряженного состояния материала шпангоута.
Подобный дефект для отсеков из ПКМ делает понятие номинального размера весьма условным: истинный размер детали из ПКМ может непрерывно меняться в зависимости от условий и сроков хранения. Это обстоятельство можно учесть точностными расчётами при проектировании изделия, а можно пойти по пути поиска методов и средств размерной компенсации. Именно разработка комплекса технологических приёмов по снижению остаточных напряжений в изделии и исключению негативных последствий этого явления является актуальной задачей для технологов.
Второй проблемой остаётся повышение прочности ПКМ в трансверсальном направлении. Необходимо добиться, чтобы технологические напряжения не превысили прочность полимерной матрицы, целостность её сохранилась, хотя избавиться от остаточных напряжений в готовом изделии нельзя. С целью торможения развития дефектов и повышения общей стойкости материала против коробления и распространения трещин при действии технологических и эксплуатационных нагрузок нами использовались компенсационные способы снижения напряжений и деформаций.
Различают объёмную компенсацию микро- и макроструктурных напряжений в материале и компенсацию локальных напряжений, обусловленных особенностями конструктивного исполнения системы «изделие – технологическая оснастка» и последовательностью этапов процесса изготовления.
С точки зрения простоты технической реализации, для снижения технологических температурных микроструктурных напряжений целесообразно использовать релаксационные свойства ПКМ при охлаждении конструкции от температуры стеклования Тс до конечной температуры Tк. Варьируя температурные условия охлаждения по ступенчато-релаксационному режиму (рис. 1), оказалось возможным добиться снижения этих напряжений [4].
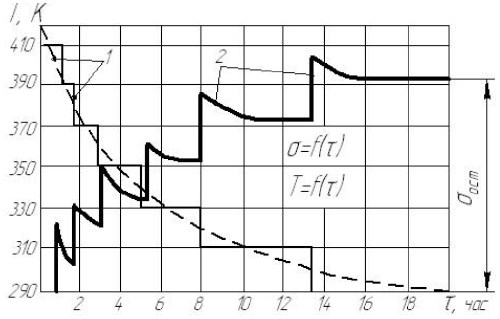
Рис. 1. Ступенчато-релаксационный режим охлаждения изделий из ПКМ: 1 — ступенчатое снижение температуры (пунктирная кривая — аппроксимация температурной зависимости); 2 — изменение микроструктурных температурно-технологических напряжений
Перепад между соседними ступенями температуры назначается из условия, чтобы возрастающие на каждом шаге снижения температуры микроструктурные напряжения не превышали прочность матрицы в данном состоянии. Временной интервал выдержки на каждой ступеньке определяется из условия максимальной релаксации температурных деформаций полимерной матрицы, достигающей при повышенных температурах величины 35%. Опыт конструкторско-технологической отработки намоточных конструкций из ПКМ показал, что для композиционных материалов на эпоксидных связующих шаг снижения температуры должен находиться в пределах 10–20°К, выдержка на каждой ступеньке — в интервале 1,5–3,5 часов. На каждом шаге более высокая скорость охлаждения должна быть при повышенных температурах, а низкая — при температурах, близких к нормальным.
Применение релаксационного способа охлаждения достаточно эффективно и при изготовлении тонкостенных оболочек из материала с резко выраженной анизотропией упругих и теплофизических характеристик в слоях по толщине оболочки. Причем режим релаксационного охлаждения сравнительно легко поддаётся автоматическому регулированию.
Следует отметить, что релаксационный режим охлаждения лишь отодвигает порог трещинообразования в ПКМ с увеличением толщины стенки и скорости охлаждения, но не устраняет его полностью. Поэтому данный способ охлаждения целесообразно использовать как дополнительное средство торможения развития дефектов наряду с применением других способов.
Одним из наиболее успешных путей снижения температурно-технологических напряжений (ТТН) является пластификация полимерной матрицы [7, 8], осуществляемая введением в состав связующего пластификаторов (каучук, дибутилфталат). При этом повышается деформируемость ПКМ при трансверсальном растяжении и межслоевом сдвиге, в связи с чем пластификация целесообразна при изготовлении оболочек с высокими требованиями к монолитности структуры и герметичности. Некоторое снижение жесткости и прочности ПКМ в направлении основного армирования следует отнести к недостаткам этого способа, ограничивающим его применение при изготовлении силовых высоконагруженных конструкций.
Для снижения усадки полимерной матрицы и сближения КЛТР армированных и неармированных слоёв целесообразно использовать наполнение связующего полыми микросферами [9]. Введение в полимерную матрицу 35–40% объёмных стекломикросфер снижает уровень ТТН на 20–30%. Это благоприятно сказывается на повышении монолитности ПКМ, хотя наблюдается снижение жесткостных и прочностных характеристик материала в направлении основного армирования и в трансверсальном направлении. По этой причине наполнение матриц микросферами применимо для изготовления ненагруженных конструкций или в качестве вспомогательного способа снижения ТТН, например, в конструкциях с механическим сшиванием слоёв ПКМ.
Монолитность и герметичность изделий из ПКМ — третья проблема. Регулярное введение по толщине стенки конструкции эластичных (армированных и неармированных) прослоек обеспечивает разбиение толщины на зоны отверждения материала, в которых условия полимеризации оказываются близкими к тем, что характерны для тонкостенной оболочки. Помимо этого, эластичные прослойки существенно повышают эксплуатационную монолитность при воздействии динамических и вибрационных нагрузок, а также герметичность оболочек. В качестве эластичных прослоек возможны резиновые смеси или слои наполнителя, пропитанного высокоэластичным связующим, например, той же химической природы, что и для формирования несущих слоёв, но с повышенным содержанием пластификатора. Основным требованием к эластичным прослойкам является химико-технологическая совместимость со связующим основных слоёв.
Универсальным средством обеспечения монолитности при изготовлении намоточных конструкций практически с любой толщиной стенки оказалось использование в качестве прослоек вспенивающихся (расширяющихся) компенсаторов. С ними гарантированно выполняется условие обеспечения монолитности структуры слоистого материала.
Эффективность работы вспенивающихся компенсаторов на этапе отверждения связующего обеспечивается тем, что деформации в материале, возникающие вследствие химической усадки связующего, компенсируются внутренним давлением в прослойке и её соответствующим расширением.
Суммарно, эффекты компенсации деформаций химической усадки, создания полей сжимающих деформаций в ПКМ за счёт давления вспенивания и повышения деформационных свойств компенсирующих прослоек приводят к значительному снижению остаточных ТТН и, как следствие, к надежному обеспечению технологической и эксплуатационной монолитности оболочек [4]. Способ достаточно системно исследован, его реализация не усложняет традиционной схемы намотки и не требует сложного оборудования.
На рис. 2 приведены значения остаточных температурно-технологических напряжений в стеклопластиковой оболочке на эпоксидном связующем УП-238 с Rвн = 75 мм и толщиной 50 мм без компенсаторов (кривая 1) и с компенсаторами из ПСБ-С (кривая 2).
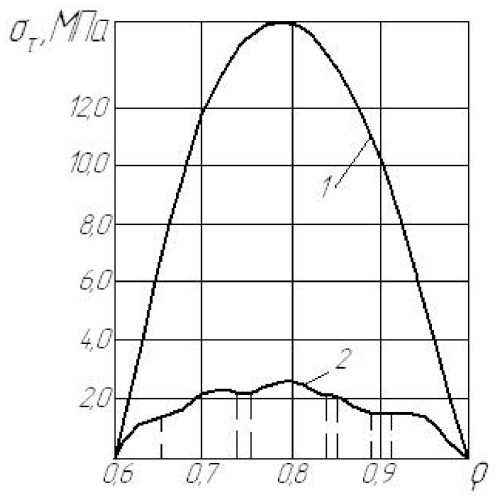
Рис. 2. Пример эффективности действия вспенивающегося компенсатора. Зависимость 1 получена расчетным путем. Изготовить оболочку с указанными параметрами без расслоений оказалось невозможно, однако при введении вспенивающихся компенсаторов монолитность оболочки была обеспечена. В ней остаточные радиальные ТТН уменьшились примерно в 7 раз.
Из рис. 2 видно, что, проектируя изделие с компенсаторами, то есть, выбирая на основе расчётов соответствующий пенополимер и определяя координаты его размещения по толщине в виде прослоек [4], можно обеспечить монолитность конструкции практически при любой толщине стенки.
При использовании компенсационного способа следует контролировать влияние компенсирующих прослоек на прочностные характеристики ПКМ. Результаты испытаний образцов стеклопластика ЭФ-ТС-П методом трёхточечного изгиба (табл. 1) показывают, что введение компенсирующей прослойки в структуру ПКМ незначительно (до 6,2%) снижает его прочность при межслоевом сдвиге. Зато введение в структуру стеклопластика прослойки полистирола ПСВ-С повышает стабильность характеристик ПКМ, в два раза снижая коэффициент вариации. Повышение стабильности значений сдвиговой прочности стеклопластика с компенсирующими прослойками объясняется тем, что полистирол, являясь индифферентным разбавителем эпоксидных смол, формирует морфологически однородную структуру компенсирующей прослойки и тем самым обеспечивает равномерное распределение давления вспенивания в процессе отверждения.
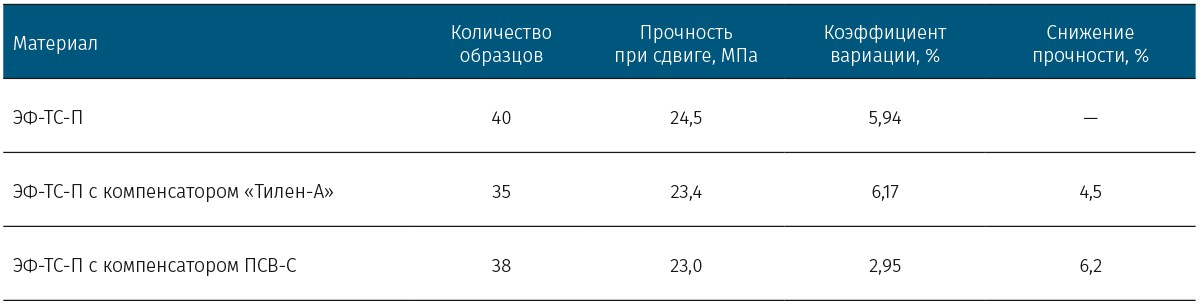
Таблица 1. Сравнительные показателимежслоевой прочности стеклопластика при сдвиге
Таким образом, вспенивающиеся компенсаторы являются наиболее эффективным средством обеспечения монолитности при изготовлении толстостенных намоточных конструкций. Ограничений по толщине стенок наматываемых оболочек в нашей практике не было. Введение этого типа компенсаторов легко поддается регулированию и автоматизации.
Анализ напряженно-деформированного состояния материала тонкостенной обечайки с учетом влияния технологической оснастки (оправки) показал, что одной из причин возникновения недопустимых макродефектов в виде межслоевых расслоений являются локальные ТТН, природа возникновения которых связана с различием температурных деформаций элементов системы «изделие — оправка». Обусловленные различием КЛТР их материалов, эти различия в деформациях достигают значительной величины, особенно при изготовлении крупногабаритных углепластиковых оболочек.
Задача компенсации таких напряжений — очередная по счёту проблема — стала особенно актуальной в связи со стремлением повысить теплостойкость проектируемой конструкции из ПКМ за счёт использования связующих с более высокой температурой отверждения.
Наиболее простым решением такой задачи оказалось применение технологических оправок, материал которых имел коэффициент линейного термического расширения, одинаковый с материалом изготавливаемого изделия. Например, в техническом решении по а. с. 1100112 оправка для изготовления деталей из ПКМ методом намотки была снабжена дополнительной обечайкой из композиционного материала с тем же КЛТР, что и изготавливаемая деталь.
Опыт отработки технологии изготовления конических углепластиковых оболочек показал, что использование оправки из углепластика является надежным средством обеспечения монолитности структуры материала обечайки. При этом, однако, приходится преодолевать сложности демонтажа отверждённого изделия с оправки, из-за отсутствия зазора между ними. К недостаткам таки оправок следует отнести их высокую стоимость, особенно для изготовления крупногабаритных конструкций. Использование таких оправок весьма проблематично для изготовления оболочек, подкрепленных изнутри перекрестным силовым набором.
При изготовлении оболочек, подкреплённых шпангоутами, основным требованием к оправке становится требование минимального воздействия формообразующих элементов оправки на уже отверждённое изделие. Это требование должно реализовываться на этапе охлаждения, поэтому идеальная оправка должна: обеспечить фиксацию геометрических параметров расположения шпангоутов на всех этапах формования и отверждения изделия, не нагружать его на этапе охлаждения и «освобождать» изделие от своего присутствия после охлаждения, не повреждая внутреннее оребрение. Примером такого решения может служить металлическая оправка (рис. 3), в которой формообразующие подкрепляющих шпангоутов элементы размещены в кольцевых пазах оправки и зафиксированы в исходном положении штырями из термопластичного материала, расплавляющегося при максимальной температуре полимеризации.
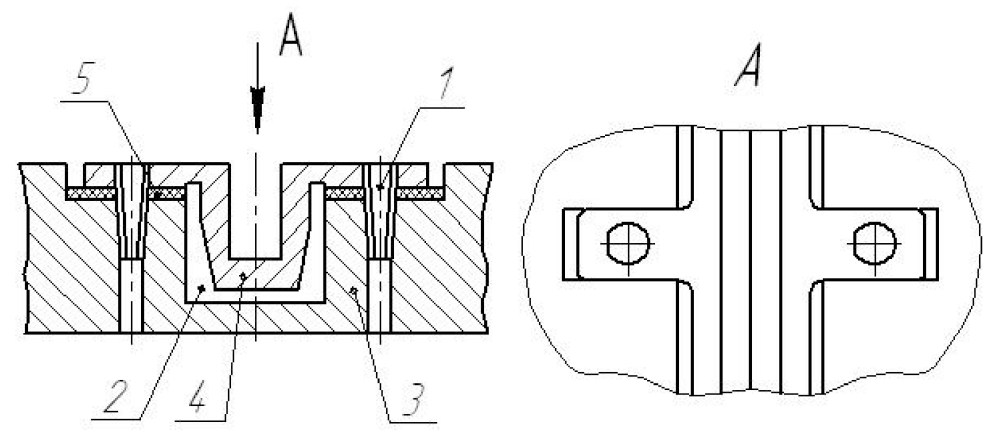
Рис. 3. Фиксация формообразующих элементов оправки с помощью выплавляемых штырей: 1 — фиксирующий штырь из термопластичного материала; 2 — кольцевой паз; 3 — обечайка оправки; 4 — формообразующий элемент; 5 — антифрикционная прокладка
Возможна пара интересных решений проблемы расфиксации формообразующих элементов оправки с кольцевыми рёбрами подкреплённой оболочки. Для этого удобно использовать металлогипсовые оправки.
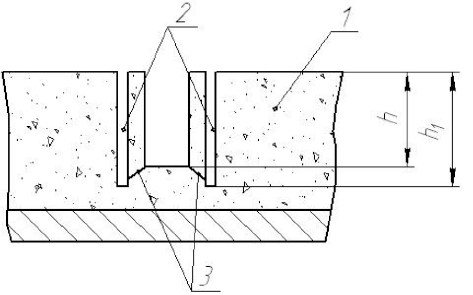
Рис. 4. Предохранительные перемычки в гипсовом слое оправки:1 — гипсовый подслой; 2 — кольцевые компенсирующие прорези; 3 — предохранительные перемычки
В первом используется разница в КЛТР гипса и материала наматываемых шпангоутов (рис. 4). С двух сторон формообразующего паза в оправке прорезают две узких щели глубиной h1 = (1,1−1,2)×h, в результате чего образуются перемычки с расчётной схемой короткой консольной балки под действием поперечного давления, возникающего при намотке шпангоута и усадке гипса на стадии охлаждения. При короткой длине балки нельзя пренебрегать напряжениями поперечного сдвига, поэтому ширина перемычки такова, чтобы исключить разрушение гипса при намотке шпангоута из-за превышения его сдвиговой прочности. На стадии охлаждения гипс разрушается сколом по корневому сечению, освобождая шпангоут.
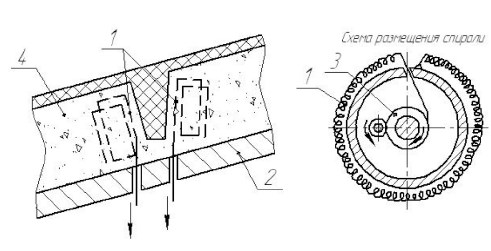
Рис. 5. Вариант принудительной расфиксации подкрепляющего шпангоута: 1 — спираль из проволоки; 2 — обечайка оправки; 3 — привод; 4 — гипсовый подслой
Без особых расчётов можно организовать принудительную расфиксацию разрушением гипса формообразующего шпангоут паза нагрузочными элементами (рис. 5). Нагрузочный элемент представляет собой спираль (лучше прямоугольного профиля), навитую из стальной проволоки. Один конец проволоки прочно закреплён на металлической обечайке оправки, другой пропущен в отверстие обечайки и соединён с приводом силовозбудителя. Размещение элементов в оправке относительно формообразующего паза понятно из рисунка.
При температуре стеклования задействуют привод и вытягивают проволоку из гипсового подслоя оправки; за счёт разрушения гипса в зоне, примыкающей к шпангоуту, кольцевое ребро освобождается от взаимодействия с оправкой.
Свои особенности в эту проблему привносит намотка конических оболочек с торцевыми шпангоутами. Здесь более важной оказывается задача амортизации напряжений, возникающих в оболочке, из-за различия температурных деформаций изделия и оправки. Решением является применение упругих кольцеобразных элементов из эластомерного материала (резина, полиуретан) с модулем упругости не более 4–5 МПа (рис. 6), причём на упругий элемент возлагается дополнительная функция — совместно с гипсовым подслоем оправки образовать формообразующую поверхность для намотки шпангоутов.
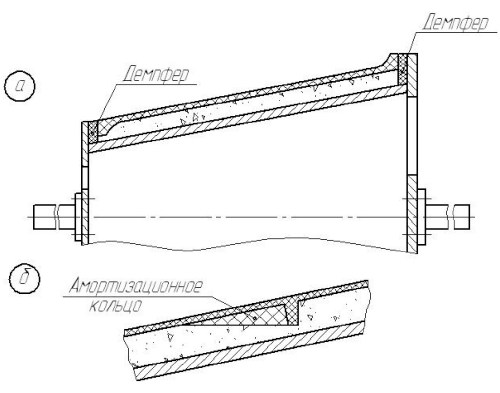
Рис. 6. Схема установки упругих элементов: а — установка резиновых демпферов на торцах оправки; б — установка амортизаторов с образованием пазов для подкрепляющих шпангоутов
Недостатком таких колец является одноразовость их использования, обусловленная старением эластомерных материалов в процессе отверждения оболочки из ПКМ. Кроме того, низкая контактная жёсткость колец не обеспечивает необходимого качества формуемых элементов оболочки, что недопустимо при изготовлении изделий повышенной точности.
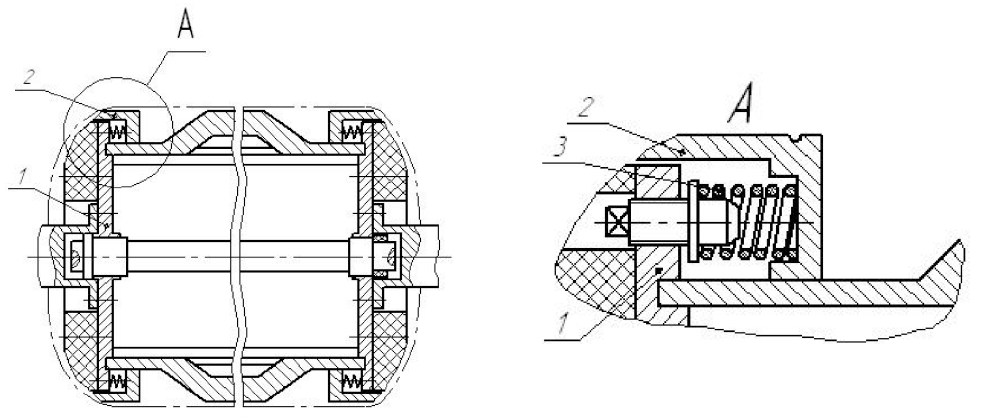
Рис. 7. Металлическая оправка с торцевыми компенсирующими элементами: 1 — торцевой диск; 2 — компенсирующее кольцо; 3 — пружина
До некоторой степени указанных недостатков лишена конструкция оправки, приведенная на рис. 7. Здесь основным элементом является компенсирующее кольцо, подпружиненное на торцевом диске оправки. С помощью вертикальной плоскости этого кольца формируется торцевая поверхность стыковочного шпангоута с поперечным сечением трапециевидной формы. Поэтому на этапе намотки компенсирующие кольца должны быть застопорены. Перед полимеризацией оболочки кольца надо расфиксировать, чтобы в дальнейшем они выполнили свою функцию. На этапе охлаждения оболочки с оправкой осевые температурные деформации металлической оправки превышают аналогичные деформации оболочки из ПКМ, сжимающие оболочку усилия амортизируются пружинами, предохраняя её от чрезмерного сжатия.
Выводы
Этим, конечно, не исчерпываются конструктивные и технологические возможности обеспечения монолитности подкреплённых оболочек из ПКМ, но всё описанное здесь — из реальной практики. В зависимости от конкретных условий возможно бесконечное сочетание компенсационных способов снижения микро- и макроструктурных ТТН в конструкциях из композитов.
В каждом случае выбор способа или комбинации методов обеспечения монолитности, удовлетворяющих комплексу конструктивных, производственных, экономических и экологических требований, всегда является самостоятельным этапом проектирования технологического процесса на основе не только справочных данных, но и с учётом практического опыта других.
Авторы обращают внимание на необходимость дальнейшего развития исследований (фундаментальных и прикладных) в области технологической механики конструкций из композиционных материалов.
В чём-то нам могут возразить. Например, сейчас в механике разрушения композиционных конструкций вопросы монолитности не считаются первостепенными, т. к. полная монолитность обеспечивает малое сопротивление продвижению трещины. Неполная монолитность с одной стороны затупляет вершину трещины, а с другой — нарушает прямолинейность траектории распространения трещины, уменьшая живучесть материала [2]. Но всегда необходимо сохранять проблему накопления информации о повреждениях в таких конструкциях, чтобы иметь возможность прогноза для ответа на ключевой вопрос: «Как долго будет служить конструкция?». Следует сохранять в памяти катастрофу ТУ-154 в Иркутске, когда самолёт рухнул на жилой дом, потеряв крыло из-за разрушения лонжерона, ослабленного бесконтрольно развившейся трещиной, превысившей критическую длину.
Литература
- Рейфснайдер К. Повреждение конструкций из композитов в процессе эксплуатации / Прикладная механика композитов: Сб. статей 1986-1988 г.г. Пер. с англ. – М.: Мир, 1989. – 358 с.
- Ханин М. В., Зайцев Г. П. Изнашивание и разрушение полимерных композиционных материалов. – М.: Химия, 1990. – 256 с.
- Болотин В. В. Влияние технологических факторов на механическую надёжность конструкций из композитов // Механика полимеров, 1972, №3. – с. 529–540.
- Томашевский В. Т., Смыслов В. И., Шалыгин В. Н., Яковлев В. С. Теория и методы обеспечения бездефектной макроструктуры армированных полимеров при переработке в конструкции специальной техники. – М.: ЦНИИ информации, 1984. – 316 с.
- Тарнопольский Ю. М. Проблемы механики намотки толстостенных конструкций из композитов // Механика композитных материалов, 1992, №5. – с. 618–626.
- Работнов Ю. Н., Екельчик В. С. Об одном способе предотвращения трещин при термообработке толстостенных оболочек из стеклопластика // Механика полимеров, 1975, №6. – с. 1095–1098.
- Томашевский В. Т. и др. Технологические методы обеспечения монолитности оболочек из стеклопластика. – Л.: ЦНИИ «Румб», 1976. – 130 с.
- Бабаевский П. Г., Кулик С. Г. Трещиностойкость отверждённых полимерных композиций. –М.: Химия, 1991. – 336 с.
- Томашевский В. Т. и др. Прогнозирование технологических дефектов и способы их предотвращения в намоточных армированных полимерах: Тезисы докладов I Всесоюзной конференции по композиционным полимерным материалам и их применению в народном хозяйстве, т. III. – Ташкент: Изд. ТПИ, 1980. – с. 40.