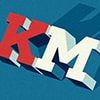
Современные материалы для средств индивидуальной бронезащиты
рубрика: материалы
«Текстильная или гибкая броня по сей день очень далека от совершенства. Думаю, что в ней реализовано не более 60–70 процентов потенциальных возможностей отечественных арамидных волокон». (Евгений Федорович Харченко, Генеральный директор АО ЦВМ «Армоком»)
Реальность сегодняшнего времени диктует нам темы для статей. Каждый день мы слышим риторику о важности качественной экипировки военнослужащих. Предприятия, выпускающие средства индивидуальной бронезащиты (СИБ), не справляются с заказами и переходят на круглосуточный режим работы и шестидневную рабочую неделю. Поисковые запросы в Интернет со словом «бронежилет» возросли в несколько раз.
Давайте разберемся какое место в этом вопросе занимают композитные материалы и какие у нас имеются достижения в этой области.
По среднестатистическим данным военных действий и конфликтов на 30% пулевых ранений личного состава приходится 70% осколочных ранений. Наиболее эффективно и в полном объеме от осколков человека оберегают средства амуниции и индивидуальной защиты, которые создаются из тканей на основе арамидных волокон, собранных в пакет в составе шлема, комбинезона и бронежилета.
Арамидные волокна для средств индивидуальной бронезащиты разработали в 70-х годах прошлого века. Сначала это были Кевлар и СВМ, схожие по химическому составу, но отличающиеся технологией производства. Несмотря на довольно высокую стоимость, данные материалы показали наилучшие физико-механические свойства при снижении веса изделий и поэтому нашли широкое применение в текстильных и композитных защитных конструкциях. Позже, в результате упорной работы российских ученых по улучшению характеристик арамидных волокон, разработаны нити второго поколения Армос и Руслан с еще более высокой прочностью. При плотности в 5 раз меньше, прочностные свойства арамидов в 3,5 раза больше самых высокопрочных марок стали. За счет своих высоких характеристик арамидные волокна нашли широкое применение в различных отраслях промышленности: армирование автомобильных шин, изготовление сверхпрочных тросов, оплетки оптических и иных кабелей, спортивного оборудования и инвентаря, в судостроении, горном деле, но все же большую популярность снискали в производстве средств индивидуальной бронезащиты, а также армированных композиционных материалов для ракетной, авиационной и атомной отраслей.
Однако совершенствуется не только материалы для бронезащиты. Разработка вооружений в разных странах тоже не стоит на месте. Постоянно появляются все новые виды боеприпасов и оружия, что влечет повышение требований к защитным свойствам средств бронезащиты. Поэтому непрерывно ведутся работы по поиску новых материалов для обеспечения необходимого уровня стойкости изделий.
Общевойсковой шлем 6Б47 «Ратник» из трёх слоёв композитных материалов на момент его принятия на снабжение был лучшим в мире. Его противоосколочная стойкость 630 м/с, весит он 1,1 кг, а лучший зарубежный общевойсковой шлем тогда весил 1,3 кг. О том «Как делают самый прочный в мире войсковой шлем» мы писали в журнале «Композитный мир» №1 (82) 2019.
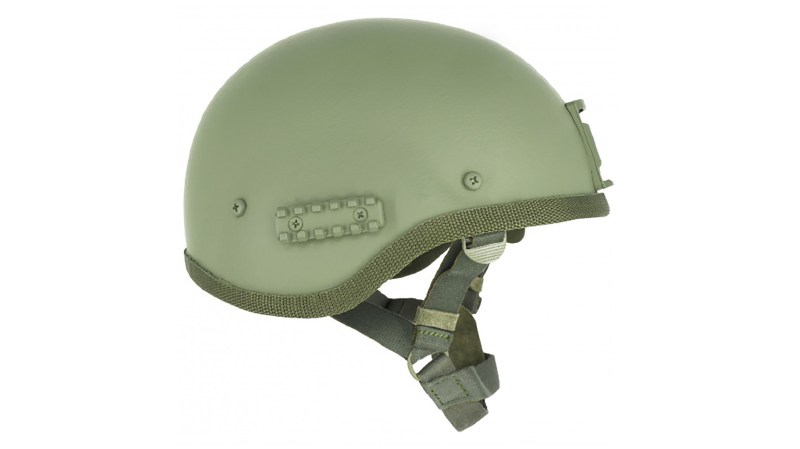
Общевойсковой шлем 6Б47 «Ратник»
Прошло несколько лет, и на Западе появились изделия с более продвинутыми характеристиками. Например, корпус нового американского бронешлема IHPS из сверхвысокомолекулярного полиэтилена (СВМПЭ) весит около 900 г и обеспечивает очень высокую противоосколочную стойкость.
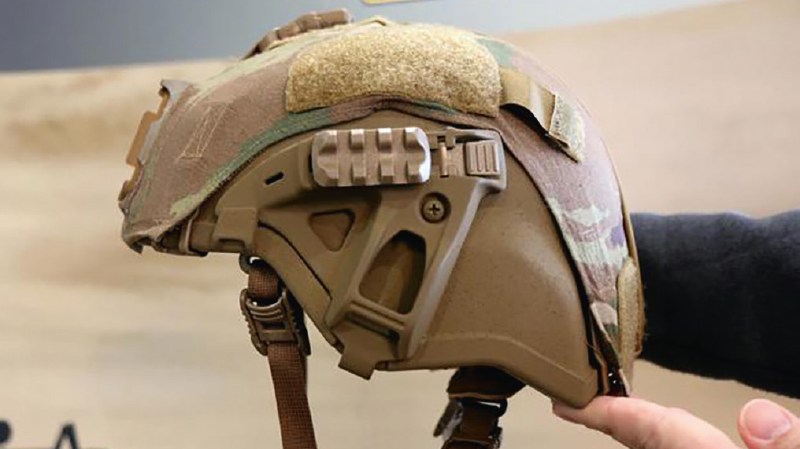
Новый американский бронешлем IHPS
В основе такого успеха западных разработчиков СИБ лежат достижения в области материаловедения. Они шагнули вперёд благодаря использованию новых материалов, прежде всего СВМПЭ и самой лёгкой керамической брони из карбида бора. К тому же, и в области конструирования шлемов у них появились интересные находки.
Каким должен быть в данном случае наш ответ? И можем ли мы чем-то ответить?
Новый способ производства арамидных нитей, освоенный на одном из предприятий в Подмосковье, позволил значительно улучшить их характеристики. В результате у нас в России появилась нить третьего поколения «Русар-С», обладающая существенными преимуществами по отношению к нити-предшественнице «Руслан». Исследования показали, что ткани из «Русар-С» на треть прочнее тканей из нити «Руслан», и композитная броня из нитей нового поколения защищает гораздо лучше. Её противоосколочная стойкость выше на 13 процентов.
Повысить защитные свойства изделий для индивидуальной бронезащиты можно также за счёт использования при производстве композитной брони волокон из СВМПЭ. В такой броне благодаря свойствам этих нитей энергия пули (или осколка) рассеивается лучше. Следовательно, появляется возможность снизить массу шлема или бронепанели (по предварительным оценкам, примерно на 15 процентов) при сохранении защитных свойств либо увеличить степень защиты, оставив неизменной массу изделия. Бронеэлементы на основе СВМПЭ нитей могут обеспечивать защиту не только от осколков и пистолетных пуль, но и от пуль длинноствольного оружия со стальным сердечником. Благодаря низкой плотности сверхвысокомолекулярного полиэтилена шлем из этого материала будет обладать плавучестью. Это свойство оценят прежде всего морские пехотинцы.
Отечественные технологии создания композитов из СВМПЭ для СИБ
В России пока нет промышленного производства СВМПЭ. Однако наши учёные из Научно-исследовательского института синтетического волокна с экспериментальным заводом (г. Тверь) и Центрального научно-исследовательского института специального машиностроения (г. Хотьково) разработали технологию и создали экспериментальную линию по производству СВМПЭ нитей. И получили волокно, которое по основным показателям превосходит сверхпрочные нити SK-75 и SK-78, производимые мировым лидером в этой области — голландской фирмой «DSM Dyneema». Казалось бы, успех композитчиков предопределён.
Следующим шагом должно стать создание в 2021–2024 годах опытно-промышленного производства нитей из сверхвысокомолекулярного полиэтилена мощностью порядка 10 тонн в год. А затем планируется развернуть промышленное производство этого материала, что позволит обеспечить Вооружённые Силы России изготовленными из СВМПЭ средствами индивидуальной защиты.
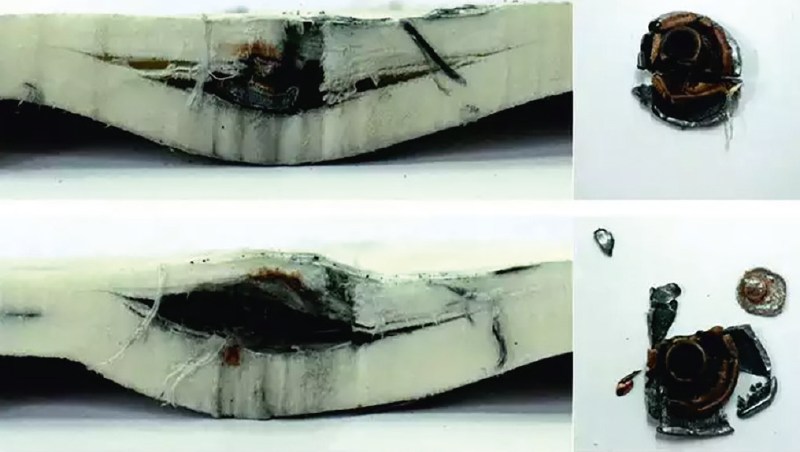
Характер разрушения пуль 7Н28 при обстреле СВМПЭ композита толщиной 10 мм — пробито 40 процентов толщины
Однако из-за почти нулевого коэффициента трения и высокой электризуемости эти волокна нельзя переработать традиционными ткацкими методами в эффективные тканые структуры. С другой стороны, никак не удавалось подобрать полимерное связующее, чтобы склеить СВМПЭ волокна в монолитный композит, ибо у него и адгезионная способность на нуле. Даже проверенные в ракетной технике высокоадгезионные эпоксиды не помогли…
И только в 2020 году инженерам из Центра «Армоком» и Центрального НИИ спецмашиностроения (г. Хотьково) удалось разработать состав композита на основе СВМПЭ волокон и, что очень важно, технологию формования не только плоских, но и криволинейных изделий из полиэтиленкомпозита.
При значительно меньшем удельном весе отечественного полиэтиленкомпозита он обладает прочностными свойствами на уровне лучших зарубежных аналогов. Однако наиболее примечательно то, что его баллистические свойства не только на 40 процентов превосходят арамидные композиты на основе ткани «Кевлар», но и ощутимо выше зарубежного СВМПЭ композита. Возможно, это связано с тем, что новый материал получается по нетрадиционной намоточно-компрессионной технологии.
Впрочем, если СВМПЭ это — дело ближайших, но всё-таки лет, то уже сегодня наши учёные и конструкторы Центра высокопрочных материалов «Армированные композиты» создали с использованием передового термокомпрессионно-намоточного метода формования (метод Харченко) новый материал, которого нигде в мире больше нет. Это сверхвысокоармированный органопластик (СВАО).
«Арамидные волокна и изделия из них не исчерпали себя, их потенциал используется не полностью», – убеждён руководитель экспертной группы по средствам бронезащиты Межведомственной рабочей группы (лаборатории) боевой экипировки при Военно-промышленной комиссии, генеральный директор Центра высокопрочных материалов «Армированные композиты» Евгений Федорович Харченко.
Композитная броня с использованием сверхвысокоармированного органопластика
Применение СВАО в керамокомпозитных бронематериалах позволяет более чем в 2 раза уменьшить арамидный слой брони в изделиях самого высокого 5-го класса защиты. К примеру, если в стандартной броне такого типа для защиты от бронебойных пуль с энергией более 3000 Дж используется органопластиковая подложка на основе арамидных тканей толщиной 9–10 мм, то благодаря применению СВАО достаточно толщины всего 4 мм. Общая толщина керамокомпозитной брони уменьшается не менее чем на 30 процентов, что применительно к бронепанелям боевой экипировки позволяет на 10–12 мм снизить поперечные размеры носимого снаряжения и почти на 1 кг — его массу. А благодаря уменьшению в полтора раза расхода дорогостоящих арамидных нитей на производство одного изделия будет достигнута заметная экономия бюджетных средств.
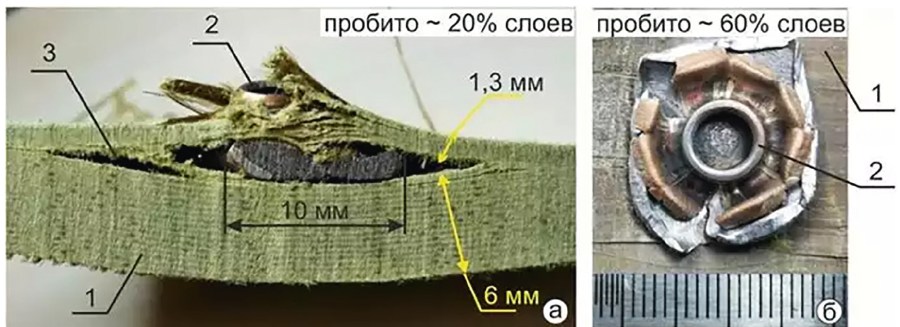
Поперечный срез бронематериала СВАО поверхностной плотностью 8 кг/м2 после обстрела из пистолета ПСМ калибром 5,45 мм (а) и бронематериал после обстрела из СР-1 калибром 9 мм (б). 1 — бронематериал; 2 — пуля; 3 — зона расслоения в месте остановки пули
Получить сверхвысокоармированный органопластик на обычном оборудовании проблематично, поэтому в Центре высокопрочных материалов «Армированные композиты» была создана первая в России научно-исследовательская лаборатория композитных бронематериалов. Её оснастили новыми станками, позволяющими выполнить все технологические операции по производству СВАО.
В этой лаборатории изготовили керамокомпозитную броню с использованием СВАО, которая превзошла наиболее известный и востребованный на мировом рынке бронематериал типа UD из СВМПЭ волокон по 3-му классу защиты. Как рассказал начальник лаборатории Антон Кормаков, наша 9-миллиметровая броня прекрасно выдержала пулю повышенной пробиваемости из пистолета Ярыгина с 5 метров. Доля пробитых слоёв органопластика при этом составила всего 33 процента. А вот импортная броня из СВМПЭ практически при той же поверхностной плотности и толщине 21 мм была пробита этой же пулей на 78 процентов. Наша броня сердечник пули разрушила, а заморская — не смогла. Как говорится, почувствуйте разницу!
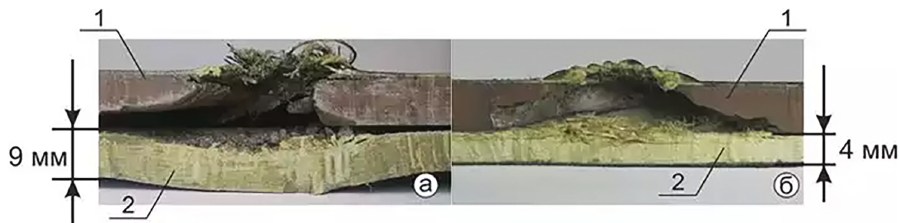
Поперечные срезы керамокомпозитных бронематериалов с использованием штатной подложки на основе арамидной ткани (а) и СВАО (б) после обстрела бронебойными боеприпасами 7,62 мм: 1 — керамический экран; 2 — органокомпозитная подложка
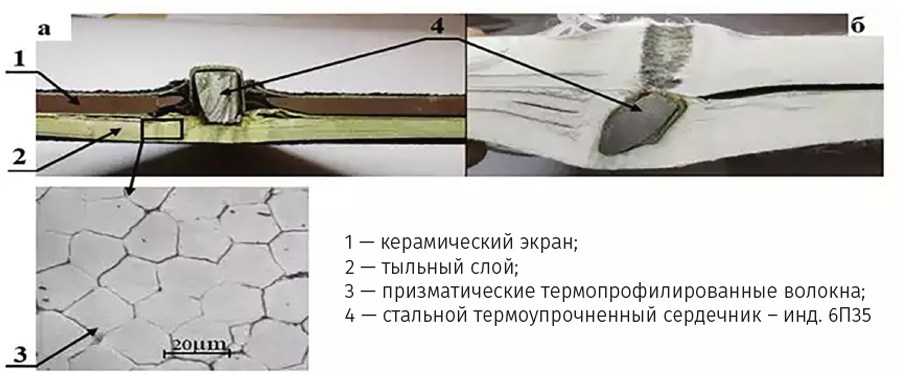
Поперечные срезы бронематериалов, после обстрела из пистолета Ярыгина разработанной керамокомпозитной (а) и традиционной полиэтилен-композитной брони на основе СВМПЭ волокон (б)
Единственным существенным недостатком всей композитной брони до сих пор была её толщина. И вот наши учёные впервые в мире смогли снизить этот параметр не на 5–10 процентов (хотя и это было бы достижением), а революционно, более чем в два раза! Одновременно двукратно уменьшилась и масса изделия. Ощутимо снизится и цена, поскольку в технологии производства теперь не требуется ткачество. И всё это — за счёт использования СВАО, изготовленного по методу Харченко. Тем самым опровергнуто считавшееся прежде аксиомой правило — о том, что толщина керамического слоя композитной брони непременно должна быть больше калибра стрелкового оружия, от которого она предназначена защищать.
Полиэтиленарамидные бронематериалы
Проводятся испытания и гибридных двухслойных полиэтиленарамидных бронематериалов. Такая броня также обладает замечательными характеристиками.
«При разработке третьего поколения общевойсковых бронешлемов мы сможем сделать накладки из СВМПЭ на лобную часть, а может и на весь шлем, что позволит обеспечить не только противоосколочную защиту, но и противопульную», — говорит Евгений Харченко. «Из автомата такой, фактически штурмовой шлем можно будет пробить только при стрельбе в упор. А с 200–300 метров и более уже не получится».
Что касается нового базового бронежилета, то без снижения уровня защиты его масса уменьшится по сравнению с нынешним на 1,3 кг. При этом повысится живучесть, то есть способность держать большее количество выстрелов в одну бронепанель. Поскольку американский аналог и сегодня тяжелее нашего, значит, в области бронежилета мы были и останемся впереди планеты всей.
Если эти задачи специалисты нашей оборонной отрасли – Центрального НИИ спецмашиностроения, Центра высокопрочных материалов «Армированные композиты», Научно-производственной фирмы «Техинком» и ЗАО «Кираса» выполнят, то мы поднимемся на новый уровень СИБ. Ведь общевойсковые шлемы никогда прежде не защищали от пули из длинноствольного оружия. А новые – смогут! Задел для этого уже создан.
Что еще влияет на бронезащитные свойства
Поглощение энергии пули или осколка происходит за счет вытягивания и разрыва волокна. Главным минусом всех тканых материалов является искривление нитей в узлах переплетения и их скрутка. Уменьшение количества скруток на 1 м.п. со 100 до 50 дает повышение противоосколочной стойкости на 10–15%. Отличным результатом обладают ткани саржевого переплетения, так как являются изотропными по основе и имеют малое искривление нитей или маты с длиной волокон 10–12 мм.
При этом рекомендуется располагать куски ткани с нахлестом по примеру рыбьей чешуи, что способствует смене траектории пули на 90°. Бронежилеты такого вида на 25-40% легче, чем похожие аналоги с металлическими вставками. Композиты на основе арамидных тканей имеют показатели противоосколочной стойкости немного ниже, так как деформация волокон ограничена связующим веществом.
Несмотря на это, они имеют преимущества перед чисто тканевыми элементами защиты:
- сохранение формы изделия после воздействия пули или осколка, что принципиально важно для шлемов;
- изготовление жестких подложек для различных типов брони для снижения давления на тело человека без образования вторичного разрушения, то есть не происходит образования зазубрин и осколков от средств защиты.
Отличные результаты получены на трехслойных конструкциях, состоящих из внешних слоев из отвержденного композита и внутреннего пакета из дискретнотканевого материала.
При этом отвержденный наружный слой исключает случаи режущих повреждений, внутренний отвержденный слой распределяет энергию удара, разворачивает и останавливает осколок или пулю. В этих случаях в качестве матрицы используют «хрупкие» — эпоксидные связующие.
Полимерная композитная броня из органопластиков, в которых волокна имеют одинаковую химическую природу с матрицей, имеют самые высокие показатели защиты.
Усовершенствование защитных средств в дальнейшем будет связано с так называемой «жидкой броней» — средний слой представляет из себя аэрогель с наночастицами кварца в полиэтилен гликоле.
Арамидные волокна могут выпускаться в двух модификациях: в кручёном и некручёном виде.
В разные периоды развития композитной науки и практики предпочтение отдавали то одному, то другому ассортименту этого армирующего материала. Несмотря на то, что за рубежом 100 процентов арамидных нитей типа Кевлар, Тварон и других выпускается без крутки, наши технологи львиную долю нитей Русар и Руслан используют только в кручёном виде. Почему?
«Причин несколько. Первая из них банальна — подкрученную нить легче сдавать заказчику, так как она обладает большей разрывной нагрузкой, или прочностью, — поясняет (Евгений Федорович Харченко, Гендиректор АО ЦВМ «Армоком» — Однако в процессе изготовления бронематериала из этих нитей они пропитываются связующим, и картина меняется. Прочность некручёной нити в микропластике существенно выше, а в намоточном органопластике значительно, на 16% превышает свойства композита из кручёных нитей». Другой причиной предпочтения кручёных нитей является их лёгкая проходимость через лентоформующие тракты намоточных станков — некручёные нити требуют более бережного отношения к себе при переработке. Однако результирующий фактор — прочность композитного материала из некручёных нитей превышает композит из кручёных нитей на 30–40 кгс/мм².
Много это или мало? «Когда-то мне, молодому инженеру, врезалась в память цитата из американского отчёта о том, что для повышения уровня прочности композитов на каждый 1 кгс/мм² необходимо затрачивать 1 млн долларов, — делится воспоминаниями Евгений Фёдорович. — А у нас разница в 30–40 кгс/мм² формируется на том же оборудовании и по той же цене».
Исследования показали, что переход к производству некручёных арамидных нитей прибавит 12–16 процентов баллистической стойкости (прочности) изготовляемой из них текстильной брони. В итоге без лишних производственных затрат наши военнослужащие получат экипировку, которая намного лучше защитит их на поле боя. Разве можно пренебречь такой возможностью? Ни в коем случае! Совершенствование технологии производства бронезащитных материалов должно быть направлено на переработку именно некручёных арамидных нитей.
Производитель арамидных нитей — АО «Термотекс» из города Хотьково — по заказу Центра «Армоком» изготовил несколько сотен килограммов нити Русар с круткой, равной нулю. В результате удалось получить значительно более прочную текстильную броню. Ткань из некручёной нити 58 текс показала противоосколочную стойкость 620 м/с при поверхностной плотности 3,7 кг/м², а штатная ткань из аналогичной кручёной нити показывает не более 540 м/с.