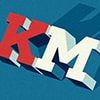
Новолачные эпоксивинилэфирные смолы для теплостойких композиционных материалов следующего поколения
рубрика: материалы
Модифицированные новолачные эпоксивинилэфирные смолы используются для изготовления композитных материалов, при эксплуатации которых требуется высокая теплостойкость. При комнатной температуре эти смолы находятся в жидком состоянии, пригодны для длительного хранения и при этом быстро отверждаются, а также подходят для широкого спектра методов изготовления изделий из композитных материалов.
На основе данных высокоэффективных смол, для проведения испытаний на механические и тепловые свойства были изготовлены композитные материалы, армированные стекловолокном и углеродными волокнами. Показатели сохранения прочностных свойств и модуля упругости при повышенной температуре у данных смол следующего поколения превышают наивысшие показатели имеющихся в продаже винилэфирных смол.
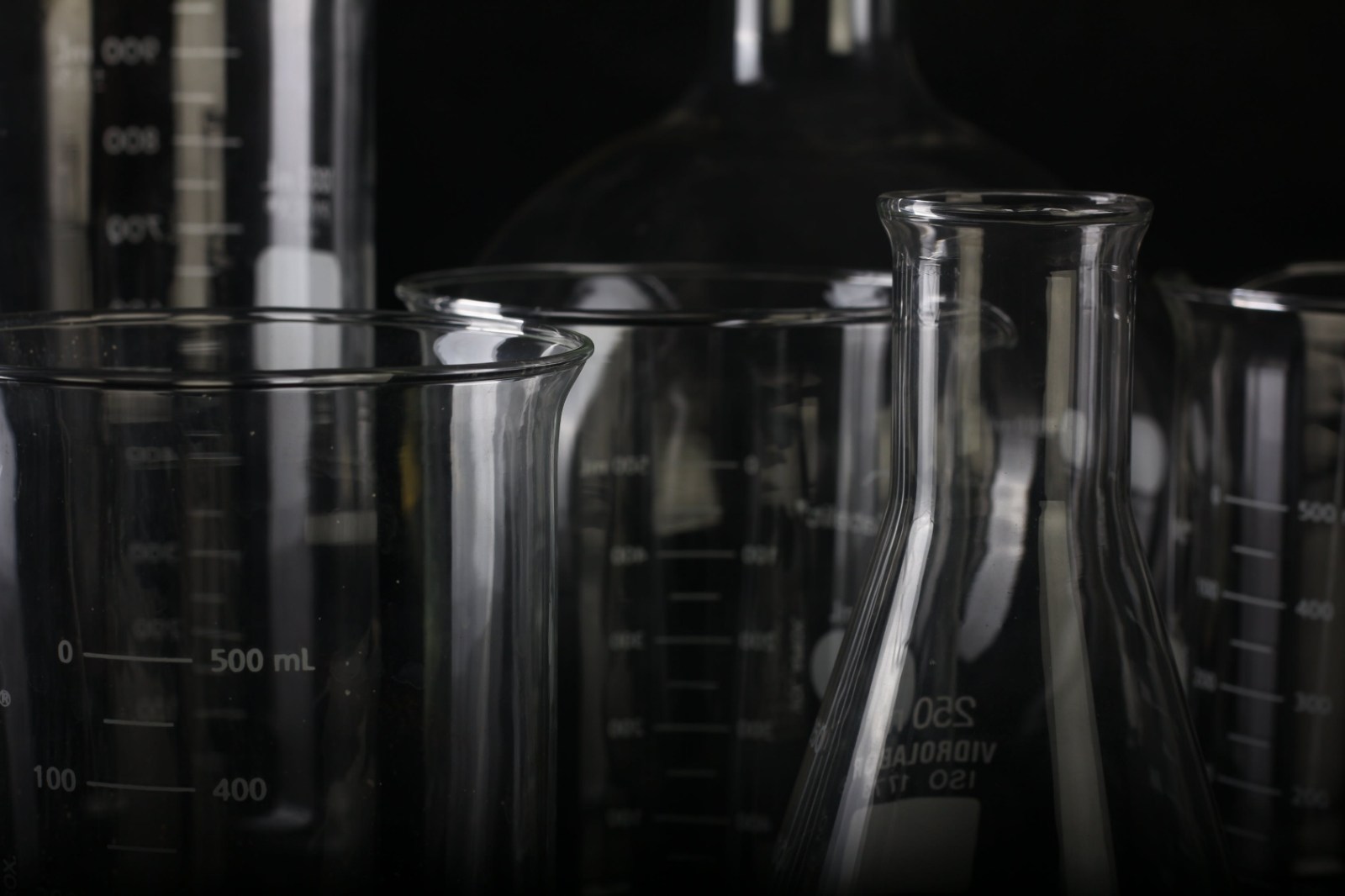
1. Введение
Винилэфирные смолы имеют долгую историю применения в жестких атмосферных условиях, так как в них сочетаются прекрасные показатели механических и тепловых свойств с очень хорошей коррозионной стойкостью, частично благодаря их внутренней структре в отвержденном состоянии. Винилэфирные смолы (ВЭ) часто являются предпочтительными смолами, когда требуется использовать методы изготовления, совместимые с ненасыщенными полиэфирными смолами (НПС), но при которых свойства НПС недостаточны. Эпоксидные новолачные винилэфирные смолы (НВЭ) обладают повышенными тепловыми характеристиками по сравнению с традиционными ВЭ на основе Бисфенола А или по сравнению с НПС. Будучи аналогичными ненасыщенным полиэфирам и эпоксивинилэфирам на основе Бисфенола А, НВЭ также отверждаются в процессе изготовления изделия из композитных материалов посредством механизма свободно-радикальной полимеризации. После начала и продолжения свободнорадикальной реакции метакрилатные группы легко сополимеризуются со стиролом. Получаемая в результате высокая плотность сшивания в готовой детали из композитного материала — непосредственное следствие действия полимерного каркаса метакрилата (рисунок 1), который способствует первосортным тепловым характеристикам.
Рисунок 1. эпоксидный новолачный винилэфир
Некоторые варианты применения НВЭ включают изготовление из них коррозионно-стойких покрытий, теплозащитных экранов, дымовых труб, инструментов из композитных материалов и прочих конструктивных компонентов из композитных материалов, где требуется высокая теплостойкость. Целью настоящего исследования была разработка новолачных винилэфирных смол с повышенными тепловыми характеристиками. Данные смолы могут быть переработаны стандартными методами для полиэфирных смол, такие как намотка, ручное формование, напыление, пултрузия, RTM, вакуумная инфузия и горячее прессование. Конечное назначение этих новых теплостойких смол включает варианты применения, перечисленные выше, а также другие сегменты рынка с трудными атмосферными условиями, в которых не используются существующие технологии ВЭ, такие как скважинная добыча нефти и газа, электростанции, детали двигателя автомобиля и авиационно-космическая отрасль.
В настоящем отчете приводятся подробные сведения о нескольких новых перспективных высокотемпературных вариантах смол из модифицированных новолачных виниловых эфиров (МНВЭ). Они сравниваются с наилучшими новолачными виниловыми эфирами (F086), имеющимися в продаже на сегодняшний день. Общее описание каждого НВЭ приведено в таблице 1. Перспективные варианты разработаны для чрезвычайной теплостойкости и варьируются от вариантов с очень высокой плотностью сшивки до пластифицированных аналогов с повышенной растяжимостью. Один перспективный вариант сочетает в себе бромированный полимерный каркас с высокой плотностью сшивки новолачного винилового эфира для обеспечения высокой теплостойкости с трудногорючестью (XR-4501). В каждом случае перспективные варианты анализировались и сравнивались с эталоном F086.
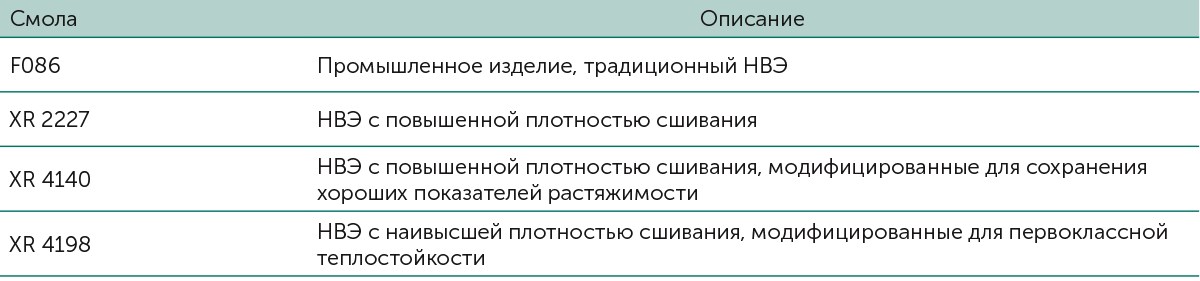
Таблица 1. Описание модифицированныхэпоксидных новолачных виниловых эфиров (МНВЭ), прошедших испытания по настоящему отчету.
В жидком состоянии оцениваются такие свойства, как вязкость и время гелеобразования, а также проводится исследование для определения пригодности новых смол при высокой рабочей температуре и в жестких атмосферных условиях. Выполняется оценка сохранения механических свойств как литого образца, так и слоистых материалов. Для дополнительного исследования термоустойчивости изучена потеря массы, как функция изменения температуры в ходе термического гравиметрического анализа (ТГА).
2. Испытания
2.1. Материалы
Все испытанные смолы по настоящему отчету являлись эпоксидными новолачными винилэфирными смолами (НВЭ), изготовленными компанией AOC, LLC по методам и формулам собственной разработки. Соли металлов были приобретены у компании OMG, диметиланилин — у компании Sigma-Aldrich, пероксиды — у AkzoNobel и United Initiators, а стекломатериалы — у компании Owens Corning. Использовались стекломатериалы на основе ровинговой стеклоткани WR24/3010 (830 гр/м2) и мата из рубленных комплексных нитей М723 (450 гр/м2). Слоистые материалы из углеродного волокна были получены на основе однонаправленной ленты 403 гр/м2 плетения 0/90 производства Saertex USA.
2.2. Оценка свойств в жидком состоянии
Оценка вязкости была проведена с помощью вискозиметра Brookfield LV DV-II+. Образцы весом 340 г были помещены в химический стакан на 400 мл, термостатированы и выдержаны при 25°С с измерением показателей вязкости в течение 60 секунд, при вращении шпинделя RV № 2 со скоростью 20 об/мин.
Время гелеобразования было измерено с помощью измерителя гелеобразования модели 22-B от компании Sunshine с использованием 100 г катализированной смолы при 25°С. Максимальные показатели температуры были измерены с помощью быстроразъемной термопары с резистивным датчиком температуры от компании Omega.
2.3. Подготовка литого образца
Литой образец является неармированной отвержденной смолой. Литые образцы смолы подготавливались по одному из двух методов, и они указаны в разделе с результатами. 400 г смолы были инициированы (катализированы) либо (1) 1% по весу Trigonox C, третбутилпероксибензоата (ТБПБ); либо (2) 0,05% диметиланилина, 0,15% раствора 12% кобальта бис (2-этилгексаноата) в уайт-спирите, и 2% Trigonox K-90, гидропероксида кумола (ГПК). Инициированные смолы были влиты в облицованные майларом стеклянные пластины 305×305 мм с проставками 3 мм. Образцы были помещены в печь и выдержаны с линейным повышением температуры от 25 до 205°С в течение 30 часов. Полученные литые образцы были нарезаны на заготовки для механических испытаний, термического гравиметрического анализа и коррозионных испытаний. В разделе 3.3 «Инициатор и постотверждение» были изучены другие пероксиды и варианты постотверждения согласно подробному описанию в этом пункте.
2.4. Схема изготовления образцов
Слоистые материалы типа II по ASME были подготовлены с использованием смолы F086 и модифицированных новолачных винилэфиров с повышенными тепловыми характеристиками (МНВЭ). Смолы были ускорены по формуле с использованием 0,05% диметиланилина, 0,15% раствора 12 кобальта бис (2-этигексаноата) в уайт-спирите, инициированного с помощью 2% Trigonox K-90, гидропероксида кумола, и отверждены при комнатной температуре. Слоистые материалы были обработаны одинаковым образом и включали включали перемежающиеся 7 слоев стекломата М723 и ровинговой стеклоткани WR24/3010 (мат, стеклоткань, мат, стеклоткань, мат, стеклоткань, мат). Слоистые материалы на 44% по весу состояли из стекломатериалов и имели толщину 7 мм. После отверждения слоистых материалов в течение 16 часов при температуре 25°С, они были дополнительно отверждены при 205°С в течение 5 часов. Слоистые материалы из углеродного волокна были подготовлены из 6 слоев однонаправленной углеродной ленты производства Saertex. Слои были нарезаны на заготовки размером 406×508 мм и сформованы методом инфузии в продольной плоскости (0–508 мм). Инфузия также выполнялась поперек направления волокон, и отверждение проводилось при комнатной температуре с долей углеродного волокна 54% по весу.
2.5. Механическое испытание
Слоистые материалы и заготовки литых образцов различных смол были подвержены механическому испытанию на универсальной испытательной системе компании Instron серии 5984, согласно ASTM D638 (испытание на растяжение), используя экстензометр компании Epsilon Tech [3542-0200-025-HT2], ASTM D790 (трехточечный изгиб), а также экстензометр компании Instron. Испытания при повышенной температуре проводились с помощью данных методов ASTM и камеры искусственного климата компании Instron [3119-410] для проверки способности сохранения свойств.
Скорость испытания на растяжение была установлена на 5 мм/мин. Скорости испытания на изгиб и расстояние между опорами устанавливались на основании толщины образца относительно ASTM D638. Литые образцы были подвержены испытанию на изгиб при 1,2 мм/мин и расстоянии между опорами 51 мм. Образцы из стеклопластика были испытаны на изгиб при скорости нагружения при 2,9 мм/мин и расстоянию между зажимом и местом приложения нагрузки 112 мм. Число заготовок на один образец равнялось пяти в соответствии с ASTM D638.
На литых образцах были проведены дополнительные механические испытания, соответствующие ASTM D648 (температура тепловой деформации/HDT). Во время испытаний, соответствующих ASTM D648 использовалось испытательное устройство Dynisco HDV 3 (деформационная теплостойкость/теплостойкость по Вика), оборудованное датчиком перемещения Mahr Federal Maxum III. Максимальная рабочая температура испытательного устройства Dy-nisco HDV 3 равнялась 280°C благодаря теплоносителю, силиконовой жидкости Dow 710R. Заготовки были испытаны в поперечном направлении статической изгибающей нагрузкой в 1,82 МПа с расстоянием от захватов до места приложения нагрузки 100 мм. В ходе испытания температура росла со скоростью 2°С/мин до тех пора, пока не произошел изгиб образца на 0,25 мм. Для сообщения о локальной температуре при наблюдении этого прогиба использовались термопары.
2.6. Термический гравиметрический анализ
Порошкообразные пробы литых смол в диапазоне 6–8 мг были изучены при температурах от 25°C до 700°C, при повышении температуры 20°C в минуту, используя термогравиметрический анализатор PerkinElmer TGA 7.
Использовался поток продувочного газа или азота (в начале) со скоростью 20 л/мин. Каждый образец был тарирован до 100% веса и выдерживался на протяжении 5 минут при 25°C. Для каждого образца производился отдельный замер, и составлялась кривая нагрева. Данный метод испытания при помощи термического гравиметрического анализа в целом соответствует требованиям, предъявляемым ASTM E1131 для измерения термического распада. Данные испытания также были повторно проведены с использованием печи для ТГА и при контакте с воздухом.
2.7. Анализ предельного кислородного индекса
Не армированные литые образцы размером 76 или 102 мм были размечены каждые 10 мм (±0,25 мм) и последняя отметка была на расстоянии 50 мм от вершины образца. Предельный кислородный индекс (ПКИ) литых образцов был измерен при помощи модуля для измерения предельного кислородного индекса GOVMARK, в соответствии с ASTM D2863.
3. Результаты
3.1. Свойства жидкости
Смолы МНВЭ были подвержены испытанию в соответствии со стандартными испытаниями свойств смол для определения гелеобразования и вязкости в качестве первого шага к обеспечению их совместимости с традиционными методами изготовления, которые используются для композитных материалов НПС и ВЭ. В таблице 2 приведены свойства смол, изготовленных по имеющейся технологии и перспективных вариантов МНВЭ с повышенной теплостойкостью. Значения вязкости и времени гелеобразования находятся в нормальном диапазоне для традиционных методов изготовления, и при необходимости могут быть изменены с учетом варьирующегося содержания мономера или ингибитора/ускорителя.
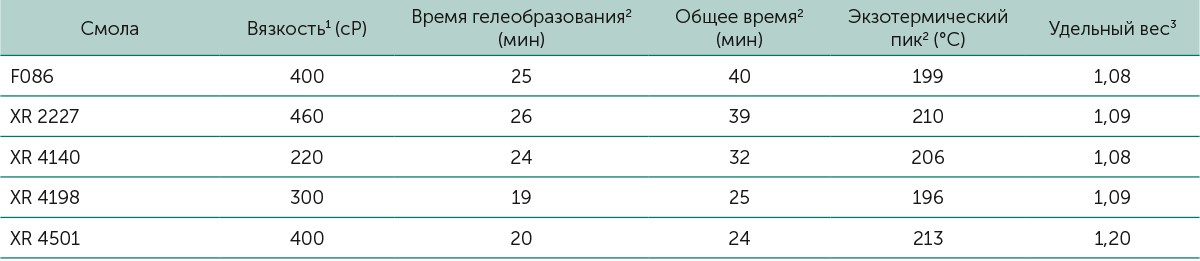
Таблица 2. Свойства традиционного НВЭ и модифицированный НВЭ в жидком виде. 1 — шпиндель Brookfield RV-2, 20 оборотов в минуту при 25°C; 2 — время гелеобразования при 25°C со 100 г смолы с 0,15% раствора 12% кобальта бис (этигексаноата), 0,05% диметиланилина и 2% Trigonox K-90; 3 — удельный вес при 25°C
3.2. Механические свойства литых образцов
Высококачественные механические свойства являются характерной особенностью виниловых эфиров, а высокая теплостойкость является ключевым отличием новолачных виниловых эфиров. Следовательно, испытание физических свойств необходимо в данном исследовании для оценки новолачных виниловых эфиров с повышенными тепловыми характеристиками. Первым этапом проверки механических свойств данных перспективных вариантов является испытание заготовок неармированных литых образцов. Литые образцы были подготовлены путем отверждения смол с помощью 1% ТБПБ и дополнительного отверждения, как изложено в разделе с испытаниями. В таблицах 3 и 4 приводятся итоговые сведения о свойствах при изгибе: свойства теплостойкости при изгибе, HDT и свойства при растяжении. Повышенная HDT была достигнута у всех перспективных вариантов в ущерб прочности и растяжимости.

Таблица 3. Свойства при изгибе (ASTM D790) при 25°C HDT (ASTM D648) 1/8 дюймов неармированных чистых литых образцов для традиционного НВЭ и модифицированных НВЭ с повышенными тепловыми характеристиками. Было произведено отверждение смол с 1% ТБПБ и дополнительное отверждение в соответствии с графиком, указанным в разделе с экспериментами.

Таблица 4. Механические свойства неармированных литых образцов при растяжении (ASTM D638) при 25°С относительно традиционных и модифицированных НВЭ, разработанных для повышенных тепловых характеристик. Было произведено отверждение смол с 1% ТБПБ и дополнительное отверждение в соответствии с графиком, указанным в разделе с экспериментами.
XR-2227 и XR-4140 была достигнута высокая прочность при изгибе со средней прочностью на растяжение. Результаты испытания литых образцов, полученных из XR-4198, на HDT являются выше величин, ожидаемых при испытании на устройстве Dynisco HDV 3 при температуре > 280°C. Результаты испытания смолы XR-4501 отображают хорошую прочность при изгибе, хороший модуль и улучшенную HDT (200°C) в сравнении с бромированным новолачным винилэфиром, имеющимся в продаже на сегодняшний день (143°C у Vipel К095). Это достигается с помощью повышения плотности сшивания при сохранении трудногорючих свойств, обеспечиваемых связью брома с основной цепью полимера.
Температуры стеклования (Tg) с помощью ДМА (динамический механический анализ) или ДСК (дифференциальная сканирующая калориметрия) не были достигнуты. Тепловые явления, близкие к Tg, во время ДСК не наблюдались.
3.3. Инициатор и постотверждение
В целом, метод достижения максимальной теплостойкости композитного материала или литого образца заключается в превышении температуры стеклования матричной смолы при дополнительном отверждении с одновременным максимальным увеличением степени отверждения. За исключением настоящего пункта, во всех исследованиях, представленных в настоящем отчете, заготовки подвергались дополнительному отверждению при температуре 205°С. Для достижения максимальной совместимости с методами, используемыми производителями в настоящее время, наряду с альтернативными пероксидами были рассмотрены более низкие температуры дополнительного отверждения. Дополнительное отверждение при 205°С в некоторых случаях может быть неприменимым для предприятий по причине использования отверждения при комнатной температуре и более низких температур дополнительного отверждения.
Используя смолу XR 4198 для данного исследования с 2% гидропероксида кумола (Trigonox K-90) с 0,05% диметиланилина и 0,15% раствора 12% кобальта (бис этигексаноата), а также отверждение при комнатной температуре, без постотверждения, была достигнута температура тепловой деформации 85°C. Тем не менее, данный параметр при постотверждении на протяжении всего одного часа и при 120°C существенно возрос до > 280°C. Это возможно произошло, потому что образцы продолжили отверждаться в ходе испытания на температуру тепловой деформации. Однако в любом случае определенный уровень постотверждения является необходимым для достижения высокой температуры тепловой деформации, что доказывается ее значением при испытании неармированного литого образца XR 4198 с 2,0% гидропероксида кумола после проведения отверждения при комнатной температуре и без постотверждения. Альтернативные катализаторы также дают различные результаты. В образце XR 4198, произведенном с 1,25% MEKP-925H, 0,15% раствора 12% кобальта (бис этигексаноата), гелеобразованием при комнатной температуре, с пятичасовым постотверждением при 160°C, была достигнута HDT при > 280°C. Попытка отверждения XR 4198 и других перспективных вариантов с помощью 98% перекиси бензоила и нагрева привела к повреждению неармированных образцов, не смотря на плавную скорость нагрева.
3.4. Механические свойства при повышенной температуре
Варианты целевого применения композитных материалов для этих НВЭ осуществляются в условиях высокой температуры. В то время как механические свойства при комнатной температуре (25°C) позволяют получить относительные данные для других доступных технологий, а показатели температуры тепловой деформации указывают на возможную пригодность новых смол при повышенной температуре, требуется провести механическое испытание при повышенной температуре для проверки этого предположения. Заготовки для каждого НВЭ были подвержены механическому испытанию как слоистые материалы. Неармированные образцы были подготовлены, как указано в пункте 2.3. Механические свойства при растяжении и изгибе, то есть характеристики при повышенной температуре, были измерены как процент сохранения в сравнении с их испытательными значениями при 25°C используя уравнение:
Винилэфирная смола часто армируется стекловолокном в большинстве вариантов применения композитных материалов, поэтому испытание слоистого стеклопластика при повышенной температуре является критически важным. Материалы из слоистого стеклопластика типа II со стекломатом и ровинговой стеклотканью были подготовлены с содержанием 44 масс. %, стекломатериалов с толщиной 7 мм. Были обрезаны заготовки для проведения испытаний на изгиб и растяжение. Результаты показаны в таблицах 5 и 6.

Таблица 5. Свойства при изгибе (ASTM D790) слоистых материалов типа II, получаемых из стандартного НВЭ и модифицированного НВЭ с повышенными тепловыми характеристиками при 25°C и 200°C.

Таблица 6. Свойства при растяжении (ASTM D638) слоистых материалов типа II, получаемых из стандартного НВЭ и модифицированного НВЭ с повышенными тепловыми характеристиками при 25°C и 200°C.
Слоистые материалы были подвержены испытанию при 200°C, что намного превышает температуру тепловой деформации F086. В этих результатах наиболее выраженным является заметное улучшение новых МНВЭ по сравнению с F086. Механические свойства при растяжении хорошо сохранились для варианта XR 4198 с наивысшей температурой тепловой деформации, при этом этот вариант также продемонстрировал наилучшие характеристики при испытании на изгиб.
Винилэфирная смола иногда смешивается с углеродным волокном в самых требовательных вариантах применения композитных материалов для улучшенной прочности и модуля. XR 4140 выбран в качестве опытного образца для этого испытания из-за своей растяжимости. Аналогичным образом очень требовательные варианты применения могут включать высокую рабочую температуру, под воздействием которой будет осуществляться постотверждение слоистого материала НВЭ в работе. Слоистые материалы из углеродного волокна XR 4140 были подвержены испытанию при 25°C и при 200°C с воздействием стандартной температуры их дополнительного отверждения 205°C и без. Эти слоистые материалы состоят из 6 слоев однонаправленных углеродных волокон производства Saertex USA с 54% по весу и толщиной 4,8 мм. Были обрезаны заготовки для проведения испытаний на растяжение и изгиб. Результаты показаны в таблице 7.
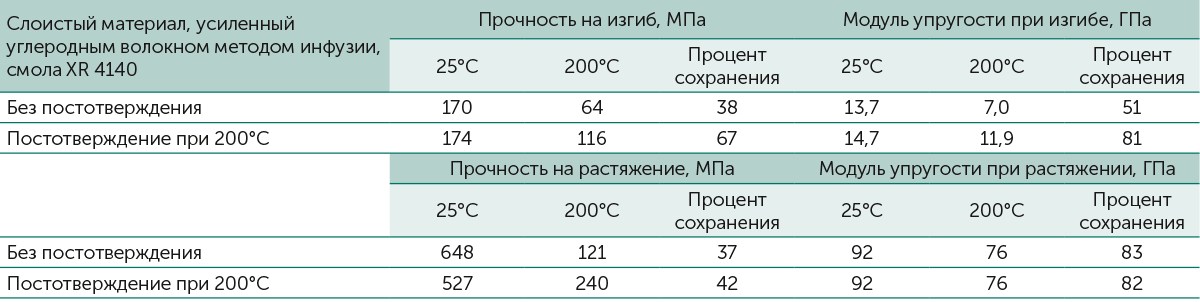
Таблица 7. Механические свойства при растяжении и изгибе слоистого материала, усиленного углеродным волокном методом инфузии, получаемого из XR 4140.
В этих результатах наблюдается выраженное улучшение по сравнению со слоистым стеклопластиком XR 4140 в абсолютных значениях во всех аспектах. Это улучшение возможно в результате использования углеродного волокна и его однонаправленного типа усиления. Испытание показало, что сохранение значений модуля и прочности на изгиб между стекловолокном и углеродным волокном на слоистых материалах после дополнительного отверждения является аналогичным.
Сохранение прочности на растяжение слоистого материала на основе XR 4140, армированного углеродным волокном, предположительно подвергается негативному воздействию вследствие сложности проведения испытания и обозначения высокого модуля однонаправленных слоистых материалов, особенно при повышенной температуре из-за возникновения дефектов на поверхности образца в зоне захвата его зажимом. В ходе механического испытания также выявлено, что главное отличие между этими слоистыми материалами из углеродного волокна со смолой XR 4140 с применением дополнительного отверждения и без него заключалось в улучшенном сохранении прочности вместо меньшей прочности при комнатной температуре.
3.5. Термический гравиметрический анализ
В то время как сохранение механических свойств при повышенной температуре всех перспективных вариантов улучшилось, снижение веса является другим фактором, который необходимо принимать во внимание при аттестации материала для эксплуатации в условиях высокой температуры. Термический гравиметрический анализ (ТГА) проводился на неармированных литых перспективных вариантах, а также на смоле, имеющейся в продаже. Они все относились к одинаковым литым образцам, подготовленным для испытания в пункте 3.2. Для термического гравиметрического анализа требуется небольшой образец, измеряющийся обычно в миллиграммах, который подвергаются нагреванию, и масса которого фиксируется. Все смолы, прошедшие испытания продемонстрировали потерю массы менее 3% при 350°С и быстрое разложение при приблизительно 400°С. Дополнительный эксперимент планируется поставить с образцами не армированных отливок и с образцами стеклопластика, увеличенных размеров. Образцы будут нагреваться воздухом с выдерживанием при высокой температуре.
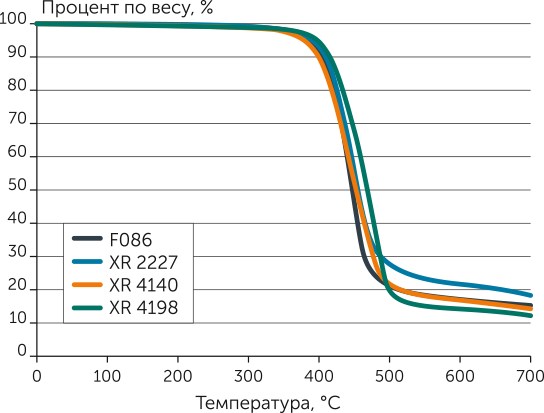
Рисунок 2. Термический гравиметрический анализ (ТГА) новолачных винилэфирных смол в атмосфере азота.
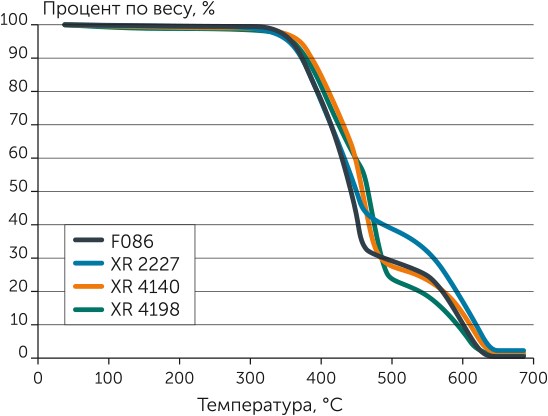
Рисунок 3. Термический гравиметрический анализ (ТГА) новолачных винилэфирных смол в воздушной атмосфере.
3.6. Испытание предельного кислородного индекса
Сравнение первоклассного огнезащитного новолачного винилового эфира, имеющегося в продаже на сегодняшний день, и аналогов с повышенной теплостойкостью (XR 4501) проводилось посредством испытания предельного кислородного индекса. Выходные данные этого испытания определяют минимальное содержание кислорода, требуемое для поддержания горения материала. Эталонный материал, используемый для сравнения с XR 4501 — первоклассный трудногорючий новолачный виниловый эфир, имеющийся в продаже, соответствует требованиям по распространению пламени ASTM E84, класс 1. XR 4501 с повышенной теплостойкостью превосходит промышленный трудногорючий новолачный виниловый эфир. Для поддержания горения требуется 33% кислорода по сравнению с промышленным новолачным виниловым эфиром Vipel K095, где требуется 29%. Оба типа смол содержат одинаковую концентрацию брома. По большей части это достигается благодаря наивысшей температуре тепловой деформации у XR 4501, которая проявляется при изгибе при 200°C, по сравнению с промышленной новолачной трудногорючей смолой —при 143°C. Дальнейшие стандартные испытания XR 4501 на распространение пламени и способность образования дыма (то есть ASTM E84 и другие) будут необходимы перед использованием в огнезащитных применениях.
4. Заключение
Были проанализированы и представлены модифицированные новолачные эпоксивинилэфирные смолы с повышенными тепловыми характеристиками. Свойства этих перспективных вариантов в жидком состоянии указали на возможность сопоставления с традиционными методами изготовления, которые используются для производства полимерных композитных материалов из ненасыщенного полиэфира и винилового эфира. Также может потребоваться подгонка значений вязкости и времени гелеобразования под конкретные применения, но эти незначительные модификации не должны влиять на контрольные испытания, представленные в данном исследовании. В дальнейшем будут изучены свойства устойчивости к коррозии этих перспективных вариантов в зависимости от применения композитных материалов. Все перспективные варианты показали улучшенные механические свойства по сравнению с трудногорючим новолачным виниловым эфиром, имеющимся в продаже, при испытаниях как слоистых материалов, так и литых образцов. Были представлены предварительные результаты для огнезащитного новолачного винилового эфира с повышенной температурой тепловой деформации. Улучшенные результаты предельного кислородного индекса и значительно повышенная теплостойкость при изгибе могут быть полезными в композитных материалах для огнезащиты оборудования. На сегодняшний день применение этих перспективных вариантов включают изготовление из них дымоходов, инструментов и труб из композитных материалов, а также использование в электрооборудовании при высокой температуре. Все данные виды применения МНВЭ находятся на испытательной стадии.