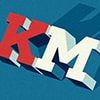
Исследование способа формования изделий из композиционных материалов
рубрика: материалы
В статье рассмотрен новый способ формования изделий из композиционных материалов. Описана технология формования с помощью матрицы и пуансона. Предложенный способ получения изделий из стеклопластика отличается возможностью изготавливать объемные изделия сложной геометрической формы без технологических оснасток, что экономически целесообразно. Разработаны и обоснованы варианты приводов позиционеров.
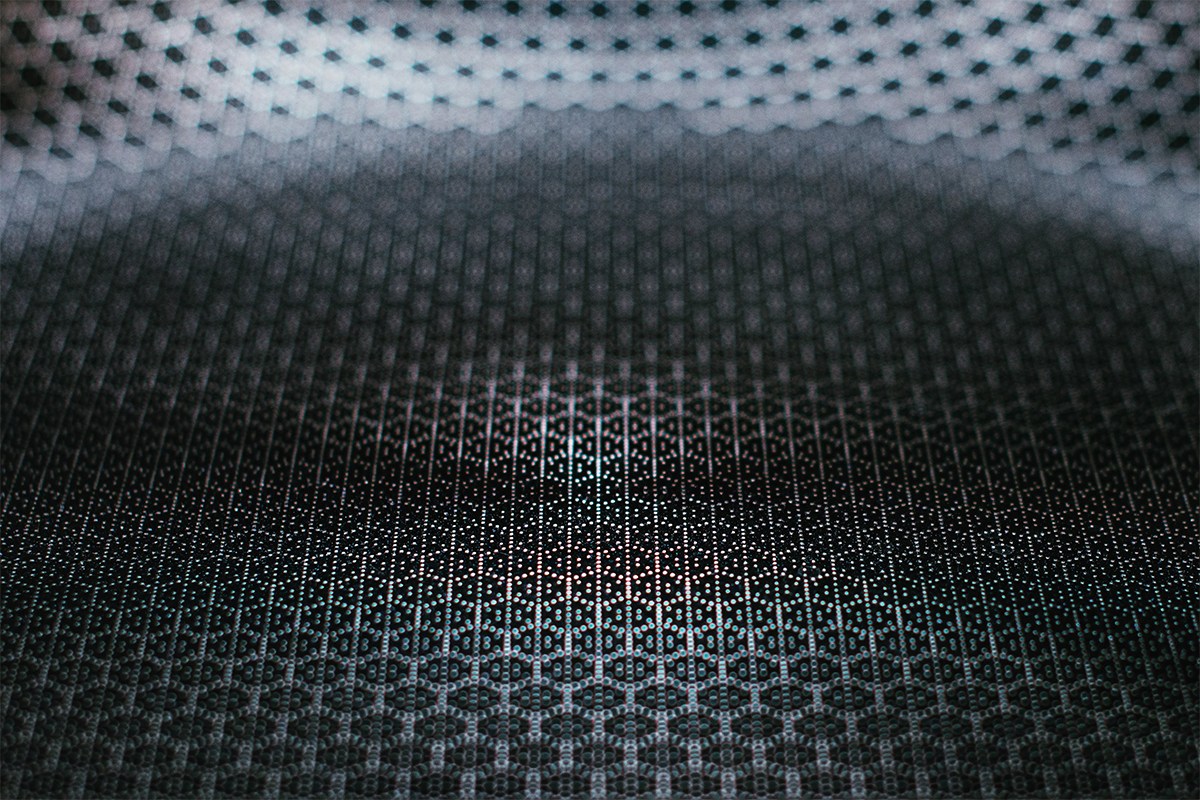
Недостатком широко применяемых для получения композитных деталей способов, таких как ручная выкладка, напыление с прикаткой и штамповка, является необходимость в технологической оснастке в виде формы или пары матрица — пуансон. Изготовление формообразующей оснастки экономически целесообразно далеко не всегда, а лишь при массовом производстве однотипных изделий, как правило, малых и средних размеров.
Задача упрощения технологии изготовления композитных изделий посредством матрицы и пуансона решена путем разработки специальной формообразующей конструкции — матрицы переменной кривизны (МПК) [1, 7].
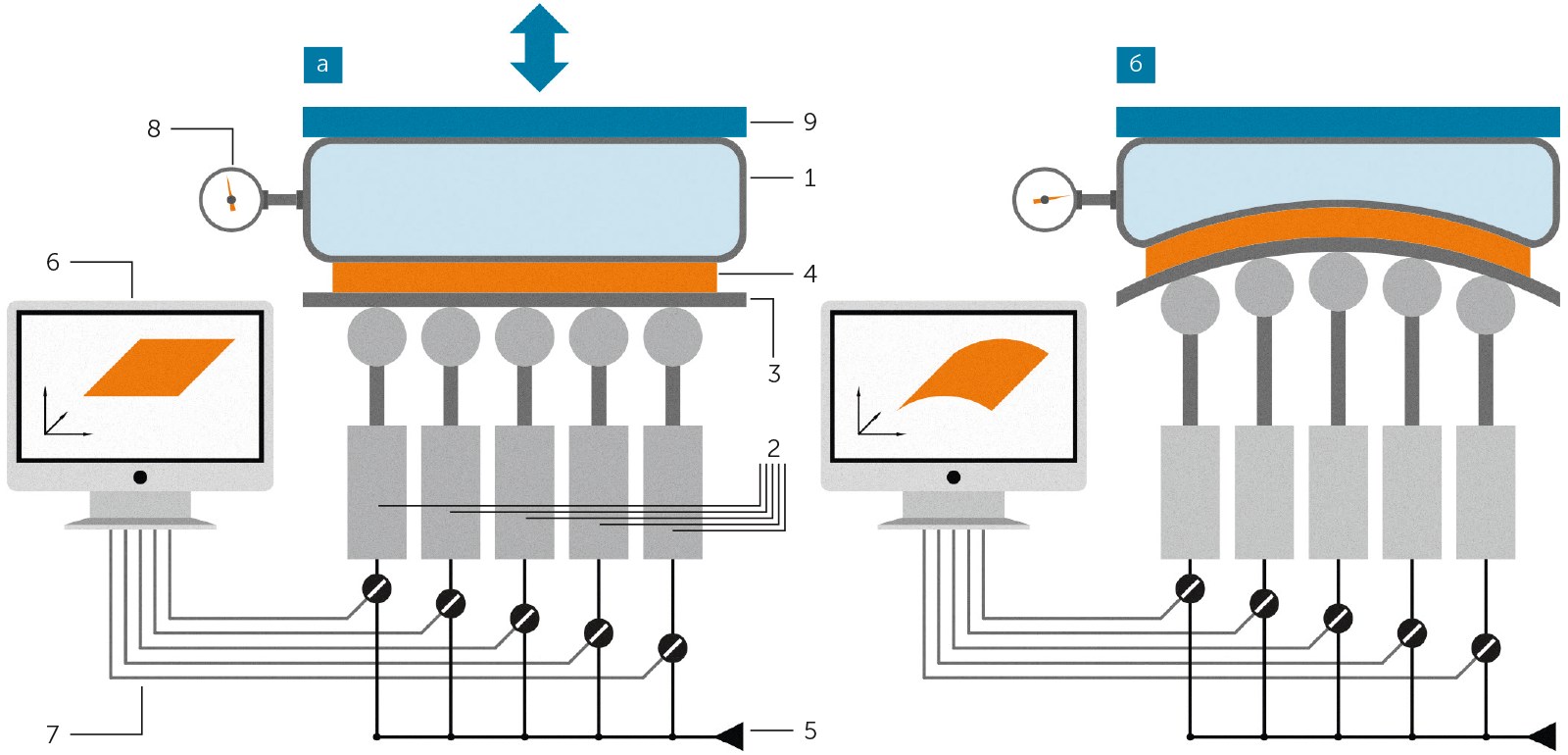
Рисунок 1. Схема установки для объемного формования на матрице переменной кривизны
Технологическая система для формования на МПК (рисунок 1–а) содержит пуансон (1) в виде баллона из эластичного материала, матрицу, образованную позиционерами (2), неподвижно установленными в несколько рядов на основании (на рисунке 2 показан один ряд), упруго-деформируемую прокладку (3), привод позиционеров (5) и управляющее устройство (6), например персональный компьютер (ПК). Армирующий материал (4) композита расположен между пуансоном (1) и прокладкой (3). ПК связан линиями (7) с исполнительными блоками системы управления позиционерами.
На рисунке 1 приведен вариант исполнения позиционеров в виде гидроцилиндров, соответственно и привод (5) представляет собой объемный гидропривод.
Воздействие пуансона на формуемый слой (4) обеспечивается избыточным давлением воздуха в баллоне, которое контролируется манометром (8). Оно создается либо подачей сжатого воздуха в баллон от компрессора, либо, как показано на рисунке 1–а, действием нажимной плиты (9) на герметично закрытый баллон при ее опускании.
Технологическая система функционирует следующим образом.
Концевые точки на головках штоков позиционеров принадлежат одной поверхности (рисунок 2). Пусть номер ряда, в котором расположен позиционер, i = 1…n, а номер позиционера в ряду j = 1…k, тогда совокупность точек объемом n × k определит топологию поверхности.
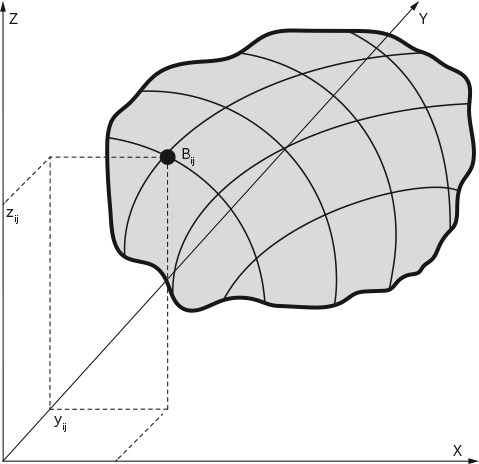
Рисунок 2. Концевая точка головки штока — как точка формуемой поверхности
На рисунке 2 точка Bij соответствует концевой точке головки произвольно взятого позиционера и принадлежит поверхности М. Смысл координат точки Bij: пара (xij, yij) есть «привязка» позиционера к основанию; zij — высота над некоторой нулевой плоскостью хОу. Если в качестве нулевой принята плоскость расположения концевых точек полностью вдвинутых штоков, то zij — перемещение, которое должен отработать позиционер номер (i, j).
Одинаковые для всех позиционеров значения координаты z означают, что будет отформована плоскость, как это показано на рисунке 1–а.
Для формования изделия со сложной поверхностью ее математическое описание закладывается в ПК. Описание по своей сути представляет собой совокупность значений координат zij, каждое из которых принадлежит конкретному позиционеру.
В исходном положении штоки позиционеров полностью вдвинуты, армирующий слой пропитан связующим, силовое воздействие плиты (9) на пуансон отсутствует (давление воздуха в баллоне практически равно атмосферному).
Включается привод позиционеров, начинается выдвижение их штоков. Текущее значение координаты z каждого позиционера контролируется системой управления. По достижении координатой величины, заданной математическим описанием поверхности, ПК по линии (7) отдает сигнал на исполнительный блок соответствующего позиционера, отключающий данный позиционер от привода, в результате чего его шток останавливается. В момент реализации заданной совокупности z будут остановлены все позиционеры, и прокладка (3) примет форму поверхности, заложенной в ПК (рисунок 1–б)
В ходе работы над установкой были изучены различные виды исполнения МПК. Простейший из них представляет собой плиту с отверстиями, расположенными по координатной сетке, число которых равно числу позиционеров. Поверхность плиты, таким образом, является плоскостью хОу. Роль позиционеров играют длинные винты со сферическими головками, устанавливаемые в отверстия и фиксируемые относительно плиты гайками. Расстояние от головки винта до поверхности плиты есть координата z точки внутренней поверхности упруго-деформируемой прокладки. Заданная конфигурация детали обеспечивается выставлением координат zij всех винтов вручную.
Наряду с такими достоинствами, как простота и дешевизна, данному варианту МПК присущи весьма существенные недостатки:
- большая трудоемкость работ
- по настройке матрицы;
- невозможность формирования заготовки
- поверхности в автоматическом режиме.
Указанные недостатки не могут служить основанием для безусловной отбраковки варианта, и в целом ряде случаев такая конструкция МПК вполне приемлема. В то же время на современном уровне развития техники ручные технологии большого интереса не представляют. Поэтому далее рассмотрены более сложные, но зато приемлемые для автоматизации и компьютерного управления варианты с электромеханическим, гидравлическим и пневматическим приводами.
Высокое качество изготовления детали предполагает использование МПК с достаточно большим количеством позиционеров на единицу площади. По-видимому, существует оптимальный шаг t по критерию минимума числа позиционеров при допустимых размерах дефектов формы поверхности. Вопрос об оптимуме t требует специальных исследований. На текущий момент данные экспериментов позволяют рекомендовать величину t = 12…50 мм.
Ход головки, который должен обеспечивать позиционер, задается конфигурацией поверхности детали, имеющей наибольший перепад координат (zmax − zmin) из номенклатуры изделий, для изготовления которых данная МПК проектируется. Для большинства изделий можно ожидать zmax − zmin ~ 100 мм.
Очевидно, что универсальность проектируемой МПК ограничивается соображениями целесообразности. Так, при запланированном выпуске комплекса деталей, наибольшая из которых имеет размеры в плане 500 × 500 мм, а сложнейшая по конфигурации — перепад zmax − zmin = 120 мм, нет смысла изготавливать МПК площадью 1 м2 с позиционерами, имеющими ход 250 мм.
Позиционер с пневматическим приводом выполняет функцию исполнительного модуля автоматизированной системы управления (АСУ). Точность позиционирования и компенсацию погрешности, обусловленной сжимаемостью газа, в его конструкции обеспечивают фрикционные стопорные элементы. В задачи пневмопозиционера АСУ не входит восприятие сколько-нибудь значимых нагрузок, поэтому для МПК он не пригоден. Важный недостаток пневмопривода состоит в том, что он реагирует на изменение нагрузки перемещением рабочего органа, и возникает необходимость включения в состав исполнительного модуля дополнительных, как правило, механических фиксаторов, которые неминуемо усложняют конструкцию и снижают ее надежность.
Гидравлический привод способен создавать многократно бόльшие усилия, управляющая аппаратура обеспечивает практическую герметичность силовых узлов, модуль упругости рабочего тела превышает 103 МПа [57Энг]. Для двигателей поступательного движения – гидроцилиндров — характерны простота и малые габариты. В первую очередь это относится к плунжерным гидроцилиндрам, о которых уже говорилось в описании технологии. Следует подчеркнуть, что гидроцилиндр в таком исполнении не нуждается в собственном корпусе (гильзе). Роль гильзы играют стенки полости. В состав силового узла позиционера с электромеханическим приводом естественно включить самотормозящуюся пару винт-гайка скольжения (ВГС). Достоинства и недостатки этого преобразователя движения, так же как и самого электромеханического привода, широко известны из технической литературы. Здесь достаточно констатировать, что среди недостатков нет факторов, запрещающих выполнение позиционера МПК в виде ВГС с электрическим приводом. Таким образом, гидравлический и электромеханический приводы вполне приемлемы для позиционеров МПК.
Описанная система и осуществляемый с ее помощью способ формования предназначены для изготовления композитных деталей различного назначения без дорогостоящих форм и штамповой оснастки.
Список литературы
- Таугер В. М., Холодников Ю. В. Альшиц Л. И. // Прогрессивные технологии производства композитных изделий // LAP LAMBERT Academic Publishing, Германия. 2014. cтр. 110.
- Грановский В. А., Сирая Т. Н. // Методы обработки экспериментальных данных. //Л. Энергоатомиздат, 1990, cтр. 288
- Холодников Ю. В., Таугер В. М. // Исследования процессов формования композитов на матрице переменной формы // Композитный мир. № 6, 2013 г. cтр. 60–64
- Справочник по композиционным материалам: в 2 кн. // под ред. Дж. Любина, М.: Машиностроение, 1988, cтр. 584
- Егоров О. Д., Подураев Ю. В. // Мехатронные модули. Расчет и конструирование: учеб. пособие. // М.: МГТУ «СТАНКИН», 2004, стр. 386.
- Таугер В. М. // Конструирование мехатронных модулей: учеб. пособие. // Екатеринбург: УрГУПС, 2009, стр. 336.
- Патент RU 2513405 приор. Опубл. 20.04.2014. БИ №11.