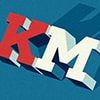
Критерии подбора полиэфирных смол для изготовления изделий из стеклопластика и искусственного камня
рубрика: материалы
Как среди многообразия представленных на рынке полиэфирных смол выбрать ту, которая идеально подойдет для решения вашей задачи? С чего начать поиск и как быстро, четко и грамотно сформулировать задачи для поставщиков сырья? Наверно, каждый производитель изделий из композитов хоть раз задавал себе эти вопросы.
А задаются ли подобными вопросами заказчики, например, стеклопластиковой продукции? «Нет, конечно», — ответите вы. И действительно, зачем им это? В данной статье я постараюсь объяснить, почему не только производителям изделий из композитов, но и их заказчикам — потребителям важно знать основные критерии, по которым осуществляется подбор исходного сырья, как избежать целого ряда проблем, имея хотя бы общие представления о выборе смол для производства композитов.
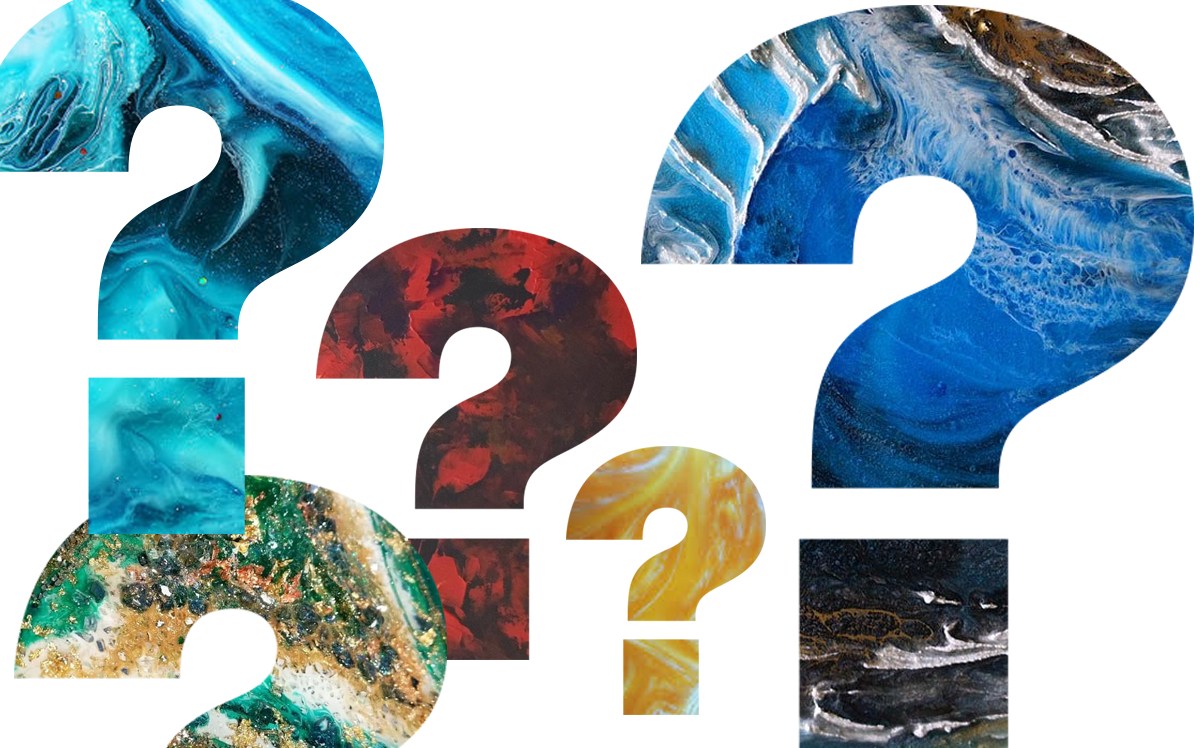
В идеале, чтобы решить задачу по подбору полиэфирной смолы, мы должны обратиться к свойствам конечного изделия и, основываясь на них, производить расчеты ламината, используя физико-механические свойства отвержденной смолы. Но, в большинстве случаев, заказчиками во главу угла ставится одна задача — это минимальная цена готового изделия. И производитель вынужден уменьшать материалоёмкость, искать более дешевое сырье. Производители связующего по цепочке вынуждены удешевлять свои продукты, используя дешевое низкокачественное сырье, упрощая процесс изготовления, не используя специальные добавки. И получается связующее, которое плохо пропитывает стекломатериалы, боится ультрафиолета, воды и имеет пониженные физико-механические свойства. Изготовить и показать заказчику изделие из данной смолы можно, но как оно будет вести себя при эксплуатации — вопрос.
Производители изделий из стеклопластика и искусственного камня для получения более низкой цены готового изделия идут на использование дешевых смол, не соблюдают производственный процесс, упрощая его. В итоге стеклопластик превращается в материал, который зачастую не способен нести на себе какую-нибудь нагрузку, не выдерживает природных атмосферных воздействий, из-за чего теряется возможность длительной эксплуатации самого изделия. Всё это негативно сказывается на репутации композитов в целом и еще больше подрывает доверие заказчиков к данному материалу.
Приведу несколько примеров. Среди наиболее распространенных изделий из композитов, можно выделить стеклопластиковые водоотводные лотки и емкости. Это те изделия, которые закапываются в землю, поэтому производитель и заказчик часто не обращают внимания ни на внешний вид, ни на свойства изделия. Возможно, что контрольные образцы и проверяются на физико-механику, но кто следит из каких сырьевых материалов сделан контрольный образец, а из каких — все остальные изделия в партии. Не буду вдаваться в вопрос подбора армирующих стекломатериалов, он тоже важен. Но в первую очередь на стойкость изделия влияет именно связующее.
На представленных в статье иллюстрациях видно к чему приводит погоня за дешевизной. Например, водоотводные лотки зачастую ждут монтажа месяц или более. При этом хранятся под открытым небом, под воздействием ультрафиолета, который разрушает изначально несоответствующее назначению изделия связующее. Да и сама смола из-за своей дешевизны порой не способна полностью пропитать, связать стекломатериалы. В итоге лотки расслаиваются, разрушаются, складываются при монтаже (рисунок 1).
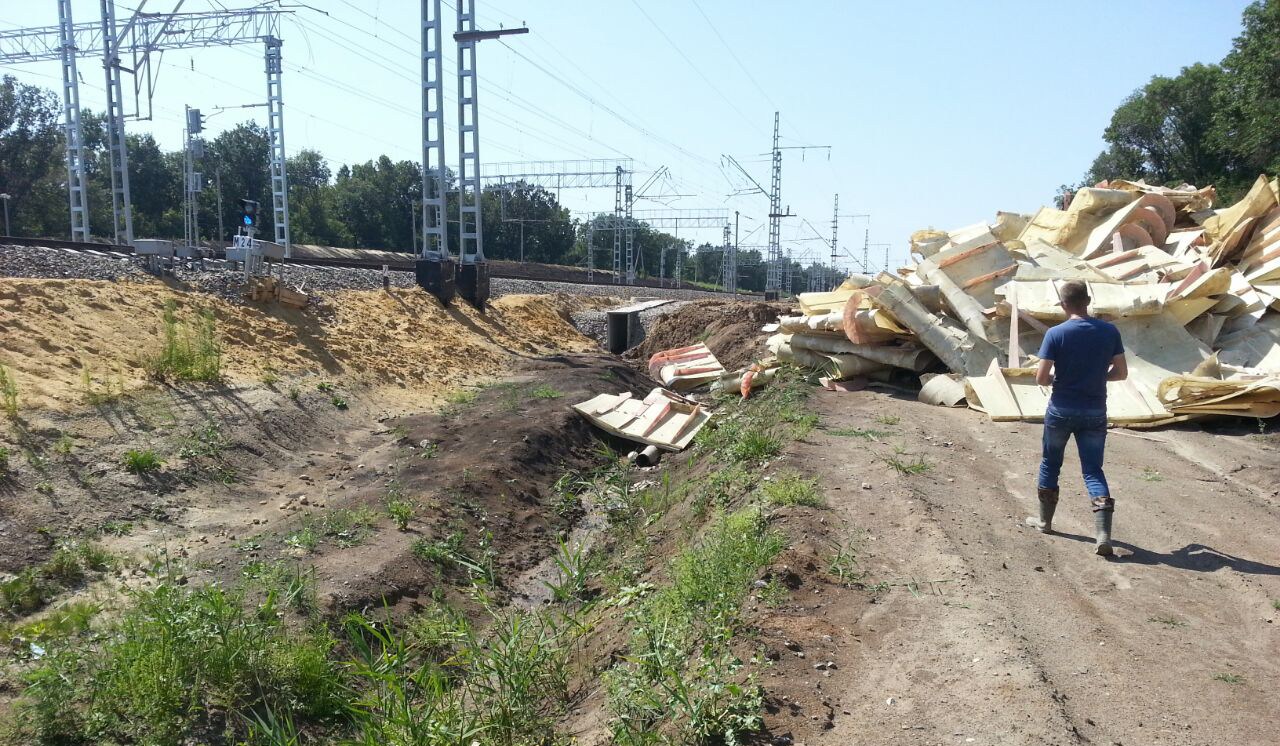
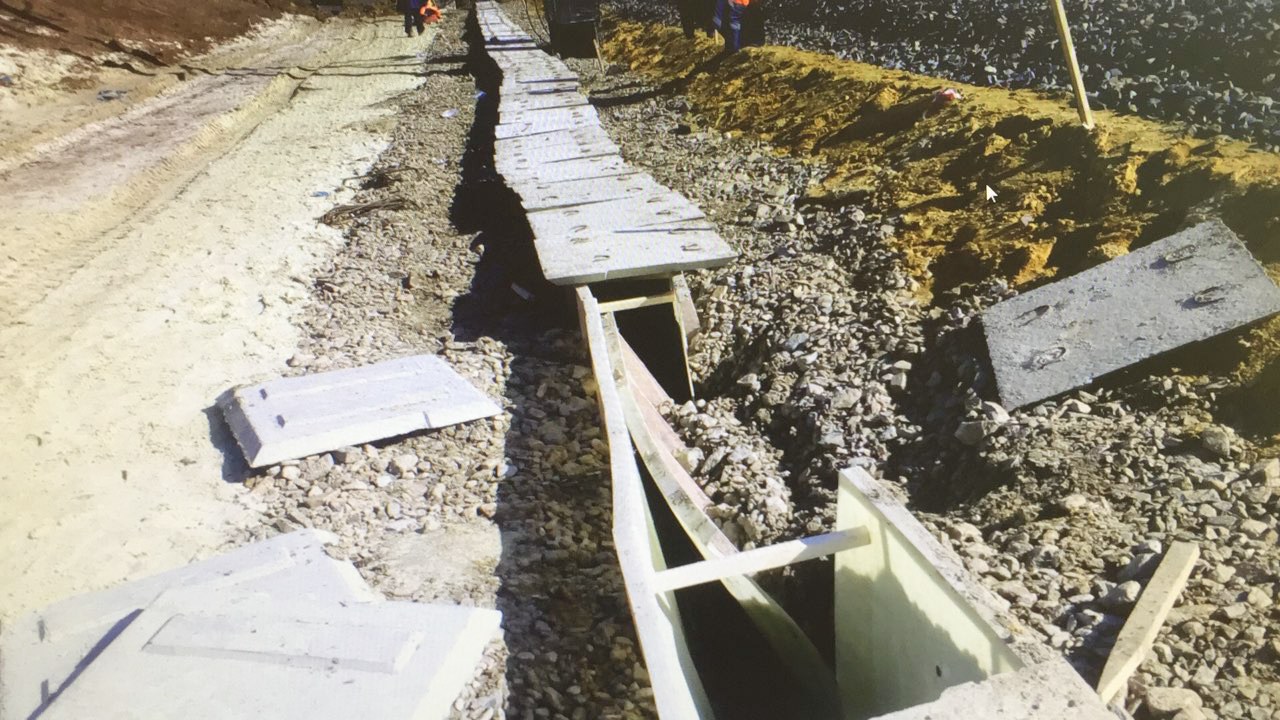
Рисунок 1. Разрушение при монтаже стеклопластиковых лотков, изготовленных из несоответствующих назначению изделия связующих
С намоткой еще страшнее. Дешевые смолы нетехнологичны и не способны поддерживать высокий темп производства при намотке, в результате чего ровинг полностью не пропитывается. Например, образуются непропитанные области наполнителя с внутренней части ёмкости (рисунок 2), а это контакт с жидкостями, и впоследствии осмос и разрушение ламината (рисунок 3).
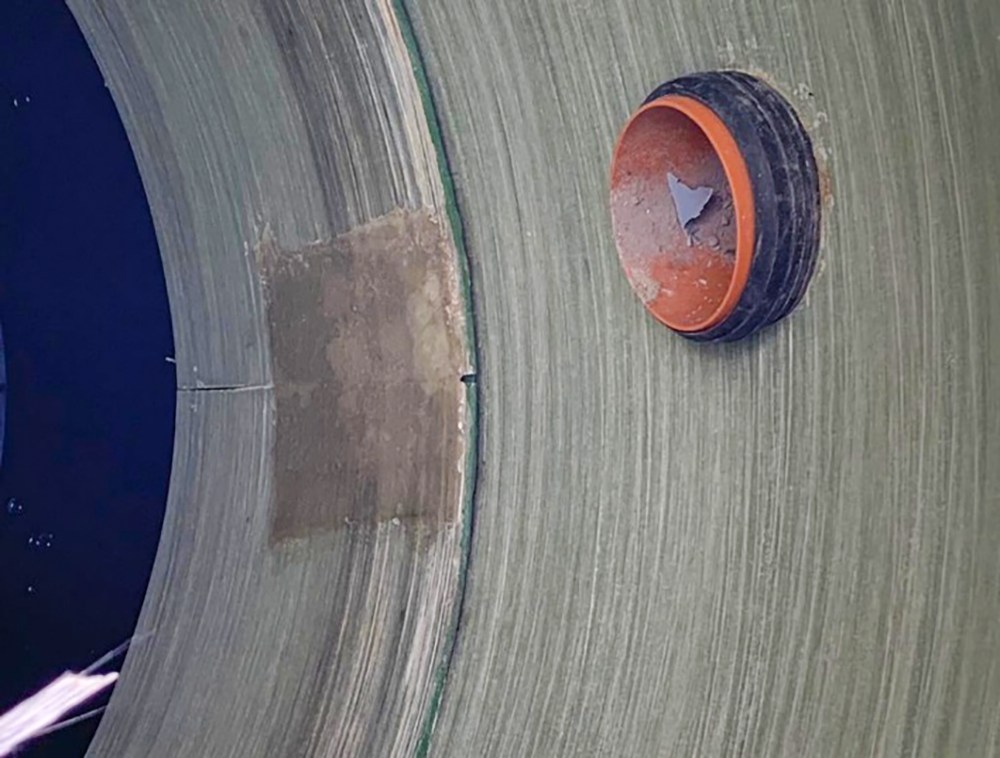
Рисунок 2. Непропитанные области наполнителя с внутренней части ёмкости
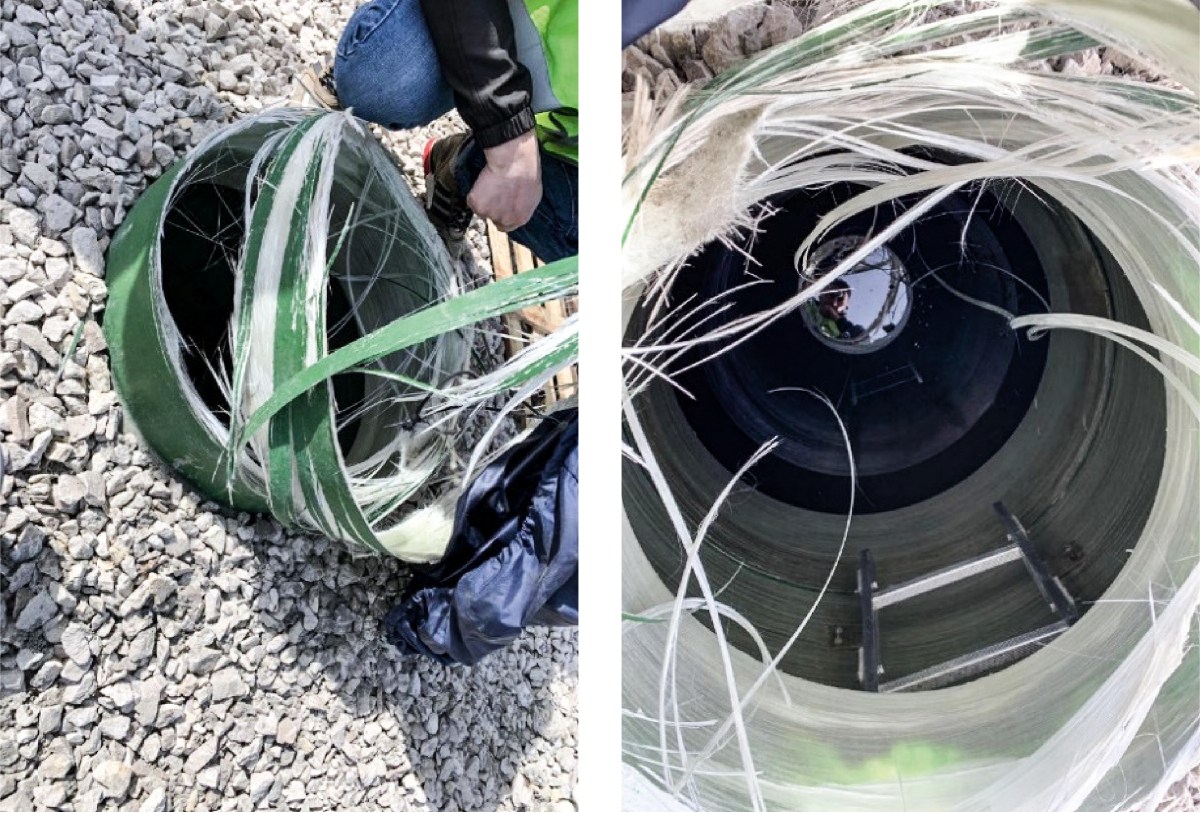
Рисунок 3. Расслоение ламината при нагрузке по причине плохой пропитки армирующих материалов связующим
Неправильный выбор смол без учета технологических особенностей производства изделий также приводит к негативным последствиям. Например, ребра жесткости зачастую наматывают тогда, когда тело ёмкости уже отвердилось или набрало прочность. На рисунке 4 видно разрушение емкости по ребру жёсткости. В данном случае это стало следствием нарушения технологии намотки, что, вполне возможно, сопровождалось использованием смолы с высоким пиком экзотермы. При намотке и отверждении ребра жесткости произошло повышение температуры выше температуры тепловой деформации (HDT) уже отвержденной смолы, из которой изготовлено тело ёмкости. Это привело к её термической деформации и потере прочности, в результате чего, при нагрузке ёмкость лопнула как раз по ребру жёсткости.
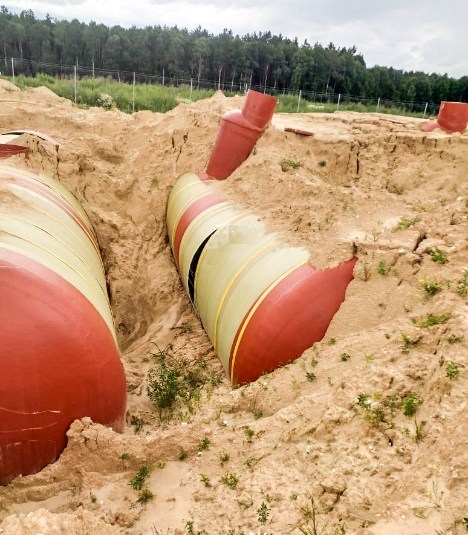
Рисунок 4. Разрушение ламината по ребру жесткости
При реализации проекта не надо смотреть на стеклопластик как на дешевый материал. Надо в первую очередь смотреть на него как на долговечный композит, способный длительное время сохранять свои потребительские и физико-механические характеристики. Его конкурентное преимущество не в первоначальной цене, а в стоимости жизненного цикла. И хорошо, когда грамотно подобрав сырье, удается предложить заказчику высококачественное изделие по конкурентной цене.
И тут мы подошли к вопросу критериев выбора исходных смол для производства изделий из композитов.
Как уже отмечалось выше, подбор смолы начинается со свойств конечного изделия. То есть путем проецирования требуемых значений характеристик готового изделия на свойства отвержденной смолы, осуществляемого параллельно с подбором соответствующего стеклонаполнения. Например, нужно твердое изделие — у смолы смотрим показатель твердости. Нужна эластичность готового изделия — обращаем внимание на удлинение при разрыве. Необходима высокая стойкость к воде и жидкостям — смотрим на показатель водопоглощения (желательно в разрезе 2–3 дней). Стоит задача изготовить пожаробезопасное изделие — смотрим показатели горючести и так далее.
Хочу отметить, что значение каждого показателя, указанное в технических характеристиках смолы, должно быть подтверждено производителем связующих результатами испытаний не только в собственных, но и в независимых аккредитованных лабораториях. Только тогда можно гарантировать качество смолы и стабильность ее показателей.
Ну а теперь перейдем, с моей точки зрения, к самому главному фактору подбора смолы — технологичности связующего, возможности его переработки с помощью заданной для производства конкретного изделия технологии. Это как раз и определяет экономическую составляющую — финансовую отдачу от изготовления изделий из стеклопластика.
В первую очередь обратим внимание на технологии производства изделий из композитов:
- ручное формование;
- напыление;
- намотка;
- литье;
- закрытое формование: RTM, LRTM, Flex Molding, инфузия;
- холодное прессование;
- горячее прессование: SMC, BMC;
- пултрузия.
Есть смолы общего применения (назначения). Обычно это непредускоренные, со средними характеристиками неотверждённой смолы материалы. Которые могут быть переработаны с помощью широкого ряда технологий, или модифицированы добавлением специальных добавок, улучшающих те или иные их свойства, необходимые для конкретного способа производства изделий. Например, добавив в смолу общего применения для литья искусственного камня специальные добавки, которые увеличивают способность смолы к поглощению наполнителя и облегчают удаление воздуха из формовочной смеси, мы закономерно получим более дорогой сырьевой материал. Но за счет его лучшей наполняемости сократиться его расход, а за счет более быстрой стадии удаления воздуха уменьшится время производства, и увеличится производительность. В итоге себестоимость конечного изделия из модифицированного продукта окажется ниже, чем у изготовленного из первоначальной простой смолы.
Помимо технологии, для которой подбирается смола, следует обратить внимание на:
- цвет и прозрачность;
- вязкость;
- тиксотропность (коэффициент);
- реакционную способность.
Рассмотрим каждый пункт по отдельности.
Цвет и прозрачность смолы
Порой на данный показатель не обращают внимания. Но более прозрачная смола и низкий показатель цветности по Хайзену означает, что смола получена по более современным технологиям с минимальным окислением в процессе поликонденсации. Это гарантирует стабильность показателей при хранении смолы, а также возможность более длительного ее хранения.
Вязкость
Часто показатель вязкости путают или сопоставляют с тиксотропностью. Это совершенно разные характеристики, отвечающие за разные свойства и возможности связующего. Смола может быть очень вязкая, но при этом нетиксотропная, и наоборот. Показатель вязкости нам дает представление о текучести смолы. На этот фактор мы обращаем внимание после определения технологического процесса изготовления детали. Например, при технологиях закрытого формования нужно связующее с низкой вязкостью, а для напыления — желательно не выше 1000 мПа•с. Хочу отметить, что существуют различные методики оценки вязкости, даже по Брукфильду есть множество способов ее определения. В Российской Федерации действует ГОСТ 25271, основанный на международном стандарте ИСО 2555, по определению вязкости. И я рекомендую придерживаться методики, регламентированной в нём.
Тиксотропность
Тиксотропность — это способность смолы изменять вязкость при механическом воздействии. Этот показатель означает, что смола в спокойном состоянии быстро набирает вязкость. Тиксотропность характеризуется коэффициентом тиксотропности. Для смол, применяемых в ручном формовании, он должен составлять 2,5. Это гарантия того, что смола не будет стекать с вертикальных поверхностей после нанесения.
Реакционная способность
Реакционная способность характеризуется целым набором показателей, включающим:
- время гелеобразования;
- температуру пика экзотермы;
- время достижения пика экзотермы;
- производный показатель — соотношение времени достижения пика экзотермы к времени гелеобразования.
Реакционная способность смолы напрямую влияет на производительность труда. И это не только гелеобразование, которое показывает, сколько времени есть у производителя для пропитки материалов. Но еще и такой немаловажный показатель — как время достижения пика экзотермы, который характеризует время, через которое начнется набор прочности. Сам процесс набора прочности ламината и его продолжительность зависят от многих факторов, в том числе и от присутствия в смоле функциональных добавок. Соотношение времени достижения пика экзотермы к времени гелеобразования — это расчетный показатель, характеризующий реакционную способность смолы, значение которого должно быть ≤ 2.
Отдельно остановлюсь на температуре пика экзотермы. Высокий пик экзотермы (190–200°С) означает, что экзотермическая реакция может начаться и в малых объемах, и при пониженных температурах, и может быть предвестником быстрого отверждения. Это хорошо при изготовлении тонких деталей и применении технологий литья и закрытого формования. При ручном формовании есть небольшое условие —
четкое и равномерное перемешивание смолы с перекисью. Иначе может возникнуть точечное и резкое увеличение пика экзотермы, что в свою очередь приведет к нежелательной усадке и короблению видовой поверхности ламината. Причем производить изделия желательно толщиной не более 5 мм, иначе могут возникнуть проблемы с матрицами, когда при высоких температурах матрица дает усадку и изменяет геометрию. При намотке же наоборот: высокий пик экзотермы просто не технологичен, так как с такой смолой невозможно будет за раз набрать толщину изделия более 10 мм, ламинат просто «закипит», не говоря уж о намотке ребер жесткости на больших емкостях. В то же время необходим комплексный подход и при выборе смолы с низким пиком экзотермы. Наряду с низким пиком смола должна быть реактивной, и производный показатель соотношений времен должен обязательно быть ≤ 2. Смола с такими показателями достигается при усовершенствовании рецептур и синтеза.
Все рассмотренные выше характеристики являются основными, определены международными стандартами и указываются в технической документации к продукту. Но у смол есть еще такие свойства, как:
- текучесть — способность смолы в наполненном состоянии растекаться вместе с наполнителем. Этот показатель очень важен для технологий литья искусственного камня и полимербетона;
- наполняемость — способность к наполнению. Также важная характеристика для литьевых процессов, когда меньшее количество смолы необходимо для пропитки большего количества наполнителя;
- пропитывающая способность, которая напрямую влияет на скорость пропитки армирующих стекломатериалов, а, следовательно, и на производительность;
- стойкость к атмосферным воздействиям и ультрафиолетовому излучению;
- способность к быстрой дегазации — выводу воздуха из ламината. Данное свойство влияет на качество и срок службы изделия, так как оставшиеся воздушные включения в стеклопластике могут привести к его осмосу и разрушению.
Эти характеристики достигаются не только с помощью модернизации рецептур и технологий синтеза смол, но и введением дополнительных функциональных добавок, которые в свою очередь имеют прямое влияние на увеличение цен на конечный продукт.
К сожалению, данная группа свойств не отражается в технических листах на смолы, но именно эти показатели помогут производителю изделий из стеклопластика и искусственного камня рассмотреть вопрос выбора сырья наиболее полно, грамотно учитывая все производственные нюансы. А сделанный правильный выбор исходных материалов — это основа, которая в совокупности с другими факторами, позволит оптимизировать процесс производства, увеличить производительность и изготовить высококачественную, соответствующую всем предъявляемым к ней требованиям продукцию с конкурентной ценой.
В заключение добавлю, что ООО «Полимерпром» это ответственный производитель и поставщик исходных сырьевых компонентов для изготовления композитов и изделий из них. Всегда готов предоставить клиентам самую полную информацию о предлагаемых продуктах, провести необходимые консультации и подобрать решение для любой производственной задачи. Еще раз призываю компании композитной отрасли Российской Федерации относиться как к выбору сырья, так и к производству в целом с максимальной ответственностью. Ведь от качества произведенных изделий во многом зависит вопрос расширения применения композитов в различных отраслях промышленности. Для развития композитной отрасли необходимы усилия всех участников рынка. Даже из-за одного некачественного изделия можно в один момент потерять достигаемое с таким трудом доверие потребителей. Давайте строить «композитное» будущее вместе!