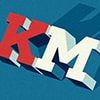
Соединительный элемент для композита и стальной конструкции
рубрика: материалы
Традиционно судостроительная отрасль сфокусирована на стали. Тем не менее наблюдается тенденция по замене стали легковесными материалами с целью увеличения грузовой нагрузки и уменьшения потребления топлива. Но здесь существуют особые требования по технологии стыка. Центр морских технологий и SLV Mecklenburg-Vorpommern разработали новое соединение композита/стали для судостроения.
Аэронавтика прокладывает путь
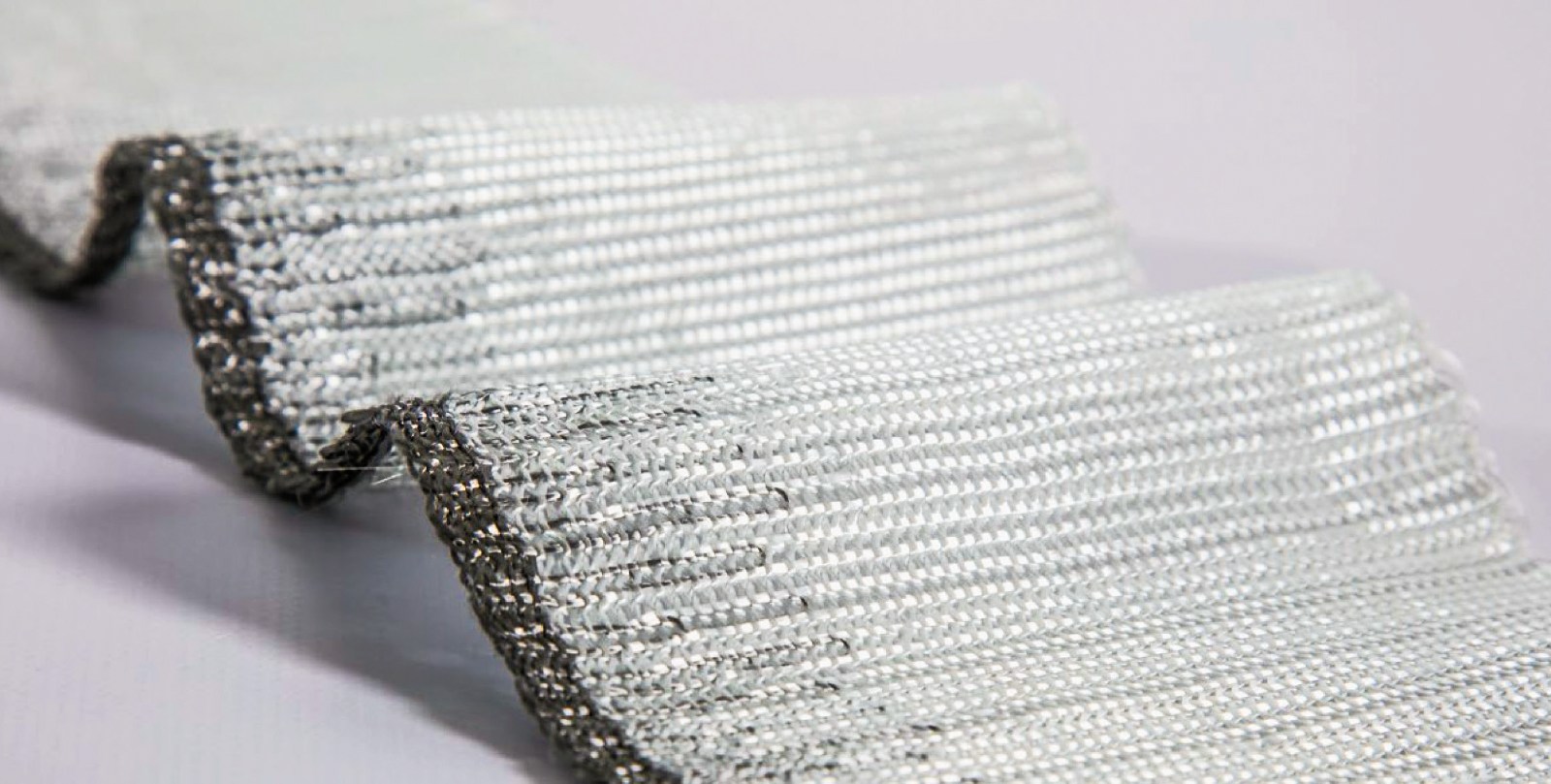
Легковесный дизайн подвижных структур включает в себя многочисленные преимущества: чем меньше будет масса конструкции для ускорения и перевозки, тем меньше будет потребление топлива, меньше транспортные расходы и меньший углеродный выброс. В некоторых случаях целью легковесной конструкции является улучшение эксплуатационных характеристик, таких как повышенная грузоподъёмность или больший диапазон. Кроме того, побочные эффекты снижения веса не являются незначительными. Меньший вес конструкции может привести к меньшим двигателям, что, в свою очередь, может привести к дальнейшему снижению веса. Существуют два различных подхода к снижению веса конструкции. Во-первых, применение принципов легковесного проектирования, таких как использование упрочненных кожей конструкций, и, во-вторых, замена материала, например, замена стали на композиты.
Аэронавигационная отрасль лидирует в сфере замены материалов. Когда в восьмидесятых годах Airbus разработал A320, на алюминиевые сплавы приходилось около 65% веса конструкции, тогда как новый A350 состоит только из 20% алюминиевых сплавов. Доля композитов, напротив, увеличилась с 13% до 53%. Аналогичная тенденция комбинирования различных материалов и более широкого использования армированных волокном полимеров (FRP) также наблюдается в железнодорожной и автомобильной промышленности.
Судостроение
Похоже, что одним из секторов, в котором так активно не учитывается тенденция к легкому проектированию и замене материалов, является гражданское судостроение. С другой стороны, на долю мирового судоходства приходится примерно 4,5% глобальных парниковых газов. По сути, контейнеровозы, танкеры и круизные лайнеры изготовлены из стали, а их конструкция сварена из более мелких стальных элементов.
Этот факт довольно удивителен, так как индустрия строительства лодок и яхт была пионером в применении композитных деталей в промышленно развитом секторе производства. Например, процесс Scrimp (разновидность вакуумной инфузии), разработанный в судостроительной промышленности, используется модифицированным образом для изготовления заднего гермошпангоута Airbus A380.
Можно найти несколько примеров успешного внедрения FRP (стеклопластика), например, шведские корветы класса Visby, показывающие, что возможно и выгодно использовать новые материалы в судостроении.
В настоящее время ветер перемен дует в судостроительной промышленности Европы, где производятся, прежде всего, специальные и круизные суда. Несколько верфей рассматривают возможность внедрения стеклопластика на судах разных типов.
Причинами применения легковесных материалов в судостроении, помимо потребления топлива, являются лучшее соотношение полезной нагрузки к конструктивному весу или уменьшение тяги. Это может открыть новые морские пути или, в случае речных круизных судов, продлить сезон. Дополнительной причиной является повышенная стабильность благодаря более низкому центру тяжести.
Несмотря на преимущества FRP, они не используются широко в судостроительной промышленности по трем причинам:
Суда представляют собой сложные конструкции, которые могут стоить от 400 до 800 миллионов евро, например, в случае круизных судов. Штрафные сборы за неисполнение обязательств являются стандартом в отрасли, что означает, что задержки могут означать миллионные штрафы.
Как правило, производимые подобные судна являются единственными в своем роде, что означает, что любое новшество должно финансироваться судном, на котором оно внедряется.
Правила и нормы являются строгими и консервативными, судна в международных водах должны проектироваться в соответствии с правилом ММО «Безопасность жизни на морях — Солас».
До недавнего времени единственным разрешенным конструкционным материалом из-за правил пожарной безопасности была сталь. Недавние изменения в правилах позволяют использовать стеклопластик при условии, что эквивалентная безопасность доказана.
Примером, демонстрирующим потенциал стеклопластика в судостроительной отрасли, является автомобильный перевозчик Siem Cicero, произведенный хорватской верфью Uljanik. На этом корабле три верхние палубы были заменены на стеклопластиковую конструкцию, что привело к снижению веса на 25% на этом участке.
Технология стыка/соединения
Поэтому, будущее судостроения — это сочетание стали и других материалов, таких как стеклопластик, поскольку нет смысла менять всю стальную конструкцию на стеклопластик. Это связано с техническими и экономическими причинами. Таким образом, технология соединения является ключевым фактором при использовании стеклопластиковых конструкций на верфях. Обычные способы соединения металла и FRP — это склеивание или скрепление болтами. Однако их нельзя применять непосредственно в судостроительной промышленности, где предпочтительным способом соединения является сварка. Типичные допуски в судостроении усложняют создание необходимых отверстий. Кроме того, минимальная толщина в 5 мм, основанная на правилах, усложняет одновременное изготовление отверстий в стали и стеклопластике. Один из аргументов против склеивания заключается в том, что суда, как правило, изготавливаются в неконтролируемой среде, а это означает, что конструкция подвергается изменениям температуры и влажности. Кроме того, склеивание — это трудоемкий и дорогостоящий процесс одобрения в судостроительной промышленности.
Стандартный коннектор для композита и стали
Целью немецкого проекта Fausst (Faser und Stahl Standard Verbindung (Стандартное соединение волокна и стали) стала разработка соединителя в соответствии с потребностями судостроительной промышленности, используя как композит, так и сталь, что соответствует правилам судостроения и не требует дополнительных специализированных этапов производства на верфи. На рисунке 1 показана технология соединения.
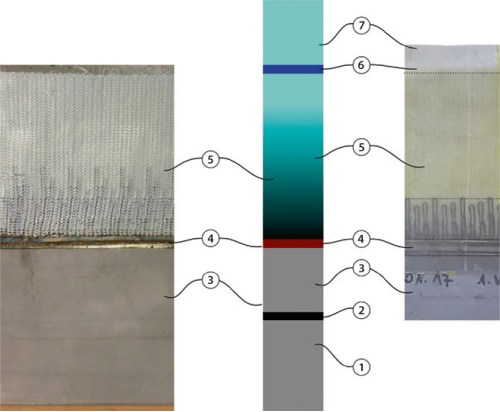
Рисунок 1. Соединение FAUSST: в незаламинированном состоянии (слева), схематически (посередине) и в заламинированном состоянии (справа). 1 — стальная структура, 2 — сварной шов, 3 — плоская сталь, 4 — сварной шов, 5 — полотно Fausst, 6 — переход в структуру Fausst, 7 — композитная структура
Доработки и изменения являются стандартными процедурами на верфях: металлические детали обрезаются до конечных размеров или допусков непосредственно на верфи. Сварка — нормальный процесс соединения. В противоположность, в случае деталей из термореактивных композитов, возможны только незначительные изменения.
Однако для обеспечения рентабельности и технологичности соединительный элемент должен уметь справляться с этими стандартными процессами на верфи. Разработанный полуфабрикат отвечает всем требованиям. Fausst состоит из металлического соединительного элемента, например плоского стержня, на который приварен один или несколько гибридных тканей. Эти гибридные ткани интегрированы в производство стеклопластика методом ламинирования и инфузии. После отверждения получается стеклопластиковая деталь со стальным краем. Этот стальной край затем может быть адаптирован к конструкции судна и приварен к нему с использованием обычных технологий судостроения.
Производство полуфабриката
На рисунке 2 показаны различные этапы производства, наблюдаемые при производстве полуфабриката. Первым шагом является создание текстильной части полуфабриката. В сотрудничестве с Fritz Moll Tex¬tilwerke был разработан гибридный трикотажный материал, который с одной стороны изготовлен из 100% стальных волокон, а с другой — из 100% стекловолокон.
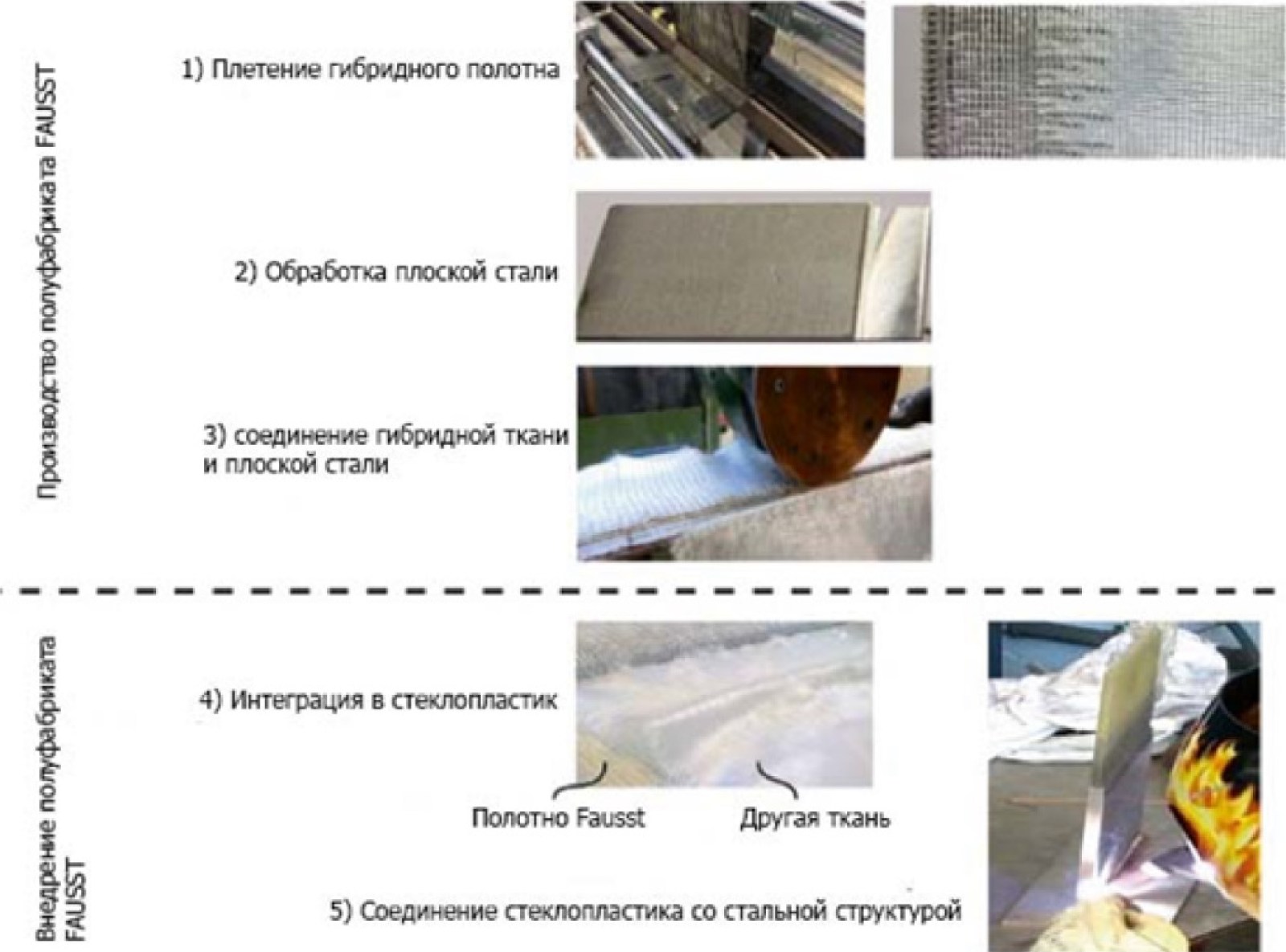
Рисунок 2. Этапы производства Fausst.
Каждый слой состоит из пяти различных типов нити, которые удерживаются между собой с помощью прошивной нити. Этими нитями являются три нити по основе и две прошивные — по утку. Нити для укладки и основы находится в направлении ширины текстиля. Каждая прошивная и по основе нить представляют собой одиночную нить, тогда как нить по утку является непрерывной. Следовательно, для ткани длиной приблизительно 150 мм требуется 60 прошивных и 180 нитей по основе и только шесть различных нитей по утку, поскольку они не покрывают всю длину ткани и изготовлены из стальной и стеклянной пряжи. Этот эффект приводит к соединению и перекрытию стальных и стеклянных волокон, что, в свою очередь, приводит к переносу нагрузки из-за трения, а также благодаря взаимодействию в точках пересечения. Производственный процесс осуществляется с помощью вязальной машины с электронным управлением, которая обеспечивает скорость производства до 100 м/ч. В представленном случае использовалась стандартная машина Comez Decortronic 1000EL, которая обычно используется в текстильной промышленности для производства лент. В настоящее время производится плоский текстиль с одной металлической стороной. Однако конструкция является адаптивной и может также изготавливаться с использованием кругловязальной машины.
Следующим этапом является проектирование металлического соединительного элемента. Необходимо учитывать четыре принципа:
- Расстояние между частью стеклопластика и местом соединения должно быть достаточно большим, чтобы предотвратить повышение температуры на участке стеклопластика выше 50°C, которая может быть при сварке ее к стальной структуре. Необходима минимальная длина.
- Данный соединительный элемент позволяет работать с ним на последующем этапе, например, при укладке его к поверхности.
- Любое напряжение на волокна должно быть распределено вдоль линии волокон, сводя к минимуму волнистость.
- Нагрузка и нейтральная ось должны быть совмещены. Таким образом, могут быть разработаны различные геометрии соединений, что позволяет соединять монолитные или многослойные (сэндвич) детали с металлической структурой (рисунок 3).
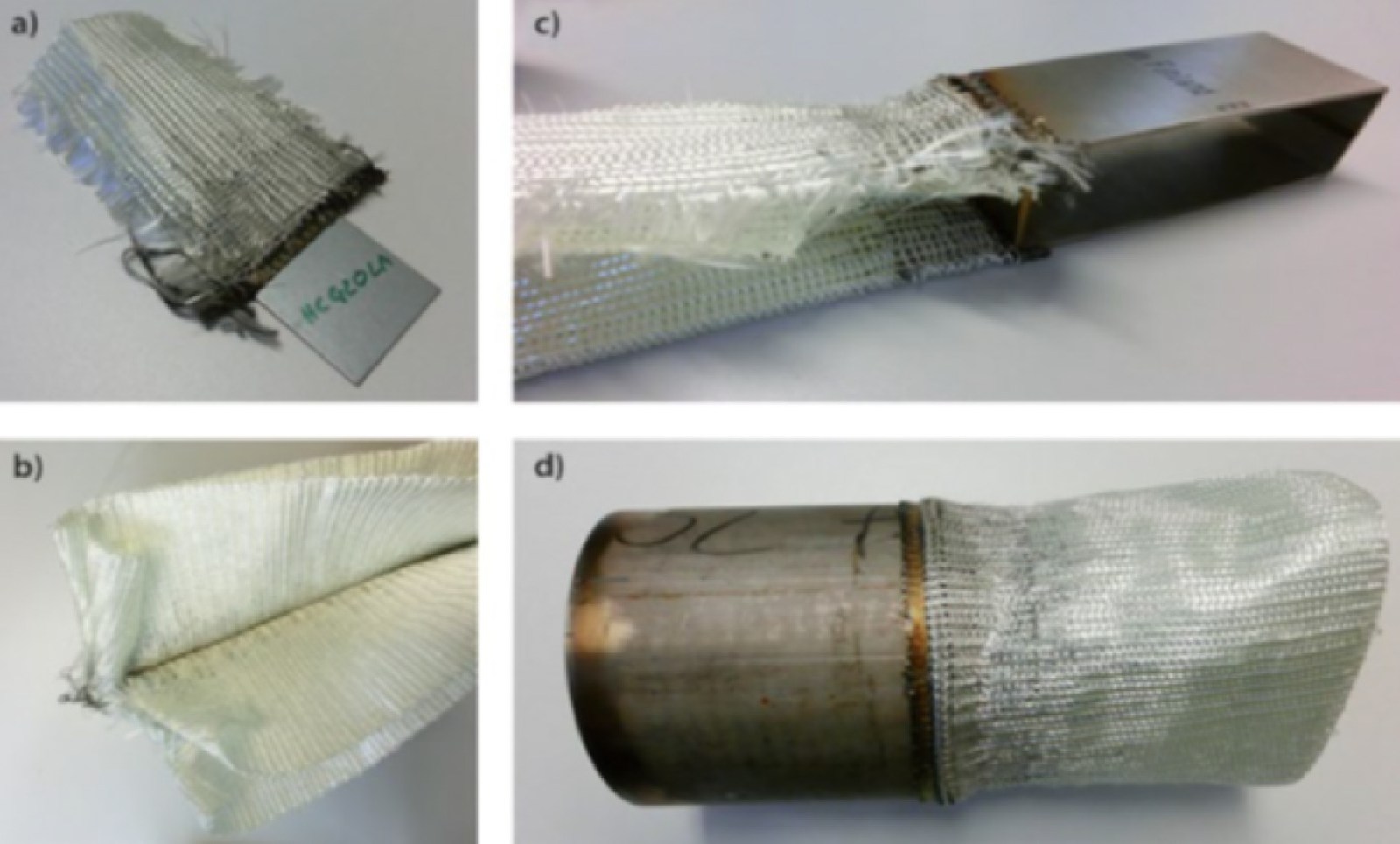
Рисунок 3. Примеры геометрии стыка: плоский коннектор различной толщины, материалов и количества слоев Fausst (a и b), профиль «коробочного» типа (с) и круглый профиль с приваренными слоями Fausst (d).
На последнем этапе один или несколько слоев гибридного плетеного материала соединяются с соединительным элементом посредством контактной сварки. Этот процесс позволяет эффективно изготавливать соединители Fausst с несколькими слоями ткани, используя надежный и хорошо известный процесс.
Идея этого проекта заключалась в попытке интегрировать детали, изготовленные специализированными производителями, такие как стеновые панели и каюты, в судно с использованием облегченной конструкции и сварки непосредственно на верфях. В других возможных случаях применения, например, в автомобильной промышленности, металлические детали могут быть первоначально соединены сваркой с гибридным текстилем, а затем может быть произведен композит на следующем этапе. Таким образом, полуфабрикат изготавливается с использованием двух разных стандартных процессов, которые могут быть автоматизированы и пригодны для массового производства.
Применение полуфабрикатов
Полуфабрикат Fausst разработан для таких производственных процессов, как ручная выкладка, формование с переносом смолы (RTM) или вакуумное формование с помощью переноса смолы/инфузии (VARTM), где каждый слой Fausst перекрывается другими слоями стеклопластика для производства непосредственно стеклопластиковой структуры. Затем весь пакет пропитывается смолой. Теоретически, в качестве волокнистого материала можно использовать препрег, если для уменьшения риска пористости также используются клеевая пленка. Затем стеклопластиковая деталь с кромкой Fausst может быть присоединена к стальной детали посредством обычной сварки.
Примеры использования
Как и в аэрокосмической промышленности, одобрение стеклопластиковых конструкций для военных кораблей подчиняется другим правилам, нежели гражданским. Это облегчает применение подобных структур. Например, на верфи Saab Kockums была разработана концепция, согласно которой надстройка фрегатов была заменена сэндвич-конструкцией из стеклопластика. В дополнение к вышеупомянутым преимуществам есть еще преимущество в уменьшенной радиолокационной сигнатуры. Соединение между стальным корпусом и стеклопластиком выполняется с использованием U-профиля, получившаяся суперструктура (стеклопластик-сэндвич) соединяется и затем приваривается к корпусу судна в U-профиле.Такой подход к соединению сравнивается с недавно разработанной системой соединений Fausst. Выбранный соединитель Fausst имеет симметричную двухступенчатую конструкцию с использованием в общей сложности четырех слоев Fausst. В сотрудничестве с Saertex, сэндвич-конструкция была изготовлена с помощью инфузии, рисунок 4.
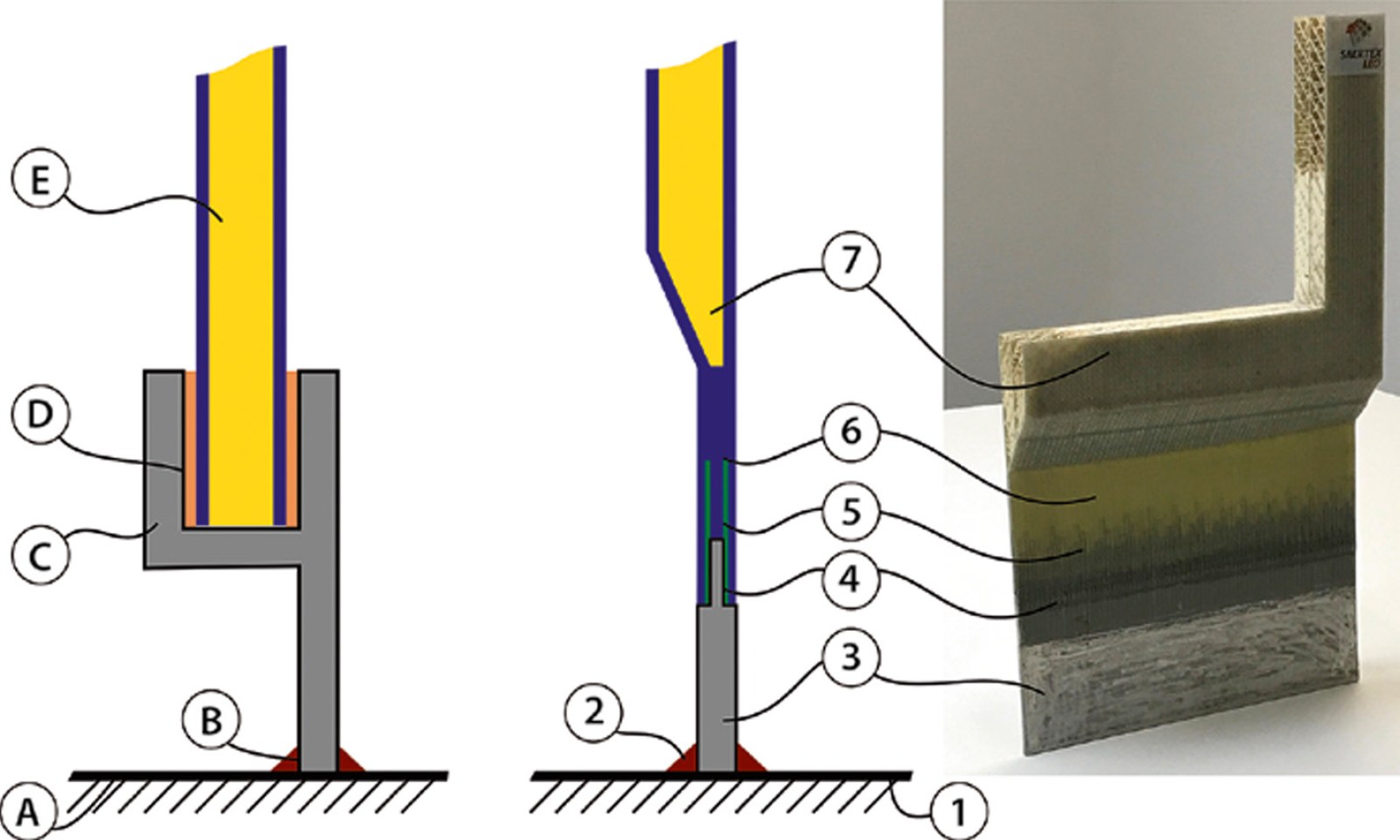
Рисунок 4. Сравнение между U-профилем и сэндвич-структурой Fausst: U-профиль схематично (слева), FAUSST-FRP схематично (посередине) и фото соединителя Fausst (справа). A — Стальная структура, B — Сварной шов, C — U-профиль, D — Адгезивный стык, E — Композит, 1 — Стальная структура, 2 — Сварной шов, 3 — Плоская сталь, 4 — Сварной шов, 5 — Полотно Fausst, 6 — Переход в структуру Fausst, 7 — Композитная структура
При проведении механических испытаний была задача измерить прочность соединяющего элемента, поэтому центр был заполнен гибридной тканью, который действовал в качестве разделителя.
Рисунок 5 показывает диаграмму смещения нагрузки образца растяжения, а также геометрию образца.
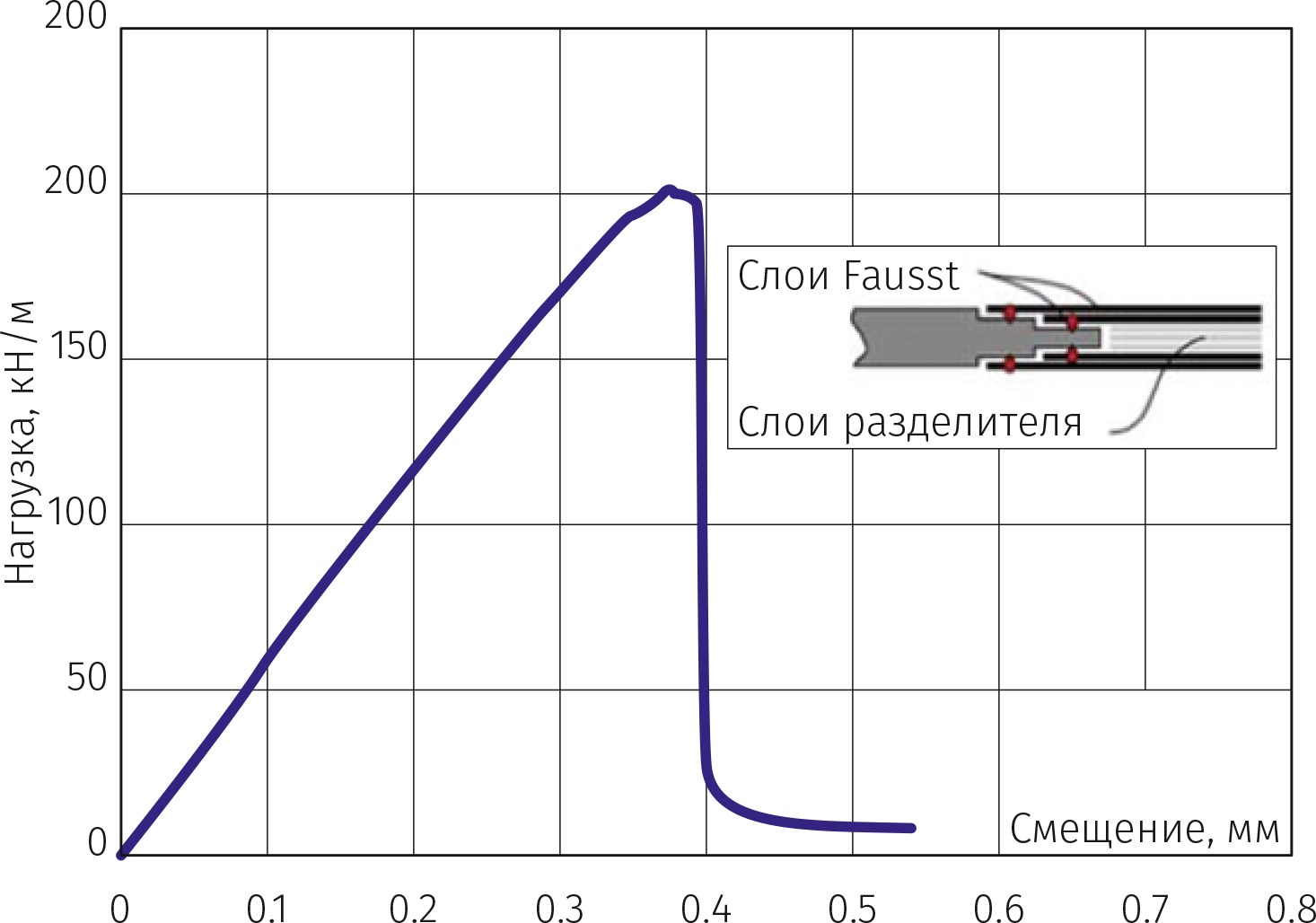
Рисунок 5. Отображение смещения нагрузки и геометрии образца конфигурации Fausst
Из-за геометрии образца невозможно рассчитать прочность, так как поперечное сечение изменяется в сварочном шве. Следовательно, определяется линейная прочность соединения, которая составляет 217 кН/м, имея реальное перекрытие 20 мм. Следует отметить, что ширина сварного шва составляет приблизительно 3 мм. В следующей серии испытаний с использованием биаксиальной ткани между гибридными слоями Fausst были достигнуты предел прочности при растяжении 260 кН/м и предел прочности при сжатии 800 кН/м.
Сравнивая эти значения с адгезивным соединением, достигаются аналогичные значения прочности на разрыв с этим перекрытием для адгезивной системы с прочностью на сдвиг 5 МПа. Это значение соответствует реалистичному значению адгезионного соединения сталь-FRP, если учитывать такие факторы, как старение. Преимущество соединения Fausst по сравнению со склейкой с профилем состоит в том, что используется меньше стали, что приводит к меньшему весу, исключает этап производства (склейка стеклопластика с профилем) и обеспечивает постоянное соединение посредством сварки.
Заключение
Полуфабрикат Fausst устанавливает новую технологию соединения стальных и стеклопластиковых конструкций. Эта технология основана на гибридном текстиле. Растягивающие нагрузки свыше 200 кН/м переносятся 4 слоями сварного текстиля Fausst. Преимущества перед клеевыми или механическими соединениями заключаются в более коротком перекрытии, оптимизированном переносе нагрузки по волокнам и скорости процесса.
Будущая цель команды разработчиков — стандартизация полуфабриката и одобрение в морской отрасли, чтобы дизайнеры могли работать с сертифицированными значениями материалов. Дополнительным преимуществом Fausst является то, что качество полуфабриката контролируется во время производства, а это означает, что во время внедрения необходимо проверять только качество стандартных процессов, таких как ламинирование и сварка.
Первым направлением применения технологии соединения была судостроительная промышленность, однако эта технология соединения также подходит и для других секторов, таких как автомобильная, железнодорожная или строительная промышленность, где необходимо переносить высокие нагрузки, требуются короткие сроки сборки или использование предварительно оборудованных полуфабрикатов.
По вопросам данной технологии просим связываться с нами: +7 (812) 748-23-98.
Статья была опубликована в номере 4 (84) 2019