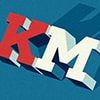
Цифровой двойник производства авиационных конструкций из композиционных материалов
рубрика: материалы
Традиционное проектирование самолета требует создания сотен тысяч чертежей и документов. Проектирование изделий и агрегатов из композитов значительно усложнено наличием большого количества дополнительных параметров конструкции. Эти параметры невозможно контролировать без использования инструментов цифрового проектирования.
1. Цифровое проектирование
Цифровое проектирование, в основе которого лежит электронная модель изделия, делает возможным отказ от выпуска чертежей и значительно уменьшает бумажный документооборот, что приводит к сокращению сроков выпуска продукции. Инструменты цифрового проектирования предоставляют инженерам наглядное описание изделия и его свойств, а единое хранилище цифровых данных об агрегате служит источником актуальной информации и исключает дублирование и работу с устаревшими данными.
Полимерные композиционные материалы (ПКМ) по сравнению с традиционными обладают меньшей массой и более высокими прочностными характеристиками. Процесс проектирования, однако, становится более сложным, поскольку при разработке инженеру необходимо постоянно уделять внимание огромному количеству параметров изделия, связанных между собой и оказывающих взаимное влияние друг на друга. Эти параметры связаны со спецификой самих материалов: главное направление армирования, количество слоев материала, их границы, идеализированная и реальная ориентация армирующего волокна каждого слоя и другие. В процессе проектирования должны учитываться особенности технологического процесса производства изделия из ПКМ, так как они оказывают значительное влияние на ключевые геометрические и механические свойства конечной детали.
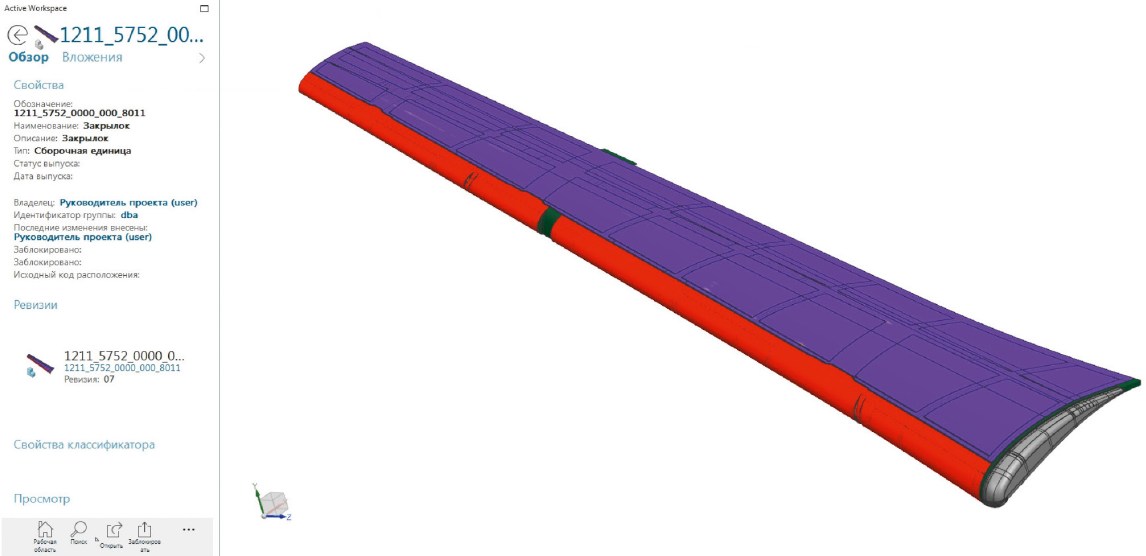
Общий вид модели закрылка из композиционных материалов: атрибуты изделия и 3D-модель
Процесс цифрового проектирования, основанный на ведущих мировых подходах «Цифровой двойник» и «Цифровая связь», начинается с определения поверхности композиционного пакета, в большинстве случаев совпадающей с поверхностью выкладочной оснастки при последующем производстве, и главного направления армирования. С помощью инструментов цифрового проектирования инженер определяет свойства различных зон детали, варьируя их толщину и меняя углы армирования материала в зависимости от предполагаемых нагрузок, моделирует поведение детали в различных эксплуатационных условиях, получая оптимальную по массе конструкцию, удовлетворяющую всем необходимым требованиям. Программный и визуальный контроль на всех стадиях разработки позволяет избежать критических ошибок, приводящих к увеличению сроков проектирования и значительному удорожанию изделия. Инструменты цифрового проектирования помогают автоматизировать многие этапы разработки, такие как получение послойной конструкции на основе зонного описания, внесение изменений и обновление конструкции в процессе ее оптимизации и прочие. Реализация подхода «Цифровой двойник» в процессе разработки предполагает учет влияния технологических факторов на свойства изделия, сводя к минимуму расхождение характеристик модели и конечного продукта. По окончании оптимизации конструкции инженер выпускает конструкторскую документацию, представленную в виде модели, оформленной согласно стандартам выпуска и обмена цифровыми данными об изделиях из композиционных материалов. Такое представление обеспечивает эффективный обмен данными об изделии как между различными службами внутри предприятия, так и между предприятием-разработчиком и внешними поставщиками.

Контуры слоев композиционного материала
Используемый подход «Цифровая связь» предполагает значительное сокращение сроков внесения изменений при необходимости выпуска новых версий конструкторской документации, обусловленных корректировкой требований к изделию. Учет нюансов композиционного производства на ранних стадиях проектирования упрощает передачу изделия на этап технологической подготовки производства, а сама конструкторская документация в цифровом виде служит основой для проведения полноценной технологической подготовки и создания программ для современного оборудования с числовым программным управлением.
2. Технологическая подготовка производства
Цифровое производство является одним из наиболее важных этапов подготовки серийного производства изделий авиационной отрасли. Здесь осуществляются технологическое нормирование, виртуальная пусконаладка производственного оборудования, определяется пропускная способность существующих мощностей, потребность в дополнительных ресурсах, решаются задачи оптимизации производства под заданную номенклатуру и анализируются различные сценарии внесения изменений в производственный план.
Построение «Цифрового двойника» композиционного производства начинается с разработки технологического процесса производства изделия, в рамках которого описывается маршрут перемещения изделия между цехами, расчитываются необходимые для производства материалы и ресурсы, готовятся данные для оборудования с ЧПУ — раскройные плоттеры, лазерные проекторы, многоосевые обрабатывающие центры, а также выпускаются электронные рабочие инструкции. Технологический процесс производства композиционного изделия состоит из набора последовательных операций, таких как ручная выкладка, формование, механообработка. Каждая из операций насыщается соответствующими переходами или действиями, на основе которых создаются последовательные интерактивные инструкции для рабочих и контролеров цехов. Расчет ресурсов и материалов основывается на цифровых данных конструкторской документации: расходы основных материалов определяются в модели еще на этапе Цифрового проектирования, а расходы вспомогательных материалов автоматически рассчитываются при помощи инструментов Цифрового производства. Благодаря подходам «Цифровой двойник» и «Цифровая связь» все конструкторские данные, с которыми связан технологический процесс, в каждый момент времени носят актуальный характер. При этом все инженеры-технологи, данные которых затронуты конструкторскими изменениями, получают оповещения с указанием действий, необходимых для обновления данных цифрового двойника производства, в результате чего поддерживается высокая степень актуальности самого цифрового двойника. Это помогает избежать традиционных проблем с использованием устаревшей документации на производстве и ведет к сокращению количества случаев незапланированного ремонта и брака, а, в конечном счете, к повышению качества продукции, выполнению установленных производственным планом сроков и сокращению издержек.
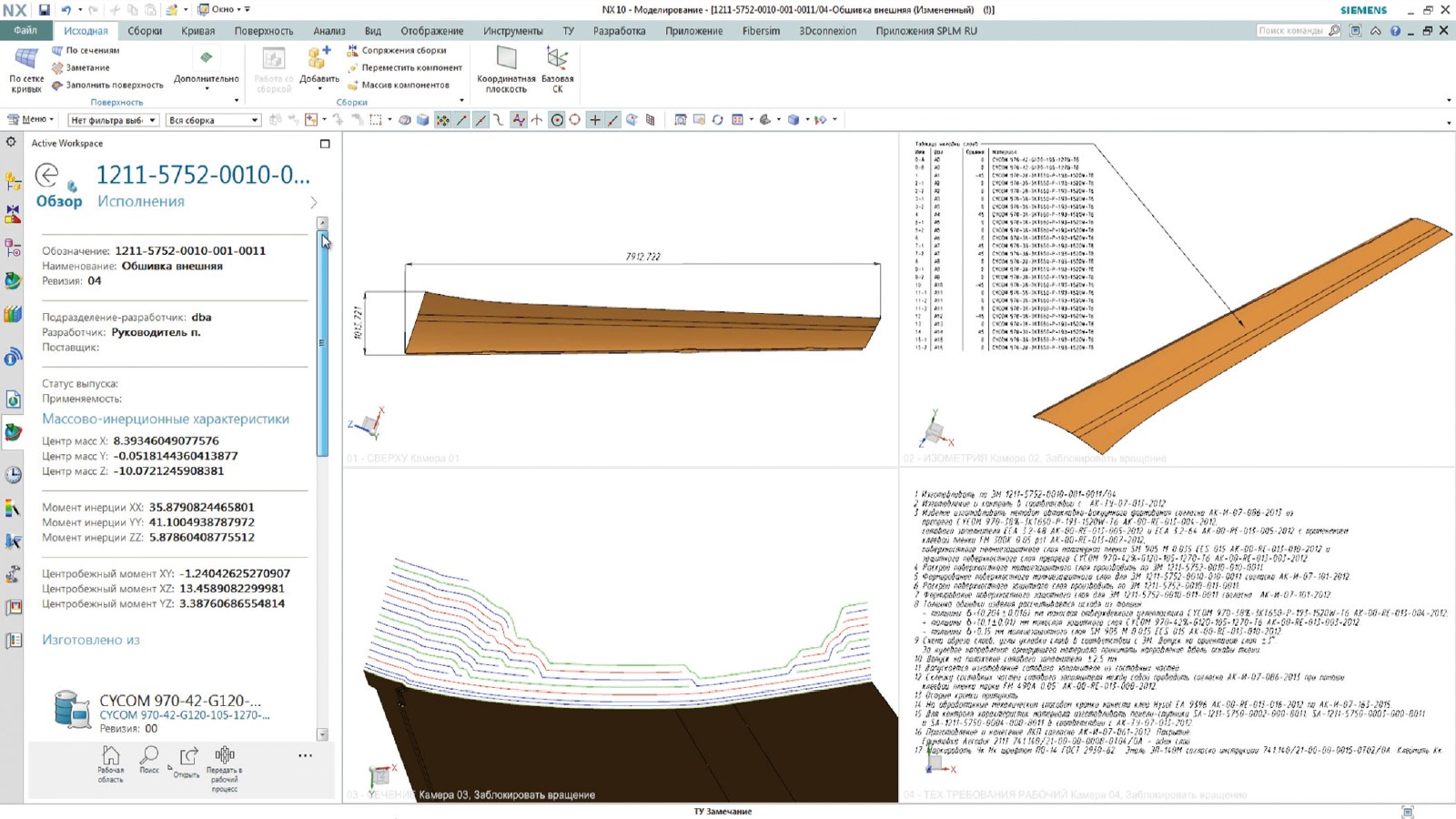
Рабочая конструкторская документация в цифровом виде
В технологическом процессе подготовки производства одной из ключевых и самых ресурсоемких задач является разработка управляющих программ (УП) для оборудования с программным управлением. В традиционном подходе технолог-программист должен увязать между собой геометрию детали и оснастки, параметры режущего инструмента и режимы резания, а также учесть особенности программирования стойки с ЧПУ, кинематику работы станка. Все это занимает длительное время и требует отладки УП непосредственно на оборудовании в цехе.
Подход Цифрового производства в виде «Цифрового двойника» механической обработки на станке ЧПУ предполагает единый процесс расчета траектории движения инструмента с последующим моделированием и отработкой программы — виртуальном аналоге обработки. Применяемые инструменты позволяют получать всю необходимую информацию о детали (геометрия, материал, технические требования), оснастке, инструменте, оборудовании в одной среде, тем самым сокращая время работы. Современные алгоритмы расчета траекторий движения инструмента, удобство и эргономика работы существенно ускоряют весь процесс, что приводит к значительному сокращению времени подготовки производства и своевременному обеспечению цехового оборудования с ЧПУ управляющими программами, позволяющими получить годную деталь с первого раза.
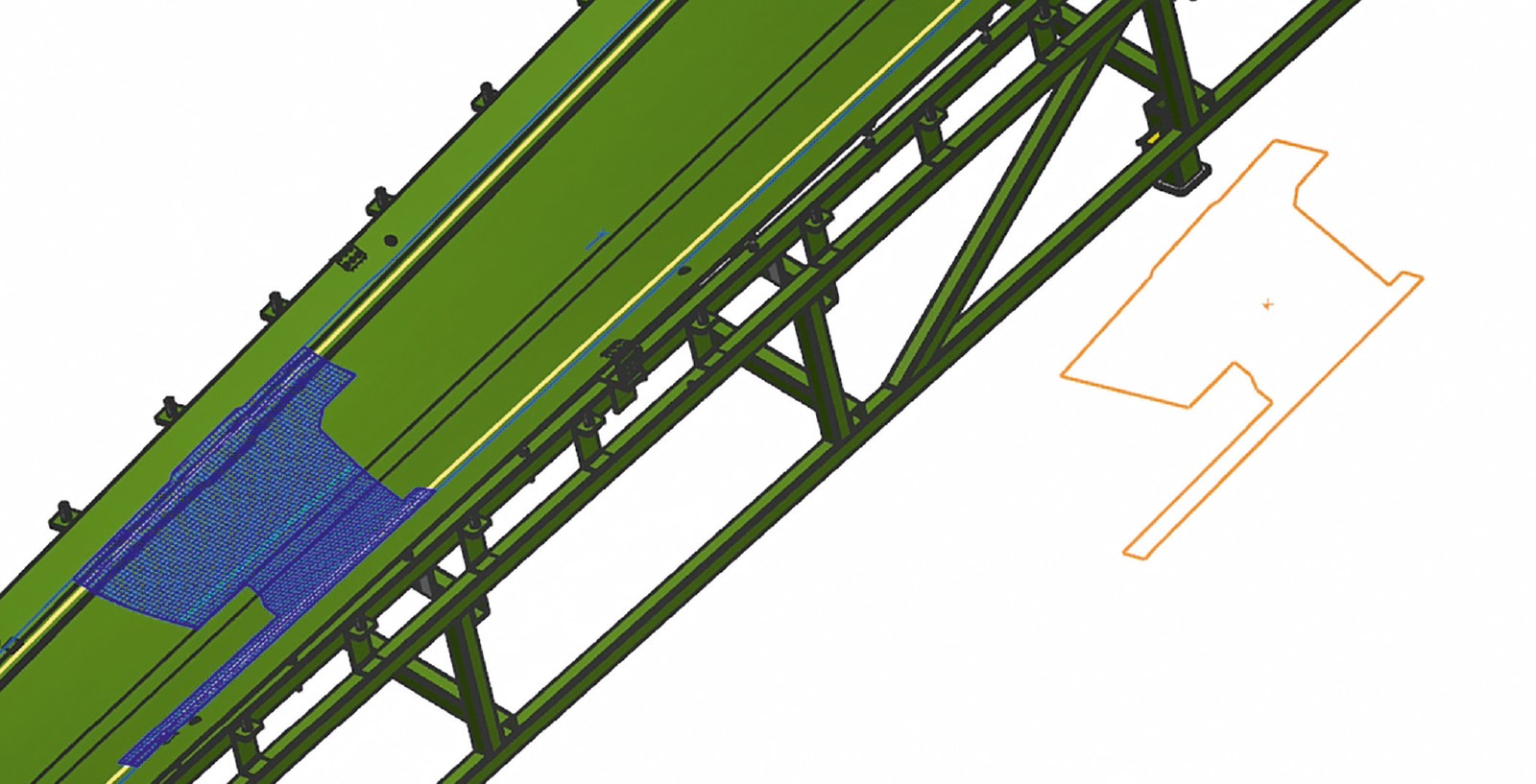
Моделирование укладки слоя композиционного материала на оснастку и развертка слоя
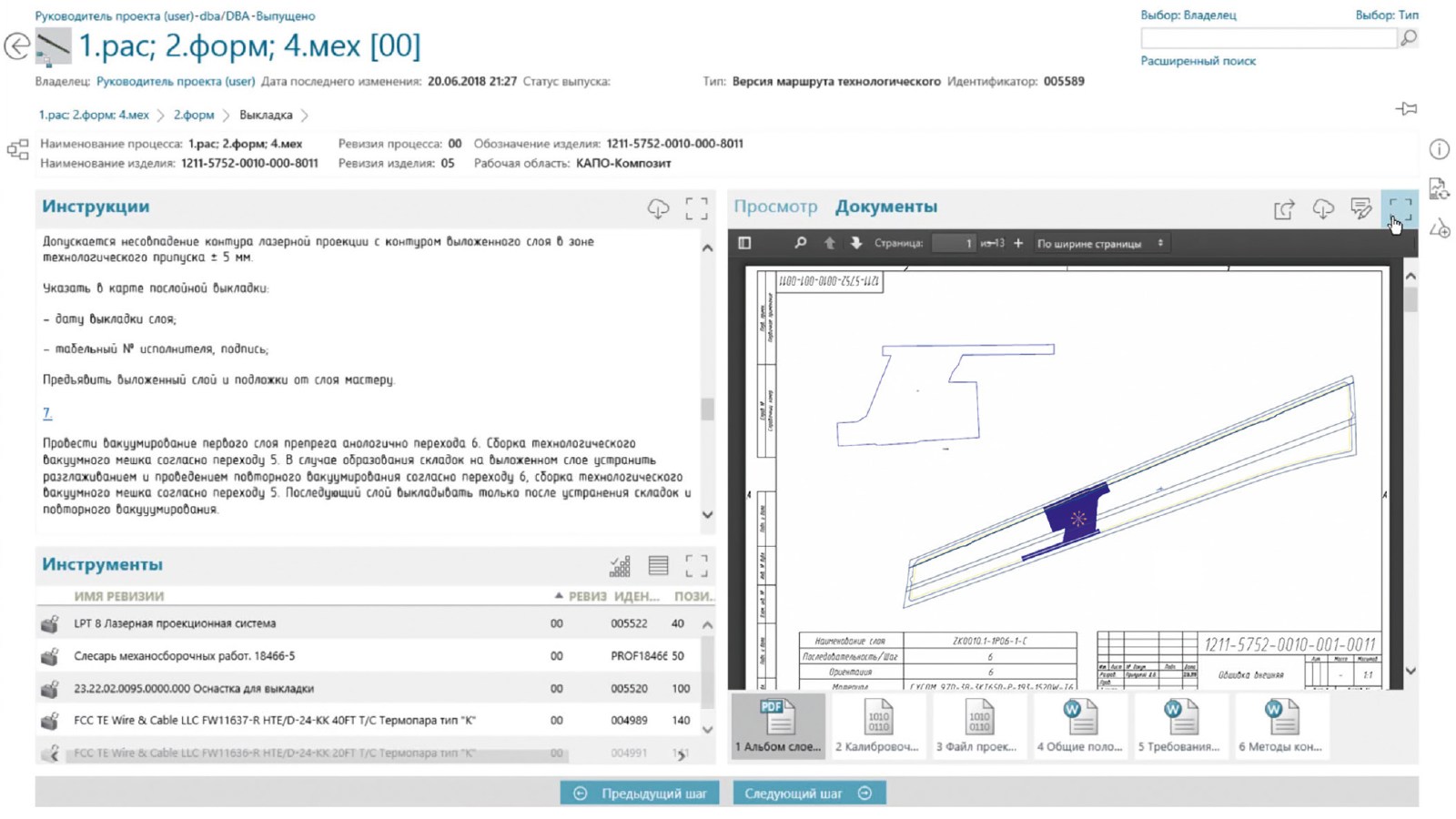
Пошаговая электронная инструкция рабочего цеха
Сложность геометрии деталей, разнообразные и сложно прогнозируемые обычными способами перемещения элементов оборудования требуют обязательного контроля качества разработанных управляющих программ — симуляции. Для этого в проект обработки добавляется «Цифровой двойник» оборудования, и осуществляется полностью идентичная реальной настройка среды изготовления детали. Такой подход обеспечивает выявление возможных ошибок в обработке детали (снятие лишнего объема материала или, наоборот, его остатки, столкновения), исключает необходимость отладки на оборудовании и снижает сроки и стоимость подготовки производства. В случае выявления ошибок или столкновений режущего инструмента с технологической оснасткой специалист оперативно вносит корректировки, а также оптимизирует управляющую программу по заданному критерию, например, по машинному времени или количеству смен инструмента. Это дает дополнительную гибкость и способствует реализации поставленной цели: снижению себестоимости, повышению пропускной способности производства.
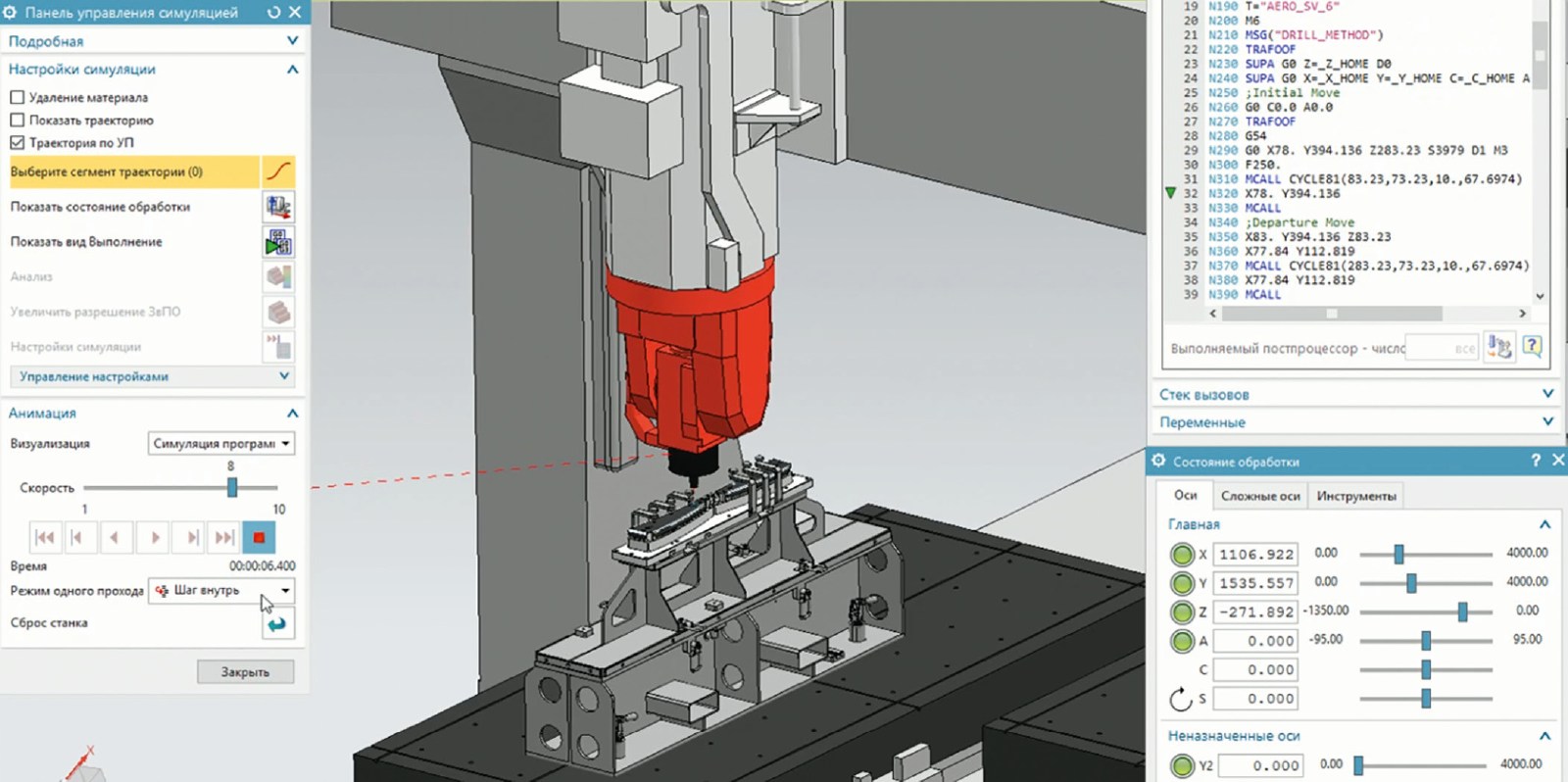
Моделирование механообработки композиционной нервюры на станке с ЧПУ
По окончании процесса расчета и симуляции специалист получает полностью готовую к внедрению УП, не содержащую ошибок.
Применение «Цифрового двойника» механической обработки на станках с ЧПУ позволяет сократить цикл времени, необходимый на внедрение и изготовление годных деталей, точно спрогнозировать требуемое время для обработки, снизить потери времени при работе оборудования с ЧПУ, снизить и даже полностью исключить несоответствия при изготовлении деталей на станках с ЧПУ.
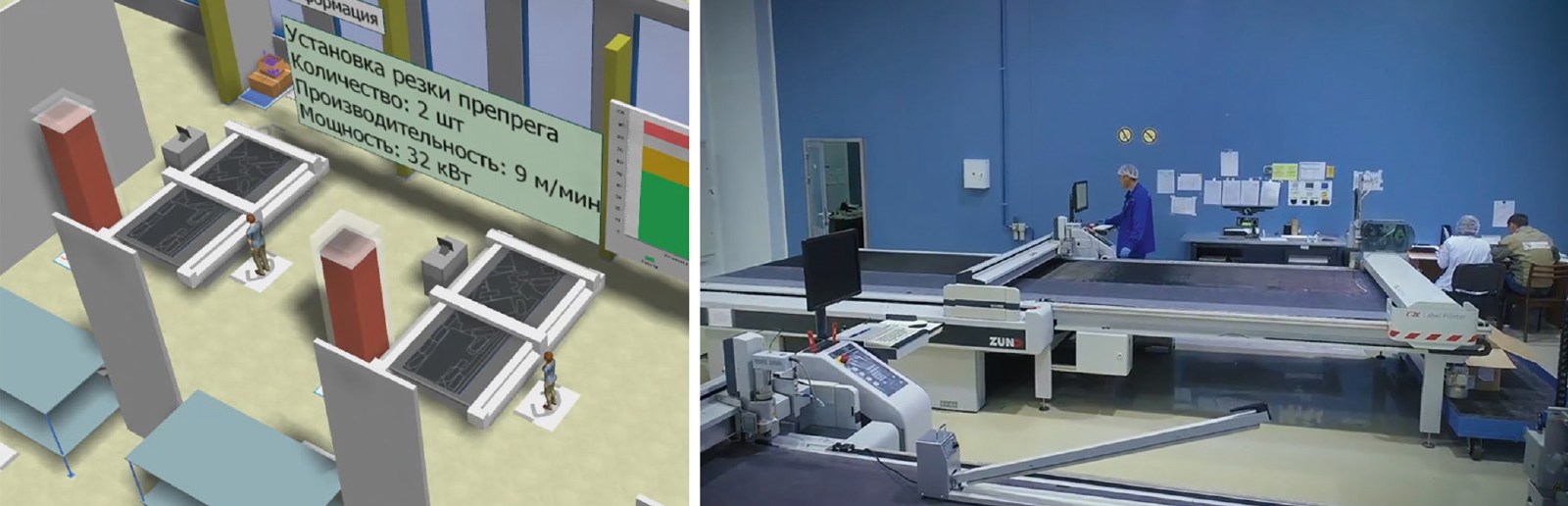
Модель и участок автоматизированного раскроя препрегов
Эффективные инструменты Цифрового производства для разработки управляющих программ обеспечивают максимальную скорость технологической подготовки, сокращение сроков запуска деталей в производство и минимизацию рисков повреждения высокотехнологичного оборудования, что положительно сказывается на сроках выполнения программы и обеспечивает высокое качество конечного продукта.
3. Цифровой двойник композиционного производства
Одной из основных задач при создании новых и реконструкции существующих производств является выбор проектных параметров, обеспечивающих выполнение заданных целевых показателей. Планировка площадей, состав оборудования и организация производства непосредственно влияют на объем инвестиций, сроки реализации и возможности будущего производства. В ходе проектирования инженерам приходится учитывать сотни и тысячи различных факторов, рассматривать не только отдельные участки, но работу всей системы в комплексе, что является исключительно сложной задачей. В то же время, очень высока цена проектной ошибки, выявленной после запуска производства, так как её устранение может потребовать дорогостоящих мероприятий, дополнительного оборудования или других ресурсов.
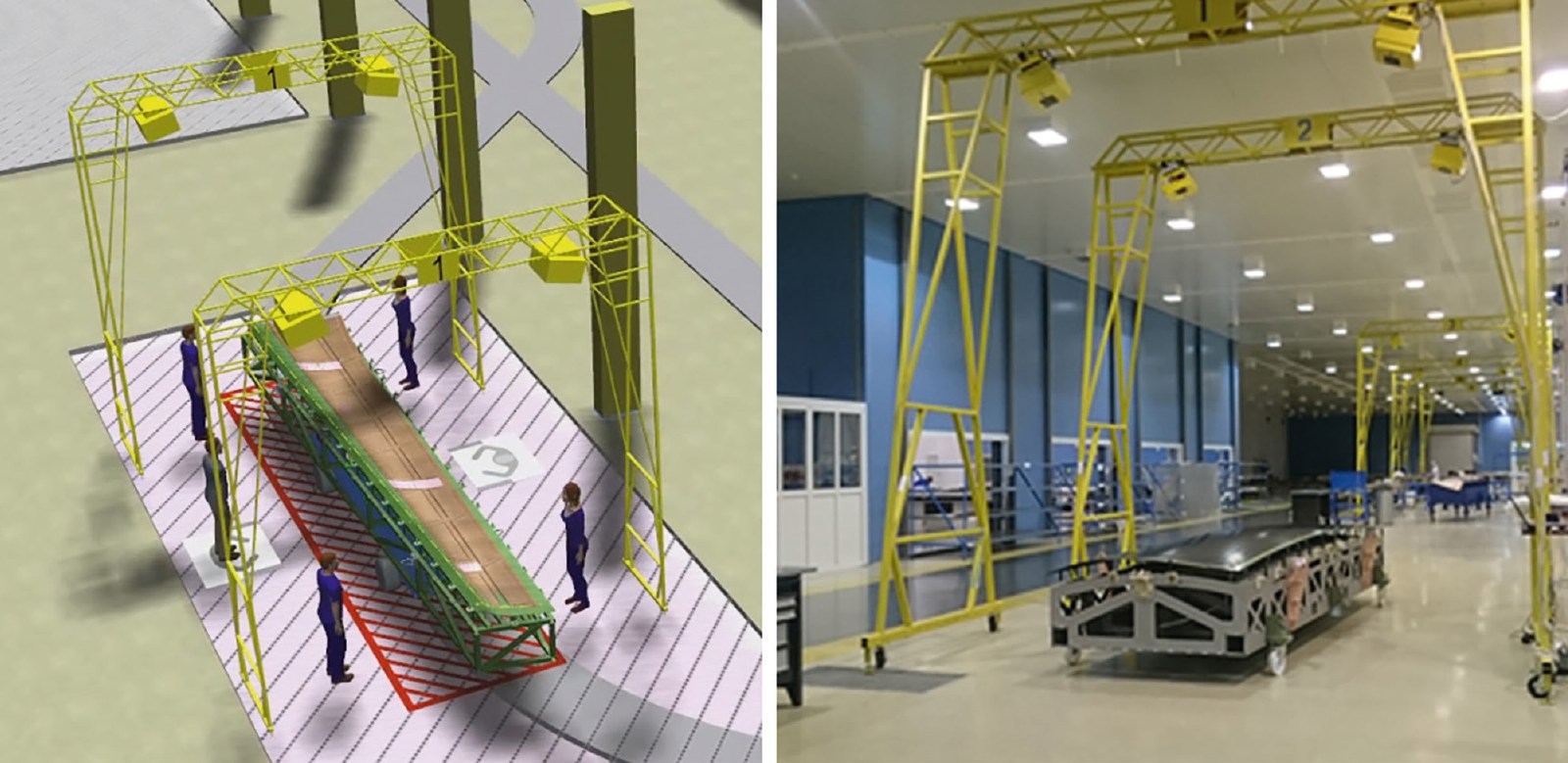
Модель и участок ручной укладки препрегов
Наряду с цифровыми двойниками изделия и технологического процесса, построение цифрового двойника производства дает возможность точно оценить достижимые показатели и качество заложенных в проект решений, обеспечить высокую степень гибкости и масштабируемости производства. Специалисты могут увидеть завод еще на этапе проектирования и проверить, как заложенные в проект решения будут работать на практике при различных условиях.
Подход на основе технологии имитационного моделирования позволяет работать со сложными объектами масштаба производственной площадки с необходимой детализацией — вплоть до отдельной операции, проводимой на рабочем месте. В ходе моделирования параметры и показатели работы можно посмотреть и скорректировать в интерактивном режиме.
Математическая модель, использованная в двойнике, учитывает самые разные параметры системы: производственную программу, номенклатуру продукции, технологический процесс для каждого типа деталей и характеристики оборудования. Параметры могут быть заданы в виде статистического распределения, что позволяет учесть случайные отклонения, неизбежные в реальном производстве, и их влияние на производство в длительной перспективе.
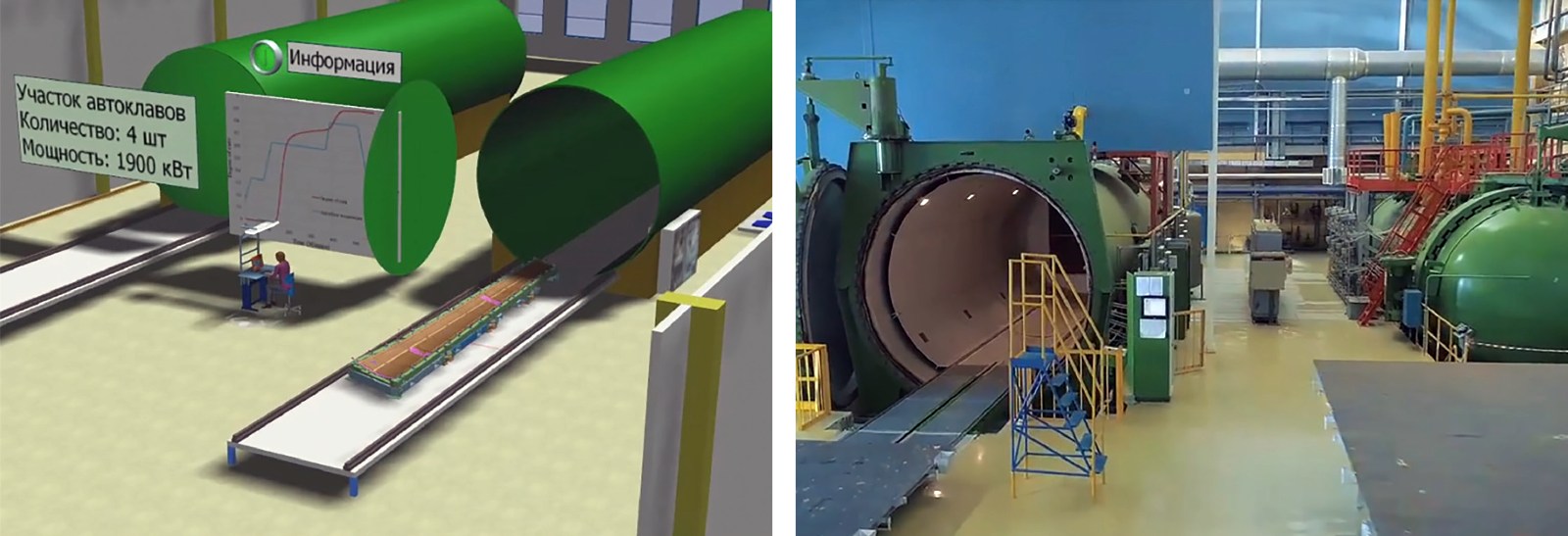
Модель и участок автоклавного формования композиционного изделия
Трёхмерная планировка служит для оптимизации материалопотоков, оценки времен и расстояний перемещения деталей, транспорта и персонала. Нормативные времена операций используются для расчета длительности цикла изготовления и загрузки оборудования. Модели оборудования включают большое количество параметров, определяющих его надежность, длительность обслуживания и ремонта, энергопотребление и множество других факторов.
Оценка работы системы может быть выполнена по любым показателям — от коэффициентов загрузки оборудования и персонала до себестоимости продукции и доли в ней полезной работы. Таким образом, «Цифровой двойник» позволяет оптимизировать совместную работу всех элементов производственной системы и гарантировать эффективную работу завода, что является основной целью процесса подготовки производства.
4. Заключение
Таким образом, «Цифровые двойники» предназначены для:
- осуществления всестороннего моделирования объекта исследования — будь то деталь, агрегат, окончательное изделие из композитов или его производство — с целью прогнозирования поведения этого объекта в различных условиях;
- формирования универсального языка описания изделий и производственных процессов на основе цифровой модели для упрощения взаимодействия как между различными подразделениями внутри предприятия, так и при общении с контрагентами.
Создание цифровых связей, объединяющих «Цифровые двойники», направлено в первую очередь на оперативное получение выборки необходимой описательной информации об объекте исследования, а также на автоматизацию проведения изменений, затрагивающих всю цепочку подготовки производства изделия.
Внедрение и использование «Цифровых двойников» на современных предприятиях авиационной отрасли целесообразно, поскольку приводит к целому набору положительных результатов: повышению эффективности процесса проектирования, снижению стоимости и сроков разработки за счет сокращения числа дорогостоящих натурных экспериментов, сокращению сроков запуска изделия в серийное производство, снижению рисков брака и срыва сроков, повышению качества готовой продукции. В свою очередь, такие результаты дают развивающимся компаниям возможность приобретать, а компаниям-лидерам — сохранять конкурентные преимущества на рынке авиационной техники, благодаря выполнению программ в срок и в рамках запланированных бюджетов при обеспечении требуемого уровня качества продукции.
5. Список литературы
- Братухин А. Г. Российская энциклопедия CALS. Авиационно-космическое машиностроение. – М.: ОАО «НИЦ АСК», 2008. –608 с.
- 4.0 RU – Цифровой закрылок МС-21. // Электрон. дан. – 2019. - Заглавие с экрана. – Режим доступа: https://youtu.be/bru5kW3SRzA
- Дежина И. Г., Пономарев А. К., Фролов А. С. Новая технологическая революция: вызовы и возможности для России / Публичный аналитический доклад по направлению «Новые производственные технологии». – М.: Сколковский Институт Науки и Технологий, 2015.
- Kazmierski C. Growth Opportunities in Global Composites Industry, 2012-2017. –2013.
Статья была опубликована в номере 5 (86) 2019