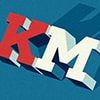
Непростые времена для композитной отрасли или еще один шанс?
рубрика: отрасль
Так что же произошло в 2022 году в композитной отрасли? И с чем мы пришли в 2023 год? В целом, если говорить о производственной сфере, отрасль справилась. Да, тенденции марта-июля были тревожными. У многих компаний запаса привычного сырья (часто импортного) оставалось на месяц, максимум на два, а дальше, как говорится, хоть кукурузой заряжай. В той или иной степени, мы все прожили пять стадий принятия неизбежного: отрицание, гнев, торг, депрессия и принятие. Кто-то — не выдержал и закрылся, кто-то — выдохнул и поехал на турецкие и китайские выставки в поисках новых поставщиков сырья и оборудования, другие — продолжали работать, постепенно заменяя импортное сырье на отечественное, перестраивая производственные цепочки и отрабатывая технологии.
На сегодняшний день мировой рынок композитов оценивается в 80 млрд долл. На нем лидируют Китай — 32% (25,6 млрд долл.) и США — 26% (21,6 млрд долл.). Сегмент России — 1 % (1,1 млрд долл.). В России среди отраслей потребителей изделий из композитов основными являются строительство (включая дорожное) — 35% (22,9 млрд руб.) и гражданское авиа- и судостроение — 19% (12,4 млрд руб.). И все авторы и аналитики в один голос заявляют, что у российского композитного рынка большой потенциал, ему есть куда расти и развиваться. Например, несмотря на экономические и политические события в 2021 году в России объем производства полимерных композитов в стоимостном выражении достиг уровня в 80 млрд рублей. Таким образом рост по отношению к производству в 2020 году составил 11%.
Однако, проблема российской композитной отрасли — импортозависимость. И это стало особенно болезненным в середине 2022 года, когда многие западные поставщики сырья и оборудования покинули российский рынок. Можно долго возмущаться, задавать вопросы, мол что мы делали последние 30 лет, почему за это время не смогли возродить малотоннажную химию, собственные производства смол, армирующих материалов. А ведь между тем, многие разработки в нашей стране существуют, еще со времен СССР, но только в виде опытных производств.
Связующие
Сегодня как никогда становится очевидным, что наша страна должна адаптироваться к новым вызовам. Одним из таких вызовов является зависимость от импорта по ряду направлений производства химической продукции. Примером здесь могут служить термореактивные смолы. Этот ценный продукт широко используется в стратегических отраслях промышленности — электронике, радиотехнике, машиностроении и строительстве. Без термореактивных смол невозможно получение многих композитов и компаундов, прочных порошковых покрытий, клеев и т.д.
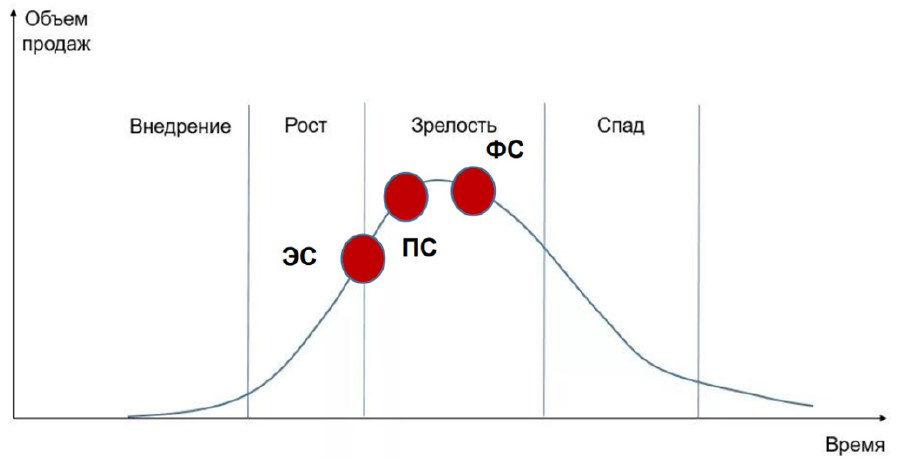
Текущая стадия жизненного цикла ключевых видов смол (эпоксидные смолы, полиэфирные смолы, фенолформальдегидные смолы)
Одним из направлений работы Комитета по химической промышленности Общероссийской общественной организации «Деловая Россия» является развитие производства продукции малотоннажной химии в России. В соответствии с поручением Президента Российской Федерации от 16 января 2021года № Пр-46 необходимо принять меры по развитию до 2030 года производства малотоннажной и среднетоннажной химической продукции и увеличению объёмов выпуска такой продукции к 2025 и 2030 годам на 30 и 70 процентов соответственно (по сравнению с объёмами 2020 года). В связи с этим Комитетом по химической промышленности «Деловой России» сформирован перечень «вытягивающих» проектов в сфере малотоннажной химии, которые могут стать драйвером ее развития. Одним из них является производство термореактивных связующих.
Рынки основных видов смол характеризуются разной степенью зрелости — если доля аминосмол в структуре мирового рынка синтетических смол постепенно сокращается, то доля эпоксидных и полиэфирных смол продолжает расти. Это связано с жизненным циклом как самих смол, так и ключевых рынков потребления для них.
Полиэфирные смолы
Объемы потребления полиэфирных смол в России в течение последних трех лет демонстрируют положительную динамику. По итогам 2021 года объем потребления в России полиэфирных смол составил 69,6 тыс. тонн. При этом на спрос со стороны композитной промышленности пришлось более 60%, оставшиеся объемы были направлены на производство ЛКМ, клеев, герметиков и прочих продуктов.
Важно отметить, что российский рынок смол до настоящего момента в значительной степени зависим от импорта. Удельный вес зарубежной продукции по итогам 2021 года составил по одним источникам около 40% , по другим — более 70%.
Поэтому запуск производства малеинового ангидрида компанией «СИБУР» на заводе в Тобольске в 2022 году является значимым фактором для снижения сырьевой импортозависимости и, следовательно, развития внутреннего выпуска полиэфирных смол. Проектная производственная мощность нового предприятия составляет 45 тыс. тонн.
Согласно оценкам экспертов, внутреннее производство в стране осуществляют около 10 крупных и средних компаний, из которых лидирующими по объему выпуска являются: ООО «Дугалак», ООО «Радуга-синтез», ГК «Аттика», АО «Камтэкс-Полиэфиры», ООО «Полимерпром», АО «Электроизолит», АО «Пермские полиэфиры».
В сентябре 2022 году компания «Дугалак» укрепила лидирующие позиции, открыв новую площадку по выпуску полиэфирных смол в Ярославле. А в конце 2022 года Группа компаний «Аттика» открыла завод в Башкирии.
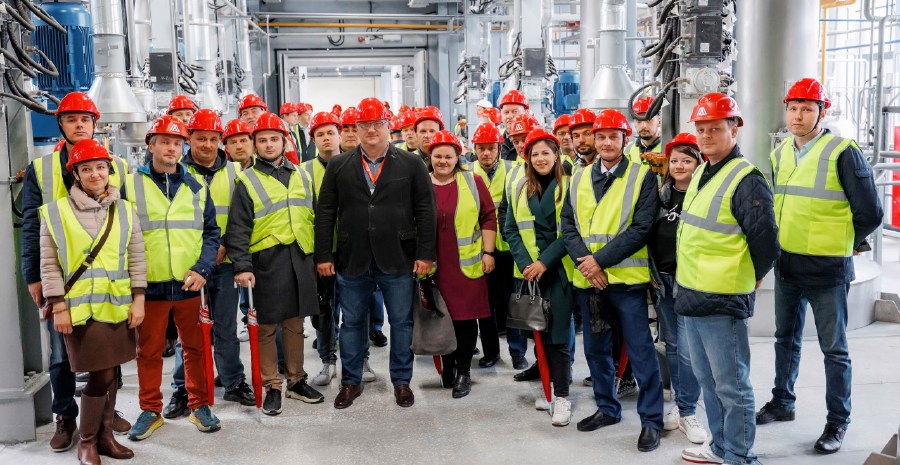
Открытие новой площадки «Дугалак» по выпуску полиэфирных смол в Ярославле (Источник: dugalak.ru)
Вроде бы все хорошо, но в чем подвох? Многие отечественные производители конечных изделий, привыкшие работать на западном ассортименте смол, жалуются на отсутствие стабильности свойств у отечественного производителя, а также на довольно узкий ассортимент. Поэтому, основная задача, которая сегодня стоит перед российскими производителями смол, — работа над качеством продукции, техническая поддержка клиентов и расширение ассортимента. И первые успешные шаги в этом направлении уже сделаны. Так компания «Полимерпром» получила сертификат соответствия на трудногорючие смолы, ООО «Дугалак» — анонсировало выпуск расширенной линейки продукции: от смол общего назначения, до смол для намотки, пултрузии и РТМ, «Аттика» — публикует в соцсетях данные о выпуске прозрачных литьевых и матричных смол.
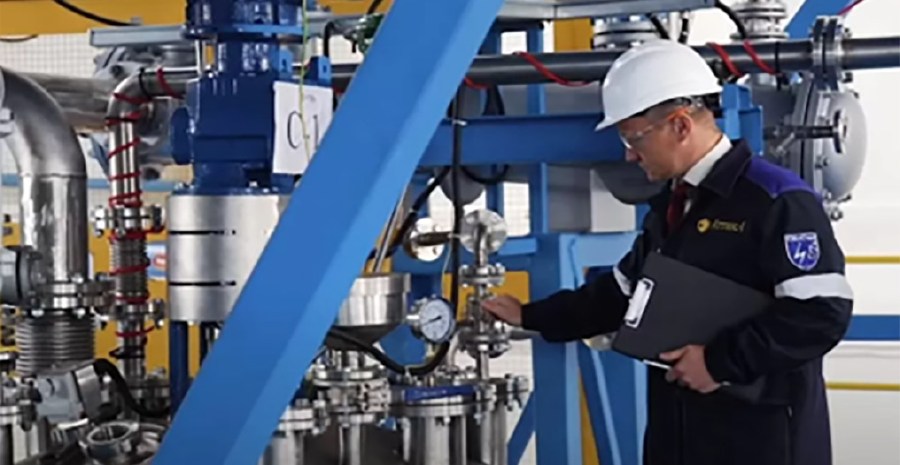
ГК «Аттика» открыла завод по производству полиэфирных смол в Башкирии (Источник: www.newprospect.ru)
Переходя от анализа текущего состояния рынка полиэфирных смол к прогнозам, важно отметить, что, согласно оценке Зорана Павловича («Дугалак»), российский рынок в перспективе следующих пяти лет будет демонстрировать уверенную положительную динамику на уровне 7–10% в год. Столь выраженный прирост будет обусловлен, прежде всего, развитием основных отраслей потребления.
Кроме того, новые инвестиции в производственные мощности, запланированные на 2022–2025 гг., согласно оценке «Смарт Консалт» во многом определяют оптимистичный сценарий развития внутреннего производства полиэфирных смол в России и дальнейшее снижение удельного веса импортной продукции.
Эпоксидные смолы
Если с полиэфирными смолами ситуация более-менее прозрачна, то с эпоксидными — все сложнее. По оценкам BusinesStat, продажи эпоксидных смол в России увеличились за 2017—2021 гг на 20,2 %: с 46,1 до 55,4 тыс. тонн. Ежегодный темп роста потребления составлял 2,2–13,8%. Среди основных драйверов роста российского рынка эпоксидных смол в последнее десятилетие можно выделить следующие: — расширение спроса со стороны предприятий лакокрасочной промышленности, — развитие производителей композиционных материалов и изделий из них, — развитие строительного комплекса, в т.ч. внедрение новых материалов для применения в строительстве.
Рынок эпоксидных смол в России преимущественно состоит из импортной продукции. В 2021 г. крупнейшим поставщиком эпоксидных смол на российский рынок была Южная Корея, доля которой составила 28,9 % всех импортных поставок. Второе место по объемам поставок эпоксидных смол на российский рынок в 2021 г занимала Германия, третье место принадлежало Китаю.
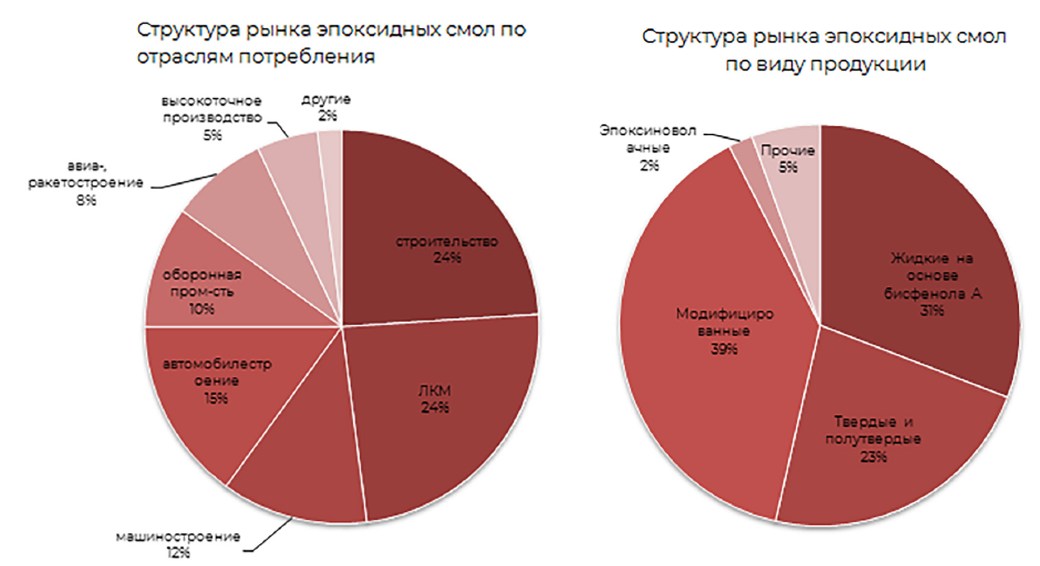
Структура рынка эпоксидных смол по отраслям потребления и по виду продукции
Объемы собственного производства невелики (примерно 10%) и к тому же сильно варьируются год от года. Основной проблемой развития производства эпоксидной смолы в России является дефицит сырьевой базы. Для того, чтобы создать рентабельное предприятие по производству эпоксидной смолы, нужно либо искать зарубежных поставщиков сырья, что делает предприятие зависимым от валютного курса и мировых цен, либо производить сырье самостоятельно, что делает бизнес рентабельным лишь при условии больших производственных мощностей. И все-таки отечественные производители удерживают свою небольшую долю за счет закона 488-ФЗ от 31 декабря 2014 г. «О промышленной политике в Российской Федерации», который обязывает предприятия, работающие в сфере гособоронзаказа, использовать только российскую продукцию.
Почти половина объема потребления эпоксидных смол приходится на строительство и производство лакокрасочных материалов. Эти отрасли в основном используют универсальные марки смол. В остальных сегментах потребления применяются в основном модифицированные составы, которые производятся на заказ на российских предприятиях.
Основа потребления — смолы на основе бисфенола А. Это как раз те жидкие, полутвердые и твердые вещества, которые относятся к категории универсальных смол и используются преимущественно в строительстве и производстве ЛКМ.
Модифицированные смолы — это соединения с более сложным составом, обычно состоящие из нескольких компонентов и предназначенные для решения конкретных задач в оборонной промышленности, самолето- и ракетостроении, конструировании судов и т. д. Однако их доля на рынке выше, чем суммарная доля указанных отраслей потребления, поэтому можно сделать вывод о том, что частично модифицированные составы применяются и в бытовых сегментах.
Основными российскими производителями эпоксидных смол являются:
- ФКП «Завод имени Я.М. Свердлова», предприятие оборонного комплекса, выпускающее, в том числе, промышленную химию: смолы фенолоформальдегидные жидкие, эпоксидно-диановые неотвержденные смолы, связующие для смол, эпоксидные модифиционованные смолы и клеи.
- АО «ХИМЭКС Лимитед», научно-производственное предприятие, созданное в 1991 г. для выпуска эпоксидных смол, активных разбавителей, компаундов, отвердителей, ускорителей отверждения, и других продуктов.
- «АО «ЭНПЦ ЭПИТАЛ» производит, разрабатывает, заменяет импортные эпоксидные смолы, отвердители, связующие.
- ОАО «Завод «Алтайский Химпром» им. Верещагина, предприятие выпускает эпоксидную смолу, полиэтилсилоксановые жидкости для смазочных масел, и продукты двойного назначения.
По ряду предприятий имеется потенциал наращивания производственных мощностей, что потенциально позволяет увеличить производство эпоксидных смол до уровня 10 тыс. тонн. Вместе с тем необходимо учитывать, что текущее состояние производственных мощностей на ряде предприятий и уровень технологии их производства в сочетании с отсутствием сырьевых цепочек для производства эпоксидных смол не позволяет обеспечить необходимую эффективность их производства по отношению к импортным аналогам
В настоящее время потенциальная емкость рынка эпоксидных смол в России оценивается не более чем в «плюс 10–15%» к текущему объему или 52–54 тыс. тонн. В перспективе потенциальную годовую потребность России в эпоксидных смолах по базовому сценарию эксперты оценивают в пределах 60 тысяч тонн.
В базовом сценарии предполагается умеренный рост внутреннего рынка на 23% к уровню 2020 года в физическом выражении (до уровня 60 тыс. тонн). В этот сценарий заложено повышение эффективности загрузки существующих производственных мощностей, а также выход на проектную мощность ОО «НПК «Химресурс» (г. Набережные Челны, Татарстан), запущенного в октябре 2020 года. Другим источником роста станет поэтапная модернизация производственных мощностей старых предприятий.
В случае реализации пессимистичного сценария при условии усиления негативных факторов, влияющих на рынок эпоксидных смол, ожидается стабилизация объемов внутреннего рынка эпоксидных смол с небольшим ростом к концу прогнозного периода на 5% к уровню 2020 года (до 51 тыс. тонн). В этом случае ожидается полный или частичный вывод производственных мощностей на старых предприятиях. Объем производства составит 6 тыс. т, что всего на10% выше уровня 2020 года.
Возможность реализации оптимистичного сценария будет зависеть от темпов развития российской экономики, интенсивности применения новых материалов и конструкций, развития рынка аддитивных технологий, расширения экспорта эпоксидных смол до уровня 5–10 тыс. тонн.
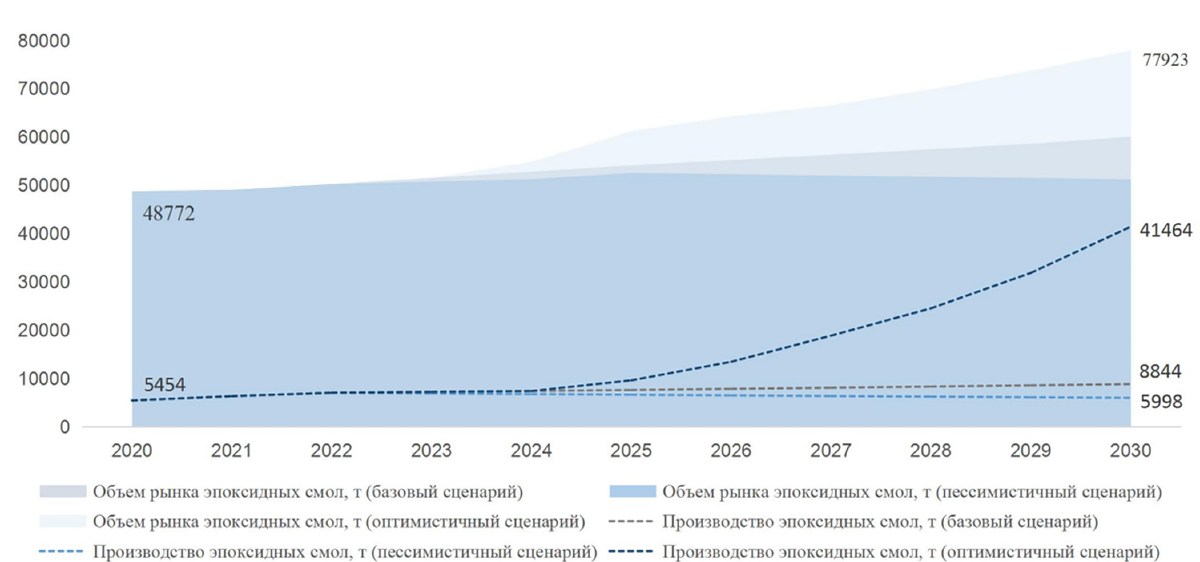
Прогнозные сценарии развития рынка и производства эпоксидных смол в 2021–2030 гг.
При оптимистичном сценарии предполагается реализация крупных проектов, направленных на развитие композитной отрасли и аддитивных технологий (ИНТЦ «Композитная Долина», промышленный кластер «Композиты без границ», ИНТЦ «Долина Менделеева»). Это приведет к росту рынка эпоксидных смол на 60% до 80 тыс. тонн к 2030 году. Оптимистичный сценарий также предполагает реализацию масштабных инвестиционных проектов в отрасли, прежде всего запуска анонсированного ГК «Титан» проекта «Создание производства биcфенола А (увеличение глубины переработки нефтехимического сырья) и производство эпоксидных смол на его основе» с ожидаемой проектной мощностью до 45 тыс. тонн. Ещё одним возможным проектом является инициированный Институтом нефтехимического синтеза им. Топчиева РАН проект по производству эпоксидных смол ( мощностью 10 тыс. т ) и сырья для их производства. Ввод дополнительных мощностей в прогнозном периоде позволит к 2030 году увеличить производство эпоксидных смол в 7 раз до уровня 40 тыс. тонн.
В целом при мировой тенденции уменьшения углеродного следа и соответствия принципам устойчивого развития рынок смол имеет хороший потенциал роста в связи с переходом от традиционных материалов на более лёгкие композиционные, в первую очередь полимерные. Ещё одним фактором роста рынка смол является интенсивное развитие рынка аддитивных технологий, позволяющий создавать локальные универсальные производства, уменьшающие затраты на логистику и разработку специальных производственных линий.
Армирующие материалы
Стекловолокно
В России общий суммарный объем производства стекловолокна (лент, ровинга, пряжи и рубленого волокна) в натуральном выражении в 2021 году составлял порядка 130 тыс. т. Производство стекловолокна и изделий из него в 2022 году по разным оценкам снизилось на 12–24%.
Общие объемы производства стекловолокна в России не позволяют говорить об экспортном потенциале данных наполнителей и их конкурентоспособности на мировом рынке, однако для удовлетворения нужд внутреннего рынка объемов производства достаточно. Основными производителями являются: АО «ОС Стекловолокно» (34% рынка (от выручки)), АО «НПО «Стеклопластик» (22%), АО «Стеклонит» (18%), ООО «П-Д Татнефть – Алабуга Стекловолокно» (14%), ПАО «Астраханское стекловолокно» (5%), ООО «Ступинский завод стеклопластиков» (5%), ПАО «Новгородский завод стекловолокна» (2%), ООО «Махачкалинский завод стекловолокна» (1%), ОАО «Завод стекловолокна» (0,2%). (данные за 2021 год).
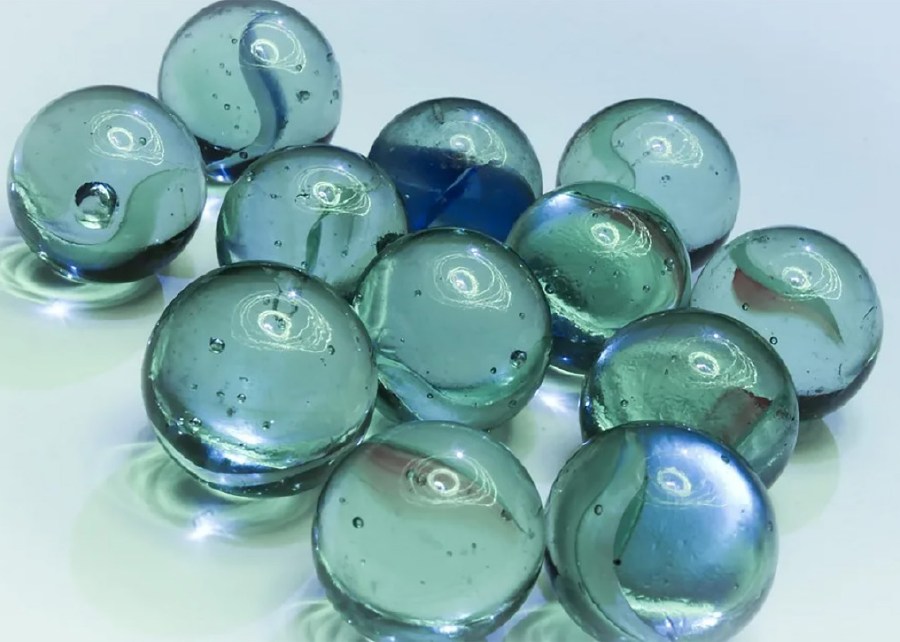
Фото 3. Производство стеклошаров Республика Дагестан, г. Дагестанские Огни (Источник: заводы.рф)
Лидером по импортным поставкам в 2022 г. является Китай (более 60%), ведущий поставщик стекловолокна — OWENS CORNING COMPOSITES (CHINA) CO., LTD (9,5%). В импорте наибольшую долю занимает сегмент low-priced с долей 61,9 %, основные поставки сегмента из стран: Китай, Беларусь, Тайвань (Китай). Сегмент high-priced представлен долей в 26,3% преимущественно из стран: США, Китай, Германия.
Большую часть продукции российских экспортеров покупает Казахстан (более 27%), крупнейший покупатель — LAUSCHA FIBER INTERNATIONAL GMBH (2,4%).
Последние новости рынка стекловолокна
Завод по производству стеклошариков для изготовления волокна, запущенный в мае 2022 года в городе Дагестанские Огни, в июле выпустил первую продукцию.
Масштабная модернизация ожидается на заводе «Астраханское стекловолокно» в первом квартале 2023 года. Решение о финансовом займе в размере 24 миллионов рублей экспертный совет Фонда развития промышленности принял ещё в конце 2022-го. Ожидается, что новое оборудование позволит увеличить объёмы производства.
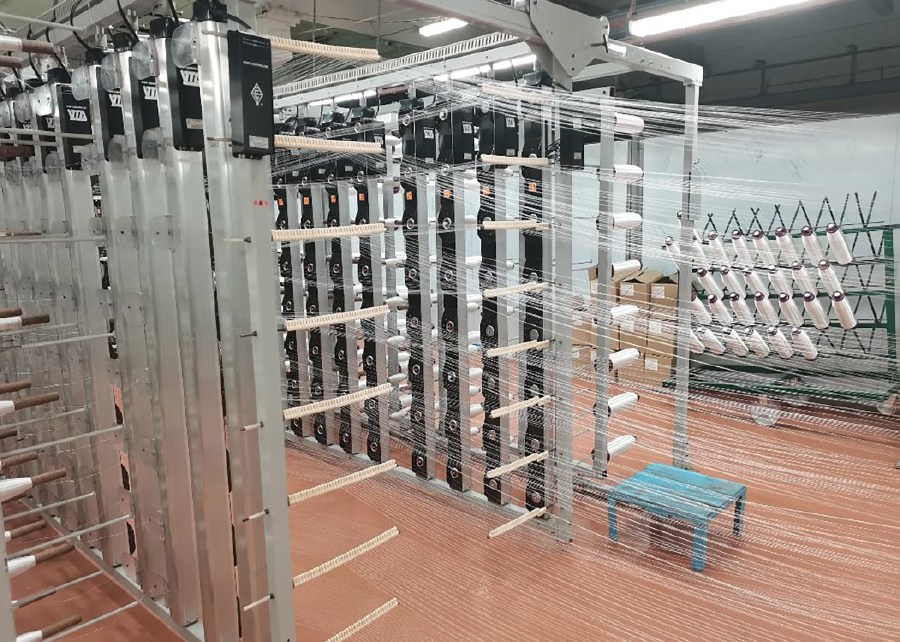
Завод Астраханское стекловолокно (Источник: astravolga.ru)
«Юматекс» завершил сделку по приобретению активов американской группы «Owens Corning» в России и Беларуси. В состав «Юматекс» вошли предприятия по выпуску стекловолокна и изоляционных материалов во Владимирской и Тверской областях, а также подразделение в Беларуси. Завод по производству стекловолокна расположен в городе Гусь-Хрустальный. Стекловолокно используется в качестве армирующих элементов стеклопластиков и других композитов в строительстве и медицине, машино- и приборостроении, автомобиле- и судостроении, а также в энергетике и авиации.
В Белоруссии ОАО «Полоцк-Стекловолокно» завершило крупнейший за последние несколько лет инвестиционный проект и дало старт производству нового вида продукции — стеклоткани электроизоляционного назначения, которая благодаря дополнительной финишной обработке теперь входит в разряд уникальных на территории СНГ. Еще одним знаковым событием стал запуск стекловаренной печи № 2 после консервации. Реализация проекта — часть стратегии технического перевооружения с прицелом на рост экспорта. Таким образом предприятие увеличит объем вырабатываемого волокна и, как следствие, готовой продукции, спрос на которую идет вверх.
В Туркменистане Открытое акционерное общество «Senagat Tehnologiýalary», производящее композитную арматуру, в августе 2022 года запустило производство стеклоровинга.
Углеродное волокно
Рынок углеродных волокон в России находится на начальном этапе своего развития. Количество отечественных предприятий малочисленно. Однако перспективы углеродных волокон и материалов на их основе крайне привлекательны.
В 2022–2023 году аналитики ООО «СтекТех» предполагают незначительный рост мирового рынка на уровне 3–5%. Дальнейшее развитие во многом будет определяться геополитической обстановкой.
В мире назревает дефицит предложения углеродных волокон. В связи с этим ведущие мировые игроки расширяют количество своих производственных площадок и ведут постоянный мониторинг как существующих, так и потенциальных рынков сбыта.
По данным экспертов, потребление углеволокна в России составляет 1–1,6% от мирового спроса, который, на 2018 г. составлял 78,5 тыс. т, а мощности производства – 149 тыс. т. Основными потребителями углеродных наполнителей в России являются атомная, космическая и авиационная промышленность, а основными производителями выступают ООО «Алабуга-Волокно», ООО «Аргон», ООО «ЗУКМ».
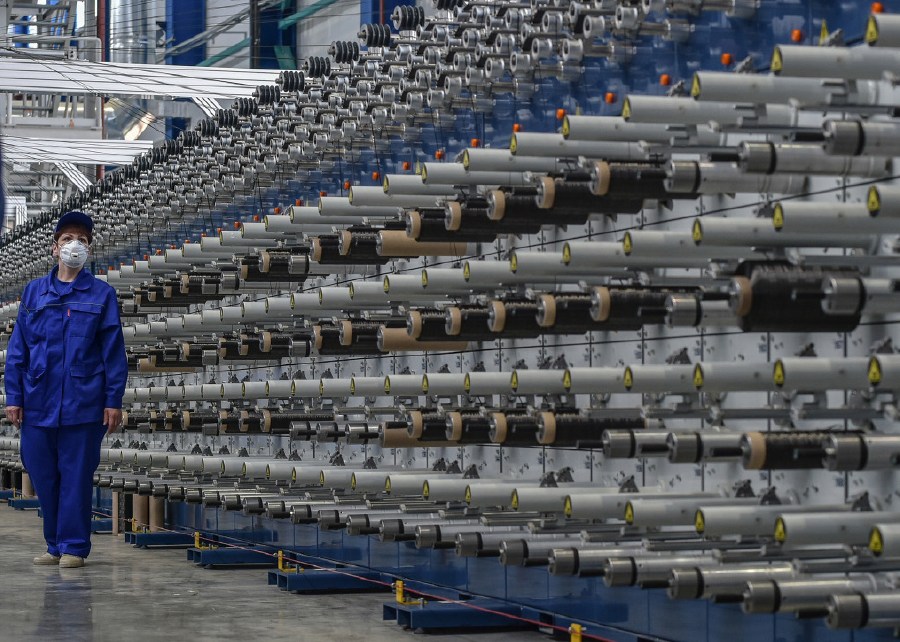
Завод Алабуга-Волокно (Источник: РБК)
Первый в России завод по производству стратегического сырья для углеродного волокна — ПАН-прекурсора — открылся в 2021 году на территории особой экономической зоны «Алабуга». Общий бюджет проекта составил 8,5 млрд рублей. Проектная мощность производства составляет 5 000 тыс. тонн ПАН-прекурсора номиналом 1К–48К.
Арамидное волокно
По данным международных консалтинговых компаний, наблюдается непрерывный рост мирового рынка арамидного волокна. По разным оценкам, его объем, включающий производство/применение как пара-арамидных (Kevlar, Twaron, Technora, Руслан, Русар и др.), так и мета-арамидных волокон (Nomex, Newstar, Teijinconex и др.), находится в диапазоне 96–120 тыс. тонн в год и 3,0–3,5 млрд долл. Доля пара-арамидных волокон составляет 63–65% и 60–78 тыс. тонн, доля мета-арамидных волокон: 35–37% и 36–42 тыс. тонн. Совокупный среднегодовой прирост прогнозируется в диапазоне 3,5–7,5%. Это свидетельствует о том, что до 2024 г. объем рынка должен быть обеспечен на уровне ~5 млрд долл. и 130–145 тыс. тонн в год .
Россия является одной из стран мира, которая наряду с США, Южной Кореей, Японией, Китаем владеет технологиями производства термостойких пара-арамидных волокон. При этом их химический состав и принятая в России технология производства обеспечивают более высокие свойства пара-арамидных волокон, чем у зарубежных аналогов. Производство мета-арамидных волокон в России отсутствует, а их ежегодные закупки достаточно высоки: более 200 тонн в год. По различным экспертным данным, объем импорта может достигать 500–800 тонн. Следует отметить, что мета-арамидное волокно под маркой Фенилон производилось в СССР (разработчик – «ВНИИСВ», г. Тверь) в г. Кустанай (Казахстан). Однако в 1996 г. завод был полностью остановлен, а оборудование продано китайской компании, которая выпускает волокно под маркой Newstar.
В России объем производства арамидного волокна не превышает 500 тонн. Арамидные волокна выпускают под торговыми марками: «СВМ», «Руслан», «Армос», «Артек», «Русар-С», «Русар-НТ», и используют для изготовления средств индивидуальной бронезащиты, кабельных изделий, огнезащитной одежды, а также в качестве армирующих наполнителей высокопрочных органопластиков. Органопластики широко применяются в конструкциях самолетов и вертолетов и являются самыми легкими полимерными композиционными материалами.
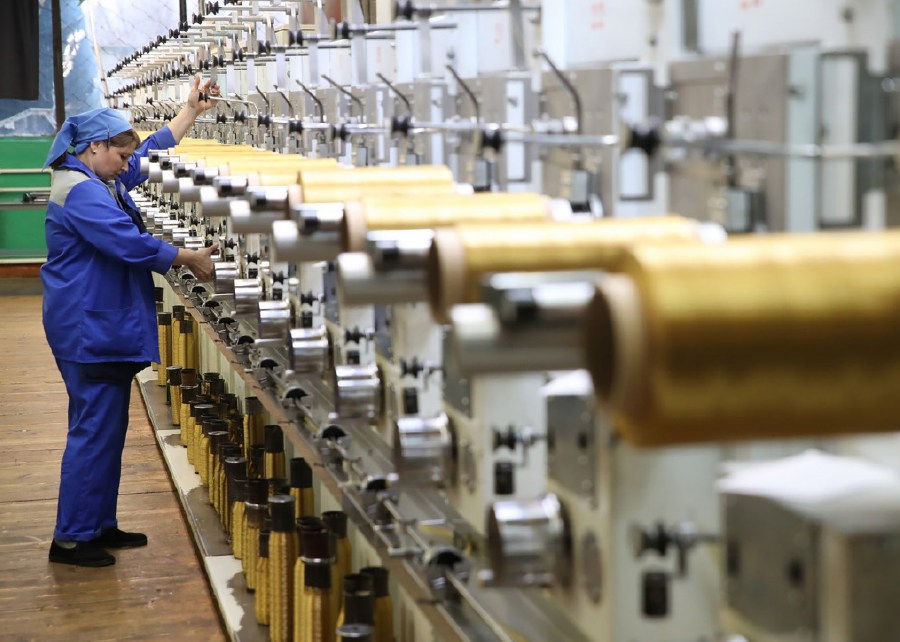
Фото 6. Предприятие Каменскволокно (Источник: compositeworld.ru)
Производителями выступают АО «Каменскволокно» (94% рынка), АО НПП «Термотекс» (4%), ООО «Лирсот» (2%). Производимое волокно по своему составу и принятой технологии обеспечивает более высокие свойства волокон, чем у зарубежных аналогов.
СВМПЭ
В России пока нет промышленного производства СВМПЭ. Однако наши учёные из «Научно-исследовательского института синтетического волокна с экспериментальным заводом» (г. Тверь) и «Центрального научно-исследовательского института специального машиностроения» (г. Хотьково) разработали технологию и создали экспериментальную линию по производству СВМПЭ нитей. И получили волокно, которое по основным показателям превосходит сверхпрочные нити SK-75 и SK-78, производимые мировым лидером в этой области — голландской фирмой DSM Dyneema. Казалось бы, успех композитчиков предопределён.
Следующим шагом должно стать создание в 2021–2024 годах опытно-промышленного производства нитей из сверхвысокомолекулярного полиэтилена мощностью порядка 10 тонн в год. А затем планируется развернуть промышленное производство этого материала, что позволит обеспечить Вооружённые Силы России изготовленными из СВМПЭ средствами индивидуальной защиты.
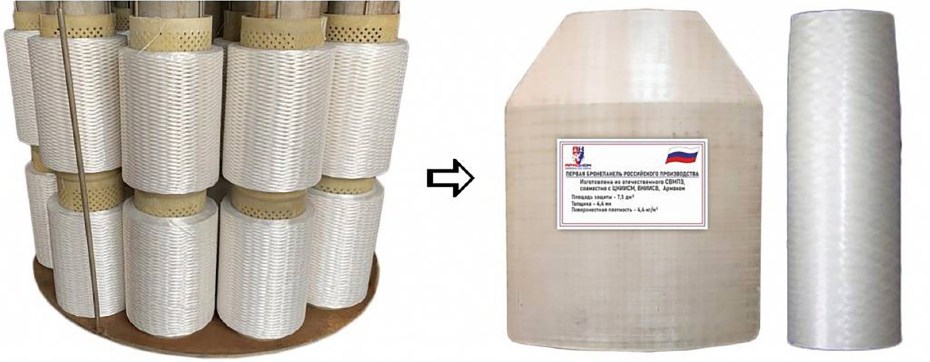
Исходные нити СВМПЭ и панели из СВМПЭ композита — грудная и ножная (Источник: armocom.ru)
СВМПЭ — сверхвысокомолекулярный полиэтилен высокой плотности. Некоторые его разновидности в 15 раз более устойчивы к истиранию, чем углеродистая сталь. Волокна из такого полиэтилена относятся к группе так называемых «суперволокон». По сравнению с другими видами армирующих волокон (арамидных, углеродных, стеклянных) волокно из СВМПЭ способно к поглощению высокоскоростного удара, обладает химической и биологической инертностью, а также абсолютно прозрачно во всем диапазоне радиоволн.
Высокие прочность и износостойкость при сравнительно низкой плотности (0,96–0,97 г/см3) делают нить СВМПЭ одним из самых перспективных волоконных материалов в различных отраслях. В частности, такие нити применяются при изготовлении средств бронезащиты — создании личных бронежилетов, а иногда и в качестве брони транспортного средства. Волокно из СВМПЭ используется при изготовлении парашютных строп и тканей, при создании высокопроизводительной парусины, а также прочных и легких канатов и сетеснастных изделий, устойчивых к воздействию морской воды, низких температур и солнечной инсоляции.
Базальтовое волокно
Непрерывное базальтовое волокно (БНВ) является достаточно «молодым» и очень перспективным видом продукции. В настоящее время технологией производства непрерывного волокна из базальта владеет ограниченное число стран, Россия и Украина были пионерами в области разработки данных технологией. Следует отметить, что развитие рынка БНВ в Китае, который в настоящее время является крупнейшим в мире производителем непрерывного базальтового волокна, в области технологий базируется на разработках, сделанных в свое время в России и на Украине. Доступность сырья для производства БНВ, расширяющийся спектр применения этого материала вызывают все больший интерес к продукции на основе непрерывного базальтового волокна. Одним из приоритетных направлений использования непрерывного базальтового волокна является производство композитных материалов.
Одной из проблем, сдерживающих развитие рынка базальтового волокна, является малотоннажное производство данной продукции отдельными производителями, что не позволяет крупным потенциальным потребителям осуществлять закупки у одного поставщиками с гарантированным качеством и объемом продукции. Также рост рынка БНВ сдерживает более высокая стоимость материалов из непрерывного базальтового волокна по сравнению с аналогами из стекловолокна.
Согласно новому отчету «Рынок базальтового волокна», опубликованному MarketsandMarkets™, ожидается, что размер мирового рынка базальтового волокна вырастет с 286 млн долл. США в 2022 году (80-90 тыс. т/год БНВ) до 517 млн долл. США к 2027 г. (140–150 тыс. т/год БНВ). при среднегодовом темпе роста 12,5% в течение прогнозируемого периода.
На сегодняшний день рынок непрерывного базальтового волокна в России развит слабо — новые производства и проекты по выпуску БНВ и продукции на его основе практически не появляются. В течение последних нескольких лет ряд компаний ушли с рынка, т.к. не выдержали конкуренции (не смогли обеспечить стабильное качество продукции, либо допустили просчеты при оценке экономической модели производства). По оценке «Инфомайн», в период 2010- 2019 гг. производство непрерывного базальтового волокна в России увеличилось всего в 2 раза, при этом спрос на данную продукции вырос за это же время в 3 раза. Производители волокна постоянно ведут работы по совершенствованию технологии производства и улучшению качества продукции.
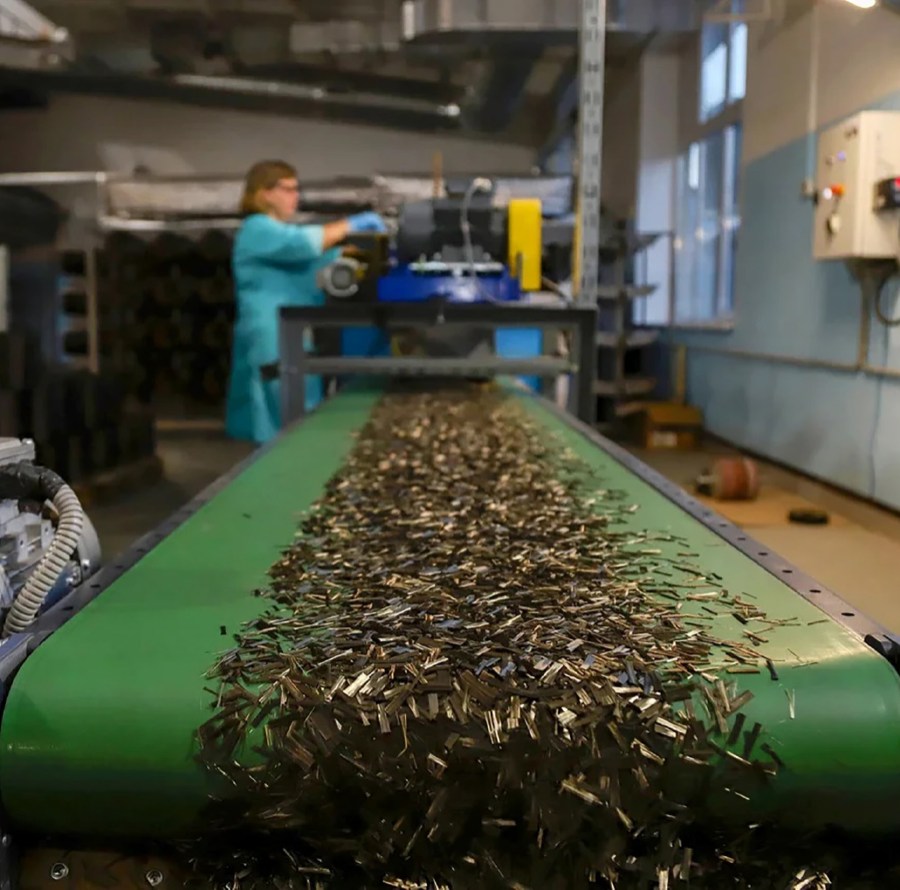
Производство базальтового волокна Магманит (Источник: vnru.ru)
Основными производителями базальтового волокна в Российской Федерации остаются ООО «Каменный Век», ООО «Русский базальт», ЗАО «НПЦ «ЛАВАИНТЕЛ», АО «Новгородский завод стекловолокна».
Вторая часть статьи, посвященная отечественным вспомогательным материалам, разработкам в области инструментов и оборудования, а также востребованным композитным специальностям и направлениям выйдет в следующем номере журнала Композитный мир.