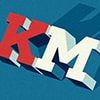
О чем писала зарубежная композитная пресса в 2022 году
рубрика: отрасль
Анализ статей нашего сайта (compositeworld.ru) показал, что в этом году большой интерес у читателей вызвали статьи о бронематериалах, перспективах российского рынка композитов и успехах в импортозамещении. А что у них? Обзор популярных статей 2022 года из журналов JEC Composites Magazine и Composites World magazine.
На первом месте по популярности статьи, посвященные автомобилестроению. А если точнее, статьи о новых материалах и технологиях, позволяющих влиять на скорость производства. Это и композиты на основе термопластов, и термореактивные композиты с высокой скоростью отверждения. Кроме этого, в связи с активным переходом на электродвигатели, усиливается тренд на еще большее снижение веса автомобилей за счет увеличения доли легких композитов в конструкциях.
Компания Tecnalia сформулировала основные направления развития композитных технологий в автомобильной промышленности. Это те принципы, которые нужно учитывать, чтобы композитные материалы могли конкурировать с металлами: использование недорогих термопластичных полимеров; развитие технологий изготовления гибридных многокомпонентных материалов, содержащих металл и композит, как со стекловолокном, так и с углеродным волокном; процессы с нулевым или минимальным браком; конкурентоспособные, быстрые и автоматизированные производственные технологии с коротким временем цикла — около 2 мин.; гибкие автоматизированные процессы, обеспечивающие различную толщину и индивидуальную укладку; использование композитов, которые могут быть подвергнуты вторичной переработке.
Сразу две статьи про колесные диски из углекомпозита попали в топ лист зарубежной прессы. Компания Bucci Composites SpA представила первый 20-дюймовый диск из углеродного волокна, предназначенный, в основном, для спортивных автомобилей и суперкаров. Карбоновый диск сочетает отличные характеристики с экономией веса более чем на 20% по сравнению с алюминиевым диском.
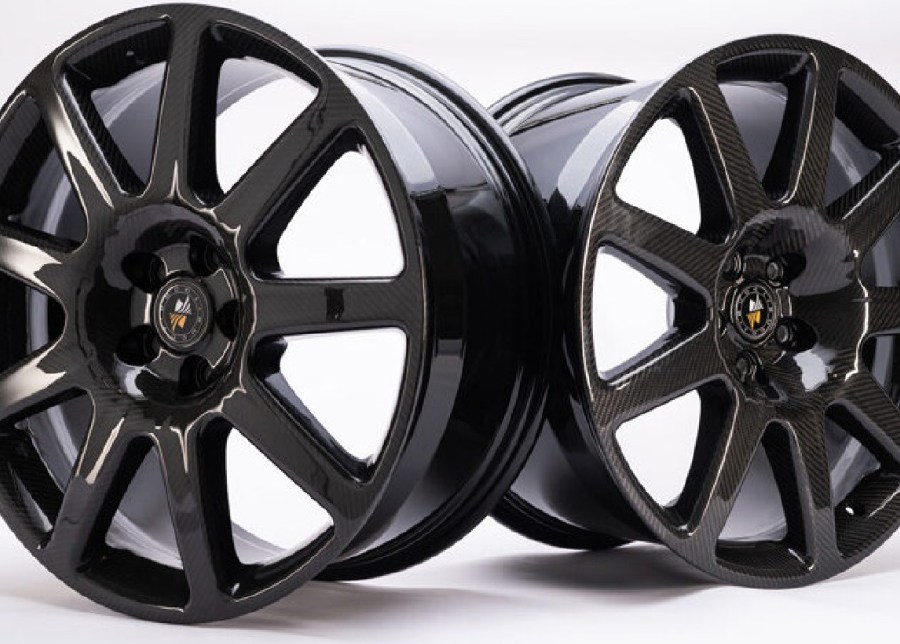
Фото 1. Колесный диск из углекомпозита Bucci Composites SpA (Источник: jeccomposites.com)
Все преимущества использования сверхлегкого диска из углеродных волокон напрямую связаны с уменьшенным весом колеса: более легкая конструкция компонентов означает меньшую инерцию вращения, что приводит к большему ускорению, более короткому тормозному пути и лучшей управляемости автомобиля. Кроме того, меньшая неподрессоренная масса означает, что шина всегда имеет наилучший контакт с асфальтом, что гарантирует отличные характеристики сцепления с дорогой.
Чтобы справиться с высокими температурами, которые возникают, особенно при использовании углерод-керамических тормозов, на внутреннюю часть обода нанесено керамическое покрытие, которое защищает углеродное волокно даже от самых экстремальных температур.
Для реализации этого проекта Bucci Composites оснастила свое производство технологией High Pressure RTM – HP-RTM. Углекомпозитный диск появится в продаже в первой половине 2023 года, первоначально только для итальянского рынка.
Компания Vision Wheel представила свой первый композитный диск из углеродного волокна на выставке CAMX 2021, заявив, что ее недорогой и крупносерийный процесс можно масштабировать для пассажирских автомобилей.
Для изготовления первых дисков команда Vision Wheel использовала технологию ручной выкладки. «Результат был успешным, — говорит сотрудник компании, — но мы поняли, что с помощью этого процесса невозможно производить миллионы дисков в год. Мы хотели найти процесс, который был бы ориентирован на массовое производство». Кроме того, необходимо было подобрать композитные материалы, которые прошли бы строгие требования автомобильных испытаний. Алан Дадли, технический менеджер Vision Wheel, объясняет, что требования Министерства транспорта США к колесам — тесты для измерения минимальной усталости, удара, радиального удара и т. д. — были разработаны с учетом пределов прочности алюминиевых и стальных колес. Композитные диски выходят из строя не так, как алюминиевые. Когда алюминиевое колесо выходит из строя при ударе, вы видите трещину на спице или в других местах. С композитами трудно определить серьезность повреждения. Это может быть внутренняя трещина, расслоение или что-то иное. Но является ли такое повреждение ремонтопригодным? Это сложно определить.
В дальнейшем, компания Vision Wheel стала искать технологию, которая позволила бы снизить стоимость материалов и время цикла. Так они перешли на технологию SMC, которая позволяла формовать изделия из недорогой, быстро отверждаемой, винилэфирной смолы и комбинации рубленого стекловолокна и углеродных волокон. Однако SMC композит из дисперсных волокон не был достаточно прочным, чтобы выдерживать самые высокие нагрузки с внешней стороны диска. Поэтому было решено добавлять в смесь некоторое количество непрерывного волокна. После длительных экспериментов компания нашла наилучшее решение. В спицы диска были введены непрерывные плетеные заготовки из углеродного волокна, которые составляют около 10% от общего веса детали. Большие сложности возникли с оптимизацией архитектуры оплетки, ориентацией волокон, чтобы в дальнейшем вся отвержденная конструкция работала как единое целое, выдерживала и перераспределяла все приложенные нагрузки. Вторая сложность заключалась в том, как гарантировать, что плетеная заготовка останется на месте во время компрессионного формования.
Данное ноу-хау привело к значительному улучшению прочности диска, однако иногда возникали проблемы с разогревом связующего в тех местах, где изделие имеет большую толщину. В итоге, винилэфирная смола была заменена на более производительную эпоксидную смолу со временем отверждения 10 минут.
Целью компании является увеличение мощностей на заводе компании в Алабаме как минимум до 50 000 единиц в год. Компания также работает над получением сертификатов ISO 9001, 14001 и TUV для своего предприятия. В долгосрочной перспективе компания планирует построить завод, способный производить миллион единиц продукции в год.
По мере того, как автомобильная промышленность быстро электрифицирует свои автопарки, среди производителей автомобильных компонентов растет интерес к использованию композитных материалов для аккумуляторных корпусов — крышек и поддонов, которые удерживают и защищают рамы и сами аккумуляторные элементы. Этому есть много причин, и главная из них — возможность уменьшить допуски по массе и укладке. Пустые металлические корпуса батарей увеличивают массу автомобиля на 110-160 кг и в настоящее время являются самым тяжелым компонентом аккумуляторных электромобилей — и это до загрузки аккумуляторных блоков.
Однако, не все так просто. Если вы останавливаете свой выбор на конструкционных композитных материалах, армированием рубленным волокном, очень важно иметь доступ к программам виртуального прототипирования и картам материалов, чтобы быстро и точно спрогнозировать свойства будущего изделия и при необходимости внести изменения в состав материалов. Производители программного обеспечения для моделирования композитных материалов, такие как Hexagon и Dassault Systèmes, наблюдают повышенный спрос на свои программные продукты, особенно со стороны производителей автомобильных компонентов по технологии SMC.
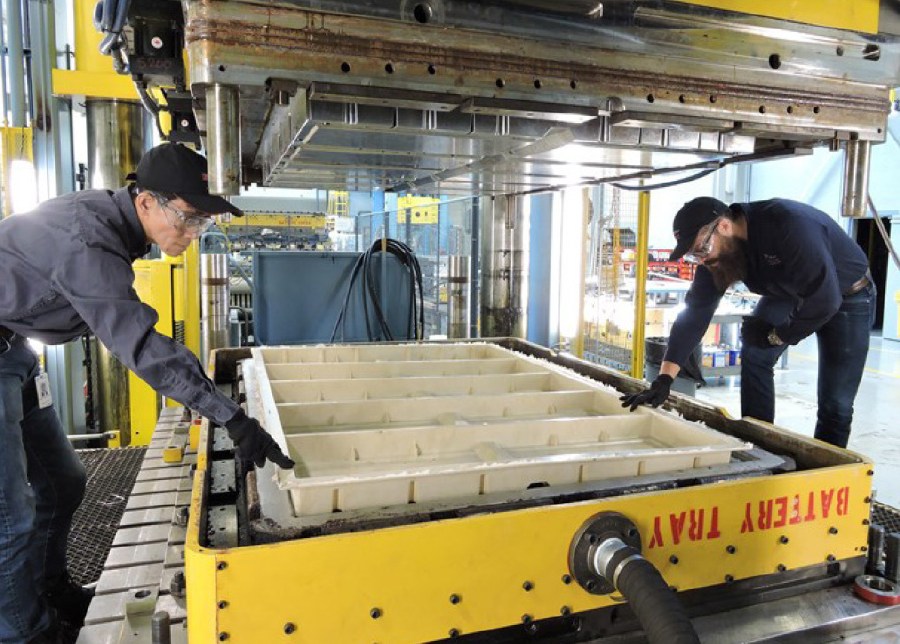
Фото 2. Специалисты компании Teijin Automotive Technologies извлекают большой аккумуляторный лоток SMC из оснастки компрессионного пресса (Источник: Teijin Automotive Technologies)
Поскольку крышки и лотки аккумуляторов могут иметь разные требования, в каждом конкретном случае требуется индивидуальный подход к выбору материалов. Например, в конструкциях корпусов Teijin Automotive обычно используется армирование рубленным стекловолокном, но там, где требуется большая нагрузка, команда может легко комбинировать слои однонаправленных или разнонаправленных непрерывных волокон с традиционным рубленым ровингом. Что касается выбора связующего, все известные виды смол — ненасыщенные полиэфирные, винилэфирные, фенолформальдегидные и эпоксидные смолы одинаково широко используются для изготовления аккумуляторных поддонов и крышек. Однако, по словам компании Magna, в последнее время ужесточаются требования по пожарной безопасности, особенно это касается грузовых автомобилей. Для таких требований наилучшим образом подходят фенолформальдегидные смолы.
Компания TPI Composites Inc. сообщила, что она провела обширную работу по выбору огнестойких материалов для корпусов аккумуляторных батарей электромобилей. Аккумуляторные поддоны и крышки — это очень сложные системы и они играют очень важную роль: защищают пассажиров автомобиля от внутренних пожаров, защищают модули от внешних пожаров, защищают элементы от повреждений во время сильных ударов и обеспечивают достаточную жесткость для переноски системы.
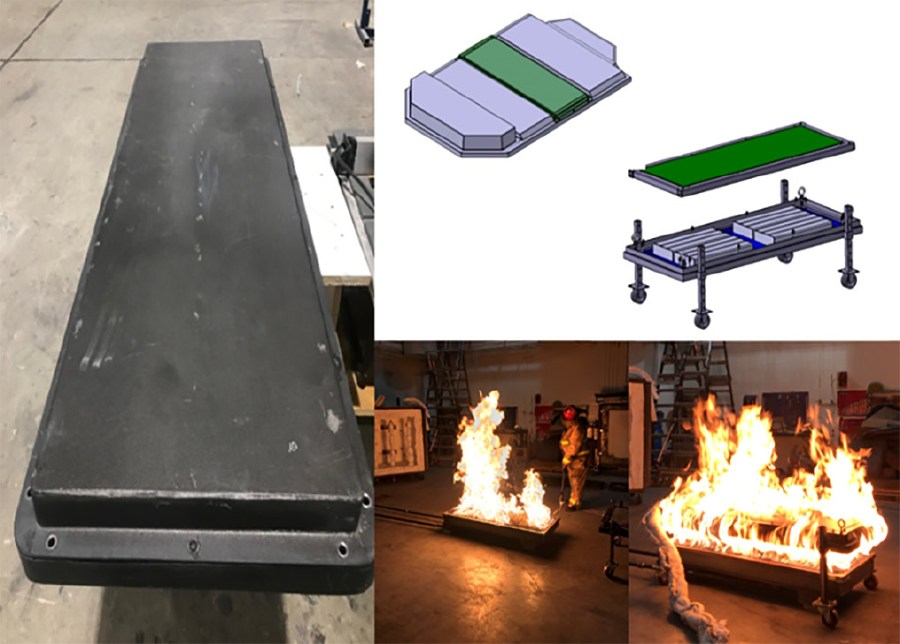
Фото 3. Испытание корпусов аккумуляторных батарей на огнестойкость (Источник: TPI Composites Inc.)
После 6 лет исследований компания TPI остановила свой выбор на конструкциях, армированных непрерывными волокнами (стекловолокно, углеродное волокно или комбинация этих волокон) и пропитанных либо фенолформальдегидной, либо высокотемпературной огнестойкой эпоксидной смолой для RTM, LCM и других технологий высокого давления.
После автомобилестроения плавно переходим к водородной энергетике. Но на самом деле речь опять пойдет о проектах для автомобилестроительной отрасли.
Эксперты по композитам из Центра перспективных производственных исследований Шеффилдского университета (AMRC) в течение года работали с Crossfield Excalibur, компанией по проектированию оснастки для ротационного формования, и Elite Ground Support Services, компанией которая имеет большой опыт в сфере изготовления композитных деталей для автомобилестроительной отрасли. Вместе они спроектировали, изготовили и испытали цилиндрический баллон высокого давления для водорода типа 4, изготовленный из углеродного волокна, намотанного на термопластичный лейнер. Резервуар был разработан для использования в большегрузных автомобилях и способен вместить 40 литров водорода при давлении 350 бар.
Стюарт Доусон, главный инженер в AMRC, уточнил: «Тяжелые дальнемагистральные автомобили являются одним из самых сложных сегментов дорожного транспорта в плане сокращения вредных выбросов и требований к большой полезной нагрузке. Для повышения экономической эффективности большегрузным автомобилям требуется большой запас хода и быстрая дозаправка. Большой вес аккумуляторов снизит потенциальную полезную нагрузку и запас хода транспортного средства и потребует длительного времени перезарядки. Таким образом, транспортные средства, работающие на водороде, — идеальное решение для тяжелых условий эксплуатации и перевозки на большие расстояния».
Однако, несмотря на прогнозируемый высокий спрос на такие резервуары в будущем, в Великобритании практически нет производственных мощностей для изготовления сосудов высокого давления из композитных материалов.
И практически одновременно с предыдущей новостью компания Plastic Omnium объявляет о строительстве во Франции крупнейшего в Европе завода по производству водородных баллонов. Будущий завод будет производить 80 000 баллонов в год, первые из которых будут выпущены в 2025 году. Речь идет о разработке и производстве баллонов под давлением 700 бар для коммерческих автомобилей.
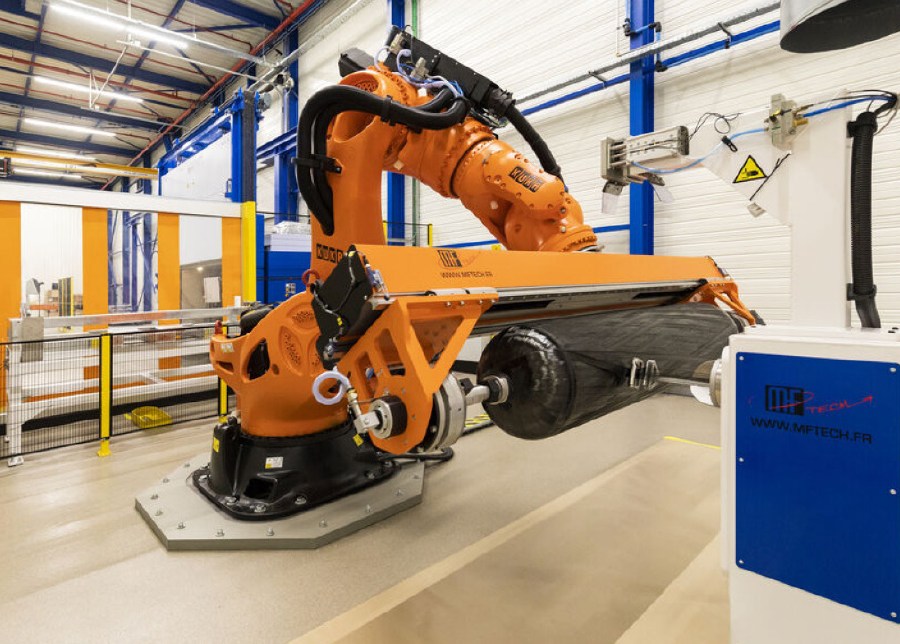
Фото 4. Планируемая мощность крупнейшего в Европе завода по производству водородных баллонов — 80 000 штук в год. (Источник: Plastic Omnium)
Plastic Omnium занимает уникальное положение на рынке баллонов благодаря своему историческому опыту и лидирующей позиции этой области. Plastic Omnium производит топливные элементы с самой высокой удельной мощностью на рынке и тесно сотрудничает с немецким производителем запчастей ElringKlinger.
Финансирование, выделенное на строительство нового завода, составит 74 миллиона евро. Это французское государственное финансирование является частью структуры PIIEC и поддерживает проекты, которые считаются важными для конкурентоспособности Европы.
От автомобильной темы переходим к композитам в авиастроении. Это статьи были на втором месте по популярности в зарубежной композитной прессе в 2022 году.
Vertical Aerospace провела пилотируемые испытания прототипа электрического конвертоплана, который планируют использовать в аэротакси. Инженеры были настолько уверены в конструкции, что первый испытательный полёт прошёл в пилотируемом режиме. В ходе него прототип, правда, лишь слегка оторвался от земли. Аппарат VX4 eVTOL является конвертопланом, то есть он взлетает вертикально подобно вертолёту, после чего поворачивает винты и продолжает лететь как самолёт.

Фото 5. Пилотируемые испытания прототипа электрического конвертоплана (Источник: Vertical Aerospace)
Всего на опытном конвертоплане установлено 8 винтов, из них 4 используется лишь при взлёте-посадке и складывается в крейсерском режиме. Vertical Aerospace заявляет о максимальной скорости 325 км/ч
и запасе хода более 161 км. Таким образом, конвертоплан сможет не только летать по городу, но и позволять путешествовать по небольшому региону. Также он способен выполнять некоторые лёгкие региональные обязанности. Разработчик утверждает, что получил более 1400 условных предварительных заказов от ряда авиакомпаний, туристических групп и других операторов. Это очень много — для сравнения: в год выпускается всего около 1000 гражданских вертолётов.
Для проектирования, испытаний и производства полностью композитного фюзеляжа, армированного углеродным волокном компания английская компания Vertical Aerospace, заключила контракт с итальянской компанией с Leonardo.
Leonardo имеет большой опыт в области композитных авиационных конструкций, полученный при участии в многочисленных гражданских и оборонных аэрокосмических программах.
Компания Airbus при разработке двухфюзеляжного самолета A350 приняла решение перейти на композитные материалы для обшивки крыла, стрингеров и 34-метровых лонжеронов крыла. Форма крыльев A350, напоминающая крыло чайки, потребовала интеграции двух угловых изменений задних лонжеронов, поэтому Airbus выбрал конструкцию, в которой задние лонжероны были разделены на три секции, каждая из которых была изготовлена с использованием автоматизированной укладки препрегов углеродного волокна на C оправки в форме. Секции лонжерона имеют длину чуть более 11 метров и после автоклавирования соединяются с использованием изготовленных на заказ пластин из углепластика для их сборки. Эти работы по изготовлению и сборке выполняются GKN Aerospace на своем предприятии в Филтоне, Великобритания.
Тем не менее, конструкции крыла следующего поколения, особенно те, которые предназначены для высокоскоростных самолетов, должны и будут развиваться до более интегрированной конструкции, которая позволит авиаконструкторам производить конструкции с совместным отверждением вне автоклава (OOA), которые могут удовлетворить высокие требования к характеристикам, стоимость и производственные требования.
Прошло совсем немного времени и компания GKN Aerospace получает новый заказ — цельный однокомпонентный 17-метровый лонжерон крыла изготовленный по технологии RTM.
Для изготовления лонжерона использовали двухслойное углеродное волокно NCF, поставляемое Teijin, которое пропитывали эпоксидной смолы Solvay Composite Materials.
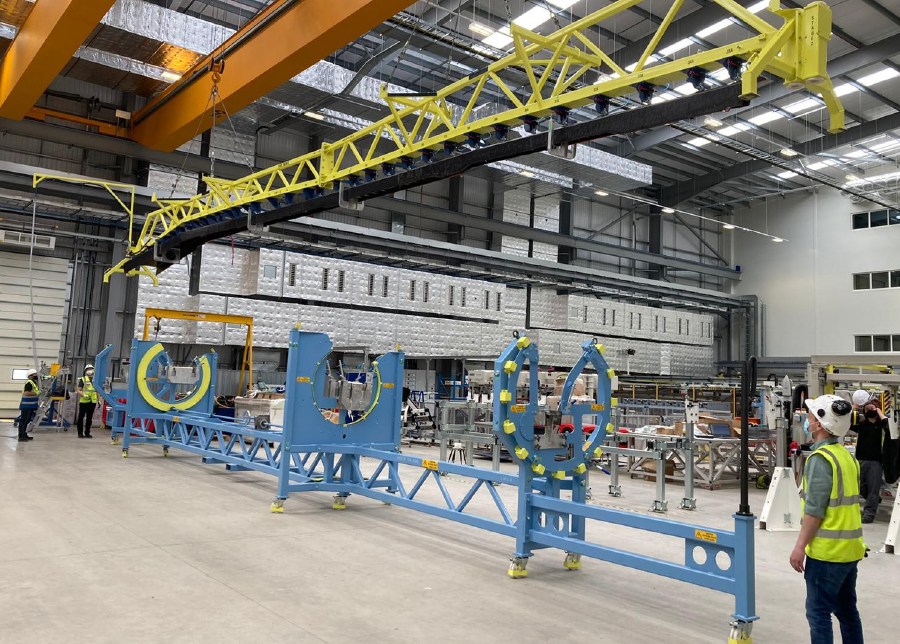
Фото 6. Готовый 17-метровый лонжерон поднимается из производственной оснастки Alpex (Источник: compositesworld.com)
Другая проблема была связана с самим процессом. Использование RTM требует, чтобы лонжерон был сначала предварительно отформован, а затем перенесен в соответствующую металлическую форму для заливки смолы и отверждения. Этот процесс не нов и, как правило, очень прост в управлении, но длина лонжерона добавляет уровень сложности, который пришлось решать GKN, особенно в условиях высокопроизводительного производства. «Расширение RTM до 17-метровой конструкции — нетривиальная задача, — отмечает специалист GKN Aerospace .
Процесс начался с выкройки армирующих материалов на автоматизированном режущем столе, после чего слои были собраны и размещены вручную в заданных местах на формовочной оснастке. После укладки каждого слоя его нагревали и прижимали для стабилизации.
Когда все слои были уложены, оснастку закрывали и нагревали для сшивания эпоксидного порошкового связующего и придания жесткости препрегу. Затем заготовка была перенесена с помощью крана из оснастки для предварительного формования в производственный оснастку. Эта оснастка имела встроенные термопары, а также датчики для измерения давления в форме, поступления смолы и степени отверждения, что помогало максимально контролировать процесс.
После того, как преформа была помещена на производственную оснастку, форма закрывалась и герметизировалась. Далее следовал процесс заливки эпоксидной смолы Solvay. Оборудование RTM, предоставленное компанией Composite Integration, включало в себя 200-литровую систему подачи смолы и насос, способный создавать давление до 10 бар .
В итоге GKN изготовила восемь образцов для оценки технологических возможностей системы. Три лонжерона были разрезаны для механических испытаний; два других использовались для испытаний на изгиб. Компания также провела обширный неразрушающий контроль (NDT). Все результаты испытаний были очень многообещающими, включая пористость <2%, и показали, что производственная стратегия, разработанная GKN, вполне работоспособна.
От авиастроения к теме биоматериалов и рециклинга. Множество работ посвящено применению биосмол и натуральных армирующих волокон для различные областей. Здесь же можно упомянуть несколько интересных статей о новых способах вторичной переработки связующих и армирующих материалов. А также любимая тема всех европейских СМИ — «Что делать с отслужившими свой срок лопастями ветряков?»
Компания Hexcel разработала новую линейку композитных материалов, изготовленных из смол биологического происхождения, армированных натуральными волокнами для отделки салонов автомобилей, яхт, для изготовления спортивного инвентаря и ветроэнергетики.
Ассортимент HexPly Nature включает проверенные смолы, такие как HexPly M49, M78.1-LT и M79, но с содержанием эпоксидной смолы биологического происхождения. Превосходные характеристики смолы остаются неизменными в новых продуктах серии Nature, сохраняя высокие механические характеристики и стабильные технологические свойства.
Кроме того, линейка продуктов HexPlyNature предлагает препреги, содержащие натуральные волокна, которые можно легко интегрировать в существующие производственные процессы.
На выставке JEC World в Париже компания Hexcel представила горные лыжи с использованием препрега из льняного волокна HexPly Nature Range M78.1-LT UD. Кроме своих экологических характеристик, препрег, армированный натуральным волокном, обладает отличными ударными характеристиками и превосходно гасит вибрации в лыжах.
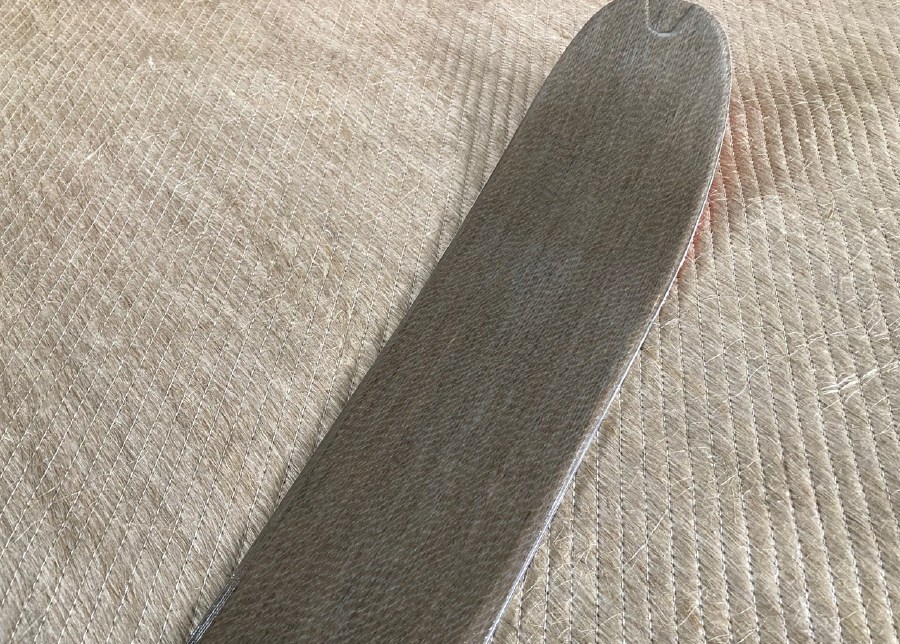
Фото 7. Компания Hexcel представила горные лыжи с использованием препрега из льняного волокна (Источник: jeccomposites.com)
В продолжение темы про лен, обзор еще одной статьи. Компания Bcomp планирует заменить девять внутренних элементов отделки из углекомпозита на композит, армированный льняными волокнами.
Новые внутренние элементы изготовлены с использованием инновационных технологий Bcomp ampliTex™ и PowerRibs™, которые используют естественные преимущества льняного волокна. Армирующая сетка powerRibs™ значительно повышает жесткость на изгиб тонкостенных элементов оболочки.
Детали, изготовленные из материалов ampliTex™ и powerRibs™, не только легкие, но и очень безопасные, поскольку в случае аварии или столкновения на них не остается острых краев или осколков. Bcomp и Porsche уже воспользовались этими преимуществами безопасности в ранее разработанном кузове, что привело, например, к снижению риска дефектов шин. Льняные композиты на 250% лучше гасят вибрации по сравнению с углеродным волокном. Еще одно преимущество льняного волокна — это шумоподавление.
Компоненты интерьера переданы гоночной команде Four Motors для проведения гоночных испытаний на выносливость на легендарной трассе Нюрбургринг. Компания Four Motors впервые участвовала в гонках с этими новыми компонентами интерьера во время шестичасовой гонки.
Благодаря сотрудничеству между инженерами Porsche и специалистами по натуральным волокнам в Bcomp качество компонентов из натуральных волокон в последние годы поднялось на новый уровень и превосходит углеродные волокна.
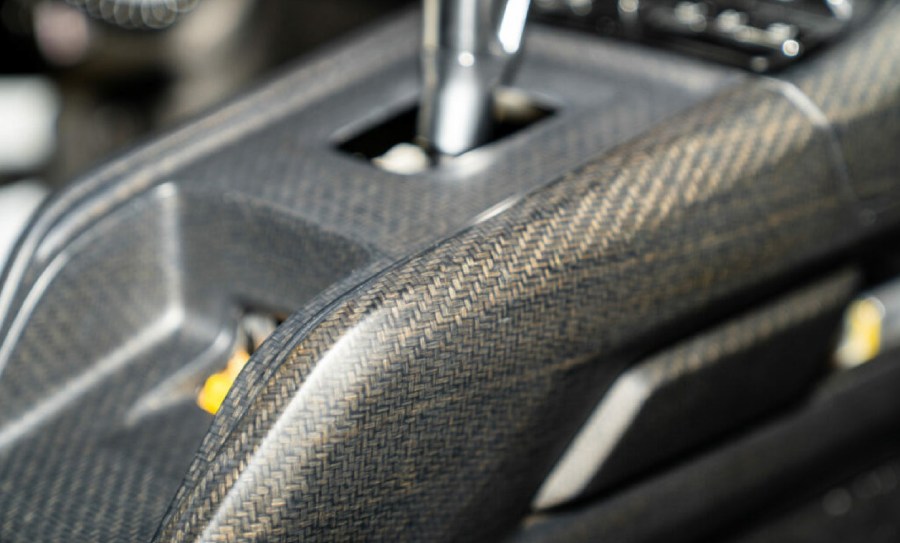
Фото 8. Экологичный интерьер гоночного автомобиля Porsche GT4 (Источник: jeccomposites.com)
Энергия ветра становится все более популярной формой возобновляемой энергии, но все еще существуют аспекты производства, эксплуатации и окончания срока службы ветряных турбин, которые производят отходы или вредные выбросы.
Существует ли надежное решение для предотвращения попадания лопастей ветряных мельниц на свалки? Аллан Корсгаард Поульсен, руководитель отдела развития ветроэнергетической компании Vestas , объясняет, что для достижения этой цели необходимо пройти три этапа. «Что касается лопастей из устаревшего парка, нам необходимо усовершенствовать существующие методы утилизации. Следующим шагом является усовершенствование методов отделения волокон от смолы для повторного использования. И, наконец, последний шаг — разрабатывать полностью перерабатываемые материалы для внедрения экономики замкнутого цикла для будущих ветряных турбин».
Поставщики, производители лопастей, OEM-производители и разработчики возобновляемых источников энергии по всему миру работают над решениями по переработке ветряных лопастей, и сейчас на рынке есть ряд многообещающих решений, которые появятся на горизонте.
Например, тайваньская компания Swancor и испанская Siemens Gamesa объявили о стратегическом сотрудничестве в области перерабатываемых лопастей ветряных турбин с намерением производить их с использованием перерабатываемой термореактивной эпоксидной смолы Swancor EzCiclo. Обе компании стремятся поставлять клиентам экологически чистые продукты и решения для переработки, чтобы достичь зеленой экономики замкнутого цикла и достичь углеродной нейтральности и инноваций в области новых материалов.
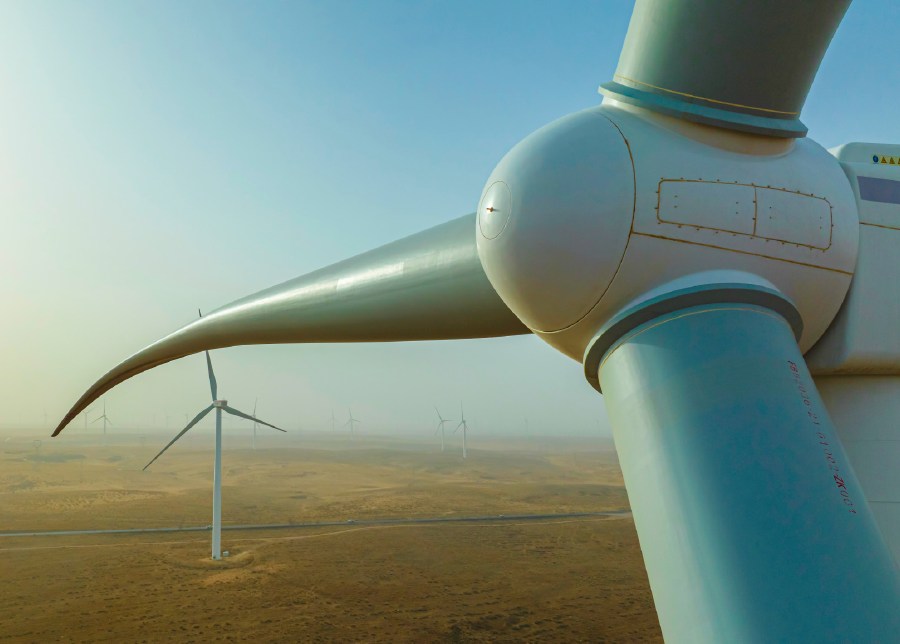
Фото 9. Swancor и Siemens Gamesa сотрудничают над созданием полностью перерабатываемой эпоксидной смолы (Источник: compositesworld.com)
Swancor, пионер оффшорной ветроэнергетики, занимается исследованиями и разработками (НИОКР) пригодной для повторного использования термореактивной эпоксидной смолы с 2015 года. Его раствор EzCiclo и растворяющая жидкость CleaVER в настоящее время проходят процесс квалификации поставщиков совместно с Siemens Gamesa с целью поставки ветроэнергетической компании.
По словам Swancor, сочетание этих технологий позволит восстанавливать и перерабатывать компоненты лопастей ветряных турбин после их вывода из эксплуатации. Восстановленные материалы, смолы, стекловолокна и углеродные волокна затем можно использовать в других целях. Сообщается, что в процессе переработки не образуются отработанные растворители и отработанные газы, что помогает решить экологические проблемы, возникающие в результате захоронения или сжигания отходов. Эта инициатива направлена на достижение цели полностью перерабатываемых лопастей ветряных турбин.
Аллан Корсгаард Поульсен из Vestas говорит: «Я хотел бы, чтобы другие отрасли производства композитных материалов подхватили это и инвестировали в разработку систем смол, которые легче перерабатывать или даже использовать в замкнутом цикле. Ветроэнергетика имеет большое количество композитных деталей, но мы не являемся отраслью с наибольшим количеством композитных отходов. Что происходит с композитными лодками в конце их жизни или с печатными платами в электронике? Я надеюсь, что ветроэнергетика станет пионером, и другие отрасли последуют ее примеру».