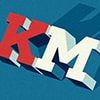
Оборудование METROM для пространственной механической обработки и 3D-печати
рубрика: оборудование
Умение мыслить нестандартно, по-новому, позволяет создавать инновационные решения. Именно эта идея была взята за основу при образовании в 2001 году компании METROM. Сейчас работой этого семейного предприятия управляет уже второе поколение его владельцев. А название METROM прочно ассоциируется с передовыми системами механической обработки с параллельной кинематикой, которые состоят из пяти позиционирующих стоек и внешней несущей конструкции, выполненной в форме икосаэдра.
Взяв за основу существующие разработки в области систем с шестью координатными осями (6-стоечных), основатель компании METROM исключил одну стойку и доработал проект первой рабочей модификации, которую уже затем усовершенствовали в ходе дальнейших исследований. Решение по исключению рабочей стойки позволило избавить рабочее пространство от ограничений, обусловленных максимальным углом наклона шпинделя в 30°. Теперь кинематическая система допускает углы наклона шпиндельной головки от 0° до 90°, а наличие поворотного рабочего стола позволяет обеспечить полную пятистороннюю механическую обработку изделий. Ключом к жесткости системы является внешняя несущая конструкция в форме икосаэдра, которая способна воспринимать значительные усилия от шпиндельной головки и передавать их на опорную поверхность.
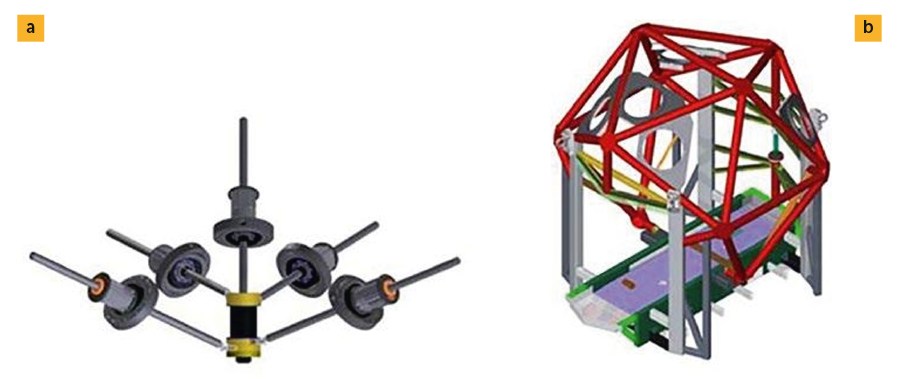
Рисунок 1. Принцип строения главного шпинделя (а) и модель двадцатигранной рамы (b)
Конструкция мехатронного высокоскоростного высокоточного оборудования представляет собой обрабатывающий узел (шпиндель), который приводится в движение посредством 5-ти стоек (рисунок 1-а), закрепленных на двадцатигранной раме (рисунок 1-b). Пять степеней свободы движения обеспечивают беспрепятственное управление движением шпинделя с режущим инструментом.
Первые системы были выполнены в виде стационарных станков с защитой расположенных внутри всех критически важных частей. Чтобы исключить попадание частиц удаляемого материала наружу, станки были оснащены встроенной системой вытяжки и полностью закрытым ограждением рабочей зоны. Внешний вид такого станка показан на рисунке 2, а его внутреннее пространство с большой рабочей зоной (диаметр 2800 мм и высота (z) 1000 мм) представлено на рисунке 3.
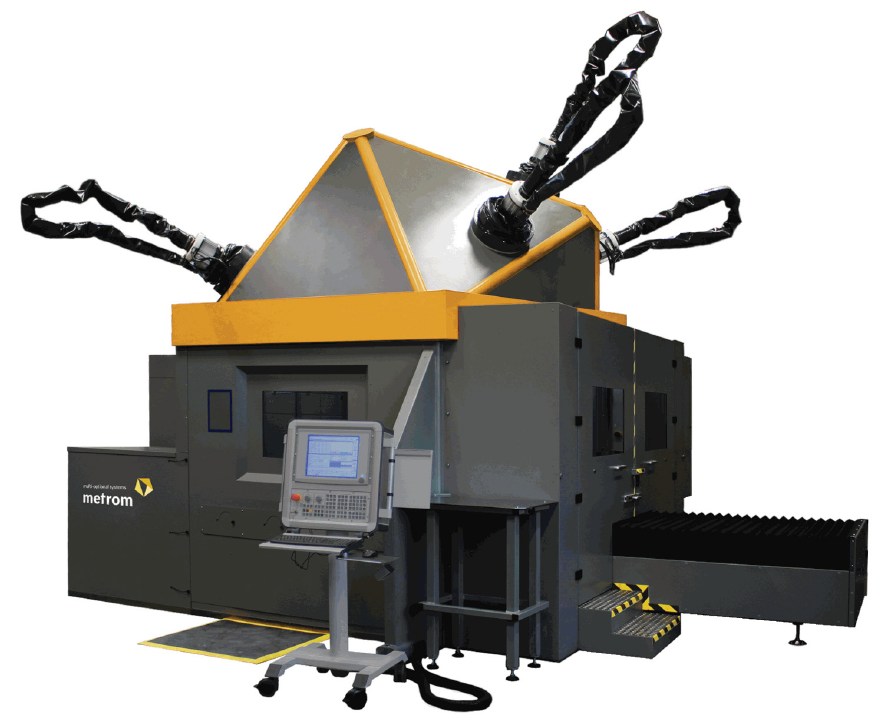
Рисунок 2. Металлообрабатывающий станок типа Р2030
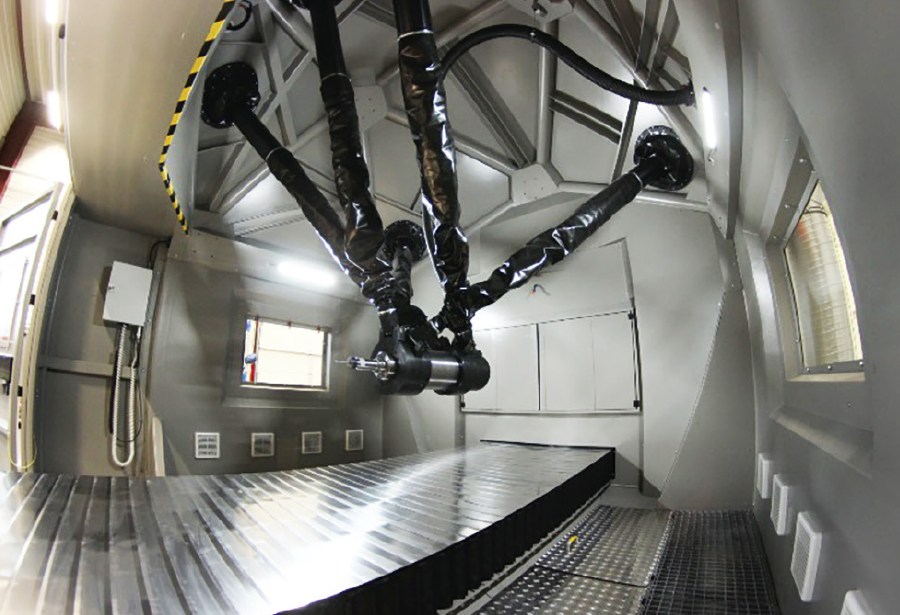
Рисунок 3. Внутренняя часть с 5-ю защищенными стойками
Такие стационарные системы позволяют обрабатывать изделия из углеродного волокна, карбида кремния, а также из металлов, полученных литьем в землю. Компанией постоянно ведутся работы по внедрению новых технологий, таких как ультразвуковое фрезерование, совершенствуется защита и система циркуляции воздуха. Кроме того, благодаря высокой жесткости одна и та же система может использоваться для обработки самого широкого спектра материалов. В их перечень входят алюминиевые сплавы, конструкционные стали, материалы высокой твердости (до HRC 62) и жаропрочные сплавы семейства Inconel. Примеры обработанных изделий из различных материалов показаны на рисунке 4.
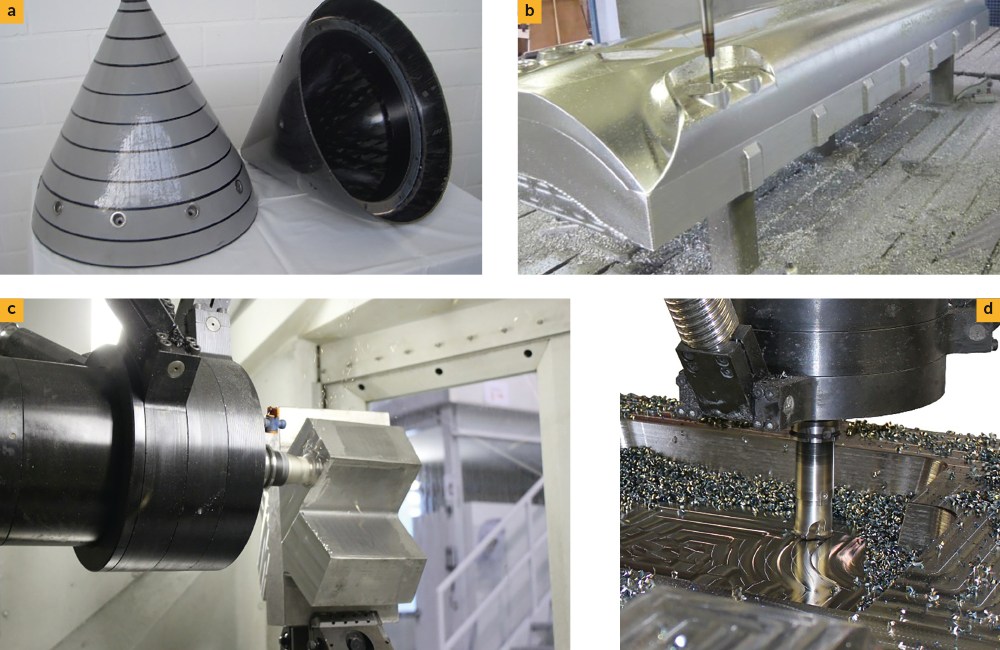
Рисунок 4. a — носовые обтекатели для самолетов, выполненные из углекомпозитов; b — алюминиевая форма для элементов отделки салона автомобиля; c — стальные узлы для конструкции крыши; d — стальные формы для штамповки.
Cтанки для обработки композитов в стандартном исполнении и под заказ
С оборудованием, которое работает на основе многостоечной параллельной кинематики, в сжатые сроки выполняется комплекс самой сложной обработки как обычных, так и композитных материалов.
В стандартном исполнении представлены 5, 6, 7-ми (и более) координатные станки следующих типов:
- стационарные станки с большой рабочей зоной;
- обрабатывающие центры портального типа;
- мобильные станки.
Преимущества оборудования METROM для обработки композитных материалов
Так как приводные стойки шпинделя обрабатывающих центров METROM находятся всегда выше зоны обработки, влияние побочных продуктов резки (абразивной пыли) на рабочие механизмы минимально.
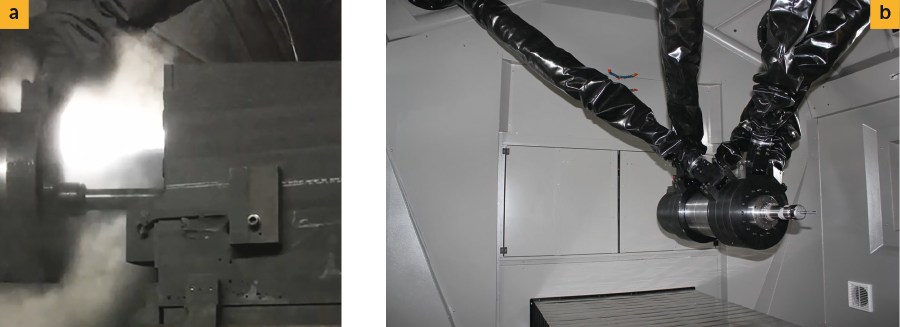
Рисунок 5. a — Работа в условиях обильного выделения абразивной пыли; b — Расположение рабочих стоек обрабатывающих центров METROM и оснащение их специальными кожухами
К тому же направляющие оснащаются специальными, не допускающими попадание пыли на оси кожухами с внутренним обдувом воздуха (рисунок 5-b).
Оборудование также оснащается станцией для чистки конуса шпинделя, инструментальной оснастки и инструмента перед его сменой, которая осуществляет обдув воздухом в 2-х или более положениях (рисунок 6-a). Магазин инструмента имеет закрытое герметичное исполнение (рисунки 6-b и 6-c).
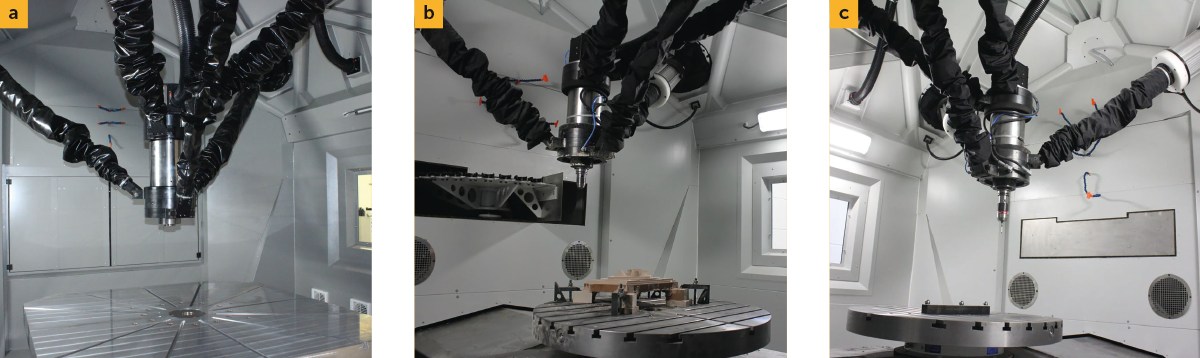
Рисунок 6. a — станция для чистки конуса шпинделя, инструментальной оснастки и инструмента перед его сменой, b,c — герметичное исполнение магазина инструмента
В рабочей зоне находится закрытый бокс для кнопок управления и маховика. Сделаны дополнительные уплотнения V-оси (стола перемещения), а также специальные крышки с прокладками для операций технического обслуживания. Стационарные станки и обрабатывающие центры обладают полностью закрытой рабочей зоной и комплектуются специальной системой вытяжки. Приточная система чистого воздуха обеспечивает уменьшение концентрации мелкодисперсной пыли в воздухе, а вытяжная система осуществляет отвод воздушной массы с примесями полимерной пыли.
Для предотвращения деламинации композита и сохранения структурной целостности слоев, прилегающих к месту реза или сверления, создаются особые условия работы с обрабатываемым изделием. Высокоскоростной режим достигается рабочей подачей до 60000 мм/мин и ускорением в 8–10 м/с2.
При необходимости глубина реза за один проход может быть настолько мала, что не будет приводить к деструктуризации поверхностных слоев и полимерной матрицы. За короткий промежуток времени станок может выполнить множество однородных операций с высокой степенью повторяемости параметров.
Высокая точность при обработке композитов очень важна, так как речь идет в основном о деталях аэрокосмической техники, энергетических устройств и прочего, где малейшее отклонение от расчетных параметров грозит изменением характеристик всей конструкции. А это может привести к разрушительным последствиям. Точность обработки по всей рабочей зоне составляет 0,005–0,0225 мм.
Чтобы предотвратить перегревание рабочих узлов оборудования и композита в месте обработки, разработчики предусмотрели охлаждение рамы и осей. Процесс осуществляется подачей охлаждающей жидкости по трубчатой конструкции, а благодаря воздушному охлаждению через шпиндель поддерживается комнатная температура рабочей зоны.
Мобильные станки и обрабатывающие модули
Уникальным решением являются мобильные 5-ти (и более) координатные станки МЕТРОМ (рисунок 7), которые позволяют осуществлять высокоскоростные высокоточные операции непосредственно на изделии без его перемещения. Особенно эффективными такие решения становятся при обработке габаритных изделий.
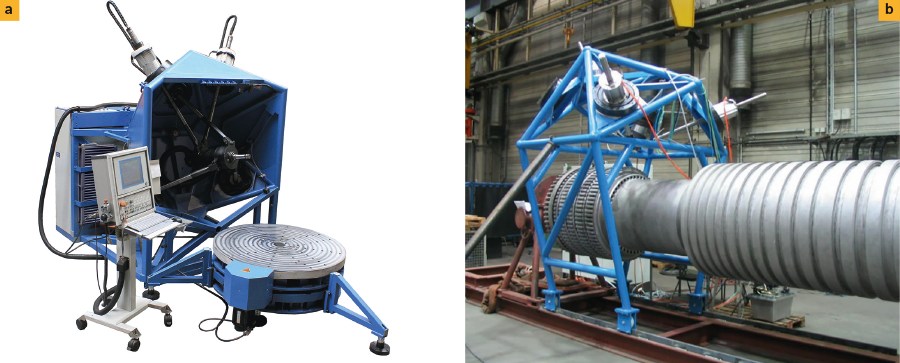
Рисунок 7. Мобильные 5-ти, 6-ти, 7-ми координатные станки METROM: a — портативный 6-ти координатный станок с поворотным столом, b — 5-ти координатный мобильный модуль, установленный на роторе газовой турбины (вес изделия около 15 тонн)
Использование таких станков в качестве модулей дает возможность построения гибких обрабатывающих комплексов с последующей перекомпоновкой под другие задачи при необходимости.
На рисунке 8 приведен пример концепции проекта по решению задачи обработки сверхгабаритных изделий из композитных материалов.
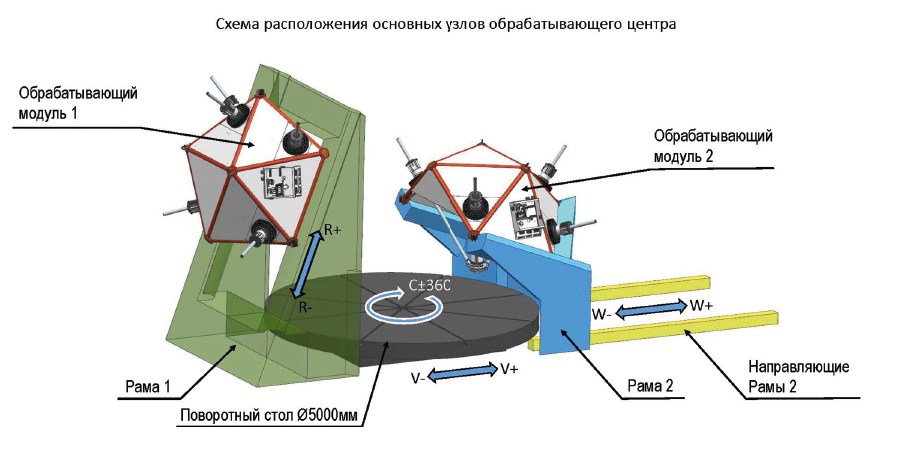
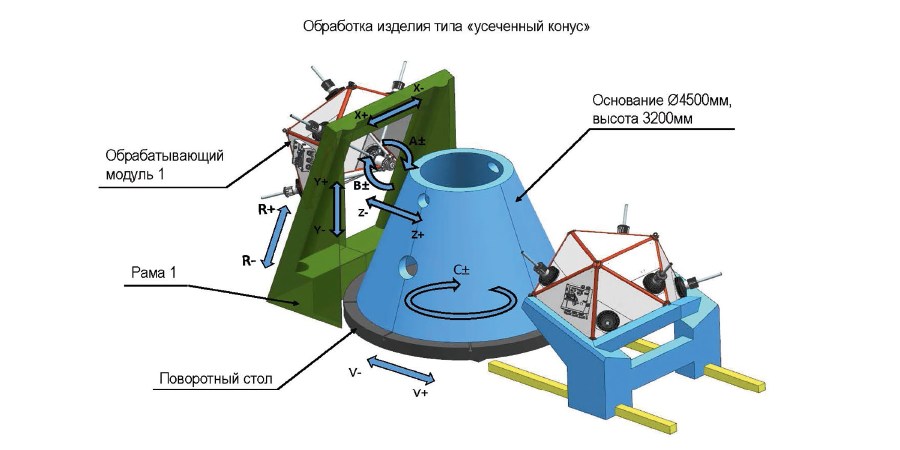
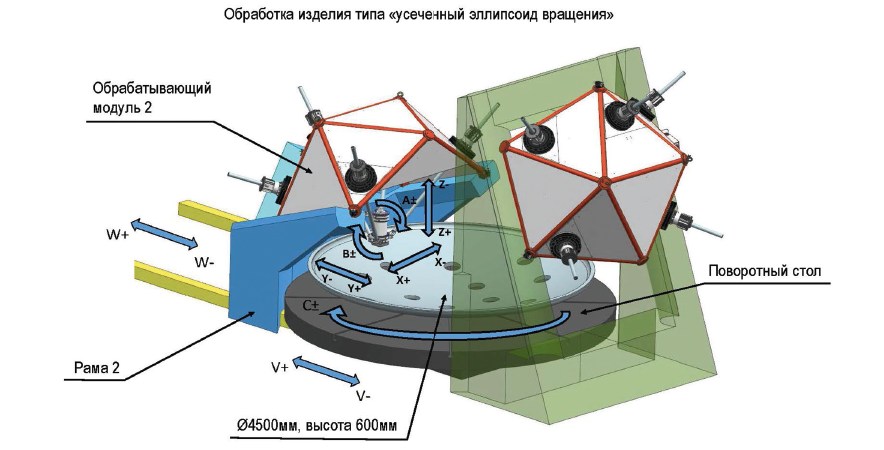
Рисунок 8. Гибкий обрабатывающий комплекс на основе мобильных 5-ти осевых станков METROM
Практика: обработка силицированного графита СГ-П 0,5П
Среди последних инжиниринговых проектов компании METROM в России следует отметить разработку технологии обработки изделий из силицированного графита СГ-П 0,5П.
Существующие технологии обработки этого материала всегда связаны с вопросами безотказности работы применяемого оборудования, его ремонтопригодностью и сроком эксплуатации. Повсеместно встречаются проблемы высокого износа применяемого оборудования из-за высокой запыленности рабочей зоны, что увеличивает себестоимость изготовления продукции.
Компания METROM совместно с компанией KNOFF Werkzeuge (производитель инструмента) разработали и успешно апробировали технологию 5-ти осевой сухой механической обработки силицированного графита СГ-П 0,5П для одного из машиностроительных предприятий ГК «Росатом». Достигнуты отличные результаты производительности.
Как уже отмечалось ранее, оборудование от METROM использует в своей конструкции принципы 5-ти стоечной параллельной кинематики, что обеспечивает повышенный срок службы и ремонтопригодность при обработке особо пыльных материалов. Стоимость приобретения и владения у станков METROM, подходящих для обработки силицированного графита, значительно ниже, чем у используемых в настоящее время решений на основе станков классической компоновки с ультразвуковой оснасткой.
Пример обработки вы можете увидеть на рисунке 9
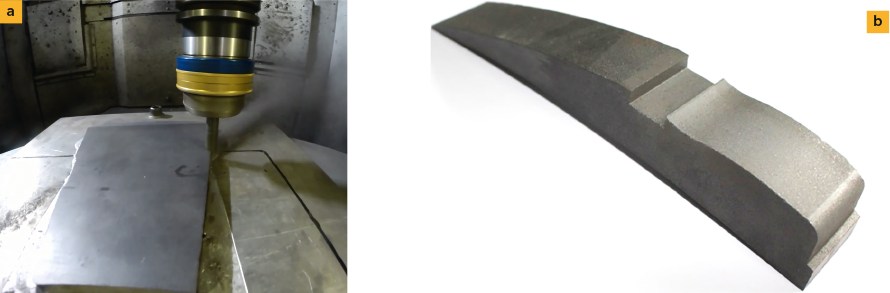
Рисунок 9. a — 5-ти осевая сухая механическая обработка силицированного графита СГ-П 0,5П; b — Обработанные изделия с радиусами и криволинейными поверхностями
Аддитивные технологии с METROM: увеличение производительности в 100 раз!
Производители изделий регулярно ставят перед разработчиками оборудования новые задачи, связанные с расширением функционала станков и уровня автоматизации технологического процесса, направленные на оптимизацию производства и снижение затрат, возникающих, например, при перемещении изделий между отдельными технологическими установками.
В связи с этим компания METROM постоянно находится в поиске оригинальных решений, которые позволят расширить возможности её оборудования для более полного удовлетворения нужд заказчиков. В качестве примера такого дополнительного технологического решения можем привести разработку мобильного обрабатывающего центра. Он предназначен для ремонта стальных литейных форм для автомобильных деталей, которые производятся последовательным сочетанием 3D-печати проволочным металлических материалом, выполняемой разработанным компанией GEFERTEC модулем, с последующими операциями фрезерования и сверления. После нескольких месяцев эксплуатации такие формы подвергаются износу, и сокращение сроков их восстановления обеспечивает автопроизводителям существенную экономию времени и трудозатрат. Компания METROM предлагает заказчикам мобильный обрабатывающий центр с 5-ю координатными осями, который в одном положении установки выполнит измерение заготовки, сварку по заданному контуру и требуемую механическую обработку (рисунок 10).
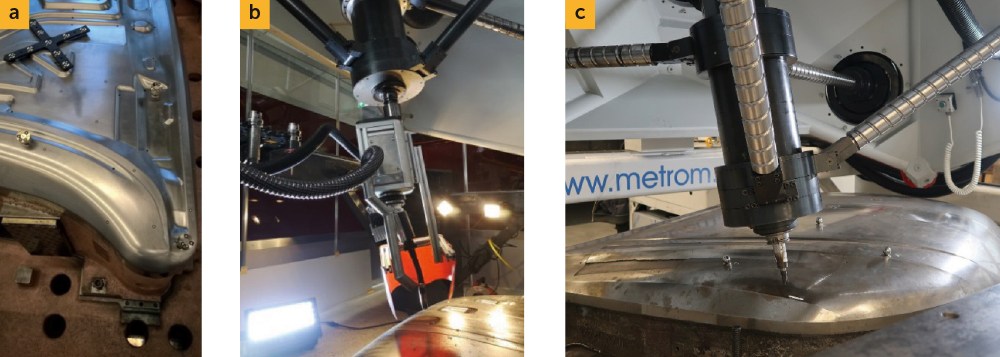
Рисунок 10. a — измерение формы, подлежащей ремонту; b —наплавка дополнительных слоев; c —фрезерование для восстановления геометрии
После завершения фрезерования применяется инструмент для устранения шероховатости поверхности, который также устранит дефекты поверхности формы наплавкой или наклепом, а также может увеличить твердость на отдельных ее участках. Все инструменты и технологические модули доступны для применения благодаря функции автоматизированной замены инструмента внутри станка, поэтому влияние оператора на работу системы ограничено выбором программы обработки. Никто и никогда ранее не выпускал подобные системы, а роботы, которые используются для автоматизированной сварки, не обладают точностью позиционирования и жесткостью конструкции, достаточными для осуществления механической обработки.
Помимо послойного наращивания в составе систем METROM доступны множество других достойных упоминания технологий. Например, сварка трением с перемешиванием (FSW), которая в определенных условиях может быть использована для соединения конструкций из углекомпозитного материала или лазерная порошковая сварка для высокоответственных изделий.
Высокопроизводительный технологический процесс послойного изготовления пластмассовых изделий с использованием стандартных гранул
Мы упомянули о 3D-печати металлов и хотим отдельно представить новинку в области объёмной печати из пластмасс, а именно высокопроизводительный технологический процесс послойного изготовления пластмассовых изделий с использованием стандартных гранул.
3D-печать представляет собой очень быстроразвивающуюся технологию, которая открывает заказчикам новые возможности производства. Институт оборудования и технологий формования Фраунгофера (Fraunhofer Institute for Machine Tools and Forming Technology — Fraunhofer Institute IWU) разработал инновационные методы изготовления пластмассовых изделий, в основе которых лежит технология послойного наращивания. Одним из таких новых методов является оснащение 5-ти стоечного станка METROM экструзионным модулем для пластифицированного материала, который способен работать со стандартными гранулами пластмассы. Это позволило обойти существующие технологические ограничения и создать новый процесс 3D-печати с высокой производительностью.
3D-печать пластмассовых изделий в настоящее время осуществляется разнообразными методами, такими как лазерное спекание (SLS), послойное наложение расплавленной нити (FDM, FLM) или технология Polyjet , а также стереолитография (SL).
Технология FDM/FLM, прежде всего, впечатляет своим простым и экономичным принципом, а также возможностью обработки выбранных стандартных материалов. Пластмассовая нить проходит через горячее сопло подающего блока и в пластифицированном состоянии наносится слоями на рабочую платформу. Однако существует ограничение скорости этого процесса, обусловленное, с одной стороны, низкой производительностью пластификации в горячих соплах, а с другой стороны — относительно низкой скоростью перемещения системы печатающей головки.
Система 3D-печати Института Фраунгофера IWU была разработана совместно с автомобильной компанией BMW и показала восьмикратное увеличение производительности за счет объединения этой технологии со скоростью обработки металлорежущего станка. Метод SEAM основан на современной технологии обработки пластмасс, в которой шнековый экструдер способен обеспечить расход материала через сопло диаметром 1 мм на уровне 5 кг/ч. Для сравнения: в технологии FLM с пластмассовой нитью для печати изделия весом в один килограмм затрачивается около 20 часов, а печать по методу SEAM — в 100 раз быстрее.
В системе 3D-печати SEAM пластмассовые гранулы, в пластифицированном состоянии проходя через модифицированный экструдер с одним шнеком и инструмент с соплом, ориентированным под углом 90°, выталкиваются на рабочую платформу машины (рисунок 11).
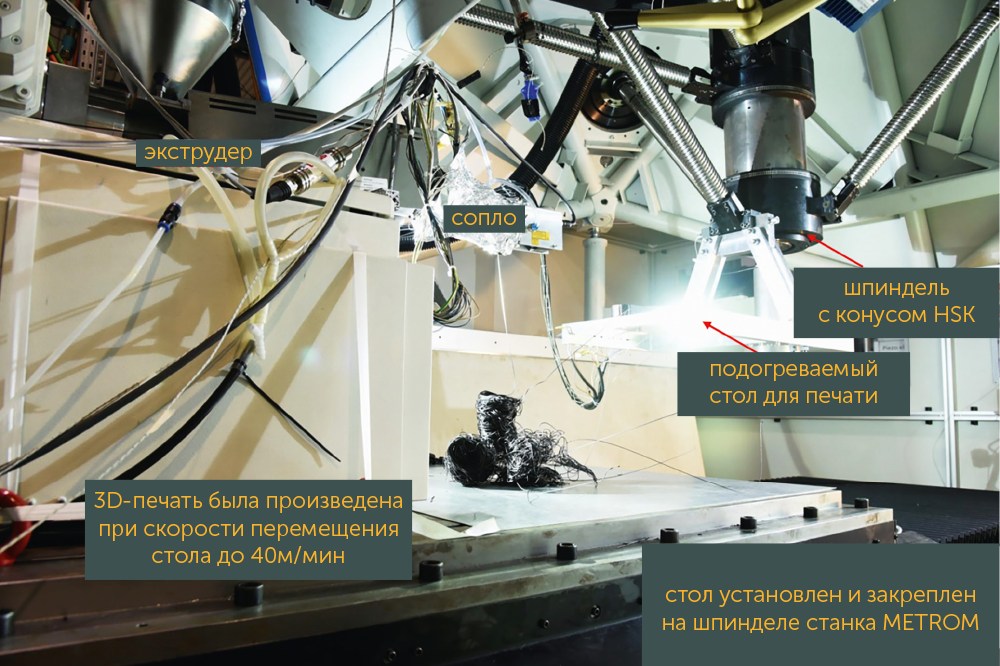
Рисунок 11. Экспериментальная установка SEAM: экструзионная головка для пластифицированного материала вместе с подвижной платформой приводится в движение и управляется при помощи 5-ти осевой системы с параллельной кинематикой от компании METROM
Перемещение рабочей платформы на первом этапе было реализовано при помощи 5-ти осевой системы с параллельной кинематикой от компании METROM (рисунок 12), рабочая скорость которой может достигать 800 мм/с. Система перемещения с 5-ю осями отличается, прежде всего, высокими динамическими характеристиками и малыми перемещаемыми массами, а значит, обеспечивает высокую точность позиционирования и траектории. Эти свойства делают ее идеальной системой для перемещения рабочей платформы.
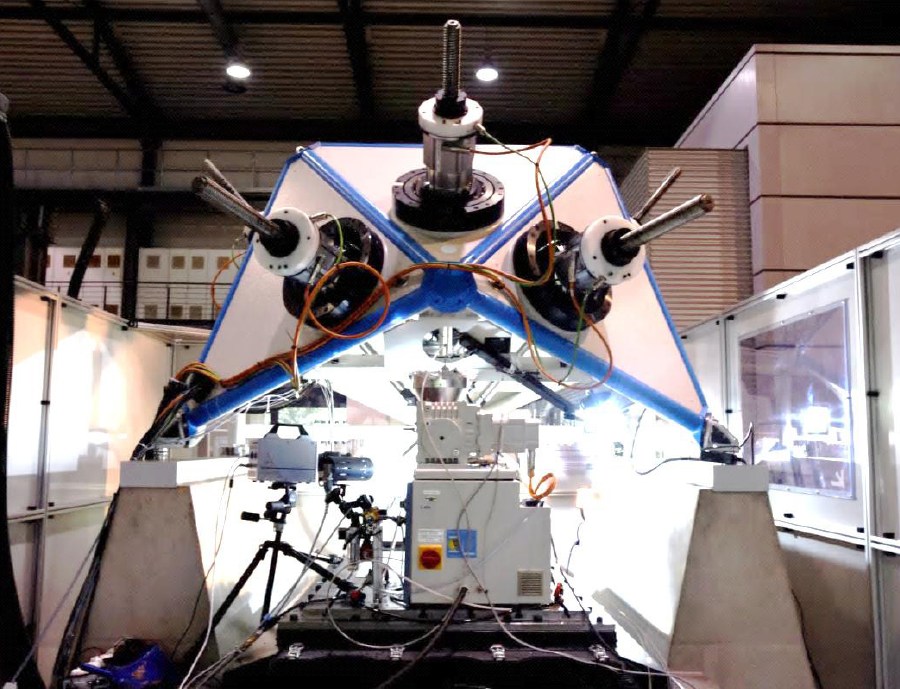
Рисунок 12. Технологическая установка на базе 5-ти осевой системы с параллельной кинематикой от компании METROM, экструзионный модуль расположен перед станком
Новая технология SEAM, в которой вместо дорогостоящей нити FLM используются стандартные пластмассовые гранулы, позволяет производить прочные пластиковые изделия. Если новый процесс сравнить по материальным затратам с технологиями FDM/FLM, то окажется, что он обеспечивает 200-кратную экономию. На начальном этапе испытаний был использован полиамид, армированный углеродным волокном (PA 6 CF), характеристики которого составили около 80% от характеристик образца, изготовленного литьем под давлением. Кроме того, хорошие результаты были достигнуты и у других стандартных пластмасс, таких как полипропилен или термопластичные эластомеры (ТРЕ), применяемые для изготовления деформируемых изделий, как показано на рисунке 13. Использование эластомеров позволяет печатать уплотнения или демпфирующие элементы.
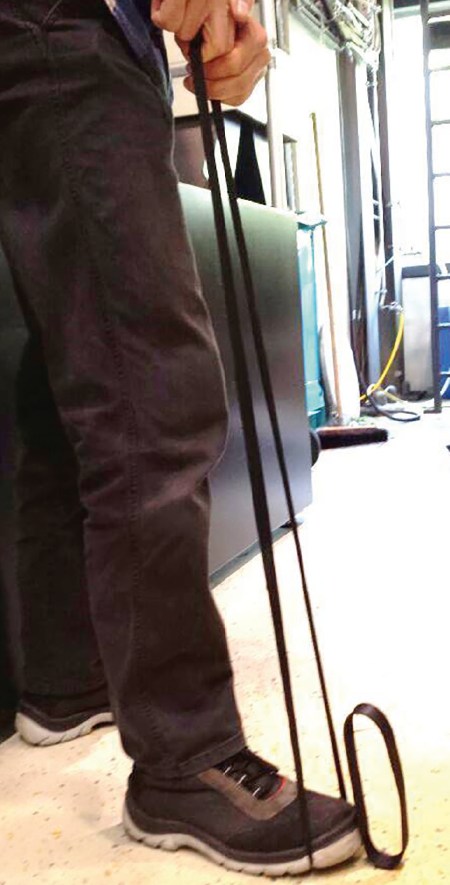
Рисунок 13. Изделие из термопластичного эластомера, полученное 3D-печатью (твердость по Шору 71, предел прочности на разрыв 10,5 МПа)
Классические заготовки, изготавливаемые из пластмасс с помощью литья под давлением, как правило, не предполагают дальнейшей обработки и имеют вид тонкостенных конструкций. Технология SEAM позволяет формировать изделие с разной толщиной стенок за счет изменения скорости перемещения стола и производительности экструзионной головки. Это позволяет исключить занимающий очень много времени процесс заполнения поверхностей и существенно повысить скорости обработки. На рисунках 14 и 15 показаны экспериментальные образцы, выполненные из полиамида, армированного углеродным волокном (PA 6 CF), с углами свеса до 46°, напечатанные без использования опорных конструкций. Процесс изготовления проходил в нормальных условиях помещения с контролем температуры на рабочей платформе или в зоне подачи материала.
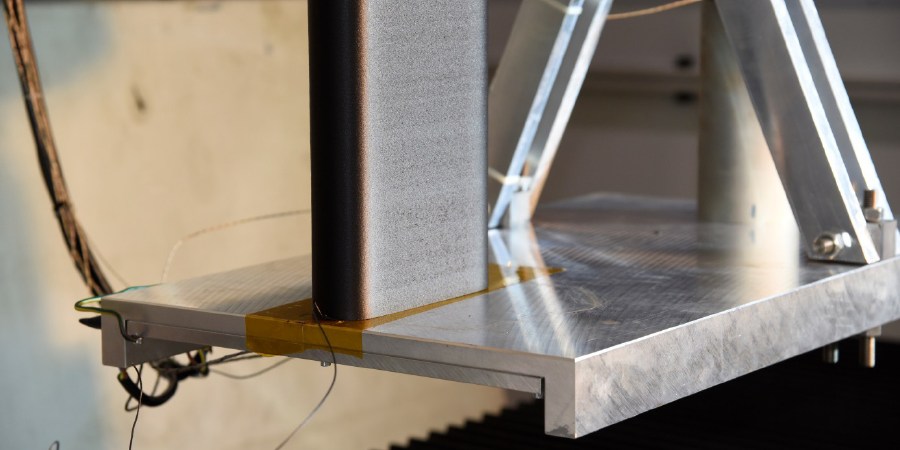
Рисунок 14. Напечатанное экспериментальное изделие: высота 300 мм, толщина стенки 2 мм, время изготовления 18 минут
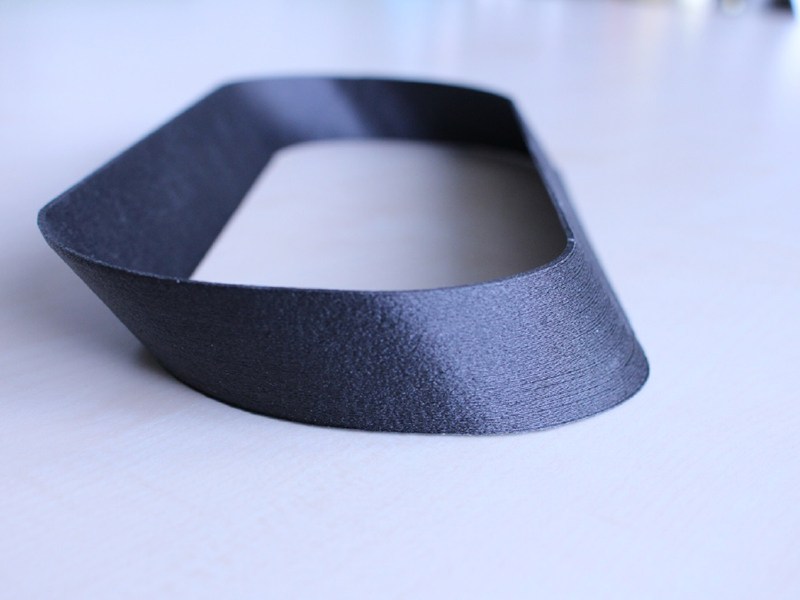
Рисунок 15. Экспериментальное изделие с углами свеса до 46°, изготовленное по диагональной схеме
Регулирование подачи материала в зависимости от скорости процесса требуется для управления печатью криволинейных и угловых элементов, а также при перемещениях рабочего органа без расхода материала. Из-за очень большой инерционности процесса пластификации в экструдере изменение расхода материала невозможно, в отличие от скорости перемещения. В силу этого был разработан дополнительный блок, располагаемый перед экструдером, который имеет расход материала, зависящий от скорости в диапазоне 0–100%.
В настоящее время устройство, находящееся в пробной эксплуатации, обеспечивает контроль расхода в классических процессах FLM при производстве сложных фасонных конструкций.
Новая технология SEAM подходит для производства крупногабаритных изделий и значительно расширяет возможности эффективного производства пластмассовых компонентов с помощью 3D-печати. Уже были изготовлены первые детали большого размера для вакуумных зажимных приспособлений (рис. 16), и выполнена непосредственная обработка крупногабаритных компонентов из волокнистых композитных материалов, как показано на рисунке 17. Кроме того, сами формы для изготовления больших изделий из пластмасс, армированных углеродным волокном, сначала можно напечатать методом 3D-печати, а затем механически обработать на той же самой технологической установке.
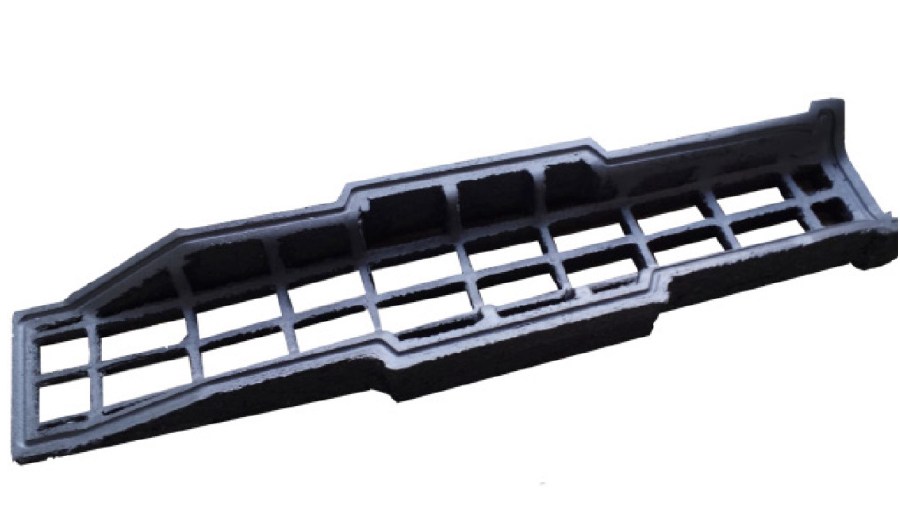
Рисунок 16. Вакуумное зажимное приспособление, изготовленное методом 3D-печати
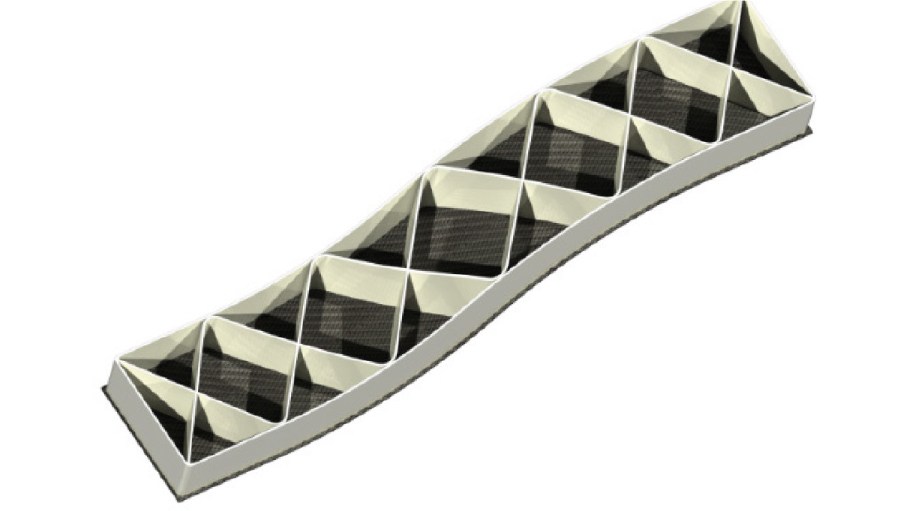
Рисунок 17. Легкий компонент конструкции, изготовленный методом 3D-печати
Технология SEAM является значимым этапом в дальнейшем развитии технологий аддитивного производства для промышленного применения и может стать решающим шагом к повышению производительности процессов 3D-печати. Экструзионный модуль SEAM был полностью модифицирован для использования в станке компании METROM с целью увеличения свободы перемещения. Полная 5-ти осевая печать и механическая обработка уже могут быть выполнены с помощью мобильного станка METROM, как показано на рисунке 18.
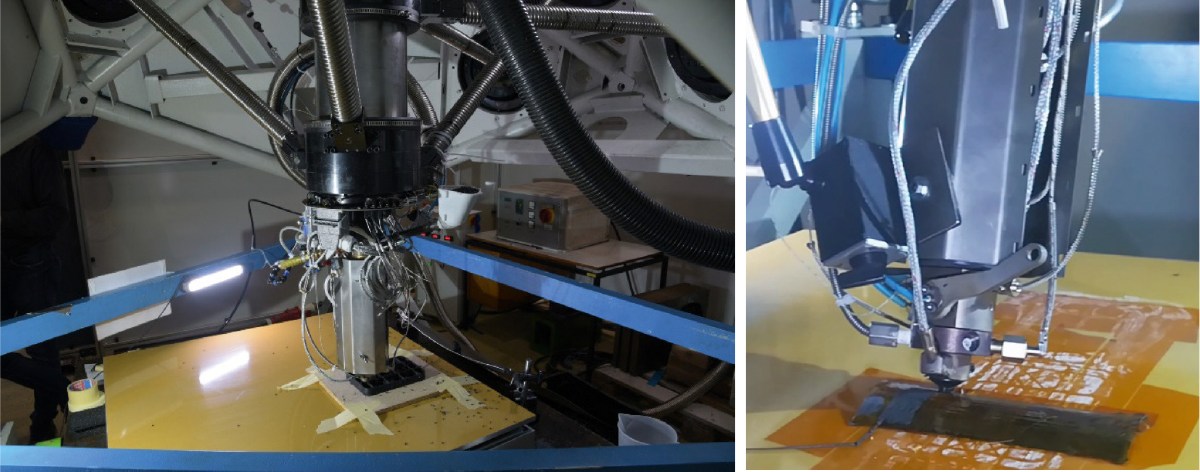
Рисунок 18. 5-ти осевая печать изделий на станке METROM
В ходе технологического процесса могут использоваться ускорения до 10 м/с² и быстрые изменения направления движения, особенно необходимые при изготовлении коротких углов. А дополнительная поворотная или продольная ось еще больше увеличит подачу и скорость наращивания изделий. Это станет частью следующих исследовательских проектов, запланированных на 2019–2020 гг.
В ближайшем будущем для создания новых направлений деятельности планируется также исследовать возможность работы и с другими материалами, например, полимерами с внедренными дополнительными твердыми элементами.