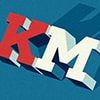
Композитные материалы в автомобилестроении: новый уровень торможения
рубрика: применение
В статье рассматривается применение композитных материалов в автомобилестроении с целью улучшения тормозных свойств транспортных средств при высоких скоростях, основные преимущества таких тормозных систем и их недостатки.
История тормозных систем в транспортной промышленности насчитывает более ста лет. Сначала использовались механические тормоза, которые работали по принципу нажатия тормозных колодок на поверхность диска. Однако, с ростом скорости и веса транспортных средств, механические тормоза стали недостаточно эффективными, что привело к созданию гидравлических тормозов. Спустя некоторое время, производители стали искать новые материалы для тормозных дисков, которые были бы более легкими, прочными и долговечными, чем стандартные металлические диски.
Первые углерод-керамические тормоза были разработаны в 1970-х годах и использовались в авиационной и космической промышленности. В их конструкции применяются особые композиты CMC (Ceramic Matrix Composites) — это материалы, в которых армирующие волокна соединены с керамической матрицей.
Керамические материалы в целом, а также CMC в частности, обладают высокой температурной стойкостью (могут выдерживать температуры выше 1000°С) и жесткостью, что делает их привлекательными для применения в тормозных системах самолетов. При высоких скоростях, во время взлета или посадки, тормозные системы подвергаются значительным термическим нагрузкам, которые могут привести к деформации и износу традиционных металлических тормозных компонентов. Применение СМС увеличивает срок службы и надежность тормозных систем, что является критически важным для безопасности полетов. Кроме того, CMC обладают легким весом, а уменьшение массы тормозных систем может улучшить экономику полетов, снизить износ других компонентов самолета и увеличить его грузоподъемность.
Углерод-керамические тормоза также используются в грузовых и пассажирских поездах, для обеспечения безопасности и более длительного срока службы тормозных систем. CMC обладают высокой устойчивостью к коррозии, что делает их привлекательными для применения в условиях высокой влажности или кислотности, например, при работе в агрессивных окружающих средах.
Первым автомобильным производителем, который применил углерод-керамические тормоза в своих автомобилях, была компания Porsche в 1988 году на модели Porsche 911 Turbo S (Type 964). Инновационные тормоза были доступны как опциональное оборудование и отличались более высокой стоимостью по сравнению с традиционными металлическими.
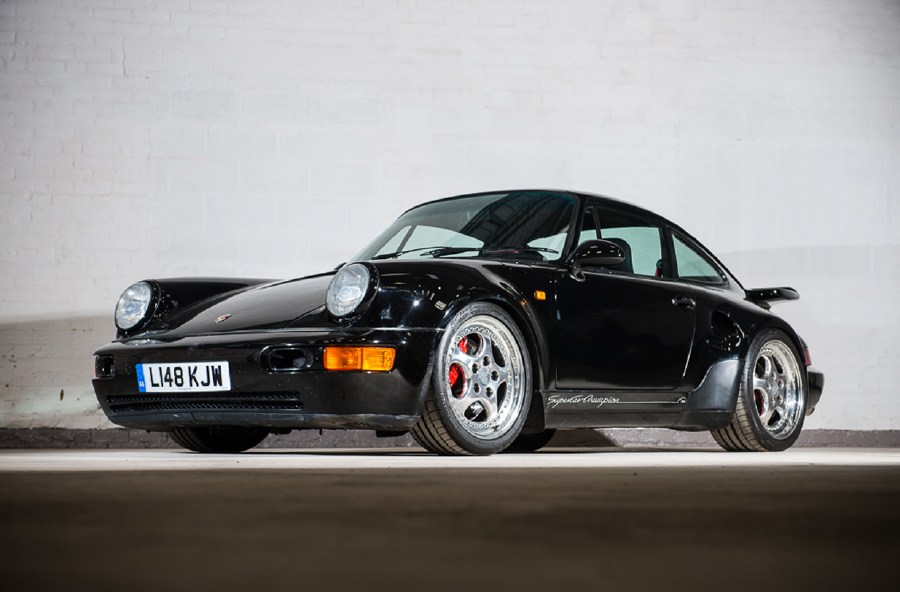
Porsche 911 Turbo S (Type 964). Источник: www.autoevolution.com
С тех пор углерод-керамические тормоза стали стандартным оборудованием в автомобилях с высокой производительностью, таких как Porsche, Lamborghini, Ferrari и других. Сегодня они также используются в гоночных болидах.
Углерод-керамические тормоза, также известные как керамические тормоза или CCM-тормоза (от Carbon-Ceramic-Matrix), представляют собой системы, в которых тормозные диски изготавливаются из композитного материала на основе углерода и керамики.
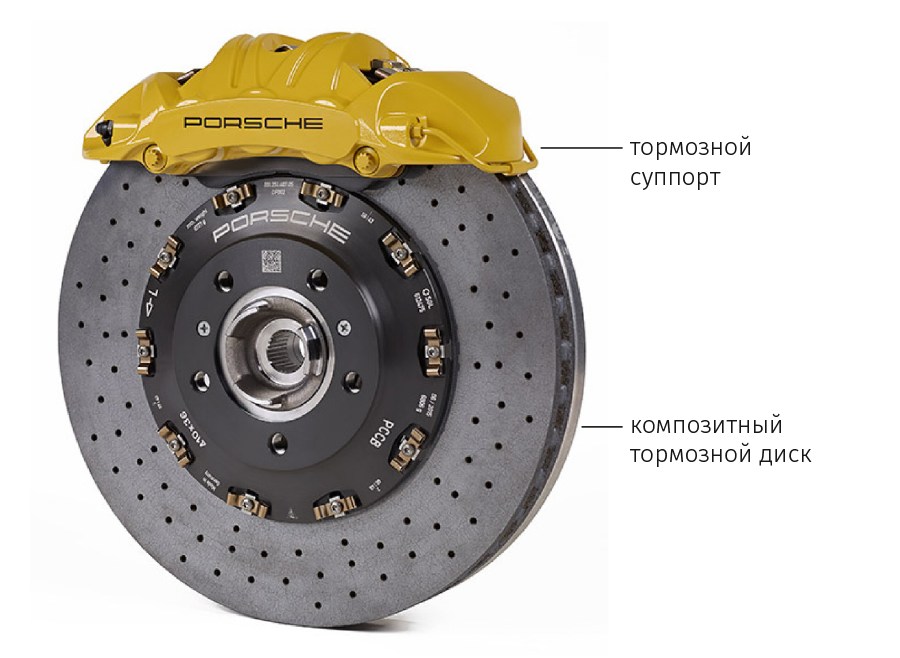
Общий вид тормозной системы CCM от компании Brembo. Источник: www.bremboparts.com
В целом, CCM системы представляют собой технологически продвинутую и высокоэффективную систему торможения, которая обеспечивает высокую жесткость, легкость, термическую стабильность и износостойкость.
Этапы производства
Каждый производитель ССМ-систем использует свои методы и разработки, обычно являющиеся корпоративной тайной. Но основной технологией для производства дисков таких систем является PIP (сокращение от Polymer Infiltration and Pyrolysis) что можно перевести как «Пропитка полимером и его последующий пиролиз».
Основными компонентами для создания композита по этой технологии являются армирующий наполнитель (в основном углеродное волокно) и полимер. Одним из наиболее распространенных полимеров, используемых в PIP-технологии, является полиимид. Также могут использоваться другие полимеры, например, полиэтиленимин (PEI), полиариламид (PAA) и полиэтиленоксид (PEO). Выбор конкретного полимера зависит от требований к конечному материалу и условий производства.
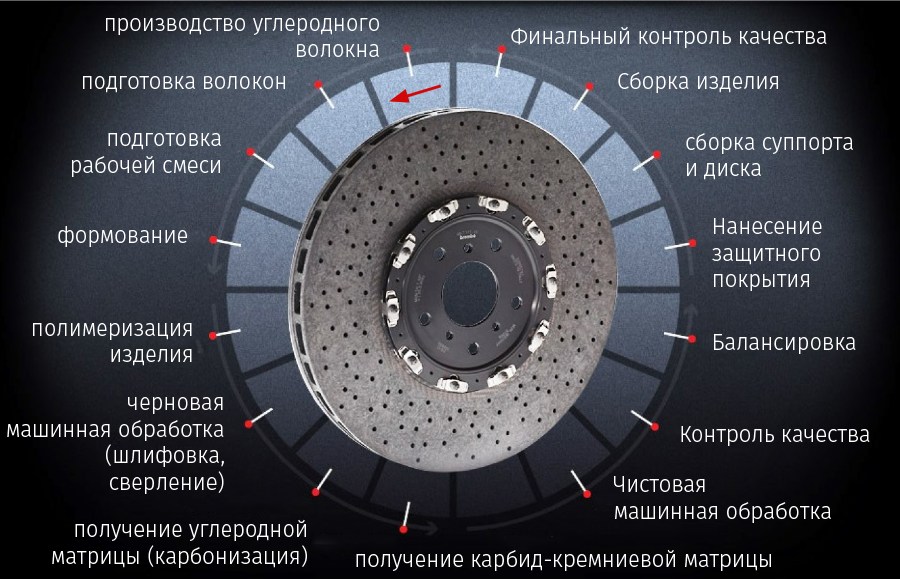
Этапы производства керамического тормоза от компании Brembo. Источник: www.bremboparts.com
На первом этапе происходит подготовка рабочей смеси. Рубленое волокно (конфигурация волокон варьируется в зависимости от желаемых свойств будущего изделия) пропитывается раствором полимера. Суть этого этапа в равномерном заполнении пространства между волокнами растворённым полимером.
Готовую смесь помещают в алюминиевую форму и запекают при температурах 500–700°С в течение 2х часов. Во время этого процесса происходит разложение растворителя и образование полимерной матрицы вокруг углеродных волокон. Затем изделие охлаждают в холодной воде и производят высокоточную механическую обработку при помощи компьютерных систем ЧПУ: шлифовка и сверление вентиляционных каналов.
Следующий этап — карбонизация. Изделие помещают в высокотемпературную печь, где оно нагревается до температуры свыше 1000°С в течение 1–2 дней. Во время этого этапа происходит процесс карбонизации полимера и образование углеродной матрицы.
Следующий этап — получение карбид-кремниевой матрицы. В тигель с установленным изделием добавляют мелкодисперсный порошок кремния. Далее диск подвергают дополнительной термической обработке при температуре около 1500°С, при которой происходит взаимодействие кремния с углеродным остатком. На выходе получается композит с уникальными свойствами.
Следующий этап — повторная обработка поверхности. Это может включать в себя шлифовку, полировку, нанесение защитного покрытия и т.д. Далее идет контроль качества: визуальный осмотр, измерение размеров и формы, анализ химического состава, испытания на прочность и т.д. После всех этапов происходит сборка и финишное тестирование готового изделия.
Подробнее о технологии PIP для производства тормозных дисков вы можете узнать в этом видео:
Таким образом, технология PIP представляет собой сложный процесс изготовления композитных материалов, а производство CCM-тормозов является трудоёмкой задачей, который требует использования специального оборудования и квалифицированных специалистов. И тем не менее CCM-тормоза являются одними из самых эффективных и продвинутых тормозных систем в настоящее время.
Преимущества и недостатки
Преимущества CCM-тормозов:
- Высокая термическая стабильность: CCM-тормоза могут выдерживать высокие температуры, что позволяет им обеспечивать стабильную работу при длительных и интенсивных нагрузках.
- Легкий вес: CCM-тормоза значительно легче стальных тормозов, что позволяет уменьшить вес автомобиля и улучшить его динамические характеристики.
- Высокий коэффициент трения: CCM-тормоза обеспечивают более высокий коэффициент трения, что позволяет уменьшить тормозной путь и улучшить управляемость автомобиля.
- Долговечность: CCM-тормоза имеют большую стойкость к износу, что позволяет им дольше служить, чем традиционные стальные тормоза.
Недостатки CCM-тормозов:
- Высокая стоимость: CCM-тормоза стоят значительно дороже стальных тормозов.
- Хрупкость: CCM-тормоза более хрупкие, чем стальные тормоза, и могут легко повредиться при механическом ударе.
- Необходимость прогрева: CCM-тормоза требуют прогрева перед использованием в холодных условиях, чтобы избежать трещин и повреждений при резком изменении температуры.
Одним из самых важных свойств композитных тормозных колодок является их способность к торможению при экстремальных температурах. Когда скорости превышают 300–400 км/ч вопрос безопасности, управляемости и сцепления с дорожным покрытием перекрывает цену производства.
Основные производители ССМ-систем
На сегодняшний день, несколько компаний занимаются производством углерод-керамических тормозов для автомобилей и других транспортных средств. Они используют различные технологии и материалы, чтобы достичь наилучшей производительности и долговечности своих продуктов.
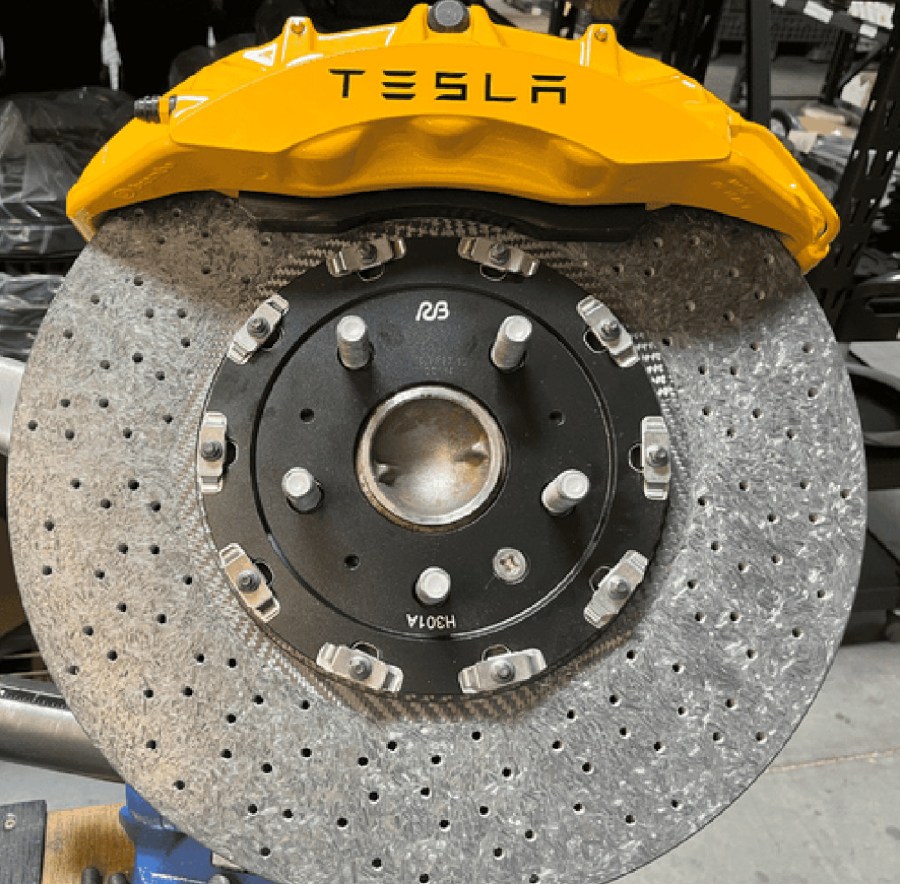
Углерод-керамические тормоза от компании Tesla. Источник: racingbrake.com
Одним из крупнейших производителей углерод-керамических тормозов является компания Brembo, которая была основана в Италии в 1961 году. Brembo поставляет свою продукцию для многих автопроизводителей, включая Ferrari, Lamborghini, Porsche, Audi, BMW и Mercedes-Benz.
Другой крупный производитель углерод-керамических тормозов — компания Carbon Ceramics Ltd. Она занимается производством тормозов для автомобилей, а также для спортивных мотоциклов. Основной клиентской базой являются сборные команды, участвующие в гонках, включая MotoGP.
Компания Ceramic Brakes Company (CBC) была основана в 2003 году и является совместным предприятием между компанией Surface Transforms plc и Goodfellow Cambridge Limited. Она специализируется на производстве углерод-керамических тормозов для автомобилей высокого класса и спортивных мотоциклов.
Кроме того, есть и другие производители, такие как SGL Carbon, Hitco Carbon Composites, PFC Brakes и т.д. Каждая компания имеет свой уникальный подход к производству и настройке своих тормозов, что делает их продукты отличающимися друг от друга.
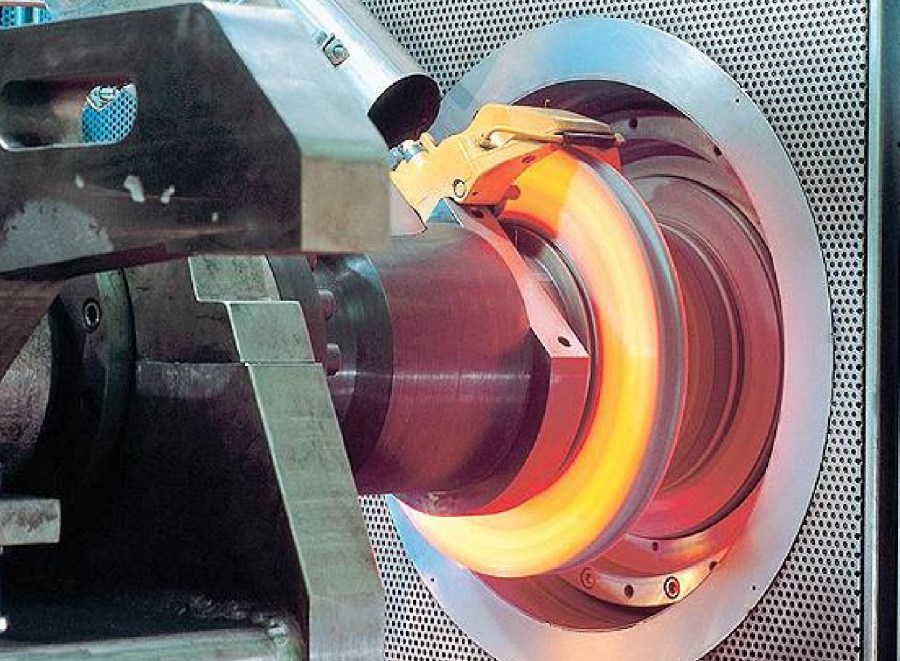
Процесс тестирования керамических тормозных дисков при температуре 900°С. Источник: www.autonews.com
Однако, важно учитывать, что композитные тормозные колодки не являются универсальным решением для всех автомобилей и ситуаций. В зависимости от условий эксплуатации и требований, традиционные металлические колодки могут быть более подходящим выбором.
Заключение
В настоящее время применение ССМ-тормозов сильно ограничено. Новатор в автотранспорте компания Tesla предлагает керамические тормоза на всех своих моделях как опцию. Цена установки такого комплекта начинается от 20 000 долларов США. Это сравнимо со стоимостью недорого автомобиля. Большинство люксовых брендов недоступно обычному покупателю, так как не только цена, но и последующее обслуживание таких автомобилей может стоить сотни тысяч долларов. А гоночные болиды являются уникальными, обычно собранными вручную произведениями искусства, где вопрос цены стоит на последнем месте.
Но несмотря на то, что CCM-тормоза имеют некоторые недостатки, такие как высокая стоимость и требование к более тщательному уходу, их преимущества неоспоримы. Большинство компаний-производителей продолжают исследования и разработки, чтобы улучшить технологию, удешевить и расширить ее применение.
С ростом интереса к экологически чистым и энергоэффективным автомобилям, в том числе и электромобилям, CCM-тормоза становятся все более востребованными, поскольку они уменьшают массу автомобиля и повышают его эффективность. Будущее CCM-технологий выглядит светлым, и они, безусловно, останутся важным элементом для различных отраслей, где важно обеспечить безопасность и надежность в экстремальных условиях.