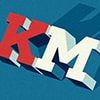
Использование перспективных ПКМ для создания авиационных конструкций
рубрика: применение
В последние годы область применения ПКМ, армированных стекло- и углеволокном для решения технических и индустриальных задач расширяется по мере получения положительных результатов длительной и успешной эксплуатации таких материалов.
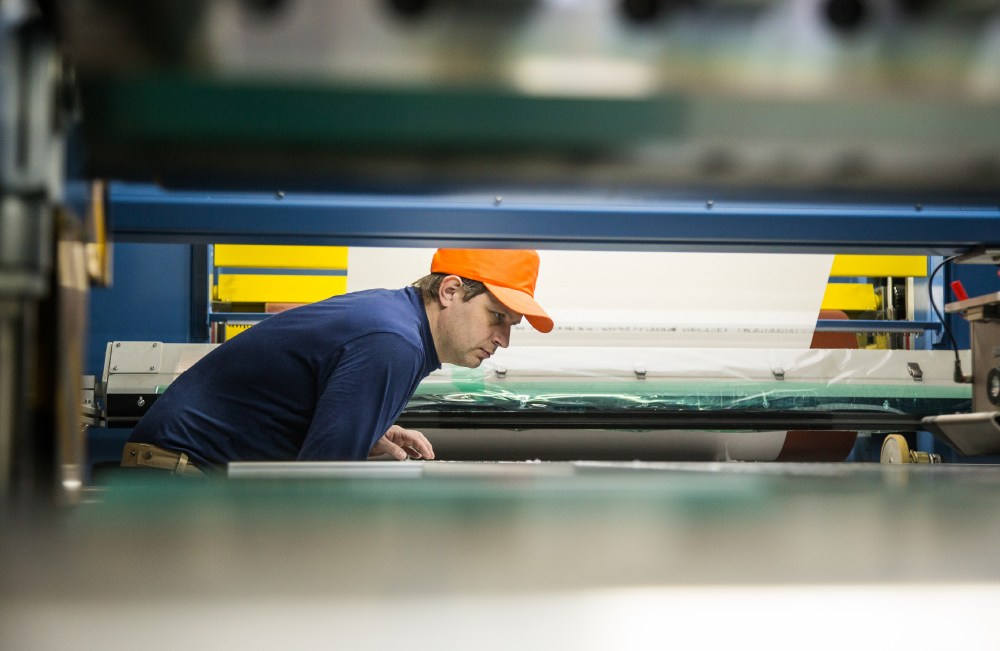
В последние годы область применения ПКМ, армированных стекло- и углеволокном для решения технических и индустриальных задач расширяется по мере получения положительных результатов длительной и успешной эксплуатации таких материалов.
Наиболее широко применяемый способ формирования конструкций из ПКМ с армированными волокнами предусматривает использование промежуточного листового материала — препрега, в котором армирующие ткани или волокна пропитаны неотвержденным термореактивным связующим. Осуществляется укладка необходимого количества слоев препрега (сборка пакета), а затем происходит нагрев при повышенном давлении (с использованием прямого прессования, вакуумного или автоклавного формования) с целью отверждения связующего и формирования изделия из ПКМ.
В настоящее время одной из мировых тенденций при разработке перспективных авиационных конструкций является замена традиционно используемых металлических сплавов на композиционные материалы. Это позволяет добиться значительного снижения веса изделий, улучшения их эксплуатационных характеристик и повышения длительности эксплуатации.
Одним из возможных решений этой важной технической задачи является применение современных композиционных материалов на основе углеродных наполнителей и модифицированных эпоксидных связующих [1]. Существующие традиционные конструкторские решения создания деталей из ПКМ и технологии, реализующие эти решения, имеют ряд недостатков. Так, зачастую детали из ПКМ создаются просто путём замены металлического материала на композиционный без изменения подходов к проектированию конструкций. Это тупиковый путь, так как интегральные конструкции и конструкции с использованием сотового заполнителя состоят из большого количества отдельных деталей, в последствии собираемых в окончательную конструкцию с помощью склеивания. Данный подход характерен высокой трудоёмкостью и большим количеством необходимой технологической оснастки, что удорожает конечную продукцию. Кроме того, большинство применяемых в настоящее время связующих для ПКМ требуют высокой температуры (170-180°С) полимеризации. Это приводит к увеличению энергозатрат, применению высокотемпературных вспомогательных технологических материалов и соответствующей оснастки.
Обычно создание новой детали происходит в следующей последовательности: проектирование конструкции, выбор материала, отработка технологии. Данная работа является попыткой создания новой детали, используя принцип неразрывности «материал — технология — конструкция», при применении которого все элементы такого «треугольника» оказывают взаимное влияние друг на друга и учитываются с начальных этапов проектирования. То есть при проектировании конструкции сразу же определяется, какая технология изготовления должна быть реализована в серийном производстве, подбирается материал, способный реализовать свои свойства в данной конструкции при использовании выбранной технологии и тому подобное.
В рамках работ в интересах российской авиационной отрасли специалистами ООО «НПП «Завод полимерно-композитных конструкций» (ООО «НПП «ЗПК») и АО «Препрег-СКМ» (UMATEX, Росатом) был реализован принцип «материал-технология-конструкция» при решении задач по замене металлических деталей самолётов на композиционные. Так, одному из авиационных КБ была поставлена задача по снижению веса изготавливаемой конструкции триммера руля направления перспективного самолёта. Существующий триммер представляет собой клёпаную алюминиевую конструкцию. Снижение веса (без ухудшения эксплуатационных характеристик триммера) предполагалось получить путем использования новых конструктивных решений и применения ПКМ на основе углеродного волокна.
Для решения данной задачи использован углепластик на основе отечественного препрега фирмы АО «Препрег-СКМ» марки АСМ102-С130UD: толщина монослоя 0,13 ±0,02; армирующий наполнитель: углеродная нить UMT 49S-12K-EP (АО «Алабуга-Волокно») [2]. Физико-механические характеристики ПКМ, полученные на основе препрега АСМ102-С130UD, представлены в таблице 1.
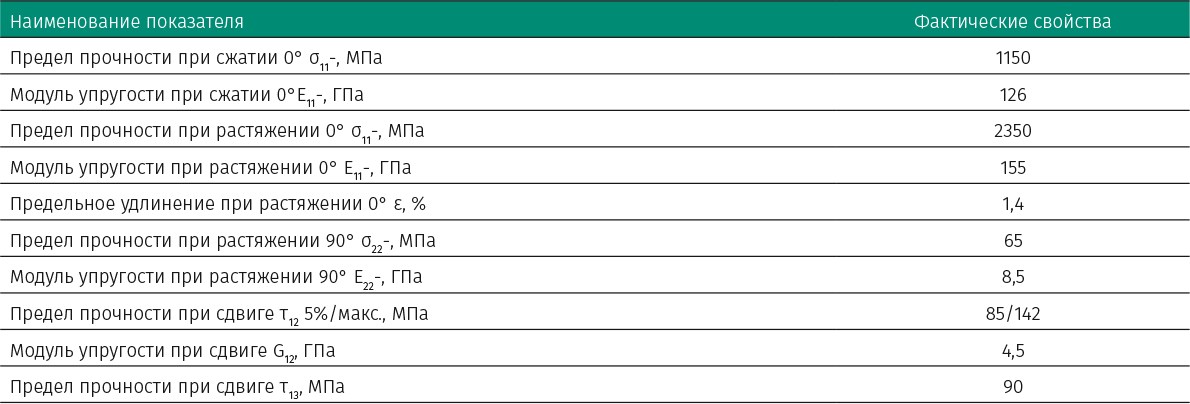
Таблица 1. Физико-механические характеристики образцов ПКМ, полученные на основе углепрепрега марки АСМ102-С130UD (автоклавная технология (давление 5 бар), исследования свойств при температуре 23 ±2°С)
Для получения препрега АСМ102-С130UD используется одноупаковочное безрастворное эпоксидное связующее марки АСМ102, которое способно формировать в процессе отверждения теплостойкую полимерную матрицу (Тg ≥ 150°С), характеризующуюся высокими физико-механическими характеристиками (прочностью при растяжении при температуре 25°С не менее 80 МПа, относительным удлинением при разрыве 3% и модулем упругости 3,4 ГПа). Связующее имеет оптимальные показатели вязкости, которые обеспечивают возможность удаления воздуха из сборки пакета, а при повышении температуры обеспечивает монолитизацию формируемого материала.
Использование в составе эпоксидного связующего марки АСМ102 комплексной отверждающей системы обеспечивает активное формообразование полимерной матрицы при температурах 130–150°С и способствует невысокой скорости взаимодействия функциональных групп при комнатной температуре. Что в итоге позволяет получить высокую степень сохранения технологических характеристик (вязкость и липкость) эпоксидного связующего и его повышенную жизнеспособность в препреге. Созданные препреги на основе безрастворного эпоксидного связующего марки АСМ102 и армирующих волокнистых наполнителей характеризуются длительным сроком хранения (до 45 суток) при температуре 23°С и не менее 12 месяцев при температуре −18°С, не содержат летучих компонентов, характеризуются хорошей драпируемостью и оптимальной липкостью при применении и могут быстро отверждаться без угрозы саморазогрева реакционной смеси. Препреги с такими характеристиками являются перспективными материалами для создания композиционных материалов конструкционного назначения с энергоэффективными режимами отверждения, в том числе возможностью формования по низкозатратным безавтоклавным ресурсосберегающим технологиям [3].
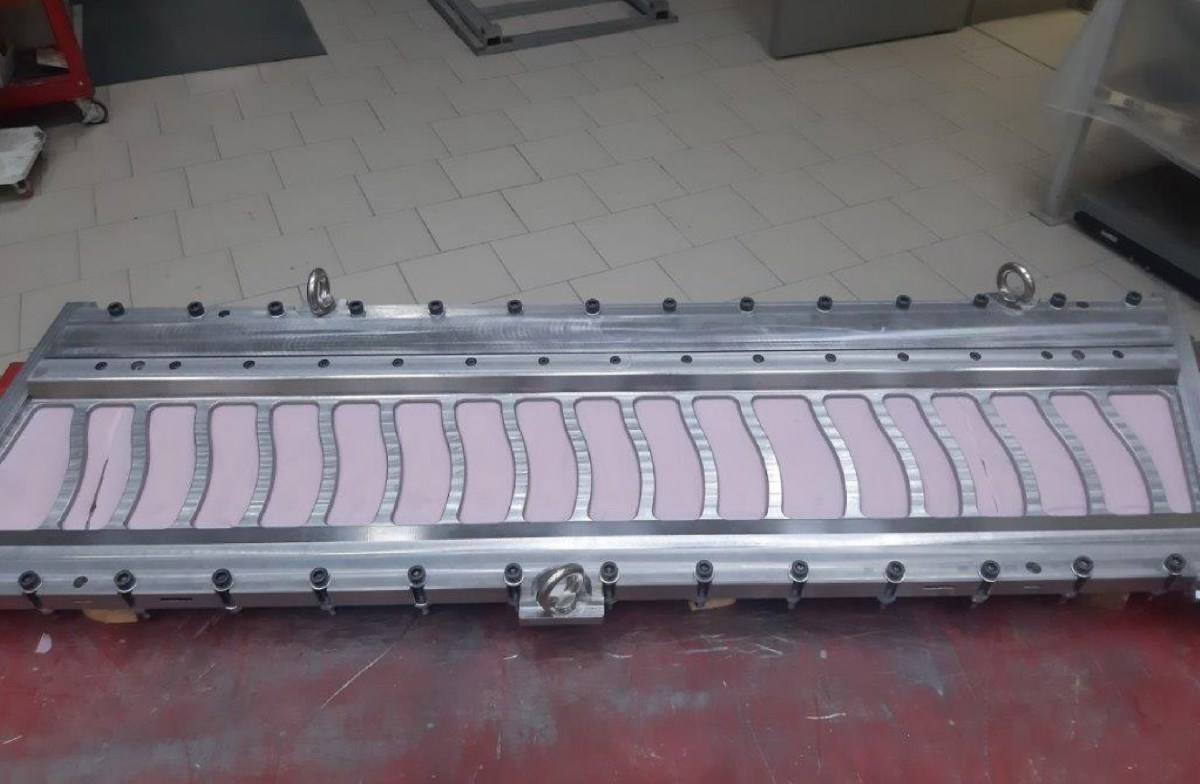
ООО «НПП «Завод полимерно-композитных конструкций» отрабатывались технологии получения двух разновидностей конструкций триммера руля направления из композиционных материалов по препреговой технологии. При разработке конструкции и технологии ставились задачи минимизировать количество отдельных деталей и технологических переходов.
В первом варианте формирования конструкции триммера (Вариант 1) из композитных материалов использована силовая схема, близкая к схеме монокока — в конструкции триммера нет стрингеров и нервюр. Оболочка триммера изготовлена из препрега, а весь объем триммера заполнен высокопрочным конструкционным пенопластом, который выполняет функцию силовых элементов. Воздушные нагрузки, приходящие на оболочку конструкции, сразу передаются на пенопласт, а с него — на лонжерон. При перетекании возникающей нагрузки на лонжерон образуются крутящие усилия, которые воспринимаются жестким треугольником «верхняя оболочка-лонжерон- нижняя оболочка». По этой причине оболочка конструкции работает только «на кручение». Конструкционный пенопласт препятствует деформациям оболочки и обеспечивает ее высокую несущую способность.
Второй вариант конструкции триммера руля направления (Вариант 2) выполнен практически по традиционной схеме. В схему второго варианта конструкции триммера входят: носок, лонжерон, обшивка и нервюры. В отличие от существующей конструкции, в предлагаемой конструкции триммера из композиционных материалов стрингеры отсутствуют.
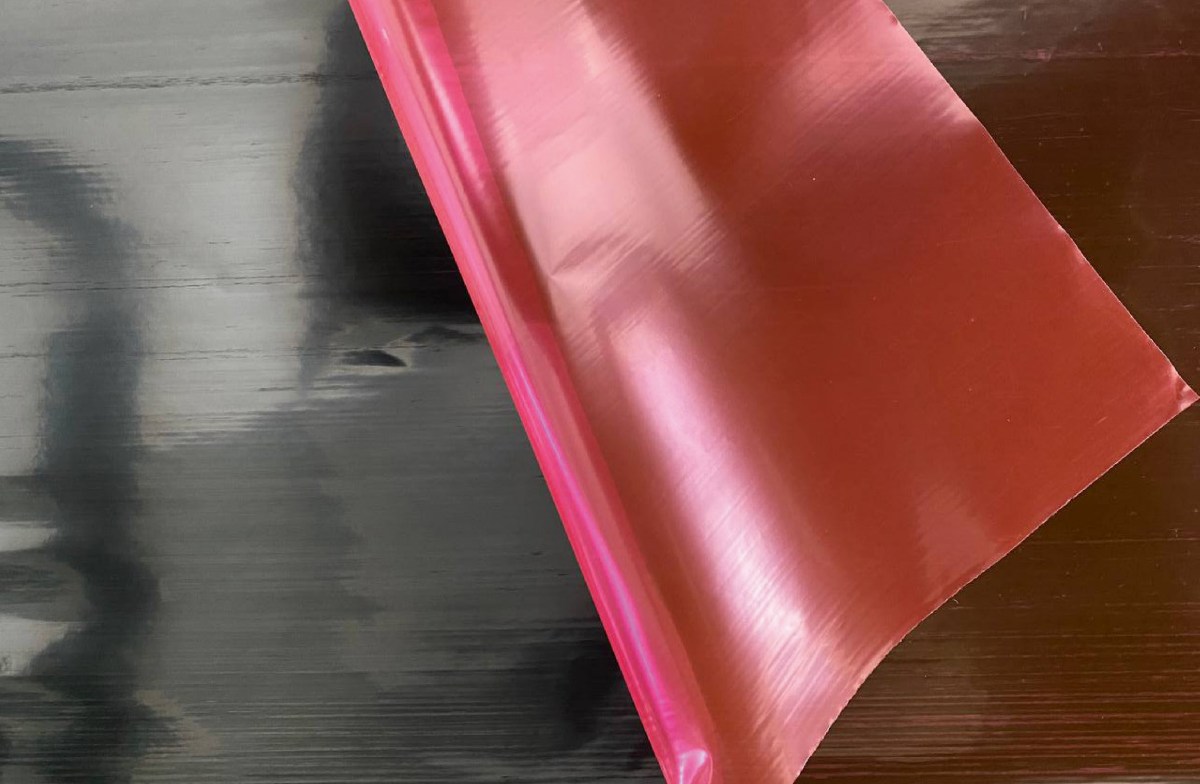
Носок триммера внешне представляет собой криволинейную поверхность, разрезанную узлами навески и приводом. В силу «разрезанности» носок практически не является силовым элементом, представляет собой часть аэродинамического контура.
При поиске наиболее рациональной силовой схемы за таковую принята схема полумонокока, где внешнее воздействие воспринимается как силовой оболочкой, так и силовым набором, в данном случае — нервюрами и лонжероном. Воздушная нагрузка воспринимается оболочкой, передает ее на лонжерон (через изгиб оболочки) и на нервюры. С лонжерона нагрузка уходит на узлы навески. Пришедшую с оболочки нагрузку нервюры также передают на лонжерон. Для увеличения запаса устойчивости нервюры имеют специально разработанную форму.
При перетекании нагрузки с оболочки на лонжерон формируются потоки крутящих усилий, воспринимаемые обшивкой и лонжероном, образующих замкнутый силовой треугольник.
Все воспринимаемые внешние нагрузки уходят на узлы навески. Кронштейны этих узлов закрепляются на лонжероне таким образом, чтобы болты крепления работали только на растяжение. Это позволило отказаться от использования прецизионных болтов.
В соответствии с принятой силовой схемой конструкции триммера и с учетом особенностей работы каждого силового элемента были назначены схемы укладки углепрепрега и количество слоев для обеспечения необходимой прочности и устойчивости.
Весовые характеристики существующего и двух разработанных вариантов конструкции триммера представлены в таблице 2.

Таблица 2. Характеристики различных конструкций триммера руля направления
Оба варианта конструкции триммера руля направления после изготовления подверглись статическим стендовым испытаниям у заказчика. В результате испытаний было установлено, что вариант 1 конструкции с пенопластовым заполнителем разрушился при нагрузке, составляющей 180% от заданной расчетной нагрузки. Вариант 2 разрушился при нагрузке, равной 471% от заданной расчетной нагрузки. Анализ структуры созданных изделий показал, что полученный высокий запас прочности не может быть незначительно уменьшен путем дальнейшего облегчения конструкции. Принятые толщины сформированного полимерного композиционного материала являются конструктивно минимальными, и даже удаление всего одного слоя из любого элемента переводит конструкцию в неработоспособное состояние.
По результатам испытаний установлено (таблица 2), что минимальным весом обладает конструкция триммера руля направления, изготовленная по варианту 2. Этот вариант оказался и самым прочным. Внешний вид триммера, изготовленного по варианту 2 представлен на рис. 1
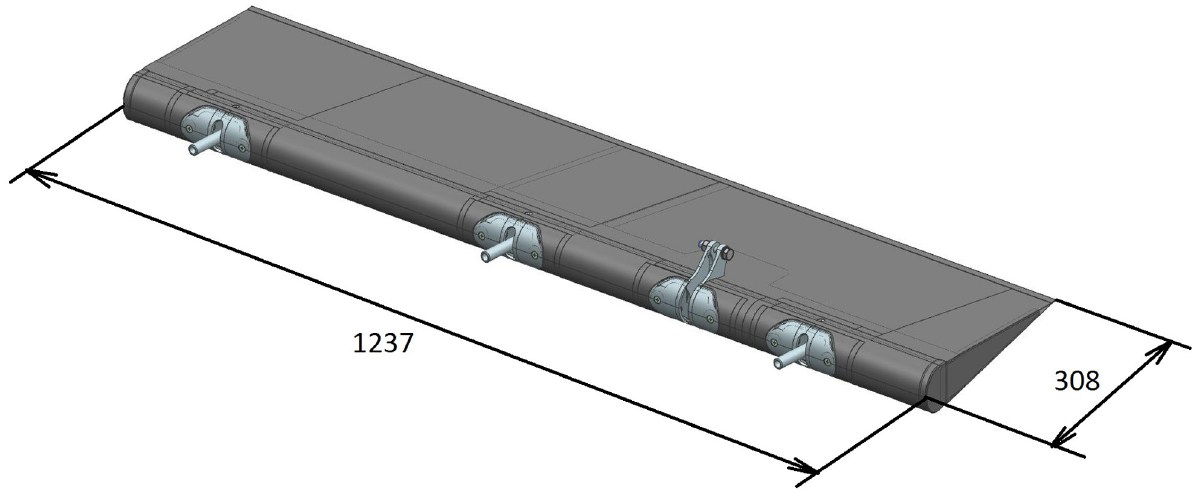
Рисунок 1. Конструкция триммера руля направления (Вариант 2)
Высокий запас прочности триммера руля направления, изготовленного по варианту 2 при минимальном весе, получен благодаря оригинальной конструкции изделия и применению углепластиков с высокими удельными прочностными характеристиками на основе отечественного препрега фирмы АО «Препрег-СКМ».
Применённый подход специалистов ООО «НПП «ЗПК» и АО «Препрег-СКМ» позволил минимизировать количество элементов детали, сократить количество технологических переходов до трех (без учёта крепежа), а количество оснастки до двух единиц. Также за счёт применения нового материала удалось при сохранении максимальной рабочей температуры до 80-120°С снизить температуру формования изделия с 170–180°С до 130–140°С, что в том числе привело к сокращению цикла изготовления детали более чем на 25%. Данный подход, по нашему мнению, является оригинальным и ранее не применялся при создании авиационных конструкций.
Также данная работа выявила потенциал для дальнейшего снижения массы авиационных конструкций. Для этого в ближайшее время АО «Препрег-СКМ» будут проводиться работы по созданию материалов со сниженной толщиной монослоя.
Список литературы
- Офицальный сайт компании «Innovative Composite Engineering», URL: www.innovativecomposite.com, дата обращения 11.01.2021 г.
- Брошюра по техническим характеристикам препрегов «Carbon fiber fabrics prepreg», UMATEX, Rosatom State Corporation, www.umatex.com, дата обращения 11.01.2021 г.
- Д. И. Коган, Л. В. Чурсова, Н. Н. Панина, Т. А. Гребенева, Е. И. Голиков, И. А. Шарова, Ю. А. Баторова. «Перспективный полимерный композиционный материал для конструкционных изделий с энергоэффективным режимом формования по ресурсосберегающим технологиям», Пластические массы, №3-4, 2020, с. 52-54.