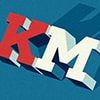
Суперъяхты из материалов Scott Bader
рубрика: применение
Практическое применение продуктов и решений компании Scott Bader при создании роскошных яхт высшего класса.
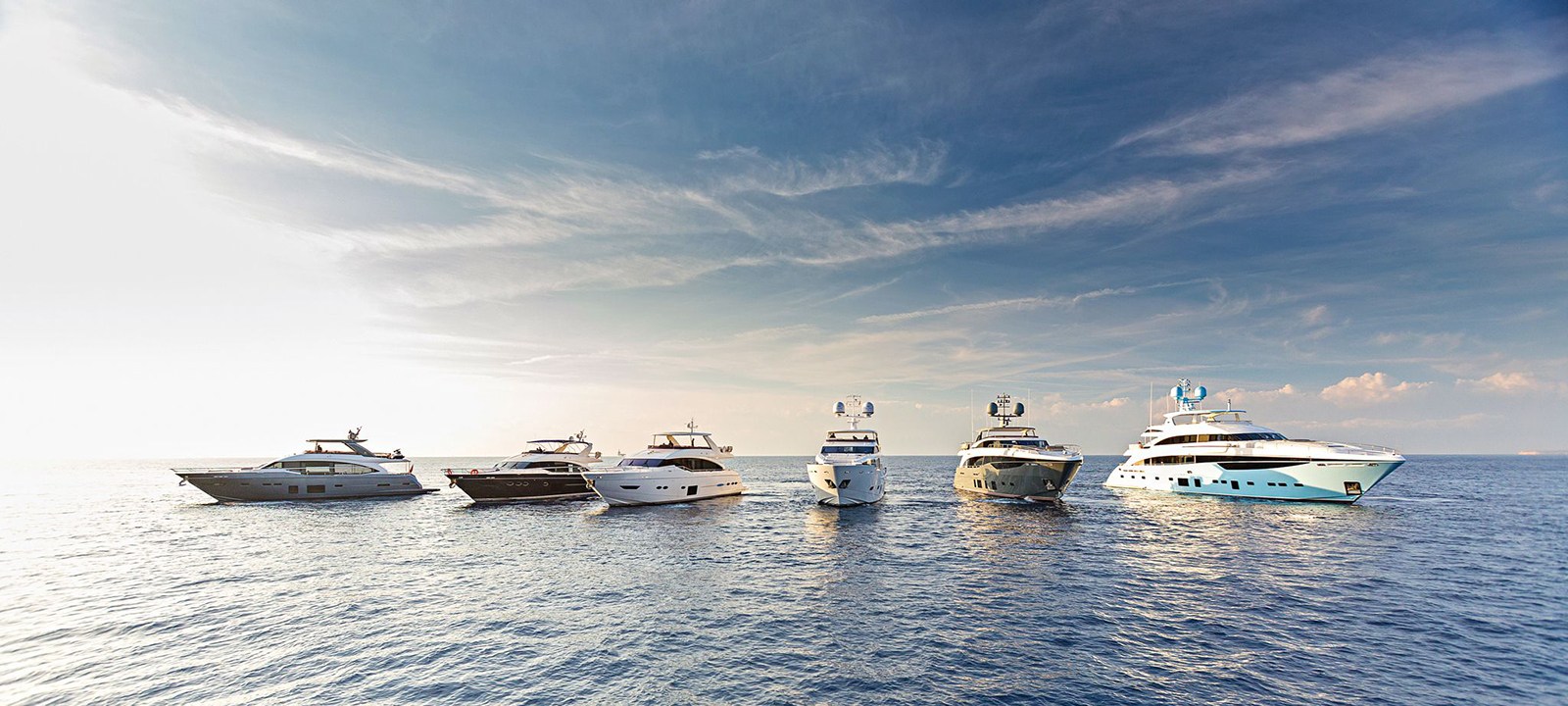
В ноябре 2020 года была построена яхта Majesty 122 от Gulf Craft с названием Happy Days. Это уже третья яхта, построенная с использованием продуктов Scott Bader, если считать c 2015 года.
В процессе строительства были использованы: винилэфирные смолы Crystic, гелькоуты, структурные адгезивы Crestomer и Crestabond, клеящие пасты Crestafix и система создания матриц Crestamould. Scott Bader и Gulf Craft сотрудничают с 2007 года.
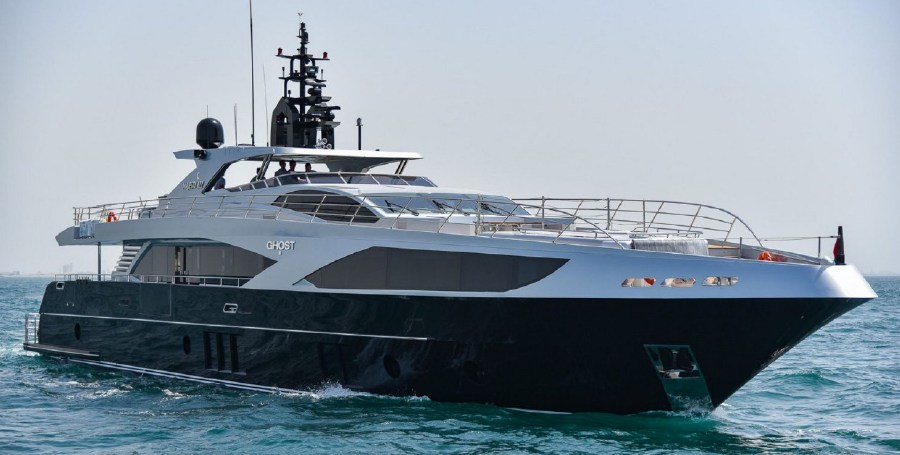
Majesty 122 — 37-метровая суперъяхта класса люкс. Яхты подобного рода используются для чартерных перевозок через Атлантический океан, поэтому материалы проходят строгий контроль перед производством.
Структурные адгезивы Crestabond позволили избавиться от винтовых креплений и надежно скрепить металлические элементы со стеклопластиковым ламинатом, значительно сократив время изготовления элементов внешней отделки.
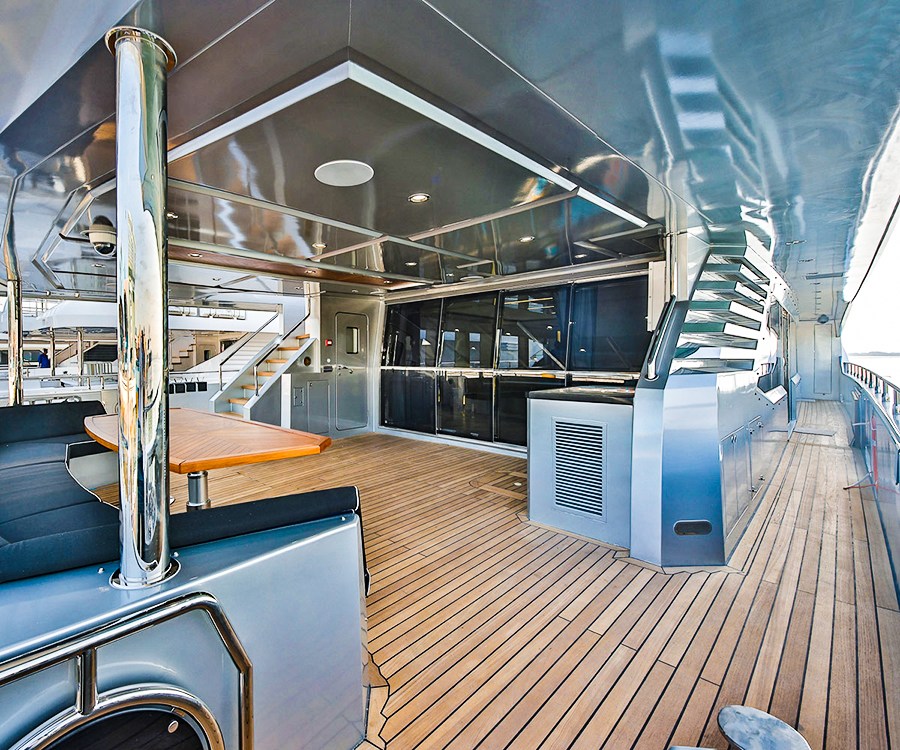
Стеклопластиковый корпус был изготовлен с использованием системы, состоящей из безусадочной смолы, матричного изофталевого неопентилгликолевого гелькоута и винилэфирной барьерной смолы. Для такого большого размера потребовалось более 150 кг окрашенного гелькоута. Колеровку такого количества гелькоута легко произвести с помощью автоматической системы Geltint всего за полтора часа.
Другой крупный производитель — Princess Yachts, с которым компания Scott Bader работает более 55 лет, недавно спустил на воду новую версию суперъяхты X95 длиной 29 метров. Ее отличительной особенностью является наличие флайбриджа и главная палуба почти во всю длину корпуса. Яхта, названная «морским внедорожником», способна развивать скорость в 23 узла при весе больше 100 тонн.
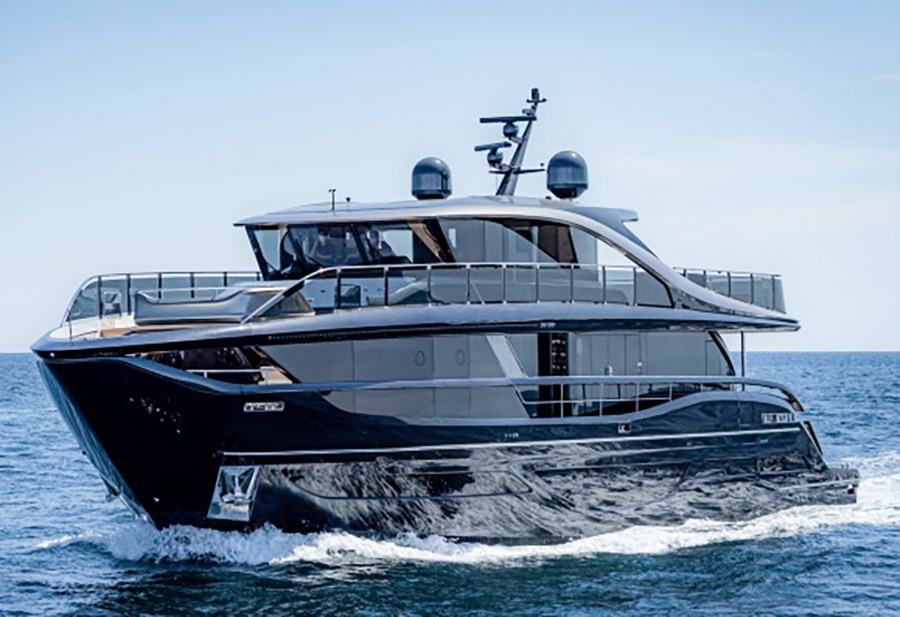
Для изготовления композитной оснастки и формы корпуса данного судна была использована матричная система Crestamould. Поверх отфрезерованной мастер-модели будущей яхты вначале напылялся шлифуемый полиэфирный грунт Primecoat, который потом полировался и покрывался глянцевым материалом Glosscoat. А уже сверху наносились слои для создания формы (матрицы) для вакуумной инфузии будущего изделия.
Первым этапом производства формы было равномерное нанесение на вышеописанные слои, покрывающие мастер-модель, воска. Затем наносился гелькоут. Потом — укладка барьерного слоя и напыление стеклоровинга с матричной полиэфирной смолой, а затем приформовывание ребер жесткости. Так как форма корпуса судна содержит углы, при которых вертикальный съем изделия невозможен, матрица являлась разборной.
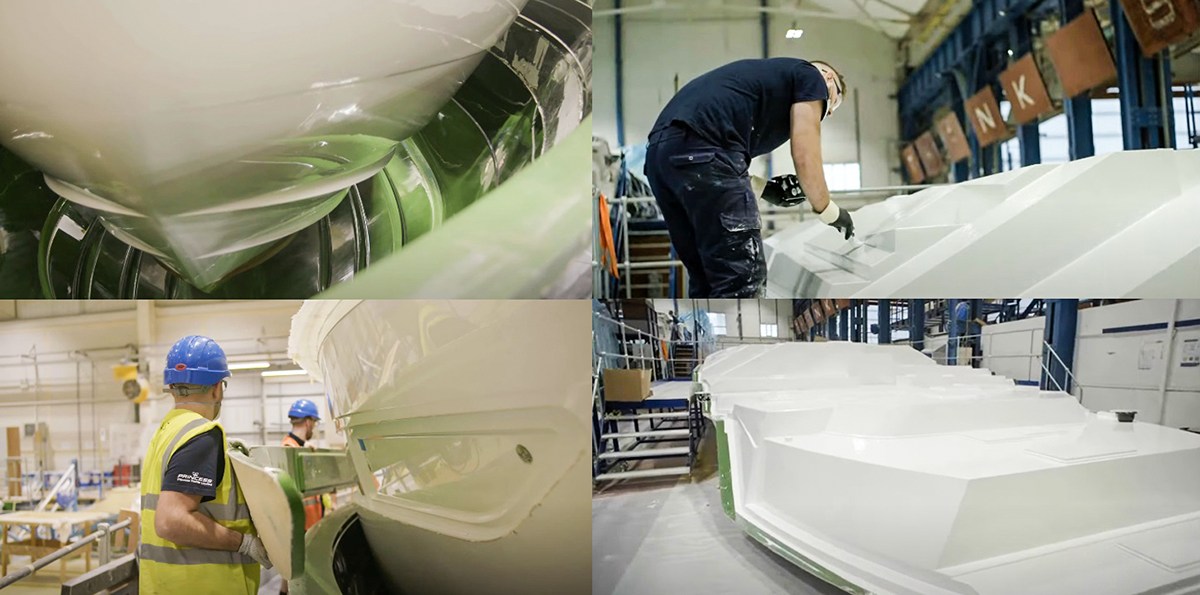
После отверждения матрицы (формы) и её съема с мастер-модели формовали непосредственно корпус яхты. Для этого после нанесения антиадгезионного слоя вначале наносили изофталевый стойкий к осмосу гелькоут.
Затем укладывали слои армируюущей, жервенной тканей и сформировывали вакуммуный пакет с полипропиленовыми трубками для распределения смолы. Благодаря использованию технологии вакуумной инфузии, удалось добиться высокой степени наполнения стеклопластика (65–70% в композите приходилось на армирующий материал), что положительно сказалось на прочностных характеристиках ламината.
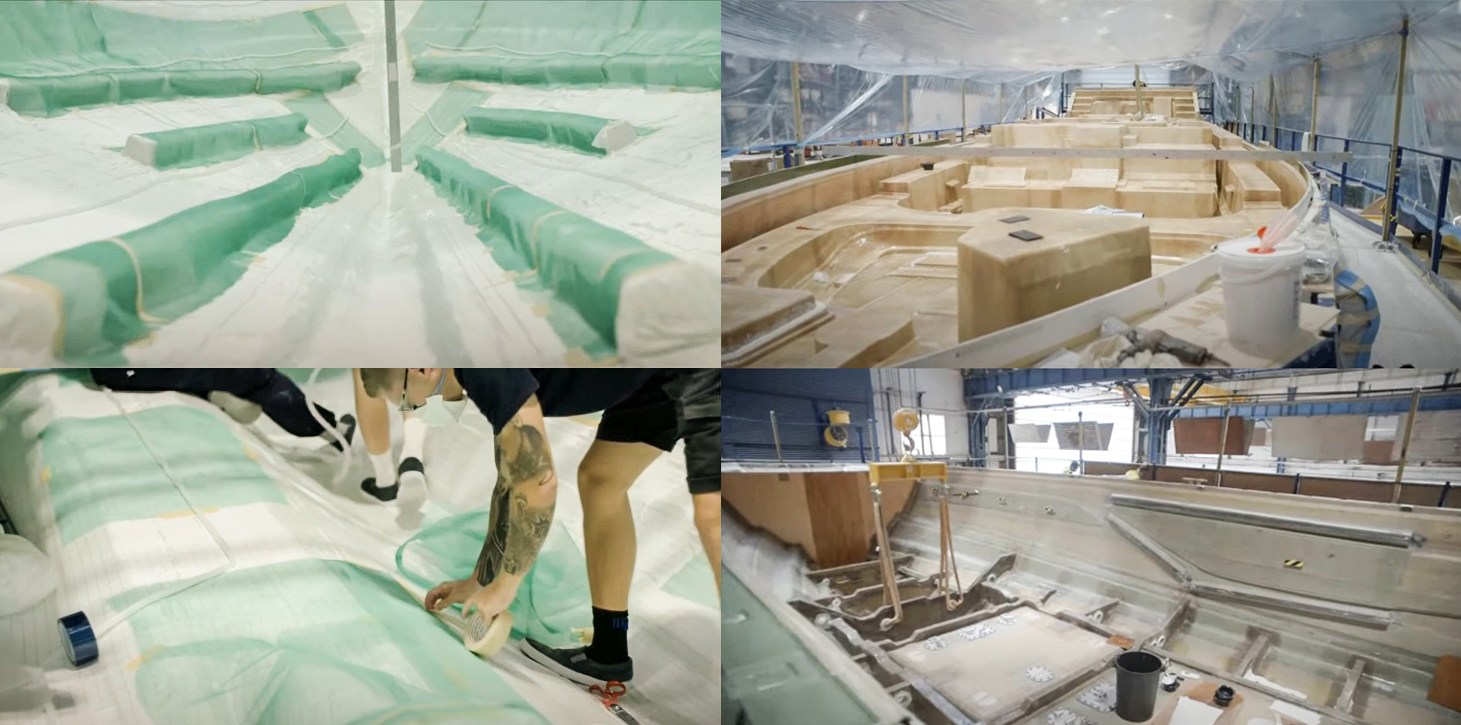
После отверждения основной части корпуса к нему для увеличения прочности конструкции с помощью адгезивов Crestafix приформовывались рёбра жесткости. Расформовку (съем изделия) производили с помощью подъемных кранов, которые извлекали готовый стеклопластиковый корпус яхты из формы. После чего уже производили сборку и установку всего необходимого оборудования и деталей.
Все перечисленные в статье материалы для формования изделий из композитов доступны и российским производителям. Заказать необходимые материалы, а также получить консультацию вы можете на сайте igc-market.ru