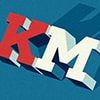
«Композитный» звук
рубрика: применение
На заре появления стеклопластиков (1960-е) применений для них уже было придумано немало. Автомобили, катера, самолёты, корпуса бытовой техники — список можно продолжать очень долго. Во многих нишах и по сей день успешно применяют и внедряют композитные технологии, разрабатывают новые, совершенствуют старые... Одной из таких областей, существующей на данный момент, стало гитаростроение.
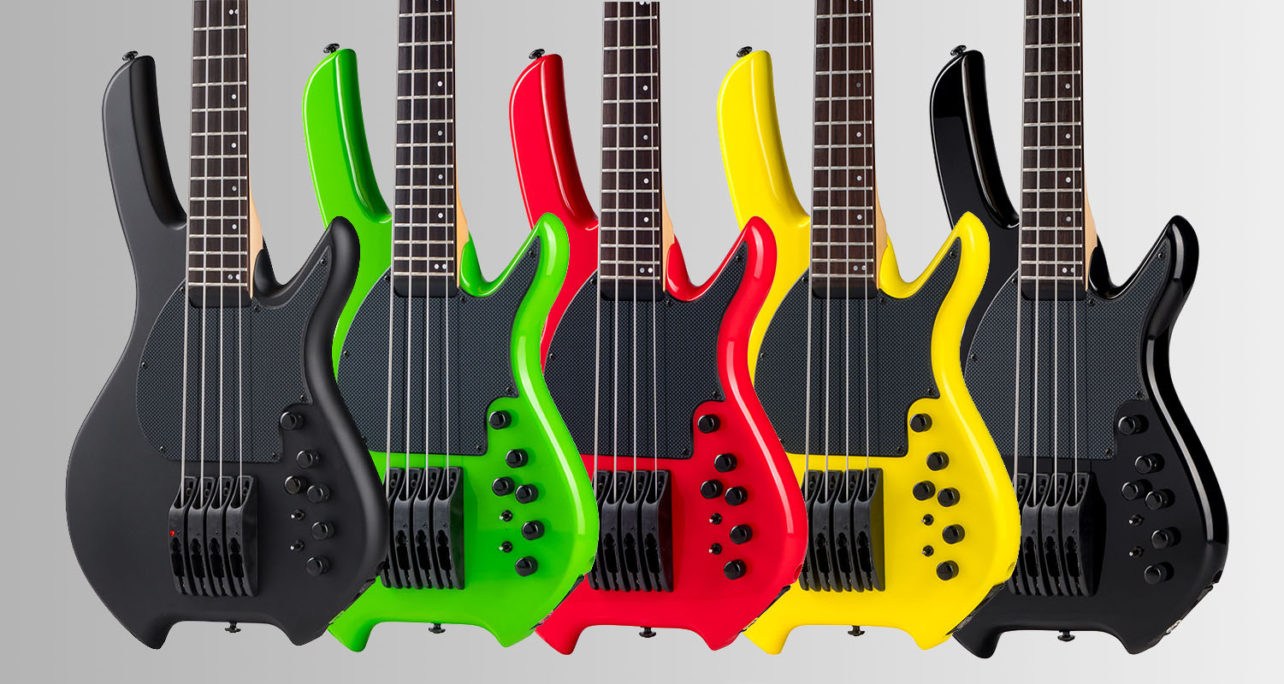
источник www.willcoxguitars.com
Немного истории
В то время как американские подростки, которые любили гитары, болтались и слушали the Ventures, не имея возможности купить дорогие инструменты от Fender и Gibson, чей-то отец строил лодку из стеклопластика. Он выкладывал стеклоткань в форму и тщательно пропитывал её смолой, чтобы после отверждения получить корпус из материала, так непохожего по своим свойствам на привычное всем дерево. А в Чикаго люди из компании Valco собирались сделать то же самое, но только с гитарами.
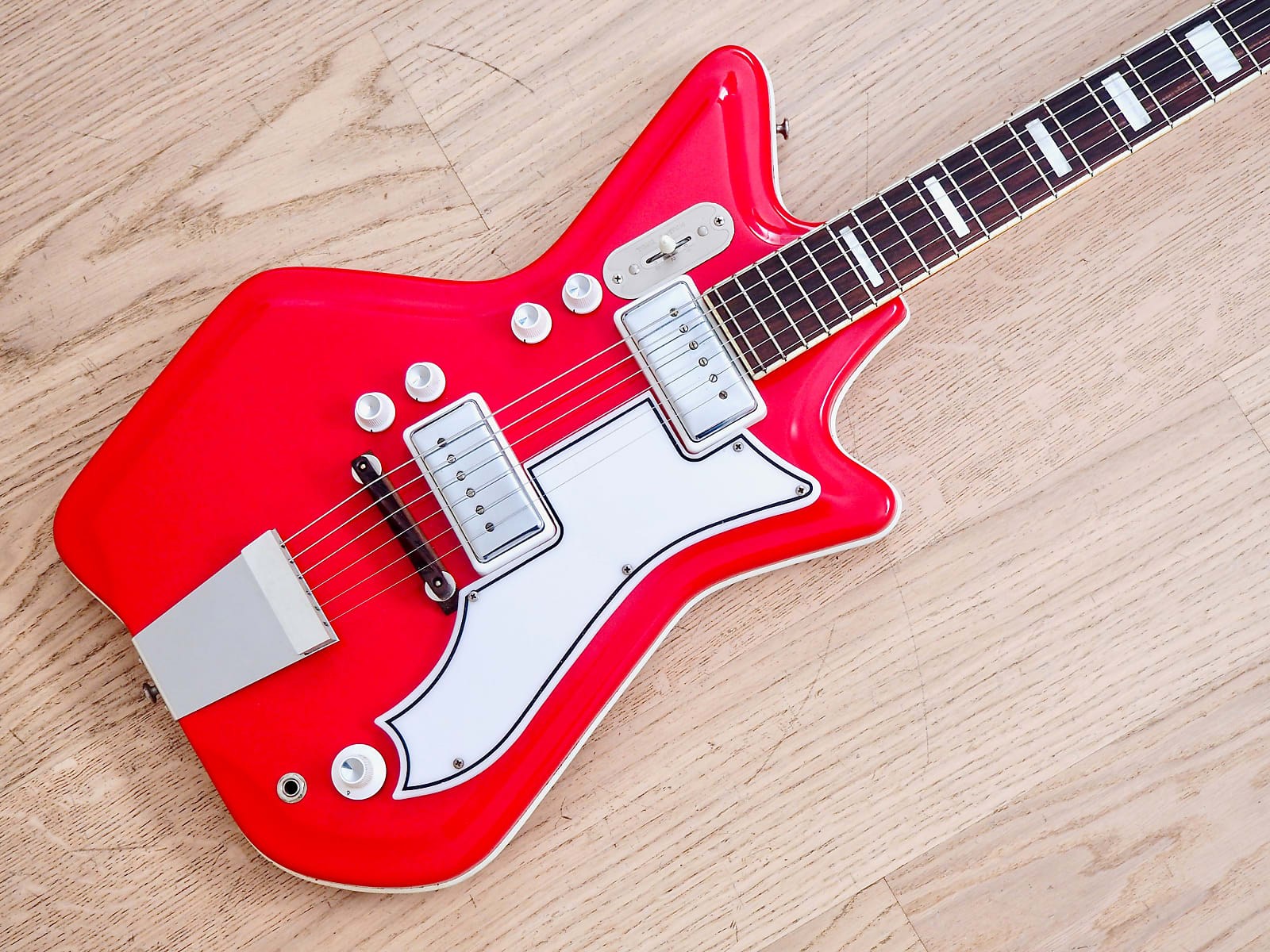
Реплика модели 1965 Airline JB by Valco с корпусом из стеклопластика (фото: gbase)
Идея производить гитарные корпуса из стеклопластика принадлежала Valco, и это решение принесло миру одни из самых ярких и интересных американских электрогитар 60-х годов. Из-за особенностей производства смола для стекловолокна может быть окрашена перед нанесением, что устраняет необходимость раскрашивания и лакирования готового инструмента. Valco назвала свой материал Res-O-Glas, давший название инструментам, чьи корпуса были изготовлены из стеклопластика, и разработала целую серию фирменных цветов. Казалось, что корпус такой гитары был цельным, но на самом деле он был собран из двух частей. При этом гриф по — прежнему изготавливался из дерева.
Все модели Res-O-Glas были очень необычными в плане дизайна и cвежих решений. Valco также перевыпустила в новом материале «дедушку всей кантри музыки» — резонаторную акустическую гитару модели Folk Star, которую в каталоге компании описывали как «самую мощную неэлектрическую гитару в мире».
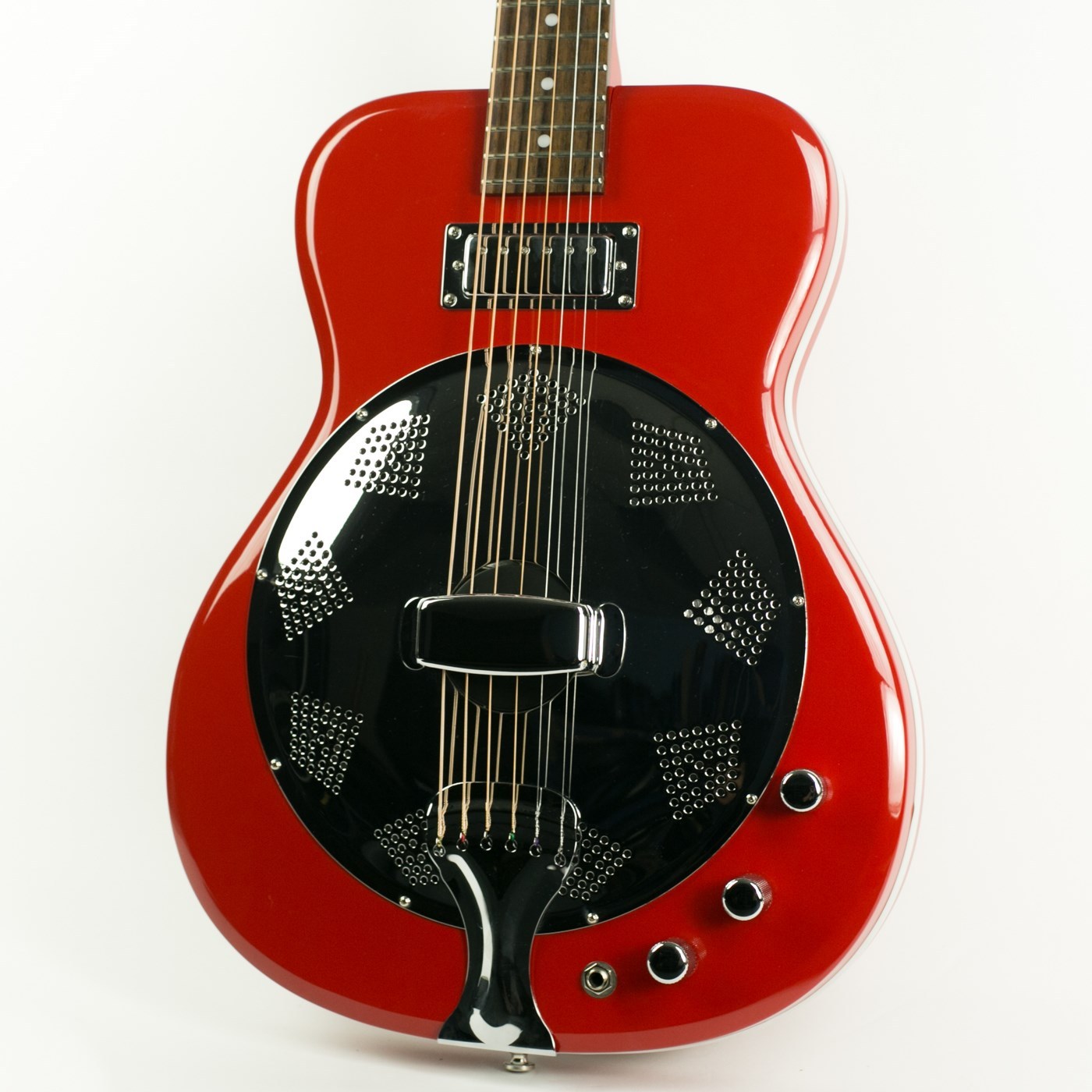
Переиздание модели Folk Star с корпусом из Res-O-Glas (фото: gbase)
Конечно, маркетологи компании лукавили, стеклопластик был прост в изготовлении и дёшев, но не мог похвастаться звучанием, которым обладали деревянные акустические и электрогитары. Основная проблема заключалась в отсутствии сустейна (длительности звучания). Звук инструментов из Res-O-Glas очень быстро затухал. На данный момент неизвестно — были ли это ошибки инженерного характера, или недостаточная изученность самого материала и смол, но факт остаётся фактом — в 1967 году компания Valco прекратила своё существование, а все гитары из Res-O-Glas стали историей.
Правда некоторые музыканты и сейчас используют гитары из стеклопластика.
«Я играю на по-настоящему старых гитарах, пластиковых», — говорит Джек Уайт, лидер группы White Stripes в документальном фильме «It Might Get Loud», имея в виду свою красную гитару странной формы с названием Airline (бренд, который владел Valco), — «на таких инструментах тяжело играть, но если вы хотите, чтобы было легко — купите новенький Les Paul или Stratocaster (популярные модели электрогитар из классических материалов), а я люблю трудности».
На видео можно в живую послушать тот самый «пластмассовый» звук знаменитой Airline
Возможно, на этой ноте и кончилась бы история композитных музыкальных инструментов, но современные возможности производств, технологии и материалы, вдохнули вторую жизнь в изобретение «мечтателей» 60-х годов.
Палка о двух концах
Если отбросить акустическую составляющую композитных материалов, то по сравнению с деревом у них есть одно неоспоримое преимущество — невосприимчивость к перепадам температур и влажности. Корпуса акустических гитар чаще всего делают из ели или кедра. Эти материалы обладают ярким, звонким и чётким звуком. Но при этом они мягкие и зависят от окружающей среды. Даже при кратковременном пребывании в условиях повышенной влажности или от резких перепадов температур гитара будет терять свои первоначальные свойства, требовать постоянной подстройки или просто приходить в негодность. Для студийных инструментов или тех, что никогда не покидают определённые климатические условия, это некритично, но как быть с дорожными и концертными гитарами? Чарльз Каман, основатель компании Ovation, был инженером и использовал композитные материалы для производства деталей вертолётов, а также был гитаристом-любителем. Именно он впервые изготовил цельный корпус вместе с грифом для акустической гитары. Он применял метод вакуумной инфузии, а потом накрывал полый корпус крышкой из того же материала. Эту гитару можно было ронять, конечно, в разумных пределах, опускать в воду. Её звучание пусть и не было таким тёплым, как у дерева, но зато не менялось ни при каких условиях.
Ещё одна компания — Composite Acoustics — является детищем аэрокосмических инженеров и поклонников гитар с большим опытом работы с композитами. Благодаря внедрению современных технологий, таких как обработка с ЧПУ, дизайн САПР, лазерные режущие устройства и система окраски азотом, компания гарантирует инструменты, которые так же совершенны и выверены до миллиметра, как и красивы.
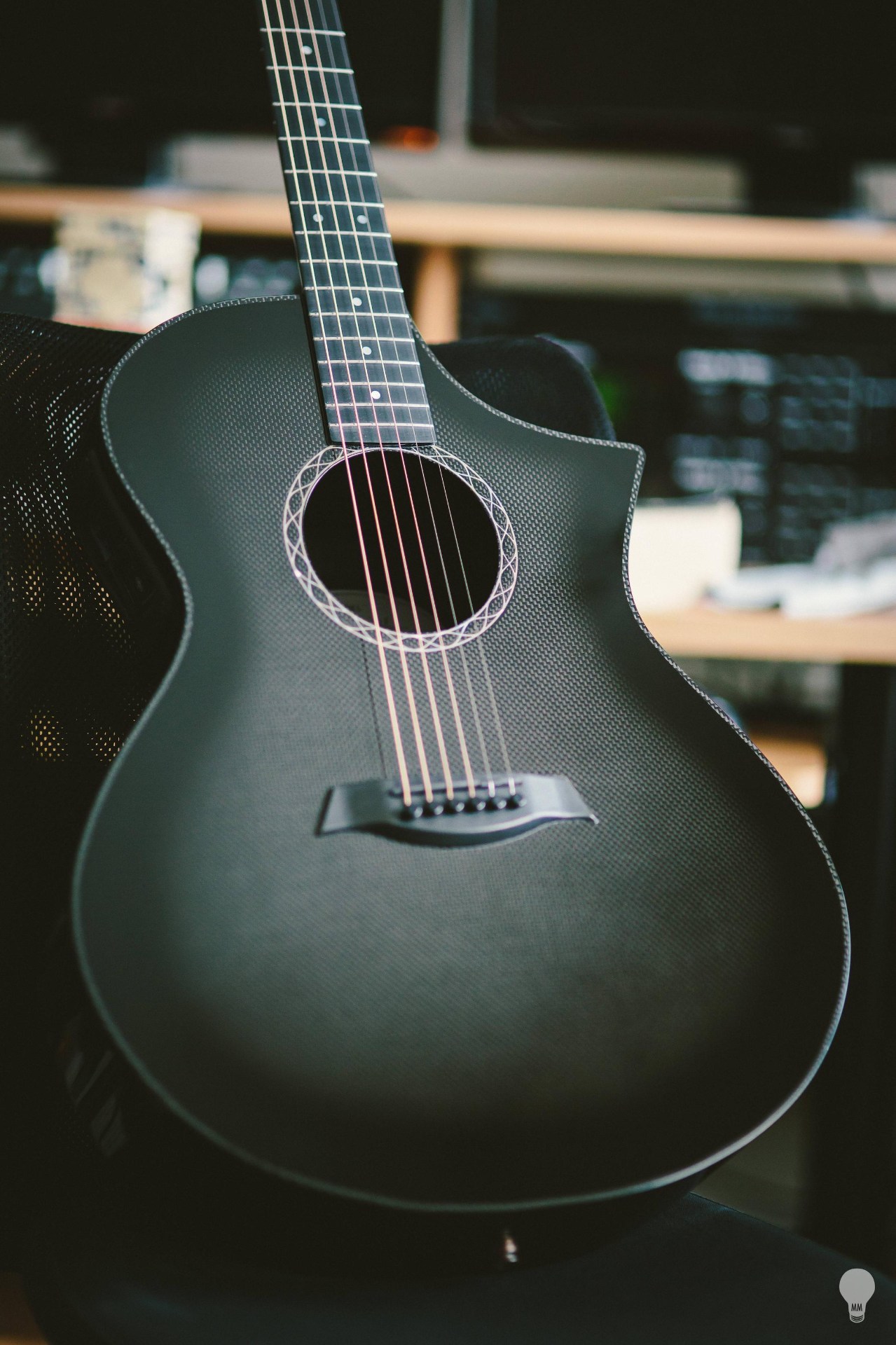
Инструмент производства компании compositeacoustics
Компания Blackbird специализируется на дорожных гитарах и укулеле. К дорожным инструментам предъявляются повышенные требования к прочности, поэтому композитные материалы, в данном случае, лучшее решение.
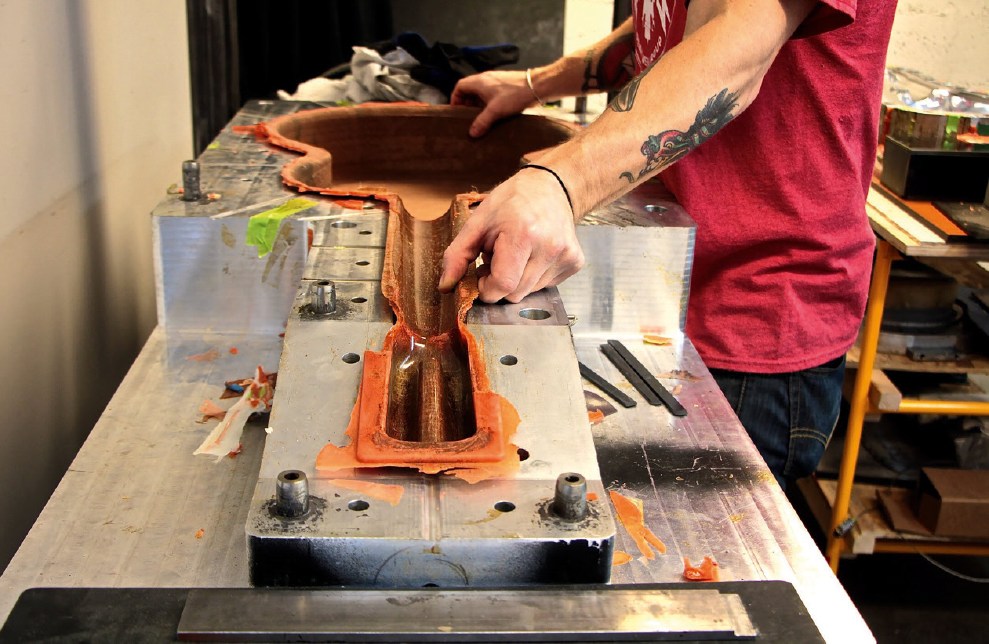
Процесс изготовления цельного композитного корпуса гитары фирмы Blackbird
Все эти гитары выглядят поистине фантастически. Но они и фантастически дороги. Самая бюджетная гитара Adamas или Ovation обойдётся в 150–200 тысяч рублей, при розничной цене недорогих акустических гитар из дерева — 8–15 тысяч рублей. Для обычного любителя — это очень дорого.
Немного другая ситуация с электрогитарами. Их корпуса в основном цельные (за исключением электроакустических инструментов) и, как следствие, производить электрогитару целиком из дорогого карбона очень накладно. Но производители всё же нашли способ применить композитные материалы. Немаловажной частью любой гитары является гриф. Именно от него зависит комфортность игры на инструменте. В случае с деревянным грифом влажность и перепады температур (это относится и к некоторым моделям акустических гитар) видоизменяют его форму, в которую при создании изначально заложен небольшой прогиб. Для исправления излишней кривизны или наоборот — увеличения прогиба, внутри грифа имеется специальный стержень — анкер. Затягивая или ослабляя гайку на его конце можно регулировать его кривизну. Этот процесс сложен и обычно доверяется профессиональным гитарным мастерам, так как неумелое вмешательство может испортить инструмент. Существуют, конечно, гитары (в основном бас-гитары) со сквозным креплением грифа, то есть не на болтах, как отдельная часть, а как часть корпуса, вклеенная прямо в него. Производители таких инструментов уверяют, что их грифы не меняют форму, но это не совсем так. Как уже упоминалось выше, температуры и влажность, сколы лака видоизменяют структуру дерева, и гриф может даже скручиваться вдоль своей оси, делая инструмент непригодным к использованию.
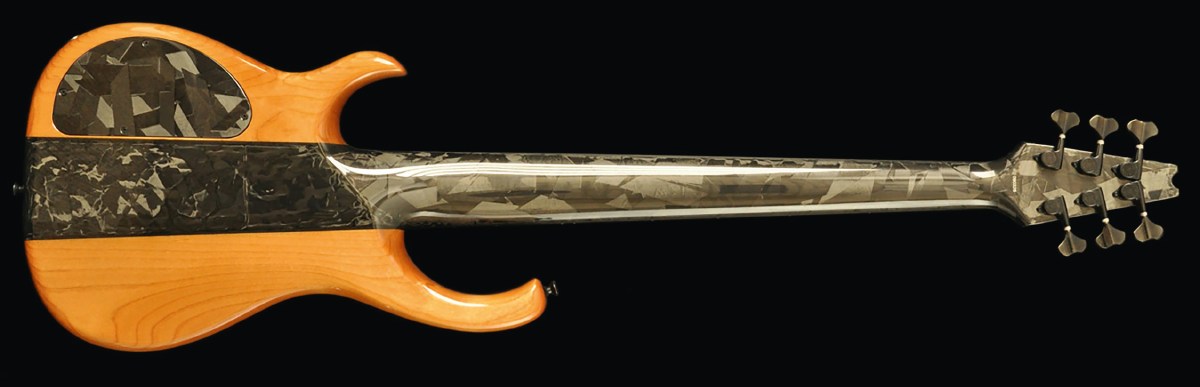
Шестиструнная бас-гитара Modulus Graphite с вклеенным грифом из углеродного волокна гарантирует неизменность формы грифа
Компания Modulus Graphite производит карбоновые грифы для своих бас-гитар. Помимо эстетической составляющей, они несут важную функцию — неизменную геометрию грифа. Его никогда не придётся подстраивать, он всегда останется в том идеальном положении, которое было до мелочей рассчитано инженерами компании. Доказательством служит то обилие известных музыкантов (в том числе и из России), использующих продукцию данной компании. Но, как и с остальной продукцией из композитных материалов, цена не выдерживает никакой критики.
Компания Moses Carbon выпускает отдельно карбоновые грифы для популярных моделей электрогитар и бас-гитар, удешевляя тем самым конечную стоимость инструмента. Так как звук электрогитар в основном зависит от корпуса, а не грифа, то его замена на композитный не внесёт существенной разницы в привычный звук. Но при этом сделает игру намного комфортнее, так как не придётся подстраиваться под постоянные изменения прогиба.
Компания Rall Guitars&Tools пошла по ещё более простому пути, она предлагает производителям гитар встраивать в свои грифы углекомпозитный стержень, обещая неизменяемую геометрию грифа.
Ну и конечно многие производители применяют карбон для отделки своих инструментов. Фактура углекомпозита ещё долго будет выглядеть стильно и футуристично, превращая привычные формы классических инструментов в нечто из научной фантастики.
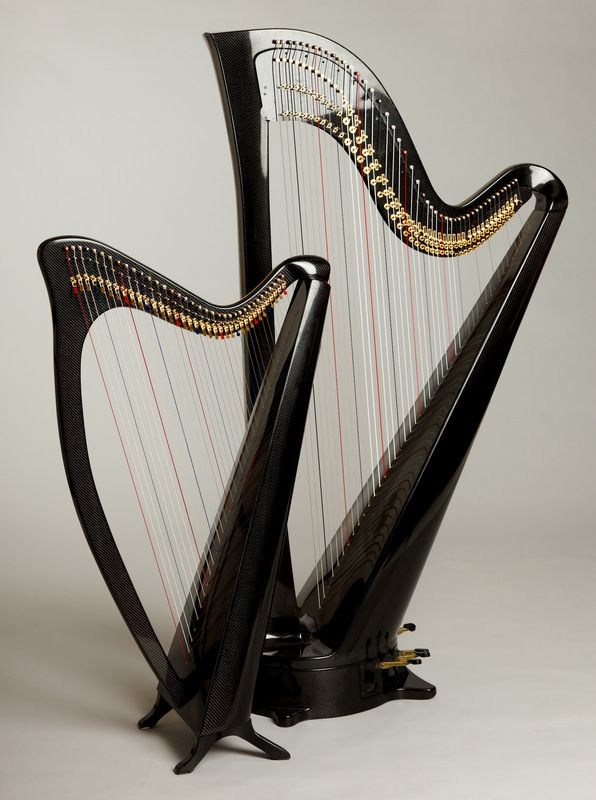
Арфа производства компании Starlight Harps
Стоит отметить, что не только производители гитар используют композитные материалы при производстве. Компания Mezzo-forte предлагает карбоновые скрипки и виолончели, обещая неизменяемую геометрию и звучание в любых погодных условиях. Компания Ricci Carbon Instruments производит карбоновые контрабасы. Компания Starlight Harps — арфы с корпусом из углеволокна, которые должны облегчить жизнь арфистам, чаще всего — женщинам, так как классические арфы из дерева — неимоверно тяжелы. Корпуса синтезаторов, других клавишных, кейсы и кофры, область применения композитных материалов в индустрии производства музыкальных инструментов и аксессуаров — достаточно обширна.
Заключение
Большинство музыкантов достаточно консервативные люди, и чаще всего выбор при покупке инструмента падает на модели из классических материалов. Очень ценятся инструменты 20–30 летней давности — считается, что звук таких гитар раскрылся в полной мере. Конечно, при условии соблюдения определённых правил хранения. Производители всё же не желают отставать от прогресса. Многие, помимо непосредственно самих композитных материалов, внедряют в технологический процесс современные технологии обработки, раскройки, прессования, формования, удешевляя и оптимизируя производство. Но почти все преимущества на данный момент разбиваются о высокую цену, а именно цена определяет выбор инструмента для 80% начинающих музыкантов. Из этого следует, что рынок композитных гитар и других инструментов направлен, в первую очередь, на нишу «элитных» инструментов, позволить себе которые может относительно небольшой процент музыкантов. Будем надеяться, что в будущем эти технологии станут доступнее, и каждый желающий сможет на собственном опыте и слухе изучить преимущества современных композитных материалов перед традиционными.
Статья была опубликована в номере 6 (75) 2017.