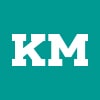
Композитные шпалы. Последние разработки. Трудности. Перспективы на будущее
рубрика: применение
В начале лета 2019 года композитный мир России облетела новость, что на Бутовской линии московского метро вместо деревянных шпал начали укладывать композитные. Ремонтные работы проходят на открытом участке Бутовской линии между станциями «Улица Скобелевская» и «Улица Горчакова», сообщает портал мэра и правительства Москвы. Сейчас здесь уложили более 600 новых композитных шпал. Шпалы из переработанного пластика служат более полувека, они устойчивее к повреждениям и не проводят электрический ток. Композитные шпалы позволяют снизить уровень шума и уменьшить вибрации при движении поезда, что помогает защитить железнодорожные пути от влияния вибрации и сократить объем ремонта.
«Большая часть Бутовской линии проходит не под землей, а на поверхности. Из-за этого ее пути требуют больше внимания, так как подвержены влиянию осадков и перепадов температуры. Шпалы, изготовленные по новой технологии, повысят безопасность движения и надежность инфраструктуры этой ветки. Всего здесь уложат более 11 тысяч композитных шпал до 2021 года. Таким образом, они заменят деревянные шпалы на всей протяженности пути Бутовской линии», — сказал глава департамента транспорта и развития дорожно-транспортной инфраструктуры Москвы Максим Ликсутов.
Источник: www.m24.ru
Введение
Железнодорожные шпалы выполняют важнейшую функцию. Шпалы обеспечивают неизменность расположения рельсовых нитей, передают давление от подвижного состава на балласт и земляное полотно.
В настоящее время на железных дорогах в России применяются несколько типов шпал:
- деревянные, которые в основном производятся из сосны, лиственницы, кедра, березы;
- железобетонные, которые состоят из натянутых струн арматуры, залитых бетоном;
- металлические, применяющиеся редко (из-за большой металлоемкости, подверженности коррозии и большому шуму при движении поездов);
- и, наконец, полимерные (композитные), которые успешно прошли испытания, но пока не нашли широко применения.
Самыми используемыми шпалами являются деревянные и железобетонные. Рассмотрим преимущества и недостатки данных шпал.
Преимуществами деревянных шпал являются:
- легкость обработки при изготовлении;
- быстрая окупаемость;
- масса шпалы (около 80 кг, это в три раза меньше, чем железобетонная шпала);
- срок службы (от 5 до 15 лет, при условии качественной обработки);
- возможность увеличения или уменьшения колеи железнодорожного пути;
- устойчивость к перепадам температур;
- диэлектрические свойства древесины;
- устойчивость сцепления с подложкой и упругость.
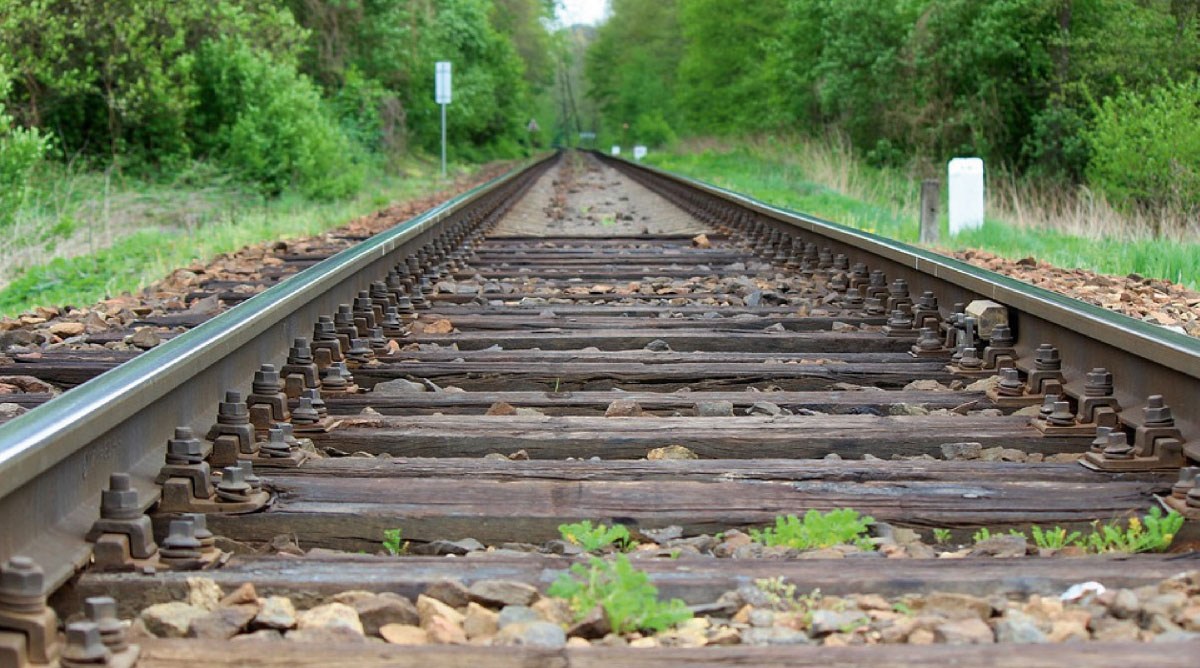
При неправильной обработке шпалы из дерева подвергаются гниению, соответственно, срок эксплуатации уменьшается
Самым главным недостатком деревянной шпалы является то, что при неправильной обработке шпалы подвергаются гниению, соответственно, и срок эксплуатации уменьшается. Также деревянные шпалы, пропитанные ядовитым креозотом, несут серьёзную угрозу экологии. Они загрязняют почву, водоемы, попадая туда с дождевой водой, а также оказывают пагубное влияние на здоровье человека. Еще одним недостатком деревянных шпал является неоднородность из размеров, что влечет за собой неоднородность упругости.
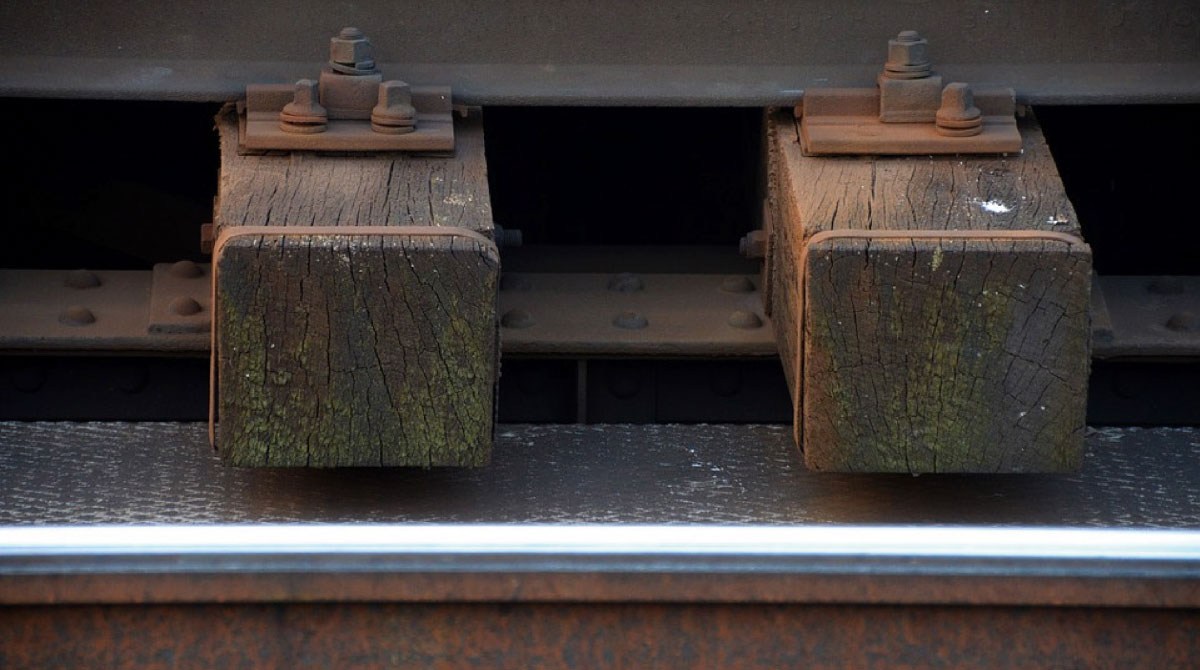
На деревянные шпалы окружающая среда оказывает большее воздействие,
чем на бетонные или композитные
Преимуществами железобетонных шпал являются:
- морозостойкость;
- продолжительный срок эксплуатации (от 40 до 50 лет);
- не поддаются коррозии;
- устойчивость рельсовой колеи и однородность пути.
Недостатками же этих шпал являются:
- повышенная электропроводность;
- хрупкость, чувствительность к ударам;
- высокая жесткость пути, что приводит к более быстрому износу рельс в местах стыков;
- значительная масса шпалы (в среднем 270 кг/шт.);
- сложность монтажа;
- высокая стоимость.
Бетонные шпалы не несут угрозы для экологии, но из-за отсутствия их вторичной переработки и должной утилизации возникают огромные свалки.
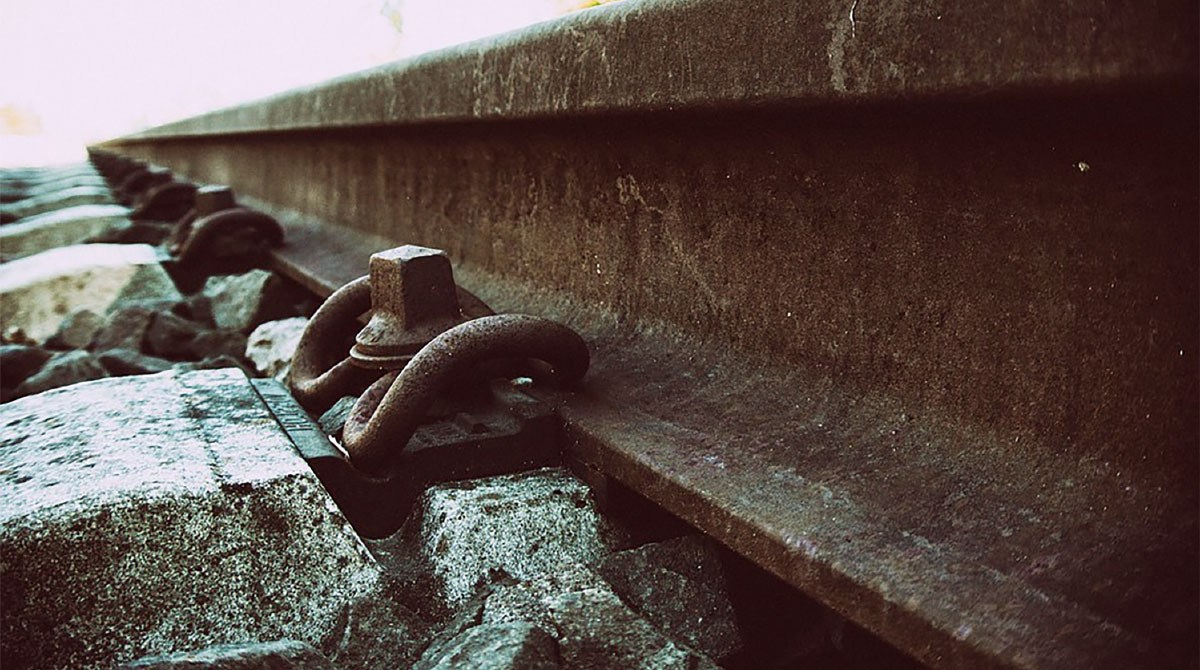
Работу с бетонными шпалами затрудняет сложность монтажа и высокий вес готового изделия
Содержание деревянного и бетонного пути является трудоемким, так как требуется регулярная замена сгнивших и треснувших шпал и частая замена резиновых амортизирующих вкладышей, более того болтовые скрепления бетонных шпал требуют периодической подтяжки. Для устранения эксплуатационных недостатков, предлагается использование нового вида шпал — полимерных. С 1990-х годов некоторые страны мира начали внедрять полимерные шпалы на железные дороги, в том числе и на скоростные (Япония, Китай). Так же активно начинают интересоваться данным видом шпал и другие страны мира, особенно страны с жарким влажным климатом (США, Индия, Таиланд и Филиппины). США является мировым лидером по производству таких шпал, так как до сих пор в США большое количество шпал из дерева, и в ходе поисков более экономичных решений для замены деревянных американские компании все больше склоняются в пользу полимерных шпал.
Последние разработки в области композитных шпал
В разных регионах мира разработан ряд технологий изготовления композитных шпал. Эти технологии стали потенциальной альтернативой деревянным шпалам. В отличие от стали и бетона, композитные шпалы можно спроектировать таким образом, чтобы они имитировали поведение древесины. При этом рельсовые пути с деревянными шпалами требуют обязательного технического обслуживания, а композитные шпалы практически не требуют технического обслуживания и более рациональны с экологической точки зрения. Далее мы рассмотрим различные типы композитных шпал в зависимости от количества, длины и ориентации волокон в них, причем рассматриваются шпалы, которые имеются в настоящее время, и технологии, которые все еще находятся в стадии исследований и разработки.
Шпалы, армированные короткими волокнами или не армированные вовсе (тип 1)
К типу 1 относятся шпалы, которые изготавливаются из переработанного пластика или из битума с наполнителями (песком, гравием, переработанным стеклом или резаными стеклянными волокнами (длина <20 мм)). Прочностные свойства этих шпал в основном обуславливаются используемым полимером. Хотя в некоторые из этих конструкций для увеличения жесткости и/или сопротивления растрескиванию вводится рубленое стекловолокно, это не оказывает существенного усиливающего влияния на улучшение конструктивных характеристик, которые требуются для применения в железнодорожных шпалах, работающих в тяжелых условиях эксплуатации. Высокая потребность в альтернативных материалах для производства шпал привела к тому, что некоторые компании, специализирующиеся на техническом обслуживании железных дорог, обратили свой взор на эти материалы и испытали их в работе. Если рассматривать материал, шпалы типа 1 предлагают ряд преимуществ, включая легкую обработку (резку, сверление), возможность использования отходов в производстве шпал, разумную цену. Однако недостатком этих шпал являются низкие показатели прочности и жесткости, ограниченная свобода выбора конструктивных решений, чувствительность к температуре и ползучести, а также низкая огнестойкость.
Шпалы, армированные непрерывными волокнами, расположенными в продольном направлении (тип 2)
Шпалы типа 2 – это шпалы, армированные в продольном направлении непрерывным стекловолокном и имеющие случайные включения очень коротких волокон в поперечном направлении или совсем не имеющие их. Прочность и жесткость в продольном направлении в основном определяются непрерывным стекловолокном, в то время как в поперечном направлении эти показатели в основном обуславливаются используемым полимером. Эти шпалы в первую очередь подходят для балластированных рельсовых путей, где напряжения в шпалах определяются изгибающей нагрузкой, но этот материал не идеален для применения на мостах (например, в качестве мостовых брусьев), где шпалы подвергаются действию комбинации значительных по величине изгибных и сдвиговых сил. Преимуществами шпал этого типа являются легкая обработка (резка, сверление), хорошая длительная прочность, высокая прочность на изгиб и не менее высокий модуль упругости. Однако с этими шпалами связан ряд сложных проблем, а именно: их низкая прочность на сдвиг и низкий модуль сдвига, ограниченная свобода выбора конструктивных решений, огнестойкость, находящаяся на границе допустимого, и высокая цена. К этой категории относятся синтетические шпалы из армированного волокном пенополиуретана (fiber reinforced foamed urethane, FFU). К ключевым характеристикам этого материала относятся его легкий вес, хорошая гидрофобность, стойкость к нагреву и коррозии, легкость обработки и срок службы более 50 лет. Армированный волокном пеноуретан используется в железнодорожной отрасли для производства шпал для путей, мостов и стрелочных переводов с широким диапазоном высоты шпалы — от 100 мм до 450 мм. Исследование акустических и динамических характеристик изготовленных из этого материала шпал для стрелочных переводов показало, что их характеристики эквивалентны характеристикам шпал из древесины лиственных пород. В 2011 году японский научно-исследовательский институт железнодорожного транспорта (Railway Technical Research Institute, RTRI) исследовал прослужившие 30 лет шпалы из армированного волокном пеноуретана, которые эксплуатировались на путях с регулярным движением поездов, и сообщил, что их всё еще можно использовать и в течение следующих 20 лет. На сегодняшний день шпалы из этого материала установлены на более чем 1300 км путей (приблизительно 2 миллиона шпал), причем основное их применение — на стрелочных переводах, открытых стальных балочных конструкциях и в туннелях. Помимо Японии, компоненты Sekisui из армированного волокном пеноуретана установлены в Германии, Австрии, Тайване, Голландии, США и Австралии. В настоящее время также изучается возможность их применения для длиннопролетного железнодорожного моста в городе Чунцин, Китай.
Шпалы, армированные волокнами, расположенными в продольном и поперечном направлениях (тип 3)
Шпалы типа 3 имеют длинные армирующие волокна как в продольном, так и в поперечном направлениях, и, следовательно, волокна работают, как на изгиб, так и на сдвиг. Конструктивные характеристики этих шпал можно задавать путем укладки армирующих волокон под разными углами в каждом направлении, в соответствии с заданными требованиями к рабочим характеристикам. В некоторых случаях недостаток непластичного поведения шпал из армированного стекловолокном полимера можно компенсировать путем включения в конструкцию нескольких стальных арматурных стержней. Вязкие свойства особенно важны, когда шпалы устанавливаются на мостах, где перед возникновением отказа ожидается появление достаточных предупреждающих признаков. Высокая свобода выбора конструктивных решений, хорошие показатели прочности на изгиб и сдвиг, легкость обработки и хорошая огнестойкость – вот основные преимущества этих шпал. Однако процесс производства композитных шпал этого типа довольно медленный, что может увеличить стоимость производства. Под эту категорию подпадают полимерные шпалы с сэндвич-конструкцией и шпалы из гибридного композита, в которых волокна ориентированы в двух направлениях, что позволяет противостоять изгибным напряжениям, а также сдвиговым усилиям.
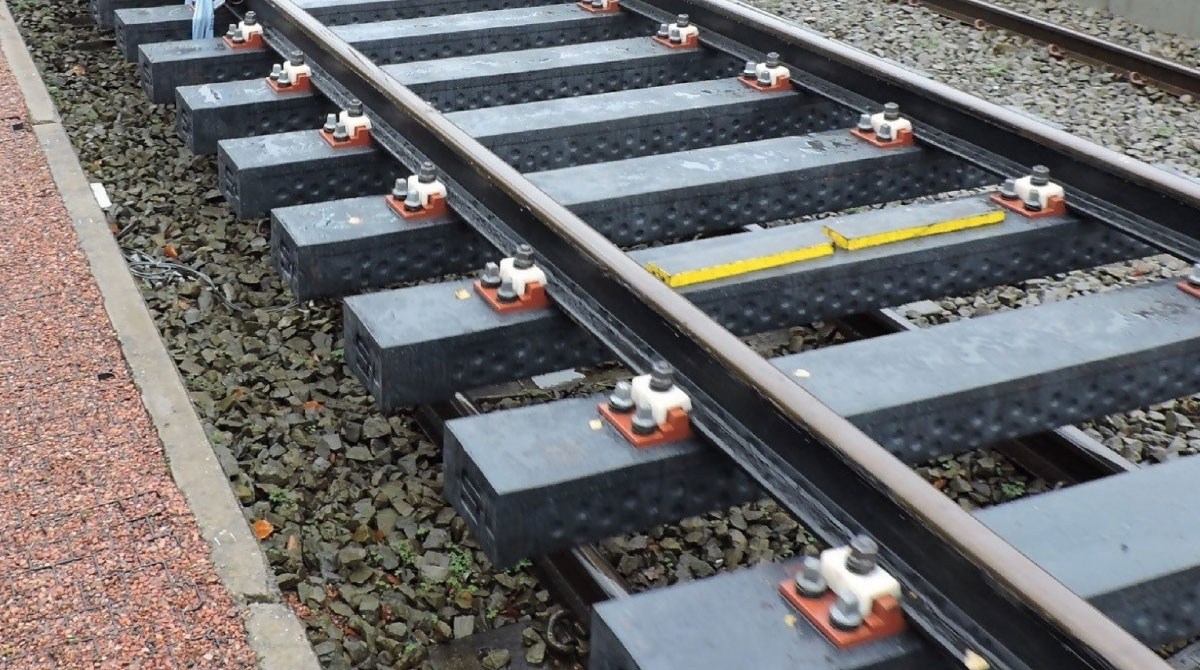
Композитные шпалы практически не требуют технического обслуживания
и более рациональны с экологической точки зрения
Проблемы использования композитных шпал
Несмотря на множество преимуществ разработанных в последнее время композитных шпал, на сегодняшний день они получили очень ограниченное признание в железнодорожной отрасли. В этом разделе представлены общие проблемы, возникающие при использовании композитных шпал.
Низкие показатели прочности и жесткости по сравнению с деревянными шпалами
Большинство конструкций композитных шпал были разработаны с целью замены существующих деревянных шпал, поскольку в этой сфере наблюдается высокая потребность в альтернативных материалах. Сообщалось, что каждый год железнодорожная отрасль США заменяет 14 миллионов деревянных шпал, при этом в другом отчете указывается, что ежегодно в США и Канаде заменяется около 5% шпал. В Австралии для поддержания железнодорожных путей в надлежащем состоянии требуется приблизительно 1,5 миллиона деревянных шпал в год.
Даже при таком высоком спросе на альтернативные варианты использование композитных шпал все еще ограничено. Это вполне объяснимо, так как большинство композитных шпал подпадает под тип 1, у которого показатели прочности и жесткости значительно ниже, чем у традиционных шпал.
Шпалы, подпадающие под тип 1, отличаются более низкими конструктивными характеристиками по сравнению со шпалами типа 2 и типа 3. В основном это связано с короткими волокнами, а иногда и с отсутствием волокон в шпалах типа 1. Напротив, шпалы типа 2 и типа 3 имеют длинные волокна, которые обеспечивают значительный усиливающий эффект для увеличения прочности и жесткости. Недавнее исследование модуля упругости шпал из армированного волокнами композита показало, что для применения на стрелочном переводе оптимальное значение может составлять всего 4 ГПа, и это позволяет поддерживать в заданных пределах как контактное давление между шпалой и балластом, так и максимальное вертикальное статическое отклонение. Кроме того, был экспериментально определен предел прочности при разрыве новых австралийских шпал из древесины лиственных пород при различных условиях, и при этом был обеспечен широкий диапазон прочности, от 47 до 110 МПа, тогда как большинство существующих композитных шпал демонстрируют низкую прочность и жесткость, особенно шпалы типа 1. Сообщалось, что трудно поддерживать безопасность путей при замене деревянных шпал композитными шпалами из переработанного пластика (тип 1), поскольку разрушения могут происходить как во время монтажа, так и в условиях эксплуатации, особенно при тяжелых динамических нагрузках. Кроме того, представители эксплуатирующих композитные шпалы подразделений железных дорог сообщают о некоторых отказах пластиковых шпал, возникающих после нескольких лет эксплуатации на железнодорожных путях, и высокий процент шпал был забракован в полевых условиях из-за проблем с контролем качества.
Включение продольных волокон делает шпалы типа 2 более прочными, чем шпалы типа 1, что позволяет противостоять изгибающей нагрузке, но их способность противостоять сдвиговым усилиям все еще остается умеренной, поскольку армирование в поперечном направлении не предусмотрено. Способность шпал противостоять сдвиговым усилиям особенно важна для применения на мостах (мостовые брусья), где шпалы подвергаются воздействию высокого сдвигового усилия из-за положения рельсов и опорных балок. Высокая способность шпал типа 3 противостоять сдвиговым усилиям достигается путем расположения армирующих элементов, как в продольном, так и в поперечном направлении.
Цена композитных шпал
Непомерно высокая стоимость большинства композитных шпал являются одной из основных причин их медленного продвижения на рынке. Компания Recycled Technologies International (RTI) заявила, что стоимость композитных шпал варьируется в диапазоне от 85 до 105 долларов США за шпалу (тип 1), причем это значение дано без учета монтажа, который весьма дорог, и затраты на него могут варьироваться в диапазоне от 70 до 200 долларов США за шпалу. Van Erp и Mckay показали, что цена на композитные шпалы с высоким содержанием волокон (тип 2 и тип 3) примерно в 5–10 раз выше, чем цена стандартных деревянных шпал. Однако ожидается, что более низкая стоимость жизненного цикла и долгий срок безремонтной эксплуатации таких шпал компенсирует их высокую первоначальную цену, которая, чтобы привлечь внимание железнодорожной отрасли, должна быть сопоставимой с ценой традиционных шпал или лишь незначительно превышать ее.
Низкая удерживающая способность
Для удерживания подкладок, которые крепят рельсы к шпалам и предотвращают вертикальные и боковые перемещения между ними, в основном используются путевые шурупы. Шпалы из древесины лиственных пород имеют сопротивление выдергиванию путевого шурупа 40 кН, в то время как для современных шпал из предварительно напряженного железобетона, поддерживающих движение более тяжелых и быстрых поездов, требуется не менее 60 кН. Низкая удерживающая способность путевого шурупа является еще одной проблемой композитных шпал типа 1. Сообщалось, что композитные шпалы, изготовленные из модифицированной смеси натурального каучука (тип 1) показали очень жесткое и неэластичное поведение при удерживании шурупов для системы крепления. Это связано с природой пластиковых материалов, которые подобно бетону не могут крепко удерживать шурупы, особенно в условиях динамической нагрузки. При использовании композитных шпал ослабление крепежа с ходом времени делает путь неустойчивым, что считается наиболее вероятной причиной аварий, связанных со сходом с рельсов на путях, уложенных на композитные шпалы. Тем не менее, удерживающая способность в шпалах типа 2 и типа 3 была улучшена за счет использования более качественных и имеющих более высокие характеристики материалов.
Образование пустот в материале
В процессе производства пластиковых композитных шпал (тип 1) сырье смешивается, расплавляется и перемешивается, чтобы создать гомогенную смесь, которая затем выдавливается в формы. После заполнения форм начинается процесс охлаждения, и в течение этого периода существует высокая вероятность образования пустот внутри материалов. Сообщалось, что композитные шпалы в зоне подрельсовой площадки продавливались внутрь в процессе эксплуатации. Кроме того, пустоты могут разрушаться и передавать напряжения от одной части к другой, что создает концентрацию напряжений и, как следствие, приводит к локальному выходу шпалы из строя до истечения срока ее службы. Эта проблема может возникнуть во время производства любого материала в зависимости от применяемой технологии, но не для деревянных шпал, которые изготавливаются из натурального дерева.
Деформация ползучести
Долговременные характеристики пластиковых шпал (тип 1) становятся критической проблемой, так как их длительная эксплуатация со временем оказывает существенное влияние на механические свойства. Сообщалось, что при длительных нагрузках композитная шпала может испытывать постоянную деформацию вследствие ползучести, скорость которой зависит от величины и продолжительности приложения напряжения, а также от температуры, при которой прикладывается нагрузка. Из-за эффекта ползучести и последующего снятия напряжений, система крепления имеет тенденцию ослабевать, особенно на криволинейном участке пути, что отрицательно влияет на удержание железнодорожной колеи. Эти эффекты могут сокращать срок службы пластиковых шпал, который, по оценкам компаний-производителей, составляет приблизительно 50 лет. Среди всех традиционных материалов шпал ползучести подвержены бетон и сталь. Кроме того, сообщалось о склонности геополимерного бетона на основе зольной пыли к возникновению значительных проблем, связанных с эффектами ползучести и уменьшения длины из-за наличия предварительного напряжения, потому что зольная пыль замедляет процесс отверждения бетона. Тем не менее, нет достаточной информации о деформации ползучести для шпал типа 2 и типа 3, и для изучения их поведения при постоянных нагрузках на рельсовых путях необходимо провести дополнительные исследования.
Недостаток информации о долговременных характеристиках
Хотя большинство производителей композитных шпал выполнили оценку статических характеристик своих изделий, долговременные характеристики с точки зрения таких аспектов, как динамические свойства, ударная прочность, усталость и длительная прочность всех типов шпал, до сих пор неизвестны. Критический системный анализ конструкции показывает, что важно исследовать эти проблемы перед монтажом, так как шпалы часто подвергаются воздействию динамических, ударных и усталостных нагрузок, а также атмосферным воздействиям. Композиционный материал подвержен ударным повреждениям, которые ведут к расслоению и растрескиванию матрицы, и, поскольку его поведение при ударной нагрузке значительно отличается от поведения при нормальных условиях нагружения, его прочность и жесткость могут значительно уменьшиться, и поэтому требуется тщательный подход к расчету. Отсутствие соответствующих знаний о композитных шпалах ограничивает их широкое применение.
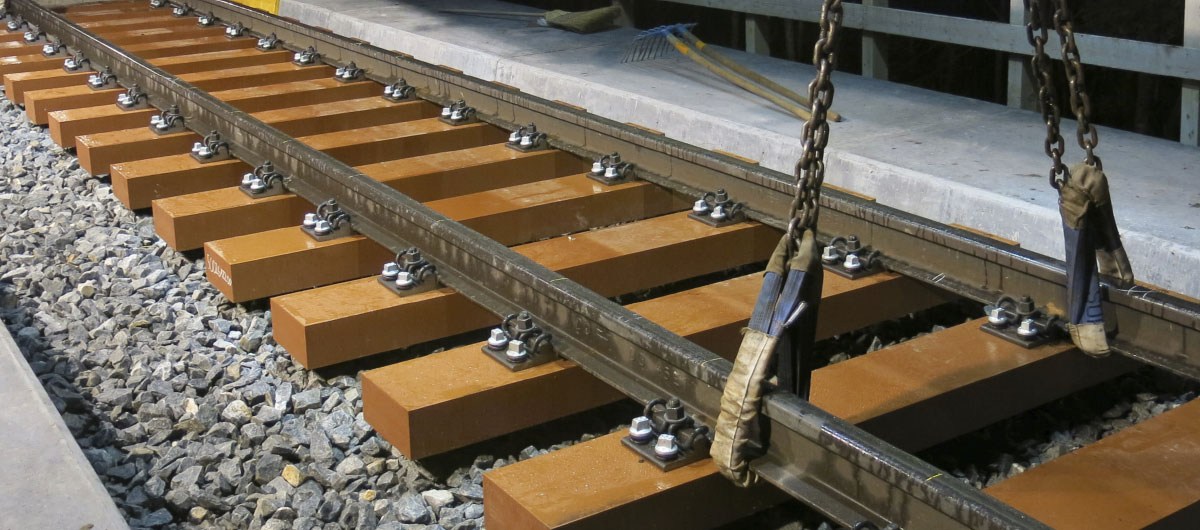
Перспективы на будущее
Основными проблемами при использовании композитных железнодорожных шпал типа 1 являются их ограниченные показатели прочности и жесткости и низкие динамические свойства, которые в большинстве случаев не сопоставимы со свойствами древесины. Ограничения, вызванные низкими конструктивными характеристиками шпал типа 1, преодолены в шпалах типах 2 и 3, но их высокая цена по сравнению со шпалами из стандартного материала все еще остается большой проблемой. Более того, недостаток в настоящее время информации об их долговременных характеристиках и отсутствие руководящих указаний для проектирования ограничивают их широкое применение. Для устранения ограничений, присущих существующим композитным шпалам, необходимо провести более серьезные исследования. Для преодоления текущих ограничений, присущих композитным шпалам, предлагаются следующие подходы.
Улучшение конструктивных характеристик
Шпалы из переработанного пластика (тип 1) имеют конструктивные характеристики, несопоставимые с характеристиками древесины. Композитные шпалы из армированного волокном пеноуретана (тип 2) благодаря наличию непрерывных армирующих волокон имеют более высокие показатели прочности и жесткости по сравнению с композитными шпалами типа 1, но в настоящее время они довольно дороги, и их применение в основном ограничивается стрелочными переводами. Поскольку показатели прочности и жесткости шпал из переработанного пластика (тип 1) значительно ниже, чем у традиционных деревянных шпал, для улучшения этих показателей предлагается использовать армирующее волокно. Однако для разработки технологий, в которых волокна работают в комбинации с термопластичным полимером, необходимы серьезные исследования. С точки зрения концепции пластиковых шпал с деревянной сердцевиной, критической проблемой может быть обеспечение соответствия требованиям соединения между пластиком и древесиной, и к тому же эти шпалы были разработаны в то время, когда исследователи искали альтернативный материал для древесины вследствие ее чувствительности к воздействию окружающей среды. Первоначальные результаты для клееных многослойных шпал типа «сэндвич» (тип 3) показали, что они работают намного лучше, чем шпалы из переработанного пластика (тип 1). Это объясняется тем, что высокопрочные волокнистые композитные оболочки на сэндвич-конструкции, работающие и в продольном, и в поперечном направлении, в результате позволяют шпалам этого типа отвечать требованиям к жесткости 4 ГПа для обеспечения безопасности и надежности железнодорожного пути.
Оптимальное использование материалов и совершенствование технологий изготовления
Одним из основных препятствий на пути к широкому применению композитных шпал типа 2 и типа 3 на железнодорожных путях считалась их цена, которая примерно в 5 – 10 раз выше, чем цена стандартных деревянных шпал, как упоминалось выше. Стандартно тут рекомендуют оптимизировать саму конструкцию и структуру композитных шпал при сохранении требуемого уровня физико-механических характеристик, что позволит и снизить изначальные расходы на сырье, а также избежать лишних отходов материала.
Кроме того, затраты связаны и с конструкцией рельсового пути, которая может варьироваться в зависимости от типа используемых шпал. Например, толщина балласта, необходимая для бетонных шпал, почти вдвое больше, чем в случае применения деревянных шпал. Это связано с плохими динамическими свойствами и высокой жесткостью бетона, что ведет к возникновению большого изгибающего момента и требует применения фундамента с опорой средней жесткости. Установка подрельсовых прокладок увеличивает стоимость изготовления пути, а также снижает скорость строительства, хотя это необходимо для обеспечения электрической и виброизоляции, контроля шума и т. п. Поэтому следует сосредоточиться на разработке конструкции композитных шпал с улучшенными динамическими свойствами, которые могут работать с балластной подушкой малой толщины и без подрельсовых прокладок.
Оптимизация конструкции шпалы может быть достигнута и путем снижения качества материалов в тех зонах, в которых напряжение незначительно. Это метод, который может быть полезен для разработки экономически выгодных композитных железнодорожных шпал. Эта технология уже была реализована в шпалах из предварительно напряженного железобетона, в которых бетонные шпалы B70 подвергнуты оптимизации на основе распределения нагрузок от колес.
Оценка характеристик в краткосрочной и долгосрочной перспективе
Помимо требований к рабочей нагрузке, эксплуатационные качества композитного материала определяются его длительной прочностью и способностью противостоять воздействиям окружающей среды, связанным с ультрафиолетовым излучением, высоким pH, высокими и низкими температурами, влажностью и т. п. Поскольку композитные железнодорожные шпалы – это относительно новые продукты, история эксплуатации которых в железнодорожной отрасли относительно невелика, по сравнению со шпалами из более традиционных материалов, краткосрочные и долгосрочные исследования поведения композитных шпал имеют большое значение для развития рынка и повышения их конкурентоспособности. Кроме того, важен регулярный мониторинг технических характеристик в процессе эксплуатации.
Проектные рекомендации и стандарты
Поскольку в настоящее время нет общепризнанного стандарта для композитных шпал (в частности, типа 3), рекомендации по их проектированию должны разрабатываться таким образом, чтобы их истинные возможности могли быть использованы для достижения удовлетворительного уровня надежности конструкции. Разработка национальных и международных стандартов будет способствовать внедрению новых композитных шпал в качестве альтернативы традиционным материалам. Для композитных железнодорожных шпал должны быть определены уравнения расчета по предельным состояниям со значениями коэффициентов частичной нагрузки и коэффициентов снижения несущей способности.
Выводы
Высокие затраты на техническое обслуживание и экологические проблемы, связанные с использованием деревянных, бетонных и стальных шпал, побудили исследователей, инженеров и конечных пользователей задуматься о продукции из альтернативных материалов, например, полимерных композитов. В последнее время в разных частях света было разработано несколько конструкций, и хотя их внедрение пока идет не так стремительно, как хотелось бы, потенциал для их применения достаточно высок. Конструкторы и технологи совместно с производителями сырья и материалов продолжают работать над устранением барьеров, тормозящих массовое применение этих новых изделий, что при грамотном подходе к реализации данной задачи обязательно принесет свои плоды. Будем надеяться, что производители композитных шпал в погоне за прибылью не забудут, что именно сейчас, на начальном этапе внедрения нового продукта, очень легко дискредитировать материал, выпустив на рынок товар ненадлежащего качества или изначально не предназначенный для требуемых условий и режимов эксплуатации. Безответственность в данном вопросе, касающемся применения как шпал, так и других изделий из композитов, будет, в конечном счете, дорого стоить всей нашей отрасли, пагубно отразившись на репутации материалов и увеличении спроса на них в различных отраслях промышленности.
Полную версию статьи (14 страниц, 4 таблицы, 8 рисунков, ссылки на зарубежные и отечественных производителей шпал) вы можете заказать в редакции журнала «Композитный мир».